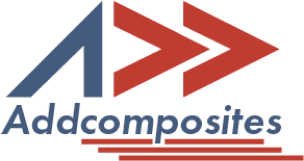
Fiber Reinforced Polymer (FRP) composites are revolutionizing industries across the board, from aerospace to infrastructure, and from energy to sports. These advanced materials, known for their exceptional strength-to-weight ratios, corrosion resistance, and design flexibility, are pushing the boundaries of what's possible in engineering and design.
In this comprehensive exploration of FRP applications, we delve into the cutting-edge developments that are shaping our world. From the sleek carbon fiber frames of electric bikes to the massive composite structures in renewable energy installations, FRP composites are at the forefront of innovation.
Did you know that FRP composites are being used to create recyclable wind turbine blades, or that they're enabling the development of next-generation spacecraft? Are you aware of how these materials are transforming urban infrastructure, making our bridges more durable and our buildings more resilient?
Whether you're an engineer, a researcher, or simply curious about the materials that are building our future, this blog offers a deep dive into the world of FRP composites. We'll explore:
Each section provides detailed case studies, recent developments, and insights into manufacturing processes and future trends. Whether you're interested in automated fiber placement techniques, sustainable composite solutions, or the integration of AI in composite manufacturing, you'll find valuable information here.
We invite you to navigate through the table of contents and explore the sections that pique your interest. Prepare to be amazed by the versatility and potential of FRP composites as we uncover how these materials are shaping the future of technology and engineering.
Fiber Reinforced Polymer (FRP) composites have revolutionized architectural design and construction, offering exceptional strength-to-weight ratios, design flexibility, and durability. These advanced materials enable architects to push the boundaries of traditional building techniques, creating innovative and high-performance structures.
This project showcases the versatility of FRP in creating lightweight, durable public art installations. The use of vacuum infusion demonstrates advanced composites manufacturing methods, highlighting the evolution of FRP fabrication techniques.
The Trillium Pavilion exemplifies the potential of 3D printing in composite structures, showcasing how advanced manufacturing techniques can create complex, organic forms in architecture.
This project demonstrates the capabilities of automated composite manufacturing in creating large-scale, complex architectural forms. The use of robotics and CNC machining highlights the precision and efficiency achievable with modern FRP fabrication techniques.
The pavilion showcases advanced fiber placement techniques in creating complex, load-bearing structures. The combination of different manufacturing methods demonstrates the versatility of FRP in architectural applications.
This innovative approach to home construction leverages additive manufacturing technologies to create efficient, sustainable housing solutions. The use of FRP in 3D-printed structures opens new possibilities for rapid, customizable construction.
SQ4D's project demonstrates the potential of large-scale additive manufacturing in residential construction, showcasing how FRP materials can revolutionize traditional building practices.
This project exemplifies the use of sustainable composites in architecture, demonstrating how recycled materials can be transformed into high-performance building components.
The integration of FRP composites in architecture continues to evolve, with emerging trends including:
As these technologies mature, we can expect to see even more innovative and sustainable FRP applications in architecture, pushing the boundaries of what's possible in building design and construction.
Fiber Reinforced Polymer (FRP) composites have revolutionized the aerospace industry due to their exceptional strength-to-weight ratio, corrosion resistance, and design flexibility. These materials have become integral in commercial and military aircraft, space exploration vehicles, and emerging electric Vertical Take-Off and Landing (eVTOL) aircraft.
FRP composites, particularly Carbon Fiber Reinforced Polymers (CFRPs), are extensively used in primary aircraft structures:
The design and manufacturing of these complex structures often involve advanced techniques such as Automated Fiber Placement (AFP).
Glass Fiber Reinforced Polymers (GFRPs) are commonly used for non-structural interior elements:
These components often utilize sandwich structures to achieve optimal strength and weight characteristics.
Advanced composites, including ceramic matrix composites (CMCs), are increasingly being used in jet engine components:
The manufacturing of these complex engine components often requires specialized techniques and equipment.
FRP composites play a crucial role in space exploration vehicles and satellites:
The extreme conditions of space require specialized testing and certification processes for these components.
FRP composites have emerged as critical materials in the rapidly evolving field of electric Vertical Take-Off and Landing (eVTOL) aircraft, often referred to as flying taxis:
The design and manufacturing of eVTOL components often leverage advanced manufacturing techniques to achieve the required performance characteristics.
