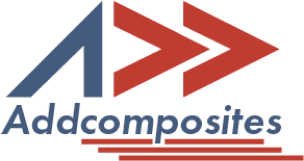
Hydrogen fuel cell technology is securing a spot in the future of advanced mobility and energy revolution, as engineers explore multiple avenues in the quest for decarbonization. The feasibility of hydrogen fuel cell vehicles specifically relies on the development of safe, lightweight, and competitive solutions for hydrogen storage. After demonstrating hundreds of prototype vehicles, today commercial hydrogen tanks are in the early stages of market launch, adopting configurations using composite materials. However, the production rate is still low and the cost is high.
The world faces a new paradigm for dealing with the threat of climate change and environmental pollution. Sustainable systems continue to emerge and mature to help reduce the environmental impacts of greenhouse gas emissions. The evolution of our power supply system seems to include the electrification of the grid. However, electrification alone will not be able to cater to all the use cases of energy requirements. This has led to the adoption of hydrogen as an alternative fuel..
Hydrogen fuel cell (FC) electric vehicles have gained global attention and are seen as a viable green alternative in decarbonization.
Similar to how an electric vehicle needs to have a supply of electricity stored onboard in a battery, a hydrogen-powered economy needs onboard storage of hydrogen in the Hydrogen tanks. As these tanks are carried onboard, it is essential to have a high specific storage capacity i.e. kg of hydrogen stored/ dry weight of the tank.
it is essential to have a high specific storage capacity i.e. kg of hydrogen stored/ dry weight of the tank.
For manufacturers/ Designers focusing on being the preferred supplier of the tanks the weight of the tank compared with the cost of production becomes the most important driver of sales. Basically any manufacturer able to combine materials in the tank shape with minimum spend will win the race. Adding intelligence is a plus, as knowing the pressure, and temperature can help plan refueling and monitor the health of the tanks.
The above article is part of the course Design and Development of Compressed Hydrogen Storage Tanks. The course covers a lot more, starting with discussing challenges in material selection and manufacturing practices, as well as cutting-edge trends being explored. Key problems in the design and analysis of the hydrogen reservoir are also addressed. Finally, testing and certification requirements are discussed as they play an important role in industry acceptance.
Hydrogen fuel cell technology is securing a spot in the future of advanced mobility and energy revolution, as engineers explore multiple avenues in the quest for decarbonization. The feasibility of hydrogen fuel cell vehicles specifically relies on the development of safe, lightweight, and competitive solutions for hydrogen storage. After demonstrating hundreds of prototype vehicles, today commercial hydrogen tanks are in the early stages of market launch, adopting configurations using composite materials. However, the production rate is still low and the cost is high.
The world faces a new paradigm for dealing with the threat of climate change and environmental pollution. Sustainable systems continue to emerge and mature to help reduce the environmental impacts of greenhouse gas emissions. The evolution of our power supply system seems to include the electrification of the grid. However, electrification alone will not be able to cater to all the use cases of energy requirements. This has led to the adoption of hydrogen as an alternative fuel..
Hydrogen fuel cell (FC) electric vehicles have gained global attention and are seen as a viable green alternative in decarbonization.
Similar to how an electric vehicle needs to have a supply of electricity stored onboard in a battery, a hydrogen-powered economy needs onboard storage of hydrogen in the Hydrogen tanks. As these tanks are carried onboard, it is essential to have a high specific storage capacity i.e. kg of hydrogen stored/ dry weight of the tank.
it is essential to have a high specific storage capacity i.e. kg of hydrogen stored/ dry weight of the tank.
For manufacturers/ Designers focusing on being the preferred supplier of the tanks the weight of the tank compared with the cost of production becomes the most important driver of sales. Basically any manufacturer able to combine materials in the tank shape with minimum spend will win the race. Adding intelligence is a plus, as knowing the pressure, and temperature can help plan refueling and monitor the health of the tanks.
The above article is part of the course Design and Development of Compressed Hydrogen Storage Tanks. The course covers a lot more, starting with discussing challenges in material selection and manufacturing practices, as well as cutting-edge trends being explored. Key problems in the design and analysis of the hydrogen reservoir are also addressed. Finally, testing and certification requirements are discussed as they play an important role in industry acceptance.