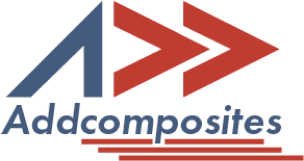
In recent years, there has been a growing awareness of environmental concerns and a push towards more sustainable materials in various industries. This trend has led to increased interest in natural fiber composites (NFCs), which offer a promising alternative to traditional synthetic fiber-reinforced materials.
Natural fiber composites are a class of materials that combine natural fibers with a polymer matrix to create a composite material with unique properties. These composites aim to harness the strengths of natural fibers while addressing some of the limitations of traditional synthetic composites.
The use of natural fibers in composites is not a new concept. In fact, people have been using natural fibers mixed with other materials for centuries. However, recent advancements in materials science and manufacturing processes have opened up new possibilities for NFCs in modern engineering applications.
As we explore the world of natural fiber composites, we'll delve into their basic composition, properties, manufacturing processes, and potential applications. We'll also discuss the challenges and future prospects of these materials in various industries, from automotive to aerospace.
For those interested in the broader context of composite materials, our introduction to composite materials provides a comprehensive overview of the field.
Join us on this journey as we uncover the potential of natural fiber composites and their role in shaping a more sustainable future for materials engineering.
Natural Fiber Composites (NFCs) are a class of composite materials that combine natural fibers with a polymer matrix. These materials aim to leverage the unique properties of natural fibers while addressing some of the limitations of traditional synthetic composites.
NFCs typically consist of two main components:
For a deeper understanding of composite materials and their components, you can refer to our comprehensive guide on composite materials.
Natural fibers used in composites can be broadly classified into two categories:
Plant-based fibers are more commonly used in NFCs due to their abundance, renewability, and relatively low cost. To learn more about different types of fibers used in composites, check out our article on fiber reinforcements.
The matrix in NFCs can be either:
For a more detailed comparison of thermoset and thermoplastic resins, visit our page on thermoplastic vs thermoset resins in FRP composites.
Natural Fiber Composites offer a unique combination of properties that make them attractive for various applications. In the following sections, we'll explore their characteristics, manufacturing processes, and potential uses in different industries.
Natural Fiber Composites (NFCs) possess a unique set of properties that distinguish them from traditional synthetic fiber composites. Understanding these characteristics is crucial for determining their suitability for various applications.
NFCs exhibit a range of mechanical properties that can vary based on the type of fiber, matrix, and manufacturing process used:
For a deeper dive into mechanical testing of composites, including NFCs, check out our article on mechanical testing of composites.
The properties of NFCs are significantly influenced by their chemical composition:
Understanding this composition is crucial for optimizing NFC performance. Our post on advanced material selection in composites provides more insights into material considerations.
To learn more about addressing some of these challenges, visit our page on challenges of switching to composite materials.
Understanding these characteristics is essential for designing and manufacturing NFCs effectively. In the next sections, we'll explore how these properties influence the manufacturing processes and applications of Natural Fiber Composites.
The production of Natural Fiber Composites (NFCs) involves various manufacturing techniques, each with its own advantages and considerations. The choice of process depends on factors such as the desired product shape, production volume, and required properties.
For a comprehensive look at composite manufacturing processes, including those suitable for NFCs, check out our fundamentals of composites manufacturing guide.
Advanced manufacturing techniques are being adapted for NFC production:
Understanding these manufacturing processes is crucial for optimizing NFC production and properties. In the next section, we'll explore the various applications of Natural Fiber Composites across different industries.
Natural Fiber Composites (NFCs) have found their way into various industries due to their unique properties, sustainability, and cost-effectiveness. Let's explore some key application areas:
The automotive sector has been one of the early adopters of NFCs, primarily for interior components:
NFCs help reduce vehicle weight, improve fuel efficiency, and enhance the sustainability profile of automobiles. For more on composites in automotive applications, see our article on driving forward with composite materials in automotive innovation.
NFCs are increasingly used in the construction industry for:
These applications benefit from NFCs' low density, good thermal insulation properties, and resistance to rot and decay.
NFCs have found applications in various consumer products:
The use of NFCs in these applications often aligns with consumer preferences for eco-friendly products. Learn more about sustainable composites in our post on sustainable manufacturing with natural fiber thermoplastic composites.
While not as widespread as in automotive applications, NFCs are being explored for non-structural components in aerospace:
For more on composites in aerospace, check our article on applications and limitations of composite materials in aerospace engineering.
NFCs are finding use in the marine industry for:
Their resistance to saltwater and lower water absorption compared to wood make them attractive for these applications.
NFCs are being used in:
Their low dielectric constant and loss factor make them suitable for these applications.
