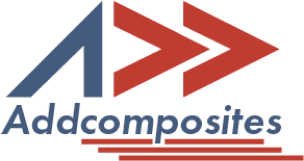
Core engineering study programs are flooded with tried and tested processes, creating very monotone projects on the ground. This has led the major focus to being on delivering results, rather than developing new approaches. In turn new materials and processing techniques entering the manufacturing world leaves educational establishments and traditional SMEs behind.
Over the past year, we have been in conversation with many educational establishments and SME manufacturers. The repeated comment is that there is quite simply not enough qualified and experienced composite engineers available. The reason being that composites is not a widely taught subject in university, and there just aren’t enough straight forward degrees focusing on composite engineering and related manufacturing processes.
Many of the composites engineers today do not come from specialized composites courses, rather their knowledge simply come from exploring their structural engineering roots. The solid modeling and computer stress analysis programs (FEA) generally do not have composite modules in them either. These modules have to be bought from specialists and then learned on-the-job under great pressure to get it the right first time, and not learn from your mistakes — as mistakes are costly.
Our experience at Addcomposites is that we have to go and hire new team members from a particular sector where composites have not been the main subjects. Our recent intern joined us following a frustrating journey to find new and innovative ventures in composites, and is now able to gain first-hand experience with us.
Our first concern is that without a qualified labor force in these materials, processes, and techniques, projects will be performed through the conventional "metallic engineers" mindset, leading to composites designed as “black steel”.
Conventional structural engineers are able to pull from industry-specific standard technical publications that have published standard properties for metallic materials, and production processes such as weldings with standards and coded qualifications. However, in the emerging world of composites, very few similar standards exist. We are starting to see exceptions, of course, eg: the CIRIA Guideline for FRP Bridge Construction — give us more of this please! — as composites become more widely known and available for general manufacturing.
This raises our concern for the time, effort, and costs associated with the mainstream development of composite components, or stand-alone composite parts, when qualified and experienced composites engineers are not involved. The iteration from testing to redevelopment requires expert knowledge in the properties and most appropriate processes. Designs are often not as optimal or cost-effective as can be achieved — raising the question of are they actually “production-ready” or just complex engineering? [1]
The above-mentioned challenges can be sub-divided into two main sections:
The advent of Additive Manufacturing has forced many FEA simulation providers to incorporate new elements for accurately calculating orthotropic materials. Assuming the core competency of the engineer is to be able to simulate using FEA tools, they would be able to predict how the structure would react to forces. Now, these newly incorporated FEA add-ons that include orthotropic, or anisotropic, element simulation should provide enough information for experienced composites engineers with analysis and testing for 3D printed and fiber-reinforced parts.
Manufacturing simulations have also come a long way. Now the engineer can simulate manufacturing and deduce its manufacturability in a cost efficient manner. This has become much more accessible through software like ADDpath.
ADDpath is a Rhino based plug-in that allows for offline programming of fiber placement and motion simulation of placement. ADDpath can be accessed separately without having the AFP tool as well.
The future of manufacturing is automated and composites manufacturers are acknowledging it now. The major trend helping in this regard is the increasing number of both industrial and collaborative robots. This has helped in increasing familiarity and assurance of continuous operations safely.
With the recent innovation of affordable ATL systems like the AFP-XS, SMEs and Technical Centers can now simply rent the system and practice the production using advanced processes like AFP for brief production runs or short term projects.
Providing SMEs with cost-effective, robotic composites manufacturing systems: Addcomposites
Addcomposites has created a plug & play toolhead that easily mounts onto any standard industrial robotic arm. The available monthly subscription of this tool package brings the capabilities of the aforementioned systems to SMEs, without a heavy price tag. Available for as low as €1999 per month, this helps in solving the puzzle to achieve Network Driven Scaling for SMEs, lowering the barrier of entry to i4.0, and enabling more growth in many application areas.
