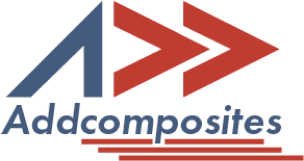
The aerospace industry stands at a pivotal moment in manufacturing evolution. As major aircraft manufacturers pledge to increase production rates to unprecedented levels, traditional autoclave-based composite manufacturing processes are being challenged to meet these demanding requirements within budget and space constraints. This push for higher efficiency, coupled with the industry's perpetual quest for lighter, stronger, and more cost-effective components, has brought resin infusion technologies to the forefront of aerospace innovation.
Traditional prepreg-based manufacturing, while proven and reliable, comes with significant limitations. The requirement for massive autoclaves not only demands substantial capital investment but also creates production bottlenecks that can hinder high-rate manufacturing. These challenges become particularly acute when considering the industry's ambitious goals - some OEMs are targeting production rates exceeding 100 aircraft per month, a scale that would require an unprecedented expansion of manufacturing infrastructure using conventional methods.
Automated Fiber Placement: A Revolutionary Way to Create Composite Parts has shown us that innovation in manufacturing processes is not just possible - it's essential. Resin infusion processes, particularly Resin Transfer Molding (RTM) and Vacuum-Assisted Resin Transfer Molding (VARTM), are emerging as compelling alternatives that promise to address many of these challenges.
Recent success stories highlight the transformative potential of resin infusion technologies:
Mastering Automated Fiber Placement, when combined with resin infusion technologies, offers a pathway to achieving:
As we look toward future aircraft designs, including novel architectures like blended wing bodies and innovations in urban air mobility, the importance of advanced manufacturing processes becomes even more critical. The Future of Composites Manufacturing isn't just about replacing existing methods - it's about enabling new possibilities in aircraft design and production efficiency.
In this comprehensive exploration, we'll delve into how resin infusion technologies are reshaping aerospace manufacturing, examine their current applications and limitations, and look at how automation and innovative solutions are helping overcome traditional barriers to adoption. We'll also explore how modern solutions are making these advanced manufacturing processes more accessible and efficient than ever before.
As we proceed, we'll see how these technologies aren't just theoretical possibilities - they're already transforming how we think about and execute aerospace manufacturing, setting the stage for the next generation of aircraft production.
Resin infusion technologies represent a fundamental shift in how we approach composite manufacturing. Unlike traditional prepreg methods, where the reinforcement comes pre-impregnated with resin, resin infusion processes separate the dry fiber placement from the resin introduction. This separation offers unprecedented flexibility in manufacturing while addressing many of the limitations inherent in conventional processes.
Can It Be Made with AFP? This question often leads us to explore two main variants of resin infusion technology:
RTM employs matched metal tooling to create a closed mold cavity. The process begins with placing dry fiber preforms in the mold, followed by injecting resin under pressure. This approach offers several distinct advantages:
VARTM utilizes a single-sided tool with a vacuum bag, making it particularly suitable for larger structures. As detailed in Understanding Tension and Compaction in AFP, this process offers unique benefits:
The adoption of resin infusion technologies brings multiple advantages that directly address current industry challenges:
Recent advancements have shown that Crafting Superior Composites through resin infusion can achieve:
The process offers significant improvements in production efficiency:
While resin infusion technologies offer compelling advantages, they also present certain challenges that need to be addressed:
Mastering Composite Defect Detection becomes crucial when working with dry fibers. Key considerations include:
Successful implementation requires careful attention to:
Modern solutions, including advanced simulation tools and in-process monitoring systems, are helping manufacturers overcome these challenges, making resin infusion processes increasingly reliable and repeatable for aerospace applications.
As we continue to advance these technologies, the combination of process understanding and innovative solutions is opening new possibilities in aerospace manufacturing, enabling the production of increasingly complex and integrated structures while maintaining the high quality standards demanded by the industry.
The aerospace industry's adoption of resin infusion technologies represents a strategic shift in manufacturing philosophy. While Automated Fiber Placement in Automotive Manufacturing has seen rapid adoption, aerospace implementation has been more measured, focusing on proving the technology through increasingly critical applications.
