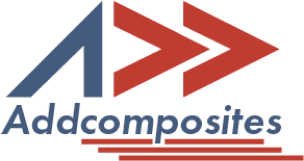
The realm of manufacturing stands on the cusp of a new era, one that bridges the gap between the digital and the tangible. At the heart of this transformation is 3D printing, a process that has transitioned from prototyping novelty to a powerhouse of production in its own right. With its roots tracing back to the 1980s, 3D printing, or additive manufacturing, has evolved through leaps and bounds, growing in sophistication, scale, and substance.
Enter Continuous Fiber 3D Printing (CF3DP) — the latest innovation that's set to redefine the manufacturing landscape. This technology is not just an incremental improvement; it's a revolutionary approach that integrates continuous fibers, such as carbon or glass, into a polymer matrix during the printing process. The result? Components that are not just prototypes, but high-performance parts boasting exceptional strength and durability, ready for the most demanding applications.
The implications of CF3DP stretch far and wide, particularly for industries where the integrity and strength-to-weight ratio of materials are non-negotiable. In aerospace, automotive, and marine sectors, the ability to produce large-scale parts that can withstand extreme forces, yet remain light, is nothing short of a game-changer. From the chassis of a race car to the fuselage of a drone, CF3DP is setting the stage for a future where design complexity is no longer a constraint, and efficiency is measured not just in cost, but in performance.
As we delve into the capabilities and prospects of CF3DP, it's crucial to understand that this is not just about printing parts; it's about reimagining the engineering process from the ground up. It's about harnessing the full potential of computational design, material science, and precision engineering to create components that were once deemed impossible. The fusion of continuous fibers into 3D printing heralds a new chapter in manufacturing — one that is poised to deliver innovations that are as robust in structure as they are groundbreaking in concept.
With the high technical acumen of our readers in mind, we will explore the intricate details of CF3DP, from the underlying mechanics to the cutting-edge advancements that are propelling this technology forward. Whether it's the strategic placement of fibers to optimize load paths or the thermal management techniques critical to maintaining material properties, we'll delve into the technicalities that make CF3DP a cornerstone of next-generation manufacturing. So, let's embark on this journey through the intricate dance of fibers and polymers, and unlock the potential that continuous fiber 3D printing promises to the world of large-scale production.
At its core, CF3DP is a specialized branch of additive manufacturing that integrates the power of continuous fibers—such as carbon, glass, or Kevlar—with thermoset or thermoplastic polymers to create composite materials in a single build process. Unlike traditional 3D printing that deposits molten plastic layer by layer, CF3DP intertwines these strong fibers within the matrix material, exponentially enhancing the part's mechanical properties.
The Process: The CF3DP process begins with a spool of fiber filament and a separate spool of thermoplastic filament. The fibers are impregnated with a polymer resin, either before or during the printing process, and then deposited in tandem with the thermoplastic material. This dual-extrusion system is meticulously controlled by software that dictates the path and orientation of the fibers, aligning them along load-bearing paths of the part being printed.
Material Science at Play: The selection of fiber material is pivotal. Carbon fibers are renowned for their high stiffness and strength-to-weight ratio, making them ideal for aerospace and automotive applications. Glass fibers offer durability and cost-effectiveness, suitable for a wide range of uses including recreational equipment and industrial components. Each fiber type brings distinct advantages to the table, allowing engineers to tailor the properties of the final product to meet specific design criteria.
The Technical Edge: CF3DP offers an unparalleled advantage in creating parts with complex geometries that traditional manufacturing methods struggle with. The ability to adjust fiber orientation on-the-fly allows for anisotropic properties—where the material's strength varies with direction—providing strategic reinforcement where it matters most. Moreover, the additive nature of CF3DP means that material is only used where necessary, minimizing waste.
