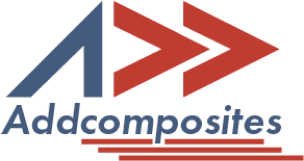
The article examines the development of Automated Tape Laying (ATL) as a manufacturing process for layering material, known as prepreg tape, onto a mold surface in a specific direction to build up layers. The process is similar to additive manufacturing, or the reverse of machining, as material is added rather than removed. The development of these systems has a long history, starting with the use of carbon fiber in aerospace manufacturing in the 1960s. The article discusses the various developmental stages of ATL and explains why they function in their current form and why they may not be in high demand.
Automated Tape Laying (ATL) is a manufacturing process in which a continuous sheet of material, known as prepreg tape, is added to a mold surface in a specific direction to build up layers in different directions, resulting in a layup. The process can be thought of as a form of additive manufacturing, or inverse machining, as the material is added rather than removed through machining.
In conclusion, the development of Automated Tape Laying (ATL) has evolved significantly since its inception in the 1960s. From its early beginnings as a process specifically developed for carbon fiber and aerospace manufacturing, the technology has undergone numerous changes and advances. In the 1980s and 1990s, challenges such as high layup speeds, difficulties in delivering tape with defined compaction pressures, and limited heating capabilities were addressed through the development of new systems and technologies. In the years since, ATL has been further refined and diversified, with a focus on increasing productivity and addressing specific layup issues. Despite the significant progress made in the field, ATL Today, they see very limited usage in aerospace and renewable energy industries owing to their high initial capital expenditures, limited geometric complexity capabilities, and higher material wastage rates than AFPs.
Addcomposites is the provider of the Automated Fiber Placement (AFP) ecosystem - including the Fiber Placement System (AFP-XS), 3D Simulation and Programming Software (AddPath), and Robotic Cells (AddCell). With the leasing program for the AFP system (AFPnext), composites manufacturers can work with thermosets, thermoplastics, dry fiber placement, or in combination with 3D Printers on a monthly basis.
The article examines the development of Automated Tape Laying (ATL) as a manufacturing process for layering material, known as prepreg tape, onto a mold surface in a specific direction to build up layers. The process is similar to additive manufacturing, or the reverse of machining, as material is added rather than removed. The development of these systems has a long history, starting with the use of carbon fiber in aerospace manufacturing in the 1960s. The article discusses the various developmental stages of ATL and explains why they function in their current form and why they may not be in high demand.
Automated Tape Laying (ATL) is a manufacturing process in which a continuous sheet of material, known as prepreg tape, is added to a mold surface in a specific direction to build up layers in different directions, resulting in a layup. The process can be thought of as a form of additive manufacturing, or inverse machining, as the material is added rather than removed through machining.
In conclusion, the development of Automated Tape Laying (ATL) has evolved significantly since its inception in the 1960s. From its early beginnings as a process specifically developed for carbon fiber and aerospace manufacturing, the technology has undergone numerous changes and advances. In the 1980s and 1990s, challenges such as high layup speeds, difficulties in delivering tape with defined compaction pressures, and limited heating capabilities were addressed through the development of new systems and technologies. In the years since, ATL has been further refined and diversified, with a focus on increasing productivity and addressing specific layup issues. Despite the significant progress made in the field, ATL Today, they see very limited usage in aerospace and renewable energy industries owing to their high initial capital expenditures, limited geometric complexity capabilities, and higher material wastage rates than AFPs.
Addcomposites is the provider of the Automated Fiber Placement (AFP) ecosystem - including the Fiber Placement System (AFP-XS), 3D Simulation and Programming Software (AddPath), and Robotic Cells (AddCell). With the leasing program for the AFP system (AFPnext), composites manufacturers can work with thermosets, thermoplastics, dry fiber placement, or in combination with 3D Printers on a monthly basis.