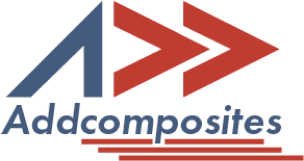
The aerospace manufacturing landscape is experiencing a significant transformation. As the industry pushes toward higher production rates and more sustainable practices, manufacturers are increasingly looking to transition from traditional thermoset composites to thermoplastic alternatives. This shift isn't just a trend – it's a strategic response to the evolving demands of modern aerospace manufacturing.
Traditional thermoset composites have long been the backbone of aerospace composite manufacturing, commanding over 90% of the carbon fiber reinforced polymer (CFRP) market. Their dominance stems from a well-established manufacturing process and decades of proven performance in critical applications. However, as the aerospace industry evolves, particularly with the emergence of Urban Air Mobility (UAM) and the push for higher production rates, manufacturers are discovering that traditional thermoset processing methods may not be sufficient to meet future demands.
Several key factors are driving this transition:
The emergence of new aerospace sectors, particularly the UAM market, demands manufacturing rates that traditional thermoset processing struggles to achieve. With companies pushing for faster, more efficient production methods, thermoplastic composites offer a compelling alternative with their significantly shorter processing times.
Environmental considerations are becoming increasingly critical in aerospace manufacturing. Unlike thermosets, thermoplastic composites offer the advantage of recyclability and reprocessing capabilities, aligning with the industry's growing focus on sustainable practices.
While thermosets have proven their worth in aerospace applications, thermoplastics offer distinct advantages in certain areas. Their superior impact resistance, damage tolerance, and chemical resistance make them increasingly attractive for specific applications.
The transition from thermoset to thermoplastic composites isn't without its challenges. It requires not just new materials, but new processing methods, equipment, and expertise. Manufacturers must consider various factors, including:
However, with proper planning and the right technology partners, these challenges can be effectively addressed, leading to a successful transition that positions manufacturers for future growth and innovation.
The journey from thermoset to thermoplastic composites represents more than just a material change – it's a paradigm shift in how we approach aerospace composite manufacturing. In the following sections, we'll explore the key considerations, challenges, and solutions that can help manufacturers navigate this important transition successfully.
To successfully transition between composite systems, it's crucial to understand the fundamental differences between thermoset and thermoplastic composites. These differences not only affect the final product performance but also dictate manufacturing processes and equipment requirements.
The key distinction between thermoset and thermoplastic composites lies in their molecular structure:
The processing requirements for these materials differ significantly, impacting manufacturing strategies:
Each material system offers distinct performance advantages:
The choice between thermoset and thermoplastic composites significantly impacts manufacturing processes:
Understanding these fundamental differences is crucial for manufacturers planning the transition. Each aspect must be carefully considered when developing new manufacturing processes and selecting equipment. The next section will explore why, despite these differences and challenges, many manufacturers are choosing to make this transition.
The shift from thermoset to thermoplastic composites represents a significant investment in both resources and organizational change. However, several compelling advantages make this transition increasingly attractive for aerospace manufacturers.
The transition to thermoplastic composites offers a compelling combination of manufacturing, performance, and sustainability benefits. While the initial investment may be significant, the long-term advantages make it an increasingly attractive option for aerospace manufacturers looking to stay competitive in an evolving industry landscape.
While the benefits of transitioning to thermoplastic composites are compelling, manufacturers face several significant challenges during the transition process. Understanding and preparing for these challenges is crucial for a successful implementation.
While these challenges are significant, they are not insurmountable. With proper planning, the right technology partners, and a systematic approach to implementation, manufacturers can successfully navigate the transition to thermoplastic composites. The key is to understand these challenges upfront and develop comprehensive strategies to address them throughout the transition process.
The transition to thermoplastic composites requires a comprehensive understanding of manufacturing processes that differ significantly from traditional thermoset methods. Let's explore the key process considerations that manufacturers need to address.