Engineering Precision: The design for CF3DP goes beyond mere geometry. It encapsulates a holistic approach to part creation, where factors such as load-bearing requirements, thermal stresses, and environmental exposure are all considered in the print strategy. Advanced software tools allow for the simulation of various load scenarios, ensuring that the fibers are precisely aligned with anticipated stress vectors, leading to parts that are optimized for both performance and longevity.
The Equation of Strength: In CF3DP, the tensile strength of a printed part can be summarized by the rule of mixtures for a composite material:
σc=Vf⋅σf+Vm⋅σm
where:
This equation underscores the synergy between fiber and polymer, illustrating how the tensile strength of a CF3DP part is a weighted sum of its constituents.
In the next sections, we will delve deeper into how CF3DP is revolutionizing industries with its unique capabilities, the challenges it faces, and the prospects that lie ahead in this dynamic field of manufacturing.
The landscape of CF3DP is rapidly evolving, with technological advancements that refine the process and expand its capabilities. Here, we explore the key developments that are pushing the boundaries of what's possible with CF3DP.
Printer Design Evolution: In the pursuit of higher efficiency and precision, CF3DP printers have undergone significant design enhancements. Modern CF3DP printers boast improved fiber impregnation systems, ensuring that the fibers are fully saturated with resin before being laid down. This is critical to achieving optimal mechanical properties in the final product.
Path Planning and Fiber Orientation: Advances in path planning algorithms have enabled printers to deposit fibers in orientations that exactly mirror the predicted stress patterns of the part in use. This optimization of fiber paths contributes to parts that are not only stronger but also use less material, reducing weight and cost. The orientation of fibers can be dynamically changed mid-print to adapt to complex geometries and loading conditions, a process that is controlled by increasingly sophisticated software.
Thermal Management: CF3DP must carefully control the temperature during the printing process to ensure proper fiber-matrix bonding and prevent warping or distortion. Innovations in thermal management include heated print beds, temperature-controlled print heads, and environment chambers, all designed to maintain the integrity of the materials during the additive process.
Material Compatibility and Multi-Material Printing: The introduction of new fiber materials and hybrid filaments has expanded the potential applications of CF3DP. Printers are now capable of handling a variety of fibers and resins, sometimes within a single print job, to create parts with localized variations in material properties.
Software Integration and Simulation: Software advancements have been critical in CF3DP's progress. Modern CF3DP relies on integrated CAD/CAM systems that can simulate the printing process, predict material behavior, and automatically generate optimized toolpaths. These systems can take into account the anisotropic nature of the printed composites, allowing designers to simulate how the part will perform under real-world conditions.
Real-Time Monitoring and Quality Control: Emerging technologies in real-time monitoring involve sensors and machine vision to oversee the printing process, detecting and correcting errors as they occur. This leads to improved quality control and consistency, reducing the rate of part failure and increasing trust in CF3DP as a manufacturing method.
Automation and AI: The incorporation of artificial intelligence (AI) into CF3DP systems is on the horizon. AI can analyze vast amounts of data to optimize the print process, predict potential issues before they arise, and even suggest design improvements. This intelligence layer aims to streamline the manufacturing process, reducing the need for human intervention and allowing for more complex and reliable part production.
Economic and Scalability Considerations: As CF3DP technologies mature, we are beginning to see a shift toward scalability and economic feasibility. This includes efforts to increase print speeds without sacrificing quality and to develop larger printers capable of producing sizable components in a single build.
Sustainability: Finally, advancements in sustainable materials for CF3DP are being explored. Biocompatible and biodegradable resins, recycled fibers, and green manufacturing practices are emerging, aiming to reduce the environmental footprint of CF3DP.
As CF3DP technology continues to develop, we can anticipate a wave of new applications, improved materials, and manufacturing practices that could redefine industry standards. The future of CF3DP is not only about what can be made but also about the innovation and efficiency with which it can be made.
CF3DP is not just a technological marvel in the lab; it's a transformative force in the field. The technology is making waves across several industries, each with its unique demands and challenges. Let's examine the profound impact CF3DP is having on key sectors.
