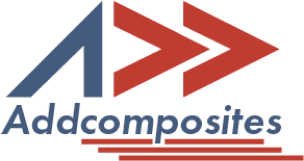
In the world of advanced manufacturing, Automated Fiber Placement (AFP) has emerged as a cornerstone technology for producing high-performance composite parts. From the latest generation of commercial airliners to cutting-edge space vehicles, AFP-manufactured components are increasingly prevalent in demanding applications where precision and reliability are paramount.
However, with great capability comes great complexity. One of the most persistent challenges in AFP manufacturing is the occurrence of gaps and overlaps during the layup process. These seemingly minor imperfections can have significant implications for part quality, structural integrity, and production efficiency.
Consider this striking statistic: inspection and rework activities consume approximately 32% of AFP cell time. That's nearly one-third of valuable production capacity dedicated to quality control and defect remediation. For manufacturers striving to meet growing demand and tight production schedules, this represents a significant bottleneck.
Defects in composite materials can manifest in various ways, but gaps and overlaps are particularly common in AFP processes. A gap occurs when adjacent tows (strips of composite material) don't touch each other, leaving a space between them. Conversely, an overlap happens when the edges of adjacent tows cross over each other.
These defects are particularly concerning because:
While some gaps and overlaps are inherent to the design process (particularly in complex geometries), many occur due to manufacturing process variations. These variations can be broadly categorized into two main types:
Understanding and predicting these manufacturing variations is crucial for several reasons:
Recent research has made significant strides in measuring and characterizing these variations, offering new possibilities for predicting and controlling defect formation. The engineering behind AFP continues to evolve, with new approaches to process monitoring and control emerging regularly.
In the following sections, we'll explore groundbreaking research that provides a comprehensive framework for measuring, analyzing, and predicting these manufacturing variations. Through this understanding, we can work towards more efficient and reliable AFP manufacturing processes.
To understand and predict manufacturing variations in AFP composites, researchers developed a sophisticated measurement system using the AFP-XS system. This compact yet powerful setup represents a significant advancement in process monitoring for AFP manufacturing.
The experimental setup consisted of four key elements:
The research team employed a comprehensive approach to measure four critical aspects of manufacturing variation:
The experimental procedure involved:
The research implemented sophisticated data acquisition methods:
This comprehensive measurement approach allows for a detailed understanding of how AFP machines and components interact during the manufacturing process, providing valuable insights into defect formation mechanisms.
This sophisticated measurement system represents a significant advancement in understanding AFP manufacturing variations. By simultaneously tracking multiple parameters, researchers can:
The insights gained from this research are particularly valuable for implementing automated fiber placement systems, as they provide a scientific basis for process improvement and quality control strategies.
The research revealed fascinating insights into how different manufacturing variations contribute to gaps and overlaps in AFP composites. Let's break down each source of variation and its significance.
The study found that robot positioning showed interesting patterns:
This finding aligns with previous observations in AFP process monitoring, highlighting the importance of precise robot control in automated manufacturing.
Perhaps the most significant finding was related to tow movement on the roller:
This discovery has important implications for AFP machine design and operation, particularly in feed system optimization.
The analysis of incoming tow dimensions revealed:
These findings are crucial for understanding material quality control in AFP processes.
The study showed interesting effects of compaction:
One of the most valuable outcomes of this research was the development of a predictive model for gaps and overlaps. The model showed:
The research provided valuable insights into how eliminating different sources of variation could improve manufacturing quality:
Perhaps most excitingly, the research demonstrated potential for real-time defect prediction:
The research successfully validated that:
These findings represent a significant step forward in understanding defects and damage in composite materials, providing a foundation for improved manufacturing processes and quality control strategies.
The findings from this research have far-reaching implications for advancing composite manufacturing. Let's explore how these insights can transform AFP processes and quality control strategies.
This groundbreaking research provides a scientific foundation for understanding and controlling manufacturing variations in AFP processes. The ability to predict and control gaps and overlaps represents a significant step forward in composite manufacturing technology.
Key takeaways include:
The future of AFP manufacturing looks promising, with these findings paving the way for:
As we continue to advance in automated composite manufacturing, these insights will prove invaluable in developing the next generation of AFP systems and processes.
To deepen your understanding of AFP manufacturing and composite materials, we recommend exploring these related topics:
Learn more about the equipment used in this research:
This blog is based on the research paper:
Pantoji, S., Kassapoglou, C., & Peeters, D. (2024). Predicting gaps and overlaps in automated fiber placement composites by measuring sources of manufacturing process variations. Composites Part B. DOI: https://doi.org/10.1016/j.compositesb.2024.111891
The authors would like to acknowledge the original researchers and their groundbreaking work in advancing our understanding of AFP manufacturing processes.
For those interested in diving deeper into specific aspects of AFP manufacturing and composite materials, please explore our comprehensive resource library:
The insights shared in this blog represent just a fraction of what's possible with modern AFP technology. At ADD Composites, we're dedicated to making advanced composite manufacturing accessible and efficient for organizations of all sizes.
📞 Ready to start? Contact us today to learn how ADD Composites can help optimize your manufacturing processes and reduce defects with our advanced AFP solutions.