Several groundbreaking implementations have demonstrated the viability of resin infusion for primary aerospace structures:
The A220's wing represents a watershed moment for resin infusion technology in aerospace. Manufactured by Spirit AeroSystems, this wing demonstrates:
AFP vs Filament Winding for Hydrogen Tank Production shows how different technologies can be optimized for specific applications. The MC-21's wing exemplifies this through:
Automated Fiber Placement: Revolutionizing Aircraft Manufacturing's Competitive Edge is particularly evident in secondary structures, where multiple successful applications include:
The global market for aerospace composites manufactured using resin infusion technologies is showing significant growth potential:
Several key factors are accelerating market adoption:
Things to Consider When Designing for ATL/AFP Manufacturing highlights how proper design can maximize economic benefits:
The industry faces several challenges in broader adoption:
New Era AI to Overcome Expertise Shortages demonstrates how technology is addressing these challenges through:
The future of resin infusion in aerospace manufacturing looks promising, with several trends emerging:
The adoption of resin infusion technologies continues to accelerate as manufacturers recognize the potential for significant cost savings, improved performance, and enhanced manufacturing flexibility. As the technology matures and more success stories emerge, we can expect to see increasingly widespread implementation across the aerospace industry.
The integration of automation into resin infusion processes represents more than just technological advancement – it's a fundamental shift in how we approach composite manufacturing. As highlighted in How to Advance Composite Manufacturing with Machine Learning, Computer Vision, and Digital Twin, automation is becoming increasingly critical for achieving consistent, high-quality results while meeting demanding production rates.
The Insane Engineering Behind Automated Fiber Placement reveals how modern AFP systems are revolutionizing dry fiber placement:
The automation of preform creation has become increasingly sophisticated, addressing several critical aspects:
Modern automated systems enable:
Process Monitoring AI for AFP Composites Manufacturing demonstrates how automated systems are transforming quality assurance:
Automated inspection systems provide:
Optimizing AFP Manufacturing Through Strategic Data Use shows how automation delivers measurable benefits:
The implementation of automation in resin infusion processes faces several challenges:
Data-driven Optimisation for Zero Defect Composites Manufacturing points to several solutions:
The Shift in Composite Manufacturing: From Traditional to Intelligent outlines the path forward:
The role of automation in resin infusion processes continues to evolve, with new technologies and approaches emerging regularly. As these systems become more sophisticated and integrated, they're not just improving current processes – they're enabling entirely new possibilities in composite manufacturing.
In the evolving landscape of aerospace manufacturing, Addcomposites stands at the forefront of democratizing advanced composite manufacturing technologies. Our approach centers on making automated fiber placement and resin infusion processes more accessible, efficient, and cost-effective for manufacturers of all sizes.
The foundation of our offering lies in two flagship systems that address different scales of manufacturing needs. The AFP-XS system exemplifies our commitment to accessibility in automated fiber placement. This single-tow system brings enterprise-level capability to a broader market through its compatibility with major robot brands including Kuka, Fanuc, ABB, Kawasaki, and Yaskawa. Automated Fiber Placement Process: A Revolutionary Way to Create Composite Parts demonstrates how this system can transform manufacturing operations with its quick installation timeframe of just one month.
For high-volume production scenarios, our AFP-X system elevates manufacturing capabilities to new heights. With its four-tow capability and material capacity sixteen times that of the AFP-XS, this system operates at speeds up to 500mm/s while maintaining precise control through advanced sensor systems. The combination of speed and precision makes it ideal for manufacturers ready to scale their production significantly.
The hardware capabilities of our systems are enhanced by our sophisticated software solutions. What is AddPath: Ultimate Solution for Precision Path Planning and Digital Twin showcases our strategic path planning software for AFP operations. AddPath represents a comprehensive solution that encompasses:
Advanced simulation capabilities and digital twin functionality transform the way manufacturers approach process planning and optimization. The seamless integration with Altair FEA software ensures that designs are not just manufacturable but optimized for performance from the start.
For those focusing on Structural Continuous Fiber 3D Printing (SCF3D), our AddPrint software provides specialized capabilities for complex CAD geometry processing. The 12-axis capability enables intricate surface printing, opening new possibilities in component design and manufacturing.
Understanding that successful implementation requires more than just individual components, we've developed comprehensive integration solutions centered around AddCell. This safety cell integration package addresses the full spectrum of implementation needs, from sophisticated safety control systems to precise base positioning and calibration tools. The digital interaction capabilities ensure that operators maintain complete control while maximizing system efficiency.
Temperature control plays a crucial role in composite manufacturing, and our heating solutions reflect this understanding. We offer versatile options including:
Our commitment to flexibility extends to supporting third-party heater integration and the Humm3 Flash lamp system. For manufacturers requiring precise temperature control, our laser system integration capabilities, including solutions from Laserline GmbH, provide options ranging from 2KW to 4KW, with custom power requirements available to meet specific needs.