Aerospace: In the aerospace industry, the stakes are as high as the skies these machines traverse. CF3DP is instrumental in manufacturing components that are robust yet feather-light. The ability to create complex geometries with tailored fiber orientation allows for parts that can endure the stressors of flight while contributing to overall weight reduction, a critical factor in fuel efficiency and payload maximization. The technology is particularly suitable for producing bespoke parts for small production runs, which is common in the aerospace industry.
Automotive: The automotive sector is undergoing a paradigm shift towards lighter, more energy-efficient vehicles. CF3DP steps into this arena with the promise of high-strength, low-weight components that can be custom-designed for specific performance requirements. This is especially beneficial for high-performance vehicles where every kilogram saved can translate into speed and efficiency gains. Furthermore, the technology's ability to iterate designs rapidly accelerates the development cycle, from concept cars to road-ready models.
Marine: For marine applications, the durability of materials is paramount, given the relentless exposure to corrosive saltwater environments. CF3DP offers the advantage of producing parts that can withstand these harsh conditions while improving the vessel's buoyancy and performance. The technology's flexibility in design also enables the creation of unique, hydrodynamic shapes that traditional manufacturing would find challenging.
Construction and Architecture: CF3DP is set to revolutionize the construction industry by enabling the production of complex structural components that are both sturdy and intricate. The ability to print large-scale parts on-site reduces transportation costs and construction times significantly. In architecture, CF3DP allows for the realization of avant-garde designs that were once considered unbuildable.
Medical Devices: In the medical field, CF3DP is beginning to find its footing in creating customized implants and prosthetics. The technology's precision and ability to use biocompatible materials mean that devices can be tailored to the individual's anatomy, offering improved comfort and functionality.
Energy: The energy sector, particularly wind power, benefits from CF3DP through the manufacturing of more efficient and durable turbine blades. The technology's capability to embed continuous fibers means these structures can better withstand the forces they encounter, leading to longer service lives and reduced maintenance costs.
Sporting Goods: CF3DP has also found a niche in the sporting goods industry, where customized equipment is highly valued. From lightweight bicycle frames to durable golf clubs, CF3DP can deliver performance-enhancing gear tailored to professional athletes' specifications.
Despite the promise and versatility of CF3DP, it is not without its hurdles. Addressing these challenges is essential for the technology to realize its full potential in large-scale manufacturing. Here, we outline the primary obstacles and the innovative solutions emerging to tackle them.
Material Limitations:
Precision and Control:
Structural Integrity:
Speed and Scalability:
Design Complexity:
Cost Factors:
Regulatory and Standardization:
Sustainability:
The integration of CF3DP into large-scale manufacturing brings with it a host of economic and design implications that reshape the traditional manufacturing landscape. Here we delve into how CF3DP influences cost structures and the design process in manufacturing.
Economic Considerations:
Design Implications:
Impact on the Workforce:
Long-Term Market Implications:
Standardization and Certification:
CF3DP presents a unique set of economic and design implications that challenge traditional manufacturing paradigms. By understanding and addressing these implications, manufacturers can not only optimize the use of CF3DP but also drive innovation and growth within their industries.
As we gaze into the horizon of manufacturing's future, CF3DP looms as a significant player, brimming with potential to usher in a new age of industrial capabilities. Let's extrapolate current trends to forecast where CF3DP might take us.
Advanced Materials and Processes:
Integrated Manufacturing Systems:
Smart Factories and Automation:
Personalization and Mass Customization:
Sustainability and Circular Economy:
Educational and Workforce Shifts:
Regulatory Evolution:
Democratization of Manufacturing:
Global Supply Chains:
Discover the future of composite manufacturing with Addcomposites! Here's how you can get involved:
At Addcomposites, we are dedicated to revolutionizing composite manufacturing. Our AFP systems and comprehensive support services are waiting for you to harness. So, don't wait – get started on your journey to the future of manufacturing today!