For early adopters of the AFP-XS system, we are running a special offer while supplies last. See if you are eligible here.
Core engineering study programs are flooded with tried and tested processes, creating very monotone projects on the ground. This has led the major focus to being on delivering results, rather than developing new approaches. In turn new materials and processing techniques entering the manufacturing world leaves educational establishments and traditional SMEs behind.
Over the past year, we have been in conversation with many educational establishments and SME manufacturers. The repeated comment is that there is quite simply not enough qualified and experienced composite engineers available. The reason being that composites is not a widely taught subject in university, and there just aren’t enough straight forward degrees focusing on composite engineering and related manufacturing processes.
Many of the composites engineers today do not come from specialized composites courses, rather their knowledge simply come from exploring their structural engineering roots. The solid modeling and computer stress analysis programs (FEA) generally do not have composite modules in them either. These modules have to be bought from specialists and then learned on-the-job under great pressure to get it the right first time, and not learn from your mistakes — as mistakes are costly.
Our experience at Addcomposites is that we have to go and hire new team members from a particular sector where composites have not been the main subjects. Our recent intern joined us following a frustrating journey to find new and innovative ventures in composites, and is now able to gain first-hand experience with us.
Our first concern is that without a qualified labor force in these materials, processes, and techniques, projects will be performed through the conventional "metallic engineers" mindset, leading to composites designed as “black steel”.
Conventional structural engineers are able to pull from industry-specific standard technical publications that have published standard properties for metallic materials, and production processes such as weldings with standards and coded qualifications. However, in the emerging world of composites, very few similar standards exist. We are starting to see exceptions, of course, eg: the CIRIA Guideline for FRP Bridge Construction — give us more of this please! — as composites become more widely known and available for general manufacturing.
This raises our concern for the time, effort, and costs associated with the mainstream development of composite components, or stand-alone composite parts, when qualified and experienced composites engineers are not involved. The iteration from testing to redevelopment requires expert knowledge in the properties and most appropriate processes. Designs are often not as optimal or cost-effective as can be achieved — raising the question of are they actually “production-ready” or just complex engineering? [1]
The above-mentioned challenges can be sub-divided into two main sections:
The advent of Additive Manufacturing has forced many FEA simulation providers to incorporate new elements for accurately calculating orthotropic materials. Assuming the core competency of the engineer is to be able to simulate using FEA tools, they would be able to predict how the structure would react to forces. Now, these newly incorporated FEA add-ons that include orthotropic, or anisotropic, element simulation should provide enough information for experienced composites engineers with analysis and testing for 3D printed and fiber-reinforced parts.
Manufacturing simulations have also come a long way. Now the engineer can simulate manufacturing and deduce its manufacturability in a cost efficient manner. This has become much more accessible through software like ADDpath.
ADDpath is a Rhino based plug-in that allows for offline programming of fiber placement and motion simulation of placement. ADDpath can be accessed separately without having the AFP tool as well.
The future of manufacturing is automated and composites manufacturers are acknowledging it now. The major trend helping in this regard is the increasing number of both industrial and collaborative robots. This has helped in increasing familiarity and assurance of continuous operations safely.
With the recent innovation of affordable ATL systems like the AFP-XS, SMEs and Technical Centers can now simply rent the system and practice the production using advanced processes like AFP for brief production runs or short term projects.
Providing SMEs with cost-effective, robotic composites manufacturing systems: Addcomposites
Addcomposites has created a plug & play toolhead that easily mounts onto any standard industrial robotic arm. The available monthly subscription of this tool package brings the capabilities of the aforementioned systems to SMEs, without a heavy price tag. Available for as low as €1999 per month, this helps in solving the puzzle to achieve Network Driven Scaling for SMEs, lowering the barrier of entry to i4.0, and enabling more growth in many application areas.
For early adopters of the AFP-XS system, we are running a special offer while supplies last. See if you are eligible here.