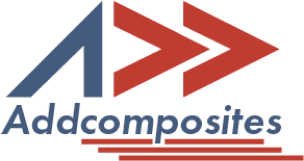
Pressure vessels are an essential component of many industrial processes, including chemical and petroleum refining, power generation, and aerospace applications. Designing and manufacturing pressure vessels require precise control over material placement, and the use of automated fiber placement (AFP) technologies can streamline the manufacturing process while ensuring quality components.
A recent webinar hosted by AddPath, a leading provider of AFP software solutions, provided valuable insights into how to use AFP technologies to optimize pressure vessel design and manufacturing. In this blog post, we summarize the key takeaways from the webinar.
The webinar was presented by James and Pravin, two experts in the field with extensive experience in the aerospace and composites industry. James is a technical sales specialist at Addcomposites, while Pravin is a composites expert and CEO at Addcomposites. The webinar video is linked below
The first part of the webinar focused on using AddPath for filament winding, which allows precise control over material placement and reduces material waste. The speakers explained that traditional filament winding processes can be limiting in terms of design optimization and material control, making AddPath an attractive solution.
The simulation process using AddPath was demonstrated, including setting up the home position and using the slider to move past each winding. Attendees were able to see the simulation in action, and the speakers mentioned that the files used in the simulation are available for attendees to play around with on their own. Overall, the first part of the webinar provided an informative introduction to the benefits of using AddPath for filament winding.
The second part of the webinar highlighted how AddPath can be used for selective reinforcement. Selective reinforcement is a process that allows for more precise material placement and reduces the amount of material needed.
The simulation process for selective reinforcement using AddPath is similar to filament winding. However, instead of selecting the full mold, a specific area is selected, and a boundary is set up. The discontinuous winding path is chosen, and a periphery is selected. The difference in this process is that the tape is cut, allowing for selective reinforcement.
The process of using AddPath for selective reinforcement includes importing curves and using user-made tool paths. AddPath's steering feature allows users to analyze steering radii and adjust material placement accordingly. This enables users to ensure that the fiber will not peel off the surface and that the component will be strong and durable.
The ability to do selective reinforcement using AddPath is a significant advantage for manufacturers as it allows them to optimize material usage while ensuring high-quality components.
The third part of the webinar focused on using AddPath for thermoplastic materials. The speakers explained the benefits of using thermoplastics, such as their recyclability and sustainability. With the use of AddPath, users can easily switch between materials based on their project requirements. This feature allows for greater flexibility and the ability to adapt to changing project needs.
The speakers emphasized that AFP technology allows for greater versatility in material choice, not limited to carbon or glass fibers but also including the matrix material used. They explained that AFP technology is ideal for sustainable travel and aviation, where thermoplastics can be utilized for their recyclability and reduced shelf-life waste.
Using AddPath for thermoplastic materials offers greater control over the manufacturing process, resulting in more efficient and sustainable production. By switching between materials, users can optimize their designs and reduce material waste.
The webinar provided valuable insights into the benefits of using AddPath for pressure vessel design and manufacturing. The speakers highlighted how AddPath can be used for filament winding, selective reinforcement, and thermoplastic materials, offering greater control and precision in the manufacturing process.
Attendees were also able to see AddPath in action through live demonstrations and simulations. Overall, the webinar showcased how AddPath can improve the efficiency and sustainability of pressure vessel design and manufacturing.
For those interested in trying AddPath, the speakers announced that a three-month license is included. They also thanked attendees for their time and encouraged them to share their learnings with others who may be interested in using AddPath for pressure vessel design and manufacturing.
Pressure vessels are an essential component of many industrial processes, including chemical and petroleum refining, power generation, and aerospace applications. Designing and manufacturing pressure vessels require precise control over material placement, and the use of automated fiber placement (AFP) technologies can streamline the manufacturing process while ensuring quality components.
A recent webinar hosted by AddPath, a leading provider of AFP software solutions, provided valuable insights into how to use AFP technologies to optimize pressure vessel design and manufacturing. In this blog post, we summarize the key takeaways from the webinar.
The webinar was presented by James and Pravin, two experts in the field with extensive experience in the aerospace and composites industry. James is a technical sales specialist at Addcomposites, while Pravin is a composites expert and CEO at Addcomposites. The webinar video is linked below
The first part of the webinar focused on using AddPath for filament winding, which allows precise control over material placement and reduces material waste. The speakers explained that traditional filament winding processes can be limiting in terms of design optimization and material control, making AddPath an attractive solution.
The simulation process using AddPath was demonstrated, including setting up the home position and using the slider to move past each winding. Attendees were able to see the simulation in action, and the speakers mentioned that the files used in the simulation are available for attendees to play around with on their own. Overall, the first part of the webinar provided an informative introduction to the benefits of using AddPath for filament winding.
The second part of the webinar highlighted how AddPath can be used for selective reinforcement. Selective reinforcement is a process that allows for more precise material placement and reduces the amount of material needed.
The simulation process for selective reinforcement using AddPath is similar to filament winding. However, instead of selecting the full mold, a specific area is selected, and a boundary is set up. The discontinuous winding path is chosen, and a periphery is selected. The difference in this process is that the tape is cut, allowing for selective reinforcement.
The process of using AddPath for selective reinforcement includes importing curves and using user-made tool paths. AddPath's steering feature allows users to analyze steering radii and adjust material placement accordingly. This enables users to ensure that the fiber will not peel off the surface and that the component will be strong and durable.
The ability to do selective reinforcement using AddPath is a significant advantage for manufacturers as it allows them to optimize material usage while ensuring high-quality components.
The third part of the webinar focused on using AddPath for thermoplastic materials. The speakers explained the benefits of using thermoplastics, such as their recyclability and sustainability. With the use of AddPath, users can easily switch between materials based on their project requirements. This feature allows for greater flexibility and the ability to adapt to changing project needs.
The speakers emphasized that AFP technology allows for greater versatility in material choice, not limited to carbon or glass fibers but also including the matrix material used. They explained that AFP technology is ideal for sustainable travel and aviation, where thermoplastics can be utilized for their recyclability and reduced shelf-life waste.
Using AddPath for thermoplastic materials offers greater control over the manufacturing process, resulting in more efficient and sustainable production. By switching between materials, users can optimize their designs and reduce material waste.
The webinar provided valuable insights into the benefits of using AddPath for pressure vessel design and manufacturing. The speakers highlighted how AddPath can be used for filament winding, selective reinforcement, and thermoplastic materials, offering greater control and precision in the manufacturing process.
Attendees were also able to see AddPath in action through live demonstrations and simulations. Overall, the webinar showcased how AddPath can improve the efficiency and sustainability of pressure vessel design and manufacturing.
For those interested in trying AddPath, the speakers announced that a three-month license is included. They also thanked attendees for their time and encouraged them to share their learnings with others who may be interested in using AddPath for pressure vessel design and manufacturing.