The realm of manufacturing stands on the cusp of a new era, one that bridges the gap between the digital and the tangible. At the heart of this transformation is 3D printing, a process that has transitioned from prototyping novelty to a powerhouse of production in its own right. With its roots tracing back to the 1980s, 3D printing, or additive manufacturing, has evolved through leaps and bounds, growing in sophistication, scale, and substance.
Enter Continuous Fiber 3D Printing (CF3DP) — the latest innovation that's set to redefine the manufacturing landscape. This technology is not just an incremental improvement; it's a revolutionary approach that integrates continuous fibers, such as carbon or glass, into a polymer matrix during the printing process. The result? Components that are not just prototypes, but high-performance parts boasting exceptional strength and durability, ready for the most demanding applications.
The implications of CF3DP stretch far and wide, particularly for industries where the integrity and strength-to-weight ratio of materials are non-negotiable. In aerospace, automotive, and marine sectors, the ability to produce large-scale parts that can withstand extreme forces, yet remain light, is nothing short of a game-changer. From the chassis of a race car to the fuselage of a drone, CF3DP is setting the stage for a future where design complexity is no longer a constraint, and efficiency is measured not just in cost, but in performance.
As we delve into the capabilities and prospects of CF3DP, it's crucial to understand that this is not just about printing parts; it's about reimagining the engineering process from the ground up. It's about harnessing the full potential of computational design, material science, and precision engineering to create components that were once deemed impossible. The fusion of continuous fibers into 3D printing heralds a new chapter in manufacturing — one that is poised to deliver innovations that are as robust in structure as they are groundbreaking in concept.
With the high technical acumen of our readers in mind, we will explore the intricate details of CF3DP, from the underlying mechanics to the cutting-edge advancements that are propelling this technology forward. Whether it's the strategic placement of fibers to optimize load paths or the thermal management techniques critical to maintaining material properties, we'll delve into the technicalities that make CF3DP a cornerstone of next-generation manufacturing. So, let's embark on this journey through the intricate dance of fibers and polymers, and unlock the potential that continuous fiber 3D printing promises to the world of large-scale production.
At its core, CF3DP is a specialized branch of additive manufacturing that integrates the power of continuous fibers—such as carbon, glass, or Kevlar—with thermoset or thermoplastic polymers to create composite materials in a single build process. Unlike traditional 3D printing that deposits molten plastic layer by layer, CF3DP intertwines these strong fibers within the matrix material, exponentially enhancing the part's mechanical properties.
The Process: The CF3DP process begins with a spool of fiber filament and a separate spool of thermoplastic filament. The fibers are impregnated with a polymer resin, either before or during the printing process, and then deposited in tandem with the thermoplastic material. This dual-extrusion system is meticulously controlled by software that dictates the path and orientation of the fibers, aligning them along load-bearing paths of the part being printed.
Material Science at Play: The selection of fiber material is pivotal. Carbon fibers are renowned for their high stiffness and strength-to-weight ratio, making them ideal for aerospace and automotive applications. Glass fibers offer durability and cost-effectiveness, suitable for a wide range of uses including recreational equipment and industrial components. Each fiber type brings distinct advantages to the table, allowing engineers to tailor the properties of the final product to meet specific design criteria.
The Technical Edge: CF3DP offers an unparalleled advantage in creating parts with complex geometries that traditional manufacturing methods struggle with. The ability to adjust fiber orientation on-the-fly allows for anisotropic properties—where the material's strength varies with direction—providing strategic reinforcement where it matters most. Moreover, the additive nature of CF3DP means that material is only used where necessary, minimizing waste.
Engineering Precision: The design for CF3DP goes beyond mere geometry. It encapsulates a holistic approach to part creation, where factors such as load-bearing requirements, thermal stresses, and environmental exposure are all considered in the print strategy. Advanced software tools allow for the simulation of various load scenarios, ensuring that the fibers are precisely aligned with anticipated stress vectors, leading to parts that are optimized for both performance and longevity.
