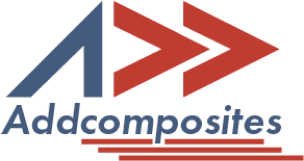
While Composites are hailed for their strength and versatility, did you know that even a tiny defect can compromise an entire structure? From invisible matrix cracks to the subtle aging of prepreg, these materials have their own set of vulnerabilities. But here's the twist: with the right knowledge and techniques, these issues can not only be detected but also repaired, restoring the composite to its original strength. Dive into our latest article to uncover the hidden world of composite materials and the unexpected challenges and solutions that come with them
Applications and Limitations of Composite Materials in Aerospace Engineering: A Comprehensive Guide : Composite materials are a vital part of aerospace engineering due to their lightweight, strong, and durable properties. Glass fiber, Kevlar, and carbon fiber are commonly used in the aerospace industry, along with matrix materials such as phenolic, polyester, and epoxy. Composite materials have been used in suborbital aerospace vehicles due to their lightweight and durability. However, these materials have limitations, and engineers must choose the right material for each application to ensure success.
Each of these defects can significantly impact the performance and reliability of composite materials. Understanding their causes, effects, and corrective measures is crucial for anyone working with or studying composites.
Understanding the loss of integrity in composite structures is essential for ensuring their safety and longevity. Proper detection, classification, and repair of defects can mitigate potential risks and extend the life of the structure.
Once damage or a defect has been identified and evaluated against appropriate criteria to determine the loss of structural or performance integrity, a repair scheme is developed. The development of a repair scheme needs to consider several practical implementation issues and review the specific repair requirements for successful design and installation.
The restitution of a defect or damage requires a good appreciation of the severity to determine the best repair scheme for the composite structure. Several factors impact the repair scheme selection and can drive the best structurally efficient repair design to a more complex repair design. For instance, using a flush repair because of aerodynamics when a doubler repair would be ideal for strength restoration.
The development of generic repair types in composite structures describes repairs for generalized defect/damage types, such as intralaminar matrix cracks, delaminations, and broken fibers. The repair design and installation requirements are crucial for ensuring the longevity and performance of the repaired composite structure.
There are four basic levels of generic repair designs: filling and sealing the damaged area (cosmetic), filling and applying a doubler patch to the damaged area (semi-structural), bonding a flush patch to the damaged area (structural), and bolting a patch to the damaged area (structural).
The defect/damage restoration can range from a simple low-viscosity resin infusion to a complex bolted repair scheme. The restoration of defects or damages is an essential requirement in the initial design of the structure. If the structure cannot be made damage-tolerant, then it needs to be inspectable. If defects/damages are found, then it needs to be designed for repair.
The concluding section provides an overview of the damage removal and repair scheme installation process. This includes a detailed discussion of surface preparation requirements and processes.
Composite materials, with their unique properties and advantages, have found extensive applications in various industries. However, like all materials, they are susceptible to defects and damages that can compromise their structural integrity. This article delved deep into:
In essence, while composite materials offer unparalleled benefits, it's imperative to understand, detect, and address their potential defects and damages. Proper detection, classification, and repair of these issues not only ensure the safety of structures but also extend their operational life. Whether you're a professional in the field or a student, a deep understanding of these aspects is crucial for the effective use and maintenance of composite materials.
Discover the future of composite manufacturing with Addcomposites! Here's how you can get involved:
At Addcomposites, we are dedicated to revolutionizing composite manufacturing. Our AFP systems and comprehensive support services are waiting for you to harness. So, don't wait – get started on your journey to the future of manufacturing today!
While Composites are hailed for their strength and versatility, did you know that even a tiny defect can compromise an entire structure? From invisible matrix cracks to the subtle aging of prepreg, these materials have their own set of vulnerabilities. But here's the twist: with the right knowledge and techniques, these issues can not only be detected but also repaired, restoring the composite to its original strength. Dive into our latest article to uncover the hidden world of composite materials and the unexpected challenges and solutions that come with them
Applications and Limitations of Composite Materials in Aerospace Engineering: A Comprehensive Guide : Composite materials are a vital part of aerospace engineering due to their lightweight, strong, and durable properties. Glass fiber, Kevlar, and carbon fiber are commonly used in the aerospace industry, along with matrix materials such as phenolic, polyester, and epoxy. Composite materials have been used in suborbital aerospace vehicles due to their lightweight and durability. However, these materials have limitations, and engineers must choose the right material for each application to ensure success.
Each of these defects can significantly impact the performance and reliability of composite materials. Understanding their causes, effects, and corrective measures is crucial for anyone working with or studying composites.
Understanding the loss of integrity in composite structures is essential for ensuring their safety and longevity. Proper detection, classification, and repair of defects can mitigate potential risks and extend the life of the structure.
Once damage or a defect has been identified and evaluated against appropriate criteria to determine the loss of structural or performance integrity, a repair scheme is developed. The development of a repair scheme needs to consider several practical implementation issues and review the specific repair requirements for successful design and installation.
The restitution of a defect or damage requires a good appreciation of the severity to determine the best repair scheme for the composite structure. Several factors impact the repair scheme selection and can drive the best structurally efficient repair design to a more complex repair design. For instance, using a flush repair because of aerodynamics when a doubler repair would be ideal for strength restoration.
The development of generic repair types in composite structures describes repairs for generalized defect/damage types, such as intralaminar matrix cracks, delaminations, and broken fibers. The repair design and installation requirements are crucial for ensuring the longevity and performance of the repaired composite structure.
There are four basic levels of generic repair designs: filling and sealing the damaged area (cosmetic), filling and applying a doubler patch to the damaged area (semi-structural), bonding a flush patch to the damaged area (structural), and bolting a patch to the damaged area (structural).
The defect/damage restoration can range from a simple low-viscosity resin infusion to a complex bolted repair scheme. The restoration of defects or damages is an essential requirement in the initial design of the structure. If the structure cannot be made damage-tolerant, then it needs to be inspectable. If defects/damages are found, then it needs to be designed for repair.
The concluding section provides an overview of the damage removal and repair scheme installation process. This includes a detailed discussion of surface preparation requirements and processes.
Composite materials, with their unique properties and advantages, have found extensive applications in various industries. However, like all materials, they are susceptible to defects and damages that can compromise their structural integrity. This article delved deep into:
In essence, while composite materials offer unparalleled benefits, it's imperative to understand, detect, and address their potential defects and damages. Proper detection, classification, and repair of these issues not only ensure the safety of structures but also extend their operational life. Whether you're a professional in the field or a student, a deep understanding of these aspects is crucial for the effective use and maintenance of composite materials.
Discover the future of composite manufacturing with Addcomposites! Here's how you can get involved:
At Addcomposites, we are dedicated to revolutionizing composite manufacturing. Our AFP systems and comprehensive support services are waiting for you to harness. So, don't wait – get started on your journey to the future of manufacturing today!