NASA's Advanced Composite Solar Sail System
NASA has developed an Advanced Composite Solar Sail System using carbon fiber and polymers to withstand extreme environmental conditions. This next-generation solar sail replaces traditional heavy propulsion systems by using the pressure of sunlight for propulsion. The new boom, made with flexible polymer and carbon fiber materials, is stiffer and lighter than previous models, improving durability and strength for challenging space environments.
Mars 2020 Rover Heat Shield
Lockheed Martin developed a heat shield using a tiled Phenolic Impregnated Carbon Ablator (PICA) thermal protection system to protect the Mars 2020 rover during its journey to Mars. This aeroshell, the largest ever built for a planetary mission at nearly 15 feet in diameter, is designed to protect the rover from temperatures of up to 3,800 degrees Fahrenheit during entry, descent, and landing (EDL).
Lunar Construction Technologies
NASA is developing new planetary construction technologies using advanced materials for building structures on the Moon. In collaboration with AI SpaceFactory, they are creating a new material for 3D printing using simulated lunar regolith. This innovative approach aims to enable the construction of sustainable habitats for future lunar exploration and Mars missions.
Thermoplastic Composites in Aircraft Interiors
A team of researchers from AIM Altitude, Composites Evolution Limited, and Sheffield Hallam University have developed a unique thermosetting resin system for use in aircraft interior parts. This nanocomposite material, based on polyfurfuryl alcohol (PFA), offers excellent mechanical properties similar to phenolic resins but without the toxic compounds, providing improved fire resistance and surface finish options.
eVTOL Advancements
Companies like Joby Aviation and Archer Aviation are making significant progress in eVTOL development:
These advancements demonstrate the rapid progress in urban air mobility solutions utilizing composite materials.
Spacesuit Innovations
The International Lunar Exploration Working Group (ILEWG) is developing a prototype spacesuit layer with a damage-detection system using Teijin Aramid's Twaron®. This innovative approach aims to create lighter, more comfortable spacesuits that are damage-resistant and can alert wearers to potential breaches.
Commercial Orbital Rockets
Orbex is building Prime, a commercial orbital rocket made of an optimized blend of lightweight carbon-fiber and aluminum composites. This design makes the rocket up to 30 percent lighter than other rockets of its size, demonstrating the potential for composites in reducing launch costs and improving payload capacity.
While FRP composites offer numerous advantages in aerospace applications, challenges such as high manufacturing costs and the need for specialized repair techniques remain. Ongoing research and development are addressing these issues, focusing on areas such as:
As aerospace technology continues to advance, FRP composites are expected to play an increasingly critical role in enabling more efficient, lightweight, and capable aircraft, spacecraft, and eVTOL vehicles. The industry is moving towards more intelligent and automated manufacturing processes, which will further enhance the potential of composite materials in aerospace applications.
Fiber Reinforced Polymer (FRP) composites continue to revolutionize the automotive industry, offering significant advantages in terms of weight reduction, energy efficiency, and overall performance. This overview highlights recent developments and specific case studies demonstrating the innovative use of composites in various vehicle types, with additional resources for in-depth exploration.
The shift towards electric vehicles has accelerated the adoption of FRP composites in automotive manufacturing. Lightweight electric motor design is paving the way for the next generation of EVs, with composites playing a crucial role.
Hyundai Creta: Simplified Trunk Floor Production
General Motors' CarbonPro Pickup Bed
Arrival's Commercial Electric Vans
For more insights on composites in EVs, explore continuous fiber composites in automobiles.
The development of hydrogen fuel cell technology is revolutionizing transport, with FRP composites playing a crucial role in lightweight hydrogen tank design.
Hyundai America Technical Center: Composite Bed for Pickup Trucks
For more information on hydrogen storage solutions, check out the guide on selecting the right hydrogen tanks.
High-Performance Vehicles
FRP composites are extensively used in high-performance vehicles to achieve superior strength-to-weight ratios and enhanced performance.
Donkervoort D8 GTO-JD70 Bare Naked Carbon Edition (BNCE)
Alfa Romeo 2020 Giulia GTA
Learn more about innovations in composite materials and their real-world applications.
FRP composites are making significant inroads in mass transit and commercial vehicle manufacturing, offering benefits in weight reduction and energy efficiency.
Yutong Electric Buses for Helsinki, Finland
Volta Zero Electric Truck
For more on composites in urban transport, read about current applications and future prospects.
