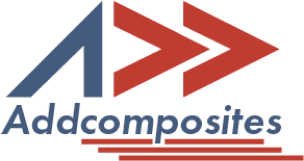
In the pursuit of space exploration, every kilogram matters. As we push the boundaries of human space flight and aim for destinations beyond low Earth orbit, the need for lighter, more efficient spacecraft components becomes increasingly crucial. Among these components, cryogenic fuel tanks stand as one of the most critical yet challenging elements to optimize.
For over five decades, metal cryogenic tanks have been the workhorses of space missions, carrying the liquid hydrogen (LH2) and liquid oxygen (LOX) necessary to launch both human crews and payloads into space. However, a remarkable statistic highlights the importance of these components: approximately 70% of a launch vehicle's dry mass consists of fuel and oxidizer tanks. This single fact presents both a challenge and an opportunity for aerospace engineers and materials scientists.
Composite materials offer a potential revolution in cryotank design and performance. By transitioning from traditional metal tanks to composite structures, engineers project weight reductions of up to 30% compared to aluminum craft—a transformation that could dramatically increase payload capacity and reduce launch costs.
Despite their promising potential, several technical hurdles have historically prevented the widespread adoption of composite cryotanks in launch vehicles:
The NASA Composite Cryotank Technology Development (CCTD) project emerged as a concentrated effort to address these challenges. Through innovative manufacturing processes and advanced material applications, the project aimed to bridge the gap between laboratory concepts and flight-ready hardware.
One of the most significant obstacles in implementing new aerospace technologies lies in crossing what's known as the "valley of death"—the challenging transition from early development (Technology Readiness Levels 2-3) to flight incorporation (levels 8-9). The CCTD program specifically targeted this gap, focusing on advancing composite cryotank technology to demonstration levels (5-6) through practical, full-scale testing.
The stakes are high: successful development of composite cryotanks could revolutionize not just traditional launch vehicles, but enable new possibilities in:
Advanced manufacturing techniques, particularly automated fiber placement and out-of-autoclave curing, stand at the forefront of making these possibilities reality. As we'll explore in this article, the journey from concept to functional composite cryotanks represents one of the most significant advances in space technology of the past decade.
The history of composites in cryogenic tank development spans over three decades, marked by ambitious programs, groundbreaking successes, and instructive failures. Each program contributed vital lessons that would eventually shape modern composite cryotank technology.
The journey began during the Reagan administration in 1982 with the National Aerospace Plane (NASP) program, designated as the X-30. This DARPA-funded initiative aimed to create something unprecedented: a single-stage-to-orbit (SSTO) spaceplane capable of reaching Mach 25. The program's ambitious goals created an urgent need for innovative composite solutions.
McDonnell Douglas Corporation (MDC) achieved a significant milestone in 1987 by completing their first composite cryotank. Their design featured a conformal load-bearing structure—a revolutionary concept at the time. The team initially explored thermoplastic graphite-reinforced materials for their high glass transition temperature but ultimately opted for a more practical 350°F amine-curing toughened epoxy system. This project marked the first successful low-temperature liquid hydrogen testing of a large composite cryotank.
The early 1990s saw the Department of Defense's Strategic Defense Initiative Organization (SDIO) launch the DC-X program. This initiative aimed to create a rapidly reusable vertical takeoff and landing (VTOL) vehicle. The program evolved into NASA's DC-XA, which made history by incorporating the first composite cryotank ever used on a flight vehicle. The 2.4-meter diameter tank featured:
This achievement demonstrated that composite manufacturing techniques could produce flight-worthy cryogenic fuel containers.
The late 1990s brought the X-33 program, part of NASA's Space Launch Initiative (SLI). Lockheed Martin's design featured a revolutionary multi-lobed honeycomb sandwich structure tank, approximately 3 meters in size. However, the program encountered significant challenges during testing:
The X-33 experience provided crucial lessons about the importance of:
While these early programs encountered challenges, they laid essential groundwork for future developments. Key learnings included:
These historical programs highlighted both the immense potential and significant challenges of composite cryotanks. Each setback and success contributed to our understanding of how to effectively design, manufacture, and implement these critical components. As we moved into the modern era of composite cryotank development, these lessons would prove invaluable in shaping new approaches and technologies.
The Composite Cryotank Technology Development (CCTD) program represented a fundamental shift in approach to developing aerospace technology. Unlike traditional government-funded research that focused primarily on advancing basic knowledge, CCTD aimed to bridge the critical gap between laboratory concepts and flight-ready systems through large-scale experimentation and ground-based testing.
The CCTD program set ambitious yet precise targets:
To achieve these goals, the program focused on developing automated composite manufacturing processes that could scale to full production.
The program adopted a two-phase strategy:
The program introduced several groundbreaking technical solutions:
The program brought together key industry players:
The program implemented a comprehensive validation strategy:
The program addressed key risks through:
This structured approach to development helped ensure that each technological advancement was thoroughly validated before integration into the final design. The CCTD program demonstrated that with proper planning and execution, complex composite structures could be manufactured reliably and efficiently for critical aerospace applications.