Understanding Tension and Compaction in AFP highlights the importance of proper material handling and processing. Our accessories line supports this need with specialized materials for AFP and SCF3D systems, precision-engineered compaction rollers, cutting blades, IR lamps, thermal cameras, force sensors, and professional-grade layup tables. These accessories aren't mere add-ons; they're integral components that optimize system performance and ensure consistent, high-quality output.
Our solutions serve diverse sectors within the aerospace industry, from commercial aviation to space applications. For instance, Design for Manufacturing: Composite Helicopter Tailboom (AFP) demonstrates how our systems can be applied to specific aerospace components, ensuring optimal results through:
What truly sets Addcomposites apart is our holistic approach to composite manufacturing automation. Beyond providing hardware and software solutions, we offer comprehensive training, global support, and seamless integration capabilities. Our team works closely with manufacturers to ensure successful implementation, from initial concept through to full production.
Through our commitment to innovation and accessibility, we're helping manufacturers overcome traditional barriers to advanced composite manufacturing, enabling them to achieve higher production rates, better quality, and improved cost-effectiveness in their operations.
The aerospace industry stands on the cusp of a manufacturing revolution, driven by the convergence of automated fiber placement, resin infusion technologies, and digital innovation. As explored in Revolutionizing Composite Manufacturing: The Promise of Future Technologies, these advancements are not just improving existing processes – they're enabling entirely new approaches to aircraft design and production.
The next generation of aircraft will demand manufacturing capabilities far beyond what traditional processes can deliver. Airbus's commitment to having a "Zero e" airplane flying by 2035 exemplifies this transformation. Their revealed concept aircraft, including a blended wing body design, will require manufacturing processes that can efficiently produce large, integrated structures while maintaining strict weight and performance requirements.
Manufacturing the Future: Next-Gen Aerospace Components demonstrates how resin infusion processes, particularly when combined with advanced automation, are uniquely positioned to meet these challenges. The ability to create large, integrated structures with complex geometries while maintaining precise fiber orientation and consistent material properties makes these technologies essential for future aircraft designs.
The future of aerospace manufacturing lies in the seamless integration of multiple advanced technologies. Artificial intelligence and machine learning are revolutionizing process control and optimization. Data-driven Optimisation for Zero Defect Composites Manufacturing shows how these technologies are already being implemented to achieve unprecedented levels of quality and consistency.
Digital twin technology is evolving beyond simple simulation to become an integral part of the manufacturing process. Real-time monitoring and adjustment capabilities are enabling adaptive manufacturing processes that can respond to variations in materials and conditions automatically. This integration of physical and digital systems represents a fundamental shift in how we approach composite manufacturing.
Environmental considerations are becoming increasingly central to aerospace manufacturing decisions. Embracing Circular Economy in Composite Materials outlines how future manufacturing processes must balance performance requirements with environmental responsibility. Resin infusion technologies, with their potential for reduced energy consumption and waste, align perfectly with these goals.
The development of new materials specifically designed for resin infusion processes continues to accelerate. From toughened resin systems to advanced fiber architectures, these materials are pushing the boundaries of what's possible in composite manufacturing. The integration of natural fibers and bio-based resins represents another exciting frontier, particularly for interior components and secondary structures.
The emerging urban air mobility (UAM) sector presents unique opportunities for resin infusion technologies. These vehicles require manufacturing processes that can efficiently produce complex geometries while maintaining strict weight and performance requirements. The Rise of Continuous Fiber 3D Printing in Large-Scale Production demonstrates how advanced manufacturing techniques are enabling these new applications.
Unlike traditional aerospace manufacturing, UAM producers aren't constrained by legacy systems and established processes. This freedom allows them to adopt innovative manufacturing approaches from the ground up, potentially establishing new standards for aerospace production efficiency and flexibility.
The future of aerospace manufacturing will demand unprecedented production rates while maintaining the highest quality standards. Automating the Future: The Role of AFP in Next-Generation Manufacturing explores how automated systems are evolving to meet these challenges. The integration of robotics, advanced sensor systems, and intelligent process control is creating manufacturing cells capable of operating with minimal human intervention.
As manufacturing processes become more automated and digitally integrated, the role of the workforce is evolving. Future aerospace manufacturing will require a new generation of skilled workers who understand both composite materials and digital systems. This evolution creates opportunities for more efficient operations while highlighting the importance of comprehensive training and development programs.