Innovative Material Applications
Ford and McDonald's Coffee Chaff Composite
BMW Motorrad Carbon Fiber Motorcycle Chassis
Discover more about advanced material selection in composites.
The automotive industry is witnessing a shift towards more advanced manufacturing processes for composite components. Automated Fiber Placement (AFP) is becoming increasingly important in automotive manufacturing.
Research and Development
Covestro and Guangzhou Automobile Group (GAC) Collaboration
For insights into the future of composite manufacturing, explore the shift from traditional to intelligent manufacturing.
The automotive industry continues to push the boundaries of FRP composite applications, from mass-market electric vehicles to high-performance sports cars and commercial transport. As the industry evolves towards more efficient and sustainable transportation solutions, FRP composites are playing an increasingly critical role in enabling lighter, more durable, and higher-performing vehicles across all segments.
For those interested in implementing advanced manufacturing techniques, learn how to implement an Automated Fiber Placement system 80% faster and with 1% of the cost of traditional systems.
Stay updated on the latest developments in composite manufacturing for the automotive industry by following Addcomposites' blog for regular insights and case studies.
Fiber Reinforced Polymer (FRP) composites continue to play a crucial role in the energy sector, offering significant advantages in various applications ranging from renewable energy generation to energy storage and distribution. Recent developments and case studies highlight the growing importance of these advanced materials in shaping the future of energy.
Wind Energy
Case Study: Siemens Gamesa's RecyclableBlade In September 2021, Siemens Gamesa Renewable Energy introduced the world's first recyclable wind turbine blade, called the RecyclableBlade. This innovative design allows for efficient separation of the resin from the composite materials at the end of the blade's life, enabling the reuse of materials in new applications.
Case Study: NREL and Montana State University Marine Energy Project In April 2021, NREL and Montana State University were awarded funding to apply additive manufacturing and composite technologies to marine energy devices. The project involves additively manufacturing internal molds designed to become a permanent part of the final load-bearing structure, printing tidal turbine blade molds in four sections and wrapping them in composite piles to eliminate points of failure.
Hydrogen Storage Systems
Case Study: Voith Group's Hydrogen Storage Tanks The Voith Group has developed the Voith Plug & Drive H2 Storage System, a complete system from tank nozzle to fuel cell inlet for heavy-duty trucks. The Carbon4Tank, made from T700 carbon fiber and a specialty epoxy-based resin, offers significant weight reduction and improved performance.
While FRP composites offer numerous advantages in energy applications, challenges such as recycling and end-of-life disposal remain. However, ongoing research and development are addressing these issues:
As the energy sector continues to evolve towards more sustainable and efficient solutions, FRP composites are expected to play an increasingly critical role in enabling advanced energy generation, storage, and distribution systems. The case studies and developments highlighted here demonstrate the industry's commitment to innovation and sustainability in the use of composite materials for energy applications.
Fiber Reinforced Polymer (FRP) composites are revolutionizing infrastructure across various sectors, offering innovative solutions to long-standing challenges. This overview examines recent developments and case studies that highlight the versatility and effectiveness of FRP in infrastructure applications.
Innovations in composite materials are driving the trend of FRP use in bridge construction and rehabilitation. Recent examples include:
FRP composites are proving invaluable in coastal protection and flood mitigation efforts:
FRP adoption has increased in response to natural disasters:
FRP's versatility has led to innovative solutions:
The diverse applications of FRP in infrastructure demonstrate its versatility and effectiveness in addressing a wide range of challenges. Key points include:
As we continue to push the boundaries of what's possible with FRP composites, we can look forward to a future where our infrastructure is not only stronger and more resilient but also more sustainable and environmentally friendly.
Fiber Reinforced Polymer (FRP) composites continue to revolutionize the marine industry, particularly in high-performance and racing boats. Recent developments showcase the exceptional strength-to-weight ratio, corrosion resistance, and design flexibility of FRP composites in various marine applications. For a comprehensive introduction to composite materials, you can refer to Addcomposites' guide on composite materials.
For more information on the various manufacturing processes used in creating these innovative hulls, check out Addcomposites' overview of composite manufacturing methods.
To understand the complexities of working with carbon fiber, read Addcomposites' carbon fiber composites processing guide.
For insights into sustainable composite manufacturing, visit Addcomposites' article on sustainable composites.
To learn more about the various types of fiber reinforcements used in these applications, check out Addcomposites' guide on reinforcement fibers.