The success of the CCTD program hinged on several groundbreaking design features that addressed historical challenges in composite cryotank development. These innovations represented a significant leap forward in composite design for manufacturing, combining theoretical advances with practical solutions.
One of the most significant innovations was the elimination of the traditional belly-band joint through one-piece wall construction:
The tank's wall construction featured a sophisticated hybrid laminate design:
The critical tank-to-skirt interface utilized a revolutionary y-joint design:
The implementation of fluted core skirts represented a major advancement over traditional honeycomb structures:
The design incorporated advanced monitoring systems:
Practical considerations for operations were built into the design:
The design incorporated features specifically for manufacturing efficiency:
Several design elements focused on maximizing performance:
These design features worked in concert to create a composite cryotank that not only met but exceeded the program's ambitious goals for weight reduction and performance improvement. The success of these innovations has laid the groundwork for future developments in composite pressure vessel technology.
The manufacturing phase of the CCTD program represented a crucial step in proving that advanced composite manufacturing could move beyond theory to practical implementation. The process combined cutting-edge automation with precise quality control at Boeing's Advanced Development Center (ADC).
The manufacturing infrastructure required several specialized components:
The manufacturing process followed a systematic progression:
The production process involved several key stages:
Several breakthrough manufacturing techniques were employed:
Comprehensive quality measures were implemented throughout:
Careful attention was paid to material handling and processing:
Final assembly required precise coordination:
Key challenges were addressed through innovative solutions:
The manufacturing process demonstrated that complex composite structures could be produced reliably and efficiently, setting new standards for aerospace manufacturing. The success of these manufacturing methods has established a foundation for future composite pressure vessel production, proving that automated composite manufacturing can meet the demanding requirements of space applications.
The success of the CCTD program hinged not just on innovative design and manufacturing, but on rigorous testing that validated performance under real-world conditions. This comprehensive testing program represented one of the most thorough evaluations of composite cryogenic structures ever conducted.
The testing program established clear criteria for success:
Testing proceeded through multiple phases:
Testing was conducted at NASA's Marshall Space Flight Center, utilizing:
The testing followed a methodical progression:
Comprehensive monitoring systems were employed:
Key findings demonstrated success in multiple areas:
Specialized testing verified hydrogen containment:
Durability was verified through extensive cycling:
The testing program validated several critical aspects:
The comprehensive testing program not only validated the performance of the composite cryotanks but also established new standards for testing and certification of large-scale composite structures for space applications. The successful completion of these tests marked a significant milestone in the advancement of composite technology for aerospace applications.
The CCTD program achieved remarkable success in advancing composite cryotank technology, demonstrating innovations in composite materials that have significant implications for future aerospace applications. The program's achievements extended beyond mere technical success to establish new paradigms in aerospace manufacturing.
The program met or exceeded its primary objectives:
Significant progress was made in manufacturing capabilities:
The program successfully bridged the development gap:
The program demonstrated significant cost advantages:
The program demonstrated environmental benefits:
The program's success has broad implications:
The program generated valuable intellectual capital:
The program opened new possibilities for:
The program confirmed the viability of:
The CCTD program's achievements represent a significant leap forward in aerospace manufacturing capability, establishing new standards for composite structure production. These results not only validated the program's objectives but also opened new possibilities for future aerospace applications.
The successful completion of the CCTD program represents more than just a technological achievement; it marks a pivotal moment in aerospace manufacturing. The implications of this success extend far beyond the immediate accomplishments, setting the stage for a new era in space exploration and aerospace innovation.
The program has opened several promising avenues for advancement:
The program's success catalyzes broader industry changes:
New possibilities emerge for future development:
The program's achievements enable new possibilities:
The program advances sustainability goals:
Key areas for continued advancement include:
The CCTD program has demonstrated that composite cryotanks are not just feasible but represent a superior solution for next-generation space vehicles. The program's success in achieving its primary objectives—33% weight reduction and 20-25% cost savings—while advancing manufacturing readiness levels marks a significant milestone in aerospace technology.
Key takeaways include:
The CCTD program's achievements have laid a solid foundation for the future of aerospace manufacturing. As the industry moves forward, the lessons learned and technologies developed through this program will continue to influence and shape the next generation of space exploration vehicles and advanced aerospace applications.
This program demonstrates that with proper planning, innovative design, and rigorous execution, complex composite structures can be manufactured reliably and efficiently for critical aerospace applications. The future of space exploration looks brighter with these advanced materials and manufacturing processes at our disposal.
This article draws primarily from the comprehensive work:
McCarville, D. A., Guzman, J. C., Dillon, A. K., Jackson, J. R., & Birkland, J. O. (2024). "Design, Manufacture and Test of Cryotank Components." In Comprehensive Composite Materials II. DOI:10.1016/B978-0-12-803581-8.09958-6
The success of the CCTD program demonstrates the immense potential of advanced composite manufacturing in aerospace applications. At Addcomposites, we're making these cutting-edge technologies accessible to manufacturers of all sizes.
Let's work together to bring the next generation of composite manufacturing capabilities to your facility.
This article was crafted with technical accuracy and industry insight to provide value to manufacturers, engineers, and technology leaders in the composite manufacturing space. For more information about implementing advanced manufacturing solutions in your operations, contact Addcomposites today.