AFP technology has evolved significantly to accommodate thermoplastic materials:
While less common for thermoplastics, manual processes may still be necessary:
A primary consolidation method for thermoplastics:
An emerging technology for thermoplastic processing:
A key advantage of thermoplastic composites:
Still relevant for certain applications:
Critical for consistent production:
Essential for process optimization:
Implementation of Industry 4.0 concepts:
The successful implementation of thermoplastic composite manufacturing requires careful consideration of these process elements. Each aspect must be optimized for the specific application while maintaining the flexibility to adapt to changing requirements and new technologies.
The transition to thermoplastic composites presents numerous challenges, but Addcomposites offers comprehensive solutions designed to make this transition smoother and more efficient. Let's explore how our integrated systems and solutions address the key challenges in thermoplastic composite manufacturing.
Our flagship AFP-XS system offers unique advantages:
Our comprehensive path planning solution:
Specialized for SCF3D printing:
Advanced manufacturing flexibility:
Enhanced winding capabilities:
Comprehensive safety and control:
Versatile heating capabilities:
Building expertise through education:
Worldwide assistance availability:
By providing these comprehensive solutions, Addcomposites helps manufacturers overcome the challenges of transitioning to thermoplastic composites while maximizing the benefits of this advanced technology. Our integrated approach ensures that manufacturers have access to the tools, technology, and support needed for successful implementation.
A successful transition to thermoplastic composites requires a structured approach that addresses technical, organizational, and operational aspects. Here are key best practices to ensure a smooth transition:
Begin with thorough evaluation:
Start small and scale systematically:
Adapt designs for thermoplastic processing:
Implement appropriate controls:
Maintain institutional knowledge:
Establish comprehensive safety measures:
Implement sustainable practices:
Regular evaluation and adjustment:
By following these best practices, manufacturers can minimize risks and maximize the benefits of transitioning to thermoplastic composites. The key is to maintain a systematic approach while remaining flexible enough to adapt to changing requirements and new opportunities.
The future of thermoplastic composites in aerospace manufacturing looks increasingly promising, with several key trends and developments shaping the industry's direction. Let's explore what lies ahead:
The rise of intelligent manufacturing:
Emerging manufacturing methods:
Expanding market opportunities:
Growing environmental consciousness:
Evolution of production methods:
The future of thermoplastic composites in aerospace manufacturing is marked by continuous innovation, increasing automation, and growing market opportunities. As technology advances and sustainability becomes increasingly important, thermoplastic composites are well-positioned to play a crucial role in the future of aerospace manufacturing.
The transition from thermoset to thermoplastic composites represents a significant shift in aerospace manufacturing, one that offers substantial benefits while presenting notable challenges. As we've explored throughout this discussion, success in this transition requires careful planning, the right technology partners, and a commitment to continuous improvement.
The shift to thermoplastic composites is more than just a material change – it's an opportunity to revolutionize aerospace manufacturing. While the challenges are real, the potential benefits make this transition increasingly attractive for manufacturers looking to stay competitive in an evolving industry.
With the right approach and support, manufacturers can successfully navigate this transition, positioning themselves for future growth and innovation. Addcomposites stands ready to support this journey with comprehensive solutions, expertise, and ongoing support.
Ready to explore how thermoplastic composites can transform your manufacturing operations? Take the first step:
The future of aerospace manufacturing is evolving, and thermoplastic composites are playing an increasingly important role. The time to begin this transition is now – let's work together to make it successful.
This blog post draws significant insights from the following academic work:
Jones III, S. L. (2022). Manufacturing Process Considerations When Transitioning From Thermoset to Thermoplastic Composite Material for Urban Air Mobility Propellers. Master's thesis, University of South Carolina. Retrieved from https://scholarcommons.sc.edu/etd/6578
This comprehensive thesis provides valuable insights into the challenges and considerations involved in transitioning from thermoset to thermoplastic composites in aerospace applications, particularly for urban air mobility components.
The technical content in this blog is additionally supported by Addcomposites' extensive knowledge base and technical documentation:
For more information about specific topics covered in this blog, please visit our comprehensive resource library at www.addcomposites.com
This blog represents a synthesis of academic research, industry experience, and Addcomposites' technical expertise. While we strive for accuracy in all our content, specific applications may require additional consideration and engineering analysis.