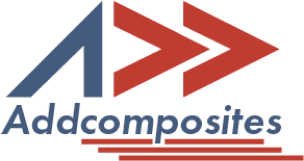
Welcome to our blog post on metal and ceramic matrix composites in aerospace engineering! In this article, we will explore the significance and applications of these composite materials, providing a comprehensive overview. So, let's dive in!
Composite materials have revolutionized the aerospace industry, enabling the development of lightweight and high-performance structures. Metal Matrix Composites (MMCs) and Ceramic Matrix Composites (CMCs) are two types of composites that have garnered considerable attention for their exceptional properties and versatility.
Understanding the properties, applications, and ongoing developments in metal and ceramic matrix composites is essential for aspiring aerospace engineers. In this blog post, we will delve deeper into the characteristics, types, and applications of these composites, shedding light on their significance in the field.
So, let's explore the fascinating world of metal and ceramic matrix composites in aerospace engineering and discover the exciting possibilities they offer for the future of aircraft design and manufacturing!
Ceramic Matrix Composites, often abbreviated as CMCs, are a type of composite material that has gained significant attention in the aerospace industry due to their unique properties. They are particularly known for their high fracture toughness, resistance to catastrophic failure, high strength, lightweight, low thermal expansion, and ability to withstand high temperatures with high oxidation resistance.
Let's break down some of these characteristics:
CMCs are typically composed of ceramic fibers embedded in a ceramic matrix. The fibers and the matrix can withstand high temperatures, making CMCs ideal for applications that require thermal resistance.
The bonds present in ceramics can be of two types: ionic and covalent. Ionic bonding occurs between metallic and nonmetallic elements, while covalent bonding happens when atoms share electrons.
Common types of reinforcements for CMCs include silicon carbide (SiC), titanium carbide (TiC), boron carbide (B4C), silicon nitrides (Si3N4), boron nitrides (BN), alumina (Al2O3), zirconia (ZrO2), and carbon (graphite or partially amorphous) and boron. These reinforcements enhance the overall properties of the CMCs.
Understanding the properties and composition of CMCs is crucial for their effective use in aerospace engineering. As we continue to innovate and push the boundaries of what's possible in aerospace, CMCs will undoubtedly play a key role in the future of this exciting field.
In composite materials, the matrix plays a crucial role in determining the overall properties of the material. It binds the reinforcement together, transfers stresses between the reinforcing fibers/particles, and protects the reinforcement from environmental damage. Let's take a closer look at the types of matrices used in composites, with a particular focus on ceramic matrices.
Ceramic matrices are commonly used in both Ceramic Matrix Composites (CMCs) and Metal Matrix Composites (MMCs). They are nonmetallic inorganic materials, composed of metallic and nonmetallic elements connected by ionic and/or covalent bonds.
Some of the common ceramic matrices include:
The fiber-matrix interfacial domain is the region where the fibers (or particles) and the matrix material interact. This interface plays a crucial role in determining the overall properties of the composite. It can consist of an interface or an interphase. Interphase implies the presence of at least two interfaces: one with the matrix and one with the fiber, and more when the interphase consists of a multilayer.
Understanding the types of matrices used in composites and the role of the fiber-matrix interface is crucial for anyone working with these materials. As we continue to innovate and develop new composite materials, the choice of matrix and the design of the fiber-matrix interface will continue to play a key role in determining the properties and potential applications of these materials.
Metal Matrix Composites, often referred to as MMCs, are another category of composite materials that have found extensive use in the aerospace industry. They are made up of a metal matrix that is reinforced with a different material, often ceramic particles or fibers, carbon fibers, or metallic fibers.
Here are some key characteristics of MMCs:
MMCs are typically made using a variety of metallic matrices. Some of the most common ones include aluminum, magnesium, titanium, and copper. The choice of matrix material depends on the specific requirements of the application. The reinforcements used in MMCs can be ceramic particles or fibers, carbon fibers, or metallic fibers. These reinforcements enhance the overall properties of the MMCs, making them stronger, stiffer, and more resistant to heat and wear.
There are several processing techniques used to manufacture MMCs. Two of the most common ones are liquid metal processing and powder metallurgy. Liquid metal processing involves mixing the reinforcement material with molten metal, while powder metallurgy involves mixing metal powder with the reinforcement material and then heating the mixture to form a solid composite. Understanding the properties and composition of MMCs is crucial for their effective use in aerospace engineering. As we continue to innovate and push the boundaries of what's possible in aerospace, MMCs will undoubtedly play a key role in the future of this exciting field.
MMCs have a wide range of applications due to their unique properties such as high strength, high ductility, and resistance to high temperatures. They are used in various industries, including the aerospace industry, where their properties are particularly beneficial.
MMCs are used in a variety of applications, including:
Research is ongoing to further improve the properties of MMCs and expand their potential applications. Some of the current research objectives include:
Understanding the applications and current research objectives of MMCs is crucial for recent graduates in the industry. As we continue to innovate and push the boundaries of what's possible in aerospace, MMCs will undoubtedly play a key role in the future of this exciting field.
Metal Matrix Composites (MMCs) and Ceramic Matrix Composites (CMCs) have emerged as crucial materials in the field of aerospace engineering. Their unique properties and versatility make them highly desirable for various applications. Let's recap the importance and applications of these composites and explore future prospects in the field.
