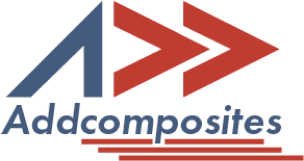
Composite Overwrapped Pressure Vessels (COPVs) are essential components in numerous industries, including aerospace, automotive, and alternative energy. With the demand for lighter and more efficient pressure vessels growing, the adoption of Automated Fiber Placement (AFP) technology in the manufacturing of COPVs has become increasingly popular. This blog post explores the benefits of AFP technology and its innovative applications for COPV tank winding.
AFP technology enables the precise placement of composite fibers, resulting in optimized material usage and reduced waste. This not only lowers production costs but also contributes to a more environmentally friendly manufacturing process.
The controlled and accurate application of fibers using AFP leads to higher-quality composite structures, which ultimately translates to improved product performance. The precise fiber placement ensures better load distribution, increasing the structural strength and durability of the COPVs.
AFP systems can lay multiple tows simultaneously, significantly reducing manufacturing times when compared to traditional hand layup or filament winding processes. This enhanced speed translates to increased production capacity and reduced lead times.
AFP technology allows for the creation of complex geometric shapes and structures, providing greater design flexibility in the development of COPVs. This enables manufacturers to tailor the design of their pressure vessels to meet specific application requirements.
In the aerospace sector, COPVs are used to store high-pressure gases for various applications, such as propulsion systems and life support. AFP technology has been employed to create lightweight, high-performance COPVs that can withstand the harsh conditions of space travel. The reduction in weight leads to significant fuel savings, lower launch costs, and increased payload capacity.
The transition towards cleaner energy sources has generated an increased demand for efficient hydrogen storage solutions. COPVs manufactured using AFP technology offer an attractive solution for storing hydrogen at high pressures. The superior strength-to-weight ratio and durability of these vessels make them ideal for use in hydrogen-powered vehicles and stationary storage applications.
The oil and gas industry also benefits from the application of AFP technology in COPV tank winding. These pressure vessels are used for storing high-pressure gases, such as natural gas and helium. The improved performance and lightweight nature of AFP-manufactured COPVs have the potential to revolutionize the gas storage and transportation sectors.
Automated Fiber Placement technology offers numerous benefits in the manufacturing of COPV tanks, including improved material efficiency, enhanced product performance, increased manufacturing speed, and greater design flexibility. Its innovative applications in industries such as aerospace, hydrogen storage, and high-pressure gas storage demonstrate its potential to revolutionize COPV tank winding processes. As AFP technology continues to advance, we can expect to see further innovations and improvements in the world of composite pressure vessels.
Composite Overwrapped Pressure Vessels (COPVs) are essential components in numerous industries, including aerospace, automotive, and alternative energy. With the demand for lighter and more efficient pressure vessels growing, the adoption of Automated Fiber Placement (AFP) technology in the manufacturing of COPVs has become increasingly popular. This blog post explores the benefits of AFP technology and its innovative applications for COPV tank winding.
AFP technology enables the precise placement of composite fibers, resulting in optimized material usage and reduced waste. This not only lowers production costs but also contributes to a more environmentally friendly manufacturing process.
The controlled and accurate application of fibers using AFP leads to higher-quality composite structures, which ultimately translates to improved product performance. The precise fiber placement ensures better load distribution, increasing the structural strength and durability of the COPVs.
AFP systems can lay multiple tows simultaneously, significantly reducing manufacturing times when compared to traditional hand layup or filament winding processes. This enhanced speed translates to increased production capacity and reduced lead times.
AFP technology allows for the creation of complex geometric shapes and structures, providing greater design flexibility in the development of COPVs. This enables manufacturers to tailor the design of their pressure vessels to meet specific application requirements.
In the aerospace sector, COPVs are used to store high-pressure gases for various applications, such as propulsion systems and life support. AFP technology has been employed to create lightweight, high-performance COPVs that can withstand the harsh conditions of space travel. The reduction in weight leads to significant fuel savings, lower launch costs, and increased payload capacity.
The transition towards cleaner energy sources has generated an increased demand for efficient hydrogen storage solutions. COPVs manufactured using AFP technology offer an attractive solution for storing hydrogen at high pressures. The superior strength-to-weight ratio and durability of these vessels make them ideal for use in hydrogen-powered vehicles and stationary storage applications.
The oil and gas industry also benefits from the application of AFP technology in COPV tank winding. These pressure vessels are used for storing high-pressure gases, such as natural gas and helium. The improved performance and lightweight nature of AFP-manufactured COPVs have the potential to revolutionize the gas storage and transportation sectors.
Automated Fiber Placement technology offers numerous benefits in the manufacturing of COPV tanks, including improved material efficiency, enhanced product performance, increased manufacturing speed, and greater design flexibility. Its innovative applications in industries such as aerospace, hydrogen storage, and high-pressure gas storage demonstrate its potential to revolutionize COPV tank winding processes. As AFP technology continues to advance, we can expect to see further innovations and improvements in the world of composite pressure vessels.