As the marine industry continues to evolve, FRP composites are playing a crucial role in enabling more efficient, lightweight, and environmentally friendly watercraft designs. However, challenges remain, including:
To address these challenges, ongoing research focuses on:
For more information on the future of composites manufacturing, read Addcomposites' article on the shift from traditional to intelligent manufacturing.
As we continue to push the boundaries of marine engineering, FRP composites will undoubtedly play a pivotal role in shaping the future of high-performance and sustainable watercraft.
Fiber Reinforced Polymer (FRP) composites continue to revolutionize military and defense applications, offering exceptional strength-to-weight ratios, corrosion resistance, and design flexibility. These advanced materials are crucial in developing cutting-edge defense technologies across various sectors.
Learn more about advanced composites in aerospace applications
Explore the future of composites in aerospace
Discover automated fiber placement in aerospace manufacturing
Read about lightweight electric motor design in aircraft
Understand the basics of carbon fiber composites
Explore automated fiber placement in complex structures
Learn about innovations in composite materials
Discover continuous fiber 3D printing technologies
Explore the fundamentals of composites manufacturing
While FRP composites offer numerous advantages, ongoing research addresses challenges such as:
Learn about the future of composites manufacturing
As defense technology evolves, FRP composites continue to play a critical role in enabling more advanced, efficient, and capable military systems across air, land, and sea applications. The integration of automated manufacturing processes, such as Automated Fiber Placement (AFP), is further accelerating the adoption and innovation in military-grade composite structures.
Fiber Reinforced Polymer (FRP) composites continue to revolutionize the sports and recreation industry, offering significant advantages in terms of performance, durability, and sustainability. This document highlights recent innovations and specific case studies showcasing the application of FRP in various sports equipment, with insights from industry resources.
The cycling industry has seen significant advancements in FRP applications, particularly in frame and wheel construction. These innovations align with the broader trend of composite materials in urban transport.
These innovations demonstrate the potential for automated fiber placement in automotive manufacturing, which could further revolutionize bicycle production.
FRP composites have found extensive applications in watersports equipment, benefiting from their lightweight and durable properties.
These developments showcase the potential for advanced material selection in composites in watersports applications.
FRP composites are making significant inroads in winter sports equipment and outdoor recreation gear, offering lightweight and durable solutions.
These innovations demonstrate the potential for composite materials in a circular world, promoting sustainable design in outdoor recreation products.
FRP composites are enhancing performance in running and other athletic pursuits through innovative shoe and apparel designs.
These developments showcase the potential for continuous fiber composites in various applications, including high-performance athletic wear.
FRP composites are making their mark in a variety of other sports, from racing to racquet sports.
These innovations demonstrate the wide-ranging applications of advanced composites manufacturing in sports equipment.
The sports and recreation industry is increasingly focusing on sustainability in FRP composite applications.
These initiatives align with the growing trend of embracing circular economy in composite materials, promoting sustainable growth in the industry.
The sports and recreation industry continues to benefit from advancements in FRP composite materials and manufacturing techniques. As composite design for manufacturability evolves, we can expect to see even more innovative applications in the future, pushing the boundaries of performance, durability, and sustainability in sports equipment.
Fiber Reinforced Polymer (FRP) composites have found innovative applications in various specialized fields, showcasing their versatility and unique properties. This section explores the use of FRP in prosthetics, anthropomorphic robotics, machine tools, and electro-thermal applications.
FRP composites have revolutionized the field of prosthetics, particularly for Paralympic athletes:
FRP composites play a significant role in the development of humanoid and industrial robots:
Explore the future of robotics with composite materials
FRP composites have found applications in various industrial machines:
Discover innovations in composite materials for real-world applications
FRP composites are increasingly used in electronic and thermal management applications:
Learn about the shift in composite manufacturing from traditional to intelligent methods
These advanced applications demonstrate the versatility and potential of FRP composites in addressing complex engineering challenges across diverse fields. As technology continues to evolve, FRP composites are expected to play an increasingly critical role in enabling more efficient, lightweight, and high-performance solutions in prosthetics, robotics, industrial machinery, and electronics.
Explore more about where composites are used in various industries
Zheng, K., et al. (2023). "A robot intelligent polishing system for fiber reinforced plastics (FRP) material combined with online measurement". The International Journal of Advanced Manufacturing Technology, 1-14.