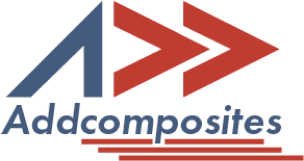
Thermoplastic composites have revolutionized materials engineering through their unique combination of recyclability, damage tolerance, and manufacturing flexibility. At the heart of their performance lies a critical but often overlooked characteristic: crystallinity. This molecular-scale phenomenon governs nearly every aspect of composite behavior—from tensile strength to chemical resistance. The crystallization process in semi‑crystalline thermoplastics like polyphenylene sulfide (PPS) and polyetherketoneketone (PEKK) creates a complex interplay between ordered crystalline regions and disordered amorphous domains. Modern manufacturing techniques like automated fiber placement (AFP) and automated tape laying (ATL) present both opportunities and challenges in crystallinity control, with cooling rates varying from 15°C/min in conventional processes to over 10,000°C/min in high‑speed additive methods 1, 3, 6. This report synthesizes cutting‑edge research on crystallization mechanisms, analyzes the multidimensional relationship between processing parameters and material properties, and provides actionable insights for optimizing composite performance through crystallinity management.
Semi‑crystalline thermoplastics achieve their unique properties through a hierarchical self‑assembly process. When cooled from the melt state, polymer chains fold into lamellar structures measuring 10–20 nm thick, which then organize into larger spherulitic domains up to 100 μm in diameter 8, 14. The degree of crystallinity—typically ranging from 20% to 60% in engineering thermoplastics—depends on the polymer's ability to form these ordered regions while constrained by:
The Avrami equation remains the primary model for describing crystallization kinetics:
X(t)=1−exp(−ktn)X(t) = 1 - \exp(-kt^n)X(t)=1−exp(−ktn)
Where X(t) represents crystallinity development over time, k is the crystallization rate constant, and n is the Avrami exponent dependent on the nucleation mechanism 6, 10. For carbon fiber‑reinforced PPS (CF/PPS), experimental studies show n values between 1.65 and 1.75 under isothermal conditions at 225–240°C 1. This deviation from ideal spherulitic growth (n = 3) indicates mixed nucleation modes influenced by fiber surfaces.
Carbon fibers act as potent nucleating agents, inducing transcrystalline layers (TCL) at the fiber‑matrix interface. Polarized light microscopy reveals these TCLs as highly oriented crystalline regions extending 5–20 μm from fiber surfaces 4, 5, 7. The transcrystalline morphology develops when:
In CF/PPS systems, transcrystallinity increases interfacial shear strength by 14.2% compared to bulk‑nucleated composites 4. This enhancement stems from mechanical interlocking between fiber surface asperities and the oriented crystalline matrix 5, 7. However, excessive TCL thickness (>15 μm) can create brittle interfacial zones, reducing composite toughness 3, 7.
The mechanical implications of crystallinity present a complex optimization landscape:
Stiffness and Strength
Storage modulus in CF/PPS increases 9.8% when crystallinity rises from 51% to 62%, while Young’s modulus improves 9.2% 4. These gains originate from crystalline domains acting as physical crosslinks, restricting chain mobility under load 14, 15. However, the relationship becomes nonlinear above 50% crystallinity due to stress concentration at spherulite boundaries 1, 3.
Fracture Toughness
Mode I fracture toughness of CF/PEEK drops 27.8% when crystallinity increases from 17% to 44% 1, 3. Ductile tearing in amorphous regions gives way to brittle cleavage through crystalline lamellae. Optimal toughness occurs at intermediate crystallinity (30–35%) where crystalline domains reinforce without creating continuous fracture paths 3, 7.
Interlaminar Properties
Interlaminar shear strength (ILSS) in CF/PPS improves 14% with slower cooling (0.5°C/min vs 10°C/min) due to enhanced fiber‑matrix adhesion from transcrystallinity 4, 5. However, rapid AFP processes (>5 m/min) reduce ILSS by 18% compared to autoclave consolidation, highlighting the trade‑off between manufacturing speed and interfacial quality 3, 6.
Crystallinity dramatically affects service temperature limits. The glass transition temperature (TgT_gTg) of semi‑crystalline PPS remains constant at 89°C, but the heat deflection temperature (HDT) increases from 135°C (20% crystallinity) to 260°C (60% crystallinity) 9, 14. This 92% improvement enables aerospace applications where sustained thermal loads exceed 200°C.
Chemical resistance follows a similar trend—crystalline regions impede solvent diffusion, reducing weight gain in jet fuel immersion tests from 1.2% (amorphous) to 0.3% (60% crystalline) 8, 14. The tortuous path through crystalline lamellae increases activation energy for penetrant molecules by 15–25 kJ/mol 12, 14.