Looking ahead, several key areas will drive continued innovation in aerospace manufacturing. Process simulation and optimization tools will become increasingly sophisticated, enabling manufacturers to validate and refine processes virtually before physical implementation. The development of new sensor technologies and real-time monitoring systems will further enhance quality control and process consistency.
The integration of artificial intelligence will extend beyond process control to encompass design optimization, predictive maintenance, and automated quality assurance. These advances will enable truly intelligent manufacturing systems capable of self-optimization and adaptation.
The future of aerospace manufacturing through resin infusion technologies is bright, but realizing its full potential will require continued investment in research, development, and implementation. Success will come to those manufacturers who embrace these technologies while maintaining the flexibility to adapt to emerging opportunities and challenges. As we move forward, the combination of advanced materials, intelligent automation, and innovative design approaches will continue to transform how we manufacture aircraft components, enabling the next generation of aerospace innovation.
The aerospace manufacturing landscape is undergoing a fundamental transformation, driven by the convergence of resin infusion technologies, advanced automation, and digital innovation. As demonstrated throughout our exploration, these technologies aren't just theoretical possibilities – they're proven solutions already delivering results in production environments. From the Airbus A220's resin-infused wing to the MC-21's innovative structures, we're seeing concrete evidence of how these technologies can revolutionize aerospace manufacturing.
Manufacturing and Recycling of Carbon Fiber Thermoplastic Composites shows us that the impact of these technologies extends far beyond simple process improvements. The ability to create larger, more integrated structures while reducing costs and improving quality represents a paradigm shift in how we approach aerospace manufacturing. This shift enables new aircraft architectures, improved performance, and enhanced sustainability – all critical factors for the industry's future.
The business case for adopting resin infusion technologies has never been stronger. The combination of reduced capital requirements, lower operating costs, and improved production efficiency creates compelling advantages over traditional manufacturing methods. When coupled with the potential for increased automation and reduced waste, these technologies offer a clear path to improved competitiveness in an increasingly challenging market.
Things to Consider When Conducting Composites Repair reminds us that successful implementation requires careful consideration of multiple factors. The integration of comprehensive solutions, from automated fiber placement to advanced process control systems, provides manufacturers with the tools they need to succeed in this evolution.
For manufacturers considering the adoption of resin infusion technologies, the path forward is clear. The first step is understanding your specific needs and challenges. Whether you're looking to improve production efficiency, reduce costs, or enable new design possibilities, these technologies offer solutions that can be tailored to your requirements.
The next step is partnering with experienced providers who can guide you through the implementation process. Companies like Addcomposites offer comprehensive solutions that address the full spectrum of needs, from hardware and software to training and support. Our approach focuses on making advanced manufacturing technologies accessible and effective for organizations of all sizes.
The Future of Composites Manufacturing isn't just about new technologies – it's about enabling new possibilities. As we continue to push the boundaries of what's possible in aerospace manufacturing, the combination of resin infusion technologies and advanced automation will play an increasingly crucial role in shaping the industry's future.
We invite you to explore how these technologies can benefit your manufacturing operations. Whether you're looking to optimize existing processes or enable entirely new capabilities, our team is ready to help you navigate the path forward. Contact us to learn more about our solutions and how we can help you achieve your manufacturing goals.
The future of aerospace manufacturing is being written today, and resin infusion technologies are playing a central role in this evolution. By embracing these technologies and working with experienced partners, manufacturers can position themselves at the forefront of this transformation, ready to meet the challenges and opportunities that lie ahead.
Start your journey toward advanced manufacturing capabilities today. Visit our website to learn more about our solutions, or contact our team to discuss your specific needs. Together, we can help you achieve your manufacturing goals and prepare for the future of aerospace manufacturing.
This blog post draws significantly from the comprehensive research presented in:
Huberty, W., Roberson, M., Cai, B., & Hendrickson, M. (2024). State of the Industry – Resin Infusion: A Literature Review. DOT/FAA/TC-23/3, Federal Aviation Administration William J. Hughes Technical Center, Aviation Research Division.
Market data and statistics cited in this blog post are derived from publicly available industry reports and the primary source document (DOT/FAA/TC-23/3). All figures should be verified independently for the most current information.
This blog post was developed with permission using information from the FAA Technical Center's research report (DOT/FAA/TC-23/3). The views and conclusions contained in this document are those of the authors and should not be interpreted as representing the official policies, either expressed or implied, of the Federal Aviation Administration or the U.S. Government.