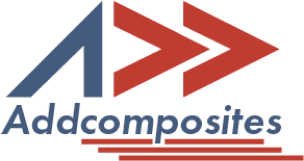
Automated Fiber Placement (AFP) technology has revolutionized the manufacturing of composite structures across various industries. As we explore the intricacies of this advanced manufacturing process, we'll also highlight innovative solutions from companies like Addcomposites, a Finnish pioneer in AFP technology.
In the quest for superior performance across various industries, engineers have long grappled with the limitations of traditional materials. Plastics, while lightweight and easily moldable, often fall short in strength and stiffness, making them unsuitable for many high-performance applications. Metals, the backbone of engineering for centuries, offer excellent strength and durability but at the cost of high density, a critical drawback in weight-sensitive fields like aerospace and automotive engineering.
Enter composite materials – a revolutionary solution that combines the best attributes of different material classes. Composites offer an enticing array of possibilities: structures that are incredibly strong yet remarkably light, with customizable thermal properties and design flexibility. From aircraft components lighter than aluminum yet stronger than steel to wind turbine blades that withstand immense forces while maintaining optimal aerodynamics, composites have opened new frontiers in material engineering.
However, the road to composite supremacy was initially paved with significant challenges:
Automated Fiber Placement (AFP) technology emerged as a game-changer, addressing many of the challenges associated with composite manufacturing. The evolution of AFP has been nothing short of remarkable:
Today, AFP technology stands at the forefront of advanced manufacturing, poised to revolutionize industries far beyond its aerospace origins. From automotive to renewable energy, from marine applications to the burgeoning field of humanoid robotics, AFP is opening new possibilities in design and production.
This comprehensive exploration of Automated Fiber Placement technology will guide you through:
As we embark on this journey through the world of Automated Fiber Placement, prepare to discover how this technology is not just changing the way we manufacture but also expanding the boundaries of what's possible in material engineering and product design. Whether you're an industry professional, an engineering student, or simply curious about cutting-edge technology, this exploration of AFP will provide you with a comprehensive understanding of a technology that's shaping the future of manufacturing.
Automated Fiber Placement (AFP) is an advanced manufacturing process designed to efficiently create complex composite structures. At its core, an AFP system draws composite material from a storage unit, routes it through a sophisticated delivery system, and precisely places it onto a substrate using a combination of heat and pressure.
The process begins with material spools, which may include a backing film for certain materials like thermoset prepregs. The composite tape is then guided through a cut, clamp, and feed (CCF) mechanism before being applied to the substrate. This basic process remains consistent across various material types, including thermosets, thermoplastics, and dry fibers, with minor adjustments to accommodate each material's specific requirements.
The journey of AFP technology began in the late 1960s and early 1970s, evolving from earlier composite manufacturing techniques. The concept of using individual tows instead of wide tapes was first documented in 1974, marking a significant shift from Automated Tape Laying (ATL) methods.
Hercules Aerospace (now part of ATK) and Cincinnati Machine were pioneers, starting development of AFP systems in the early 1980s. These early machines combined the differential payout capability of filament winding with the compaction and cut-restart capabilities of ATL. By the late 1980s, AFP machines became commercially available and were adopted by major aerospace companies like Boeing, Lockheed, and Northrop.
The 1990s saw significant advancements in AFP technology. Systems capable of delivering up to 24 tows at once were developed, dramatically increasing productivity. The ability to steer fibers along curvilinear paths was a game-changer, allowing for more complex geometries and optimized fiber orientations.
The turn of the millennium brought focus to improving process reliability and productivity. Innovations in automated inspection, high-speed systems, and modular AFP heads marked this era. By 2010, highly accurate robots were demonstrating remarkable precision, with a 3-sigma accuracy of ±0.08 mm.
Today, AFP technology continues to evolve, with current research focusing on high-throughput systems, minimal defect layups, and in-situ thermoplastic processing. The integration of AFP with other advanced manufacturing technologies promises to further expand its capabilities and applications.
Modern AFP systems have evolved to incorporate filament winding capabilities, offering a best-of-both-worlds approach that significantly expands manufacturing possibilities. This convergence of technologies represents a major leap forward in composite manufacturing flexibility.
Filament winding, traditionally used for creating cylindrical or spherical structures, excels in high-speed production of parts with continuous fiber reinforcement. By integrating these capabilities into AFP systems, manufacturers can now switch seamlessly between precise layup and high-speed winding operations within a single setup.
