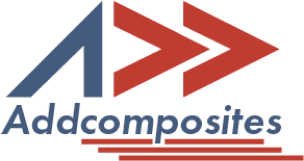
Vacuum-assisted Resin Transfer Molding (VARTM) is a closed-mold process that has revolutionized the manufacturing of fiber-reinforced polymer (FRP) composite parts. This chapter introduces the basic concepts of VARTM, its historical development, and how it compares to other composite manufacturing processes.
VARTM is a manufacturing process that combines the benefits of traditional Resin Transfer Molding (RTM) with the advantages of open-mold hand layup processing. The process involves the following key elements:
Learn more about composite materials
In VARTM, the pressure difference between the environmental (atmospheric) pressure and the vacuum pressure is utilized to compact the fiber preform and draw the resin into the mold. This unique approach allows for the production of high-quality, large-scale composite parts with relatively low tooling costs.
VARTM has been developed over the past two decades as an evolution of traditional RTM processes. Key milestones include:
These advancements have led to VARTM becoming a widely adopted process in various industries, including marine, aerospace, automotive, and renewable energy.
VARTM offers several advantages over traditional composite manufacturing methods:
Explore challenges in switching to composite materials
VARTM combines the following key benefits:
However, VARTM also has some limitations:
Despite these challenges, VARTM has become a preferred method for manufacturing large composite parts in many industries due to its versatility and cost-effectiveness.
Discover more about composites manufacturing methods
In the following chapters, we will delve deeper into the fundamentals of VARTM, explore the process setup and procedure, and discuss the critical elements of VARTM process design.
Understanding the fundamental principles behind Vacuum-assisted Resin Transfer Molding (VARTM) is crucial for optimizing the process and producing high-quality composite parts. This chapter explores the key physical phenomena that govern the VARTM process.
The resin flow in VARTM is governed by Darcy's law, which describes fluid flow through porous media. The generalized Darcy's law is given by:
u_D = -(K/μ) * ∇P
Where:
Continuity equation:
∇ · u_D = 0
Learn more about resin flow in composite manufacturing
Key aspects of resin flow in VARTM include:
Fiber preform compaction is a critical aspect of VARTM that affects the final part quality and fiber volume fraction. The relationship between compaction pressure and fiber volume fraction can be described by models such as:
P_comp = A * ((V_f - V_f0) / (V_f∞ - V_f))^4
V_f = V_f1 * P_comp^BWhere:
Where:
Explore more about fiber reinforcements
Compaction affects:
Resin viscosity plays a crucial role in the VARTM process, affecting flow behavior and filling time. The viscosity of thermoset resins used in VARTM is typically modeled as a function of temperature and degree of cure:
μ = μ_0 * exp(E/(R*T)) * exp(a_c * α)
Where:
Key considerations for resin viscosity in VARTM:
The curing process in VARTM involves complex heat transfer and chemical reactions. The one-dimensional energy balance equation for the curing process is:
ρ_c * c_pc * ∂T/∂t = ∂/∂z(k_czz * ∂T/∂z) + ρ_r * ε_r * H_r * ∂α/∂t
Where:
The cure kinetics can be modeled using equations such as:
∂α/∂t = A * exp(-E/(R*T)) * α^m * (1-α)^n
Where A, E, m, and n are cure kinetic parameters.
Learn about composite curing and processing
Important aspects of curing in VARTM:
Understanding these fundamental principles allows for better process control and optimization in VARTM, leading to improved part quality and reduced manufacturing defects.
The Vacuum-assisted Resin Transfer Molding (VARTM) process requires careful setup and execution to produce high-quality composite parts. This chapter provides a detailed guide to the VARTM process setup and procedure, highlighting key steps and considerations.
A typical VARTM setup consists of the following components:
Follow these steps to set up and execute a VARTM process:
Explore composites manufacturing methods
To ensure a successful VARTM process, keep the following points in mind:
Learn about process monitoring in composites manufacturing
By carefully following these steps and considering the key points, you can successfully execute a VARTM process to produce high-quality composite parts. The next chapter will delve into the critical elements of VARTM process design, which will help you optimize your setup for specific applications.
Vacuum-assisted Resin Transfer Molding (VARTM) has gained popularity in various industries due to its unique combination of benefits. However, like any manufacturing process, it also has its limitations. This chapter explores the advantages and disadvantages of VARTM, providing a balanced view of its capabilities and challenges.