The Equation of Strength: In CF3DP, the tensile strength of a printed part can be summarized by the rule of mixtures for a composite material:
σc=Vf⋅σf+Vm⋅σm
where:
This equation underscores the synergy between fiber and polymer, illustrating how the tensile strength of a CF3DP part is a weighted sum of its constituents.
In the next sections, we will delve deeper into how CF3DP is revolutionizing industries with its unique capabilities, the challenges it faces, and the prospects that lie ahead in this dynamic field of manufacturing.
The landscape of CF3DP is rapidly evolving, with technological advancements that refine the process and expand its capabilities. Here, we explore the key developments that are pushing the boundaries of what's possible with CF3DP.
Printer Design Evolution: In the pursuit of higher efficiency and precision, CF3DP printers have undergone significant design enhancements. Modern CF3DP printers boast improved fiber impregnation systems, ensuring that the fibers are fully saturated with resin before being laid down. This is critical to achieving optimal mechanical properties in the final product.
Path Planning and Fiber Orientation: Advances in path planning algorithms have enabled printers to deposit fibers in orientations that exactly mirror the predicted stress patterns of the part in use. This optimization of fiber paths contributes to parts that are not only stronger but also use less material, reducing weight and cost. The orientation of fibers can be dynamically changed mid-print to adapt to complex geometries and loading conditions, a process that is controlled by increasingly sophisticated software.
Thermal Management: CF3DP must carefully control the temperature during the printing process to ensure proper fiber-matrix bonding and prevent warping or distortion. Innovations in thermal management include heated print beds, temperature-controlled print heads, and environment chambers, all designed to maintain the integrity of the materials during the additive process.
Material Compatibility and Multi-Material Printing: The introduction of new fiber materials and hybrid filaments has expanded the potential applications of CF3DP. Printers are now capable of handling a variety of fibers and resins, sometimes within a single print job, to create parts with localized variations in material properties.
Software Integration and Simulation: Software advancements have been critical in CF3DP's progress. Modern CF3DP relies on integrated CAD/CAM systems that can simulate the printing process, predict material behavior, and automatically generate optimized toolpaths. These systems can take into account the anisotropic nature of the printed composites, allowing designers to simulate how the part will perform under real-world conditions.
Real-Time Monitoring and Quality Control: Emerging technologies in real-time monitoring involve sensors and machine vision to oversee the printing process, detecting and correcting errors as they occur. This leads to improved quality control and consistency, reducing the rate of part failure and increasing trust in CF3DP as a manufacturing method.
Automation and AI: The incorporation of artificial intelligence (AI) into CF3DP systems is on the horizon. AI can analyze vast amounts of data to optimize the print process, predict potential issues before they arise, and even suggest design improvements. This intelligence layer aims to streamline the manufacturing process, reducing the need for human intervention and allowing for more complex and reliable part production.
Economic and Scalability Considerations: As CF3DP technologies mature, we are beginning to see a shift toward scalability and economic feasibility. This includes efforts to increase print speeds without sacrificing quality and to develop larger printers capable of producing sizable components in a single build.
Sustainability: Finally, advancements in sustainable materials for CF3DP are being explored. Biocompatible and biodegradable resins, recycled fibers, and green manufacturing practices are emerging, aiming to reduce the environmental footprint of CF3DP.
As CF3DP technology continues to develop, we can anticipate a wave of new applications, improved materials, and manufacturing practices that could redefine industry standards. The future of CF3DP is not only about what can be made but also about the innovation and efficiency with which it can be made.
CF3DP is not just a technological marvel in the lab; it's a transformative force in the field. The technology is making waves across several industries, each with its unique demands and challenges. Let's examine the profound impact CF3DP is having on key sectors.
