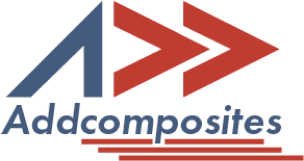
We would like to express our deepest gratitude to Yonglin Chen, Junming Zhang, Zefu Li, Huliang Zhang, Jiping Chen, Weidong Yang, Tao Yu, Weiping Liu, and Yan Li for the article "Manufacturing Technology of Lightweight Fiber-Reinforced Composite Structures in Aerospace: Current Situation and toward Intellectualization". Your invaluable insights into the manufacturing technologies for continuous fiber-reinforced polymer composites have significantly contributed to our understanding of the subject. You work has significantly contributed to the following blog. Your work has not only enlightened us but also our readers. We appreciate the depth of research and the comprehensive review of the technologies, their evolution, and future trends. Your contribution to this field is truly commendable. Thank you for your dedication and for sharing your knowledge with us
Main manufacturing technologies for Composites
Traditional molding technologies for fiber-reinforced polymer composites primarily include Autoclave and Out of Autoclave (OoA) methods.
Autoclave and OoA molding technology
The traditional molding technologies are moving towards numeralization and intellectualization to improve efficiency, reduce costs, and enhance the quality of the final products. Here are some of the key developments:
Residual stress and PID prediction of a four-layer CFRP
Liquid Composite Molding involves the use of a dry fiber preform laid in a mold cavity, followed by the injection of resin into the mold until the entire cavity is filled. The resin-infused preform is then cured, cooled, and demolded.
There are three main variants of RTM: Low Pressure RTM (LP-RTM), High Pressure RTM (HP-RTM), and Compression RTM (CRTM).
The LCM technologies are moving towards numeralization and intellectualization to improve efficiency, reduce costs, and enhance the quality of the final products. Here are some of the key developments:
Monitoring systems for resin flow
Automated Layup Technology involves the use of automated systems to lay up composite materials, which can significantly improve efficiency, reduce material consumption, and increase the level of automation.
Automated layup technology
The ALT technologies are moving towards numeralization and intellectualization to improve efficiency, reduce costs, and enhance the quality of the final products. Here are some of the key developments:
Additive Manufacturing involves the use of 3D printing technologies to create objects from 3D model data, usually layer upon layer. It's a rapidly growing field that offers significant advantages over traditional manufacturing methods, including the ability to create complex geometries, use a wide range of materials, and customize products.
Robot arm for additive manufacturing
Traditional additive manufacturing technologies for continuous carbon fiber-reinforced composites
The Additive Manufacturing technologies are moving towards numeralization and intellectualization to improve efficiency, reduce costs, and enhance the quality of the final products. Here are some of the key developments:
In the ever-evolving world of manufacturing, the technologies for creating fiber-reinforced polymer composites have seen a significant transformation. This journey, from traditional molding technologies to more advanced and efficient methods, has been both challenging and rewarding.
But the journey doesn't end here. The future of composite manufacturing lies in the numeralization and intellectualization of these technologies. We're moving towards an era where intelligent platforms will integrate design and manufacturing technologies, leading to the development of smart composite structures. These structures will not only be used in advanced aircraft but will also play a crucial role in the exploration of outer space.
Discover the future of composite manufacturing with Addcomposites! Here's how you can get involved:
At Addcomposites, we are dedicated to revolutionizing composite manufacturing. Our AFP systems and comprehensive support services are waiting for you to harness. So, don't wait – get started on your journey to the future of manufacturing today!
We would like to express our deepest gratitude to Yonglin Chen, Junming Zhang, Zefu Li, Huliang Zhang, Jiping Chen, Weidong Yang, Tao Yu, Weiping Liu, and Yan Li for the article "Manufacturing Technology of Lightweight Fiber-Reinforced Composite Structures in Aerospace: Current Situation and toward Intellectualization". Your invaluable insights into the manufacturing technologies for continuous fiber-reinforced polymer composites have significantly contributed to our understanding of the subject. You work has significantly contributed to the following blog. Your work has not only enlightened us but also our readers. We appreciate the depth of research and the comprehensive review of the technologies, their evolution, and future trends. Your contribution to this field is truly commendable. Thank you for your dedication and for sharing your knowledge with us
Main manufacturing technologies for Composites
Traditional molding technologies for fiber-reinforced polymer composites primarily include Autoclave and Out of Autoclave (OoA) methods.
Autoclave and OoA molding technology
The traditional molding technologies are moving towards numeralization and intellectualization to improve efficiency, reduce costs, and enhance the quality of the final products. Here are some of the key developments:
Residual stress and PID prediction of a four-layer CFRP
Liquid Composite Molding involves the use of a dry fiber preform laid in a mold cavity, followed by the injection of resin into the mold until the entire cavity is filled. The resin-infused preform is then cured, cooled, and demolded.
There are three main variants of RTM: Low Pressure RTM (LP-RTM), High Pressure RTM (HP-RTM), and Compression RTM (CRTM).
The LCM technologies are moving towards numeralization and intellectualization to improve efficiency, reduce costs, and enhance the quality of the final products. Here are some of the key developments:
Monitoring systems for resin flow
Automated Layup Technology involves the use of automated systems to lay up composite materials, which can significantly improve efficiency, reduce material consumption, and increase the level of automation.
Automated layup technology
The ALT technologies are moving towards numeralization and intellectualization to improve efficiency, reduce costs, and enhance the quality of the final products. Here are some of the key developments:
Additive Manufacturing involves the use of 3D printing technologies to create objects from 3D model data, usually layer upon layer. It's a rapidly growing field that offers significant advantages over traditional manufacturing methods, including the ability to create complex geometries, use a wide range of materials, and customize products.
Robot arm for additive manufacturing
Traditional additive manufacturing technologies for continuous carbon fiber-reinforced composites
The Additive Manufacturing technologies are moving towards numeralization and intellectualization to improve efficiency, reduce costs, and enhance the quality of the final products. Here are some of the key developments:
In the ever-evolving world of manufacturing, the technologies for creating fiber-reinforced polymer composites have seen a significant transformation. This journey, from traditional molding technologies to more advanced and efficient methods, has been both challenging and rewarding.
But the journey doesn't end here. The future of composite manufacturing lies in the numeralization and intellectualization of these technologies. We're moving towards an era where intelligent platforms will integrate design and manufacturing technologies, leading to the development of smart composite structures. These structures will not only be used in advanced aircraft but will also play a crucial role in the exploration of outer space.
Discover the future of composite manufacturing with Addcomposites! Here's how you can get involved:
At Addcomposites, we are dedicated to revolutionizing composite manufacturing. Our AFP systems and comprehensive support services are waiting for you to harness. So, don't wait – get started on your journey to the future of manufacturing today!