The field of composite materials in aerospace engineering continues to evolve, and future prospects are promising. Here are some developments to look forward to:
Commercialization of CMCs and developments for next-gen performance
Welcome to our blog post on metal and ceramic matrix composites in aerospace engineering! In this article, we will explore the significance and applications of these composite materials, providing a comprehensive overview. So, let's dive in!
Composite materials have revolutionized the aerospace industry, enabling the development of lightweight and high-performance structures. Metal Matrix Composites (MMCs) and Ceramic Matrix Composites (CMCs) are two types of composites that have garnered considerable attention for their exceptional properties and versatility.
Understanding the properties, applications, and ongoing developments in metal and ceramic matrix composites is essential for aspiring aerospace engineers. In this blog post, we will delve deeper into the characteristics, types, and applications of these composites, shedding light on their significance in the field.
So, let's explore the fascinating world of metal and ceramic matrix composites in aerospace engineering and discover the exciting possibilities they offer for the future of aircraft design and manufacturing!
Ceramic Matrix Composites, often abbreviated as CMCs, are a type of composite material that has gained significant attention in the aerospace industry due to their unique properties. They are particularly known for their high fracture toughness, resistance to catastrophic failure, high strength, lightweight, low thermal expansion, and ability to withstand high temperatures with high oxidation resistance.
Let's break down some of these characteristics:
CMCs are typically composed of ceramic fibers embedded in a ceramic matrix. The fibers and the matrix can withstand high temperatures, making CMCs ideal for applications that require thermal resistance.
The bonds present in ceramics can be of two types: ionic and covalent. Ionic bonding occurs between metallic and nonmetallic elements, while covalent bonding happens when atoms share electrons.
Common types of reinforcements for CMCs include silicon carbide (SiC), titanium carbide (TiC), boron carbide (B4C), silicon nitrides (Si3N4), boron nitrides (BN), alumina (Al2O3), zirconia (ZrO2), and carbon (graphite or partially amorphous) and boron. These reinforcements enhance the overall properties of the CMCs.
Understanding the properties and composition of CMCs is crucial for their effective use in aerospace engineering. As we continue to innovate and push the boundaries of what's possible in aerospace, CMCs will undoubtedly play a key role in the future of this exciting field.
In composite materials, the matrix plays a crucial role in determining the overall properties of the material. It binds the reinforcement together, transfers stresses between the reinforcing fibers/particles, and protects the reinforcement from environmental damage. Let's take a closer look at the types of matrices used in composites, with a particular focus on ceramic matrices.
Ceramic matrices are commonly used in both Ceramic Matrix Composites (CMCs) and Metal Matrix Composites (MMCs). They are nonmetallic inorganic materials, composed of metallic and nonmetallic elements connected by ionic and/or covalent bonds.
Some of the common ceramic matrices include:
The fiber-matrix interfacial domain is the region where the fibers (or particles) and the matrix material interact. This interface plays a crucial role in determining the overall properties of the composite. It can consist of an interface or an interphase. Interphase implies the presence of at least two interfaces: one with the matrix and one with the fiber, and more when the interphase consists of a multilayer.
Understanding the types of matrices used in composites and the role of the fiber-matrix interface is crucial for anyone working with these materials. As we continue to innovate and develop new composite materials, the choice of matrix and the design of the fiber-matrix interface will continue to play a key role in determining the properties and potential applications of these materials.
Metal Matrix Composites, often referred to as MMCs, are another category of composite materials that have found extensive use in the aerospace industry. They are made up of a metal matrix that is reinforced with a different material, often ceramic particles or fibers, carbon fibers, or metallic fibers.
Here are some key characteristics of MMCs:
MMCs are typically made using a variety of metallic matrices. Some of the most common ones include aluminum, magnesium, titanium, and copper. The choice of matrix material depends on the specific requirements of the application. The reinforcements used in MMCs can be ceramic particles or fibers, carbon fibers, or metallic fibers. These reinforcements enhance the overall properties of the MMCs, making them stronger, stiffer, and more resistant to heat and wear.
There are several processing techniques used to manufacture MMCs. Two of the most common ones are liquid metal processing and powder metallurgy. Liquid metal processing involves mixing the reinforcement material with molten metal, while powder metallurgy involves mixing metal powder with the reinforcement material and then heating the mixture to form a solid composite. Understanding the properties and composition of MMCs is crucial for their effective use in aerospace engineering. As we continue to innovate and push the boundaries of what's possible in aerospace, MMCs will undoubtedly play a key role in the future of this exciting field.
MMCs have a wide range of applications due to their unique properties such as high strength, high ductility, and resistance to high temperatures. They are used in various industries, including the aerospace industry, where their properties are particularly beneficial.
MMCs are used in a variety of applications, including:
Research is ongoing to further improve the properties of MMCs and expand their potential applications. Some of the current research objectives include:
Understanding the applications and current research objectives of MMCs is crucial for recent graduates in the industry. As we continue to innovate and push the boundaries of what's possible in aerospace, MMCs will undoubtedly play a key role in the future of this exciting field.
Metal Matrix Composites (MMCs) and Ceramic Matrix Composites (CMCs) have emerged as crucial materials in the field of aerospace engineering. Their unique properties and versatility make them highly desirable for various applications. Let's recap the importance and applications of these composites and explore future prospects in the field.
The field of composite materials in aerospace engineering continues to evolve, and future prospects are promising. Here are some developments to look forward to:
Commercialization of CMCs and developments for next-gen performance