The advantages of this hybrid approach are numerous. For complex parts with both open and closed sections, the system can use AFP for precise layup on open surfaces and switch to filament winding for closed, cylindrical sections. This is particularly beneficial in industries like aerospace, where components often combine multiple geometric features.
The key to this versatility lies in advanced control systems and software. These systems manage the transition between AFP and winding modes, adjusting parameters like fiber tension, compaction pressure, and heating on the fly. For winding operations, the software calculates optimal winding angles and patterns, ensuring structural integrity while maximizing production speed.
Moreover, this combined capability allows for innovative manufacturing strategies. For instance, a part might start with a filament-wound core for speed and continuous reinforcement, followed by precisely placed AFP layers for local reinforcement or to create specific surface features.
The integration of AFP and filament winding capabilities in a single system not only enhances production flexibility but also opens up new possibilities in part design. Engineers can now conceive of structures that leverage the strengths of both processes, potentially leading to lighter, stronger, and more efficient composite parts.
Addcomposites offers two advanced AFP systems that exemplify the latest in fiber placement technology:
AFP-XS: A compact system designed to upgrade existing robots for research and small batch production. It's capable of aerospace-grade quality layups and is compatible with a wide range of materials.
AFP-X: A robust system for high-volume production, featuring increased material capacity and advanced sensors for continuous, precise operations on complex aerospace and large components.
These systems represent significant advancements in making AFP technology more accessible and versatile across industries.
The journey of automated fiber placement begins with proper material preparation. Composite materials typically come in the form of tapes, which require specific handling:
Once prepared, the material must be carefully loaded into the AFP system:
With the material loaded and the AFP program ready, the actual layup process begins:
The cutting and restarting process is crucial for creating complex layups:
As layers accumulate, several factors come into play:
Through this meticulous step-by-step process, AFP systems can create complex, high-performance composite parts with a level of precision and consistency unattainable through manual methods. The ability to fine-tune each aspect of the layup process contributes to the production of lightweight, strong, and highly engineered composite structures.
To streamline the AFP process, Addcomposites offers sophisticated software solutions:
The choice of material in Automated Fiber Placement (AFP) significantly influences the manufacturing process, final product characteristics, and production economics. Let's explore the main material types used in AFP and their implications:
Prepregs, or pre-impregnated fibers, are the traditional go-to material for AFP in high-performance applications:
Dry fiber tapes are increasingly popular, especially when combined with subsequent resin infusion processes:
Thermoplastic composites offer unique advantages in AFP:
Towpregs represent an innovative approach to prepreg manufacturing:
When selecting materials for AFP, several factors come into play:
The choice of material in AFP is not just about the final part properties, but also about optimizing the entire manufacturing process. As AFP technology continues to evolve, the ability to process a wide range of materials efficiently is becoming a key factor in its adoption across various industries. The trend towards materials like Towpregs showcases the industry's drive towards combining high performance with cost-effectiveness, potentially opening up new applications for AFP technology.
Addcomposites' AFP systems, particularly the AFP-XS, showcase remarkable material versatility:
This versatility allows manufacturers to explore a wide range of composite materials and manufacturing techniques using a single system.
Automated Fiber Placement (AFP) technology, while advanced, still faces several engineering challenges. However, innovative solutions and evolving technologies are continuously addressing these issues, making AFP more accessible and efficient.
Challenge:
Solutions:
Challenge:
Solutions:
Challenge:
Solutions:
Challenge:
Solutions:
Challenge: Higher resin content leading to more residue in the AFP system.
Solution: Implementing regular cleaning routines and designing systems for easy maintenance access.
Challenge: Potential for resin buildup, though less than towpregs.
Solution: Developing streamlined cleaning processes and using materials optimized for AFP processing.
Challenge: Accumulation of fiber debris in narrow channels, particularly in the cutter area.
Solution:
Challenge: High heat exposure causing roller degradation.
Solution:
By addressing these challenges with innovative solutions, the AFP industry is moving towards more accessible, efficient, and versatile systems. The shift from large, complex machines to more compact, user-friendly systems is democratizing AFP technology, making it available to a broader range of industries and applications. This evolution is not only solving existing problems but also opening up new possibilities in composite manufacturing.