As the dominant crystallization factor, cooling rate (β\betaβ) requires precise regulation:
The crystallization window concept helps balance these competing properties. For CF/PPS, maintaining tool temperatures between 87°C (crystallization onset) and 270°C (melting point) enables isothermal crystallization during AFP layup 3, 21. This approach achieves 44.1% crystallinity at 380°C laser temperature and 120°C tool temperature—comparable to autoclave processing but with 80% faster cycle times 3.
Tool temperature (TtoolT_{tool}Ttool) directly impacts crystallization kinetics through:
Experimental data shows CF/PPS crystallinity increases from 17.6% to 44.1% as TtoolT_{tool}Ttool rises from 40°C to 120°C at constant laser power 3, 21. The relationship follows an Arrhenius‑type behavior:
χc=Aexp(−EaRTtool)\chi_c = A \exp\left(-\frac{E_a}{RT_{tool}}\right)χc=Aexp(−RTtoolEa)
Where χc\chi_cχc is crystallinity, EaE_aEa the activation energy (453 kJ/mol for PPS), and RRR the gas constant 1, 6. Maintaining TtoolT_{tool}Ttool above 87°C extends crystallization time from 2.6 ms to 8.6 s, allowing spherulite development up to 10 μm in diameter 1, 3.
Laser‑assisted AFP uses 250–380°C preheating to achieve matrix consolidation. Higher laser temperatures (380°C vs 250°C) improve crystallinity by 24% through:
However, placement speed introduces competing effects:
The inverse relationship between speed and crystallinity stems from shortened crystallization time (tct_ctc):
tc=Tm−Ttoolβt_c = \frac{T_m - T_{tool}}{\beta}tc=βTm−Ttool
At 31 m/min, β\betaβ exceeds 10,000°C/min, quenching the matrix into a metastable amorphous state 1, 3. Post‑process annealing can recover 60–80% of potential crystallinity but adds manufacturing steps 6, 21.
DSC thermograms reveal crystallization behavior through:
χc=ΔHm−ΔHccΔHm0×100%\chi_c = \frac{\Delta H_m - \Delta H_{cc}}{\Delta H_m^0} \times 100\%χc=ΔHm0ΔHm−ΔHcc×100%
Where ΔHm0\Delta H_m^0ΔHm0 is the enthalpy of a 100% crystalline polymer (80 J/g for PPS) 4, 15. Figure 1 (not shown) illustrates dual melting peaks in slow‑cooled CF/PPS, indicating separate bulk and transcrystalline morphologies 4, 5.
Cryofractured surfaces imaged at 10 kV reveal:
Energy‑dispersive X‑ray spectroscopy (EDS) maps show sulfur enrichment in crystalline areas due to PPS backbone alignment 5, 9.
Wide‑angle XRD (WAXD) quantifies crystallinity through the Hermans orientation function:
f=3⟨cos2ϕ⟩−12f = \frac{3\langle\cos^2\phi\rangle - 1}{2}f=23⟨cos2ϕ⟩−1
Where ϕ\phiϕ is the angle between polymer chains and the fiber axis. Highly oriented transcrystalline regions achieve f>0.85f > 0.85f>0.85, compared to f≈0.3f \approx 0.3f≈0.3 in bulk spherulites 5, 7.
Boeing’s 787 Dreamliner utilizes CF/PEKK composites with 35–40% crystallinity for fuselage frames 6, 11. Process optimization achieved:
Key parameters:
BMW i3 battery trays employ AFP‑manufactured CF/PPS with 28% crystallinity, balancing:
Post‑process infrared annealing increases crystallinity to 35% for improved creep resistance under 90°C operating conditions 3, 21.
Morphology‑Property Mapping
Digital twins correlate spherulite size/distribution to fatigue life using finite element analysis (FEA) 6, 10.
Crystallinity control represents the cornerstone of thermoplastic composite performance, demanding careful balancing of competing mechanical, thermal, and processing requirements. Through strategic manipulation of cooling rates (2.5–10,000°C/min), tool temperatures (40–280°C), and placement speeds (5–31 m/min), manufacturers can tailor crystallinity from 17% to 62% to meet application‑specific needs. Emerging technologies like machine learning and in‑situ monitoring promise to revolutionize crystallinity optimization, potentially reducing development cycles by 70% while improving material utilization. As industries push toward higher operating temperatures and faster production rates, mastering crystallization science will remain critical for unlocking the full potential of thermoplastic composites.