Aerospace: In the aerospace industry, the stakes are as high as the skies these machines traverse. CF3DP is instrumental in manufacturing components that are robust yet feather-light. The ability to create complex geometries with tailored fiber orientation allows for parts that can endure the stressors of flight while contributing to overall weight reduction, a critical factor in fuel efficiency and payload maximization. The technology is particularly suitable for producing bespoke parts for small production runs, which is common in the aerospace industry.
Automotive: The automotive sector is undergoing a paradigm shift towards lighter, more energy-efficient vehicles. CF3DP steps into this arena with the promise of high-strength, low-weight components that can be custom-designed for specific performance requirements. This is especially beneficial for high-performance vehicles where every kilogram saved can translate into speed and efficiency gains. Furthermore, the technology's ability to iterate designs rapidly accelerates the development cycle, from concept cars to road-ready models.
Marine: For marine applications, the durability of materials is paramount, given the relentless exposure to corrosive saltwater environments. CF3DP offers the advantage of producing parts that can withstand these harsh conditions while improving the vessel's buoyancy and performance. The technology's flexibility in design also enables the creation of unique, hydrodynamic shapes that traditional manufacturing would find challenging.
Construction and Architecture: CF3DP is set to revolutionize the construction industry by enabling the production of complex structural components that are both sturdy and intricate. The ability to print large-scale parts on-site reduces transportation costs and construction times significantly. In architecture, CF3DP allows for the realization of avant-garde designs that were once considered unbuildable.
Medical Devices: In the medical field, CF3DP is beginning to find its footing in creating customized implants and prosthetics. The technology's precision and ability to use biocompatible materials mean that devices can be tailored to the individual's anatomy, offering improved comfort and functionality.
Energy: The energy sector, particularly wind power, benefits from CF3DP through the manufacturing of more efficient and durable turbine blades. The technology's capability to embed continuous fibers means these structures can better withstand the forces they encounter, leading to longer service lives and reduced maintenance costs.
Sporting Goods: CF3DP has also found a niche in the sporting goods industry, where customized equipment is highly valued. From lightweight bicycle frames to durable golf clubs, CF3DP can deliver performance-enhancing gear tailored to professional athletes' specifications.
Despite the promise and versatility of CF3DP, it is not without its hurdles. Addressing these challenges is essential for the technology to realize its full potential in large-scale manufacturing. Here, we outline the primary obstacles and the innovative solutions emerging to tackle them.
Material Limitations:
Precision and Control:
Structural Integrity:
Speed and Scalability:
Design Complexity:
Cost Factors:
Regulatory and Standardization:
Sustainability:
The integration of CF3DP into large-scale manufacturing brings with it a host of economic and design implications that reshape the traditional manufacturing landscape. Here we delve into how CF3DP influences cost structures and the design process in manufacturing.
Economic Considerations:
Design Implications:
Impact on the Workforce:
Long-Term Market Implications:
Standardization and Certification:
CF3DP presents a unique set of economic and design implications that challenge traditional manufacturing paradigms. By understanding and addressing these implications, manufacturers can not only optimize the use of CF3DP but also drive innovation and growth within their industries.
As we gaze into the horizon of manufacturing's future, CF3DP looms as a significant player, brimming with potential to usher in a new age of industrial capabilities. Let's extrapolate current trends to forecast where CF3DP might take us.
Advanced Materials and Processes:
Integrated Manufacturing Systems:
Smart Factories and Automation:
Personalization and Mass Customization:
Sustainability and Circular Economy:
Educational and Workforce Shifts:
Regulatory Evolution:
Democratization of Manufacturing:
Global Supply Chains:
Discover the future of composite manufacturing with Addcomposites! Here's how you can get involved:
At Addcomposites, we are dedicated to revolutionizing composite manufacturing. Our AFP systems and comprehensive support services are waiting for you to harness. So, don't wait – get started on your journey to the future of manufacturing today!