Addcomposites addresses several key challenges in AFP technology:
Automated Fiber Placement (AFP) technology has found its way into a diverse range of industries, revolutionizing the manufacturing of composite structures. From traditional aerospace applications to emerging fields like humanoid robotics, AFP systems are proving their versatility and value. Let's explore the key applications and case studies across various sectors:
In the automotive sector, AFP is being used to produce lightweight body panels, impact-resistant structures, and components for electric and hydrogen-powered vehicles
In the clean energy sector, AFP technology is being employed for the production of efficient, large-scale wind turbine blades
The versatility of modern AFP systems, particularly compact and adaptable designs, is enabling a new era of composite manufacturing across these diverse sectors. By offering consistent quality, data-driven production, and the ability to work with a wide range of materials, AFP technology is not only improving existing applications but also opening doors to new possibilities in composite structure design and manufacturing. As industries continue to demand lighter, stronger, and more efficient components, AFP systems are poised to play an increasingly crucial role in meeting these evolving needs.
Addcomposites' solutions have found applications across various industries:
As Automated Fiber Placement (AFP) technology continues to evolve, it is poised to play an increasingly crucial role in advanced manufacturing. The future of AFP is characterized by greater versatility, integration with other technologies, and expansion into new markets. Here are the key trends and developments shaping the future of AFP:
The future of AFP technology is characterized by enhanced software capabilities for path planning, process simulation, and optimization, integrating design, manufacturing, and quality assurance into a unified digital ecosystem
The development of integrated hybrid manufacturing cells, combining AFP, filament winding, and additive manufacturing in single, flexible production units, represents a significant trend in the evolution of AFP technology
The future of AFP technology is characterized by its increasing versatility, integration with other advanced manufacturing technologies, and expansion into new markets. As AFP systems become more compact, adaptable, and cost-effective, they are likely to find applications in a wider range of industries, from aerospace and automotive to robotics and sustainable energy.
The convergence of AFP with additive manufacturing, advanced robotics, and sophisticated digital tools is set to revolutionize how complex composite structures are designed and produced. This evolution will not only enhance the capabilities of AFP but also contribute to more sustainable, efficient, and innovative manufacturing practices across various sectors.
As these technologies mature, we can expect to see AFP playing a crucial role in addressing global challenges, from climate change mitigation through lightweight transportation to the development of advanced robotics for various applications. The future of AFP is not just about improving existing processes, but about reimagining what's possible in composite manufacturing and opening new frontiers in material science and engineering.
Addcomposites is at the forefront of several trends shaping the future of AFP technology:
As AFP technology continues to evolve, companies like Addcomposites are playing a crucial role in driving innovation, improving accessibility, and expanding the applications of this transformative manufacturing process.
As we've explored throughout this comprehensive look at Automated Fiber Placement (AFP) technology, it's clear that we are witnessing a revolutionary shift in composite manufacturing. AFP has not only overcome many of the initial challenges associated with composite production but has also opened up new possibilities in design, efficiency, and application across a wide range of industries.
The future of AFP technology is bright and full of potential. As systems become more compact, versatile, and cost-effective, we can expect to see AFP playing a crucial role in addressing some of the most pressing challenges of our time:
The ongoing developments in AFP technology – from enhanced process control and multi-material capabilities to integration with additive manufacturing – promise to further expand its capabilities and applications. As the technology continues to mature, we can anticipate more industries recognizing the potential of AFP to revolutionize their manufacturing processes and product designs.
Automated Fiber Placement stands at the intersection of materials science, robotics, and digital manufacturing. It represents not just an improvement in how we make things, but a fundamental shift in what we can make. As we look to a future that demands stronger, lighter, and more efficient structures across all sectors, AFP emerges as a key enabling technology.
For engineers, designers, and industry leaders, staying abreast of AFP developments will be crucial in maintaining a competitive edge. For researchers and innovators, AFP presents a rich field for exploration, with the potential for groundbreaking discoveries in materials, processes, and applications.
The journey of AFP from a specialized aerospace technology to a versatile, accessible manufacturing process is a testament to the power of innovation and the importance of cross-disciplinary collaboration. As we continue to push the boundaries of what's possible with composites, AFP will undoubtedly play a central role in shaping the future of manufacturing and material science.
In conclusion, Automated Fiber Placement is not just a manufacturing technology; it's a gateway to new possibilities in design, efficiency, and sustainability across industries. As we move forward, the potential of AFP to transform our world – from the cars we drive to the energy we harness and even the robots that may one day work alongside us – is limited only by our imagination and ingenuity.