VARTM offers several significant benefits that make it an attractive option for composite manufacturing:
Learn more about advantages of composite materials
Despite its many advantages, VARTM also has some limitations and challenges:
Explore challenges in composite manufacturing
To better understand the position of VARTM in the landscape of composite manufacturing, let's compare it with other common processes:
Learn about various composites manufacturing methods
VARTM offers a unique combination of benefits, making it particularly suitable for large, complex composite parts where cost-effectiveness is crucial. Its main advantages lie in its flexibility, scalability, and relatively low tooling costs. However, users must be aware of its limitations, particularly in terms of air leakage risks and fiber volume fraction control.
By understanding these advantages and disadvantages, manufacturers can make informed decisions about when to use VARTM and how to optimize the process for their specific applications. As technology continues to advance, many of the current limitations of VARTM are being addressed through innovations in materials, process control, and simulation tools.
Successful implementation of Vacuum-assisted Resin Transfer Molding (VARTM) requires careful consideration of several critical elements. This chapter focuses on three key aspects of VARTM process design: mold temperature selection, flow process design, and fiber preform compaction and fiber volume fraction control.
Mold temperature plays a crucial role in VARTM process optimization, affecting various aspects of the manufacturing process and final part quality.
Learn more about composite curing processes
Optimizing the resin flow process is critical for achieving complete wet-out and minimizing defects in VARTM parts.
Utilizing flow simulation software can help optimize the VARTM process:
Explore flow process design in composite manufacturing
Achieving the desired fiber volume fraction and maintaining uniform part thickness are critical for part quality and performance.
Utilize compaction models to predict and control fiber volume fraction:
Learn about fiber reinforcements in composites
Successful VARTM process design requires the integration of these critical elements:
By carefully considering and optimizing these critical elements, manufacturers can design robust VARTM processes that consistently produce high-quality composite parts.
Despite its many advantages, Vacuum-assisted Resin Transfer Molding (VARTM) can present several challenges that may lead to defects in the final composite part. This chapter explores four major areas of concern: air entrapment and dry spots, thickness and fiber volume fraction uniformity, curing and thermal management, and the spring-in phenomenon.
Air entrapment and dry spots are common issues in VARTM that can significantly impact the quality and performance of the final part.
Learn more about defects in composite materials
Achieving consistent part thickness and fiber volume fraction across large or complex parts can be challenging in VARTM.
Explore composite manufacturing process control
Proper curing and thermal management are crucial for producing high-quality VARTM parts, especially for thick or large components.
Learn about curing in composite manufacturing
Spring-in is a common dimensional accuracy issue in curved composite parts manufactured using VARTM.
Explore challenges in composite manufacturing
Understanding and addressing these defects and challenges is crucial for successful implementation of VARTM in industrial applications. By employing advanced process control, simulation tools, and innovative material solutions, manufacturers can mitigate these issues and produce high-quality, dimensionally accurate composite parts using VARTM.
Vacuum-assisted Resin Transfer Molding (VARTM) continues to evolve, with recent advancements addressing sustainability concerns, enhancing material properties, and improving process efficiency. This chapter explores three key areas of recent development: green composites and bio-based materials, nanocomposites manufacturing, and process variations for improved performance.
The growing emphasis on sustainability has led to increased interest in green composites and bio-based materials in VARTM processes.
Learn more about natural fiber composites
The incorporation of nanomaterials in VARTM processes has opened new avenues for enhancing composite properties and functionality.
Explore innovations in composite materials
Continuous innovation in VARTM processes has led to several variations aimed at enhancing part quality, reducing cycle times, and expanding application ranges.
Learn about advanced manufacturing techniques
These recent advances in VARTM technology demonstrate the process's adaptability and potential for future growth. The integration of sustainable materials, nanomaterials, and innovative process variations is expanding the capabilities of VARTM, making it an increasingly attractive option for a wide range of applications. As research continues, we can expect further improvements in part quality, process efficiency, and the environmental impact of composite manufacturing using VARTM techniques.
The Vacuum-Assisted Process (VAP) is an innovative variation of VARTM that incorporates a semi-permeable membrane to enhance process control and part quality. This chapter explores the VAP process, its unique characteristics, and the benefits it offers over traditional VARTM.
VAP introduces a crucial modification to the standard VARTM setup by incorporating a membrane layer that is permeable to gases but impermeable to resin.
