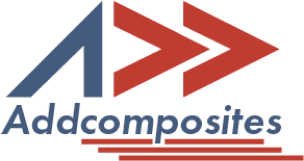
A hydrogen tank, also known as a hydrogen cylinder or hydrogen storage vessel, is a specialized container designed to store hydrogen gas under high pressure. These tanks play a crucial role in the hydrogen economy, enabling the storage and transportation of hydrogen for various applications, from fuel cell vehicles to industrial processes.
Key Features of Hydrogen Tanks:
The industry classifies hydrogen tanks into five main types, each with unique characteristics and applications:
Type I: All-Metal Tanks
Type II: Metal Liner with Composite Hoop Wrap
Type III: Metal Liner with Full Composite Wrap
Type IV: Polymer Liner with Full Composite Wrap
Type V: Linerless All-Composite
For a more detailed comparison of these tank types, refer to our article on Types of Hydrogen Tanks: Technological Differences and Advantages Explained.
The manufacturing process varies depending on the tank type:
Learn more about these manufacturing techniques in our chapter on composite manufacturing methods.
Selecting the appropriate tank type depends on several factors:
For guidance on material selection, refer to our guide on How to Select the Right Hydrogen Tanks Liners, Matrix, and Fiber Materials.
As we continue to innovate in the field of hydrogen storage, we're seeing exciting developments:
Understanding the different types of hydrogen tanks is crucial for designing and developing sustainable compressed hydrogen storage solutions. Each type offers unique advantages and challenges, and the choice depends on the specific application and requirements.
In the next chapters of our Design and Development of Sustainable Compressed Hydrogen Storage Tank course, we'll explore the manufacturing techniques, material selection, and design optimization for these advanced storage systems.
Ready to dive deeper into the world of hydrogen storage? Continue to the next chapter where we'll discuss the manufacturing techniques for composite hydrogen tanks.
The above article is part of the course Design and Development of Compressed Hydrogen Storage Tanks. The course covers a lot more, starting with discussing challenges in material selection and manufacturing practices, as well as cutting-edge trends being explored. Key problems in the design and analysis of the hydrogen reservoir are also addressed. Finally, testing and certification requirements are discussed as they play an important role in industry acceptance.