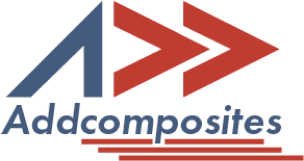
The use of hydrogen as a clean and renewable energy source is gaining significant attention as we shift towards sustainable energy solutions. According to the International Energy Agency, global hydrogen production was estimated at around 70 million metric tons in 2021, with green hydrogen production increasing to 2-3 million metric tons annually [1]. However, the safe and efficient storage of hydrogen remains a major challenge due to its low energy density and high compressibility. Hydrogen needs to be stored under high pressure to achieve practical energy density for various applications.
In this article, we will explore the different types of tanks used to store hydrogen under pressure, their technological differences, and their advantages. Understanding these storage solutions is crucial for the widespread adoption of hydrogen as a fuel source in various sectors, including transportation and industry.
A hydrogen tank is a specialized container designed to store hydrogen in either gaseous or liquid form. It may also be referred to as a hydrogen cylinder, cartridge, or canister. The construction of a hydrogen tank must meet stringent physical requirements based on the pressure and temperature of storage. These requirements are regulated by government agencies and international standards such as ISO 15869 and ISO 14687:2019 [2].
Key considerations for hydrogen tank design include:
The continuous innovation in materials science and manufacturing processes has led to significant advancements in hydrogen tank design and performance. Hydrogen fuel tanks are used in a variety of applications, including fuel cell and electrolyzer systems, rockets, and space flight. Typically, a hydrogen tank is part of a larger hydrogen storage system that may include compression equipment, safety valves, and monitoring systems.
There are five types of gas tanks that can be used for both stationary and mobile applications to store hydrogen. Each type has unique characteristics and is suited for different applications.
Type 1 tanks are the most basic and common gas cylinders, made entirely of metal, typically steel or aluminum alloys.
Learn more about metal materials in composites
Type 2 tanks are an improvement over Type 1, featuring a metal liner with partial fiber reinforcement.
Learn more about filament winding process
Type 3 tanks mark a significant advancement in hydrogen storage technology, particularly for vehicle applications.
Learn more about automated fiber placement
Type 4 tanks represent the current state-of-the-art in high-pressure hydrogen storage for mobile applications.
Learn more about composite materials in hydrogen tanks
Type 5 tanks are the most advanced and experimental design, featuring a linerless all-composite construction.
Learn more about advanced composite manufacturing techniques
The main differences between the five types of tanks lie in the materials used to manufacture them and their resulting performance characteristics. Here's a comparison of key factors:
For mobile applications of hydrogen, Type 4 tanks are commonly used because they provide the highest storage density while maintaining a good balance of weight efficiency and manufacturability. They are ideal for passenger cars and heavy-duty commercial vehicles where weight and space are critical factors.
Type 3 tanks are often preferred for larger vehicles like buses and trucks, where the slightly lower storage density is offset by potentially lower costs and simpler manufacturing.
Type 1 and Type 2 tanks continue to be used in industrial and stationary applications where weight is less critical, and lower cost is a priority.
Type 5 tanks represent the cutting edge of hydrogen storage technology, with potential applications in aerospace and other specialized fields where extreme weight savings are crucial.
Hydrogen tanks come in different types, each with its own technological differences and advantages. The choice of tank type depends on the specific application, desired storage density, cost considerations, and safety requirements. As the world moves towards a more sustainable future, the efficient and safe storage of hydrogen will become increasingly important.
Future developments in hydrogen tank technology are likely to focus on:
The ongoing research and development in this field will be crucial in overcoming the remaining challenges in hydrogen storage and enabling the widespread adoption of hydrogen as a clean energy carrier. As we continue to innovate, hydrogen storage technology will play a vital role in the transition to a sustainable energy future.