The typical VAP layup consists of the following components (from bottom to top):
Learn more about VARTM process variations
The success of the VAP process heavily relies on the properties and performance of the semi-permeable membrane.
Membrane performance can be modeled based on:
Explore advanced materials in composite manufacturing
The VAP process offers several advantages over standard VARTM, leading to improvements in both the manufacturing process and the final part properties.
Key observations:
Learn about process optimization in composite manufacturing
The Vacuum-Assisted Process (VAP) represents a significant advancement in VARTM technology. By incorporating a semi-permeable membrane, VAP offers improved process control, reduced defects, and enhanced material properties. As membrane technology continues to evolve and process optimization techniques advance, VAP is likely to find increasing application in the production of high-performance composite parts, particularly in industries demanding high quality and consistency, such as aerospace and automotive.
As Vacuum-assisted Resin Transfer Molding (VARTM) continues to evolve, new applications emerge, and research drives further improvements. This chapter explores the future of VARTM technology, highlighting emerging applications, ongoing research and development efforts, and potential areas for process enhancement.
VARTM's versatility and cost-effectiveness are opening doors to new applications across various industries.
Explore innovations in composite materials applications
Continuous research efforts are driving VARTM technology forward, addressing current limitations and exploring new possibilities.
Learn about advancements in composite manufacturing
Several areas show promise for enhancing VARTM technology and expanding its capabilities.
Explore sustainable manufacturing in composites
VARTM technology stands at the forefront of advanced composite manufacturing, poised for continued growth and innovation. The emerging applications across aerospace, renewable energy, automotive, and infrastructure sectors highlight the versatility and potential of this process. Ongoing research in areas such as advanced simulation, smart manufacturing technologies, and novel materials promises to address current limitations and unlock new possibilities.
The potential for further process improvements, particularly in areas of enhanced control, improved resin systems, automation, and sustainability, suggests that VARTM will continue to evolve and maintain its relevance in the composites industry. As these advancements materialize, we can expect to see VARTM playing an increasingly important role in the production of high-performance, cost-effective composite structures across a wide range of applications.
The future of VARTM lies in its ability to adapt to changing industry needs, incorporate cutting-edge technologies, and address growing sustainability concerns. By leveraging these opportunities and overcoming existing challenges, VARTM is set to remain a key player in shaping the future of composite manufacturing.
This chapter provides hands-on exercises and real-world case studies to reinforce the theoretical concepts of Vacuum-assisted Resin Transfer Molding (VARTM). Through these practical applications, readers will gain a deeper understanding of VARTM process design, troubleshooting, and industrial implementation.
In this exercise, we'll walk through the process of designing a VARTM setup for a simple flat panel.
Design a VARTM setup for a flat composite panel with the following specifications:
Calculate the required resin volume:
Resin volume = Part volume * (1 - Target Vf)
Resin volume = (500 mm * 500 mm * 5 mm) * (1 - 0.50) = 625,000 mm³ ≈ 625 mL
This section presents common VARTM issues and strategies to resolve them.
Problem: After infusion, a 10 cm diameter dry spot is observed near the vent.
Potential Causes and Solutions:
Problem: The cured part shows significant thickness variations, with the area near the injection point being thicker.
Potential Causes and Solutions:
Problem: Microscopic analysis reveals high void content (>2%) throughout the part.
Potential Causes and Solutions:
Explore defects in composite materials
This section examines case studies of VARTM applications in various industries.
Company: GreenWind Energy Solutions Component: 60-meter wind turbine blade
VARTM Implementation:
Challenges and Solutions:
Outcomes:
Company: AeroComposites Inc. Component: 3m x 2m fuselage panel with integrated stiffeners
VARTM Implementation:
Challenges and Solutions:
Outcomes:
Company: ElectroDrive Innovations Component: Electric vehicle battery enclosure (1.8m x 1.2m x 0.3m)
VARTM Implementation:
Challenges and Solutions:
Outcomes:
Explore composite applications in automotive industry
These practical exercises and case studies demonstrate the versatility and potential of VARTM in various applications. By working through the design exercise, troubleshooting scenarios, and analyzing real-world implementations, readers can gain valuable insights into the practical aspects of VARTM processing. The ability to adapt the VARTM process to different scales, geometries, and performance requirements highlights its continued relevance in advanced composite manufacturing.
As the technology continues to evolve, with innovations in materials, process control, and automation, VARTM is expected to play an increasingly important role in producing high-performance, cost-effective composite structures across multiple industries.