As technology advances and sustainability becomes increasingly important, we can expect to see NFCs in even more diverse applications. The next section will discuss the factors affecting the performance of Natural Fiber Composites in these various applications.
The performance of Natural Fiber Composites (NFCs) is influenced by various factors, from the selection of raw materials to the manufacturing processes used. Understanding these factors is crucial for optimizing NFC properties for specific applications.
The interface between fibers and matrix is critical for stress transfer and overall composite performance:
For more on bonding in composites, see our article on joining composite materials.
For insights on quality control in composite manufacturing, check our post on composites manufacturing: tracking and reducing waste.
Understanding and controlling these factors is essential for designing and producing NFCs with optimal performance for specific applications. In the next section, we'll explore methods for enhancing Natural Fiber Composite properties.
To overcome some of the limitations of Natural Fiber Composites (NFCs) and expand their potential applications, various methods have been developed to enhance their properties. These techniques focus on improving fiber-matrix compatibility, reducing moisture sensitivity, and enhancing overall performance.
For more on fiber modifications, see our article on fiber reinforcements.
Our post on advanced material selection in composites provides more insights into material additives.
Combining natural fibers with synthetic fibers can lead to improved mechanical properties and reduced moisture sensitivity:
This approach can offer a balance between performance and sustainability. Learn more about hybrid composites in our article on innovations in composite materials.
Incorporating nanoparticles or nanofibers can enhance various properties of NFCs:
Developing and using bio-based matrices that are more compatible with natural fibers can lead to improved interfacial bonding and overall composite performance. This also enhances the sustainability profile of the composites.
For more on fabric designs, see our article on reinforcement fibers: terminology, types, and formats.
By employing these enhancement methods, researchers and manufacturers can significantly improve the performance of NFCs, making them suitable for a wider range of applications. The next section will discuss the environmental impact and sustainability aspects of Natural Fiber Composites.
Natural Fiber Composites (NFCs) are often touted for their environmental benefits. However, a comprehensive understanding of their sustainability requires considering various factors throughout their lifecycle.
For more on sustainable materials in composites, check our article on sustainable manufacturing with natural fiber thermoplastic composites.
LCA is crucial for understanding the true environmental impact of NFCs:
Our post on composite materials in a circular world provides insights into sustainable design considerations.
NFCs often have a lower carbon footprint compared to traditional composites:
The recyclability of NFCs varies depending on the matrix material:
For more on recycling composites, see our article on manufacturing and recycling of carbon fiber thermoplastic composites.
While natural fibers are renewable, their production can have environmental impacts:
Adopting sustainable manufacturing practices can further enhance the environmental profile of NFCs:
Our post on the shift in composite manufacturing from traditional to intelligent discusses advanced, more sustainable manufacturing approaches.
Various certifications and regulations are emerging to validate the environmental claims of NFCs:
Understanding these aspects is crucial for companies looking to market NFCs as environmentally friendly alternatives.
While NFCs offer significant potential for improving the sustainability of composite materials, it's important to consider their entire lifecycle and continue research into optimizing their environmental performance. The next section will discuss the challenges and limitations of Natural Fiber Composites.
While Natural Fiber Composites (NFCs) offer numerous benefits, they also face several challenges and limitations that need to be addressed for wider adoption across industries.
For insights on managing material variability, see our article on advanced material selection in composites.
Our post on challenges of switching to composite materials discusses moisture-related issues in detail.
For a comparison of properties, check our introduction to composite materials.
Our article on fundamentals of composites manufacturing covers various processing considerations.
For more on composites in advanced applications, see our post on applications and limitations of composite materials in aerospace engineering.
Our article on embracing circular economy in composite materials discusses end-of-life considerations.
Addressing these challenges is crucial for the continued development and adoption of NFCs. Ongoing research and development efforts are focused on overcoming these limitations to expand the potential applications of Natural Fiber Composites. The next section will explore future potentials and research directions in the field of NFCs.
As technology advances and sustainability becomes increasingly important, Natural Fiber Composites (NFCs) are poised for significant developments. Here are some key areas of future potential and ongoing research:
For insights on matrix developments, see our article on thermoplastic vs thermoset resins in FRP composites.
Our post on embracing circular economy in composite materials provides insights into this area.
For more on AI in composites, check our article on machine learning to optimize AFP composite production.
As research in these areas progresses, we can expect to see Natural Fiber Composites playing an increasingly important role in various industries, offering sustainable alternatives to traditional materials while meeting demanding performance requirements.
Addcomposites. (n.d.). Challenges of Switching to Composite Materials. Retrieved from https://www.addcomposites.com/post/challenges-of-switching-to-composite-materials