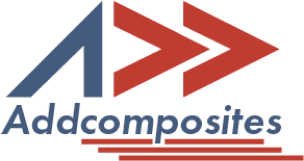
The electric vehicle (EV) industry is undergoing a period of rapid growth and innovation, driven by increasing consumer demand and government regulations aimed at reducing carbon emissions. A key aspect of this transformation is the growing use of composite materials in EV manufacturing. Composites offer a unique combination of lightweight, high strength, and design flexibility, making them ideal for enhancing vehicle performance, efficiency, and safety. This report explores the current state of composite materials in the EV industry, focusing on how automation techniques such as Automated Fiber Placement (AFP), filament winding, Large Format Additive Manufacturing (LFAM), and large-format continuous fiber 3D printing are adding value to the manufacturing process. It also examines the role of Addcomposites and its systems in influencing production automation in this sector.
Composite materials, typically consisting of a reinforcing fiber and a polymer matrix, have emerged as a crucial element in modern EV design. Their high strength-to-weight ratio allows for significant weight reduction compared to traditional materials like steel and aluminum, directly contributing to improved energy efficiency and extended driving range1. This is particularly important for EVs, where battery weight is a major factor affecting performance. By reducing the overall mass of the vehicle, composites enable EVs to travel further on a single charge, addressing one of the key concerns for potential EV buyers2.
Several types of composite materials are used in EV design, each with its own set of properties and advantages:
Beyond lightweighting and structural applications, composite materials show promise in energy harvesting for electric vehicles. Energy harvesting involves converting ambient energy into usable electrical energy, which can reduce reliance on the vehicle's battery and enhance overall energy efficiency4. Composites can be used in various types of energy harvesters:
Studies have shown that incorporating carbon nanotubes into a copper matrix can increase the electrical current capacity of copper wires by up to 14%, leading to more efficient and power-dense electric motors5. This highlights the potential of composite materials to enhance the performance of key EV components.
The ability to engineer composite materials with specific thermal properties is crucial for managing the temperature of EV batteries6. By effectively regulating battery temperature, composites can contribute to improved battery efficiency, lifespan, and overall vehicle performance.
Composites also exhibit dielectric properties, meaning they can act as electrical insulators7. This is crucial in EVs for protecting sensitive electronic components and ensuring safety.
Furthermore, composites excel at absorbing and dispersing impact energy, contributing to improved crashworthiness and passenger safety8.
Specifically, glass reinforced composites (GRC) offer a cost advantage compared to other high-performance materials like aluminum and titanium, making them an attractive option for EV battery enclosures and structural components9.
To further enhance their properties, composite materials can be modified with additions like polyurethane coatings and polyamide fibers to increase abrasion resistance10. This allows for the creation of even more durable and long-lasting components.
The EV industry is increasingly adopting automation techniques to enhance the manufacturing process of composite parts. These techniques not only improve production efficiency and reduce costs 11 but also enable the creation of complex designs and optimized structures.
Automated Fiber Placement (AFP)
AFP is a sophisticated manufacturing process that involves the precise and automated laying of continuous fiber reinforcements onto a mold or mandrel12. A robotic arm or gantry system, guided by advanced software, places the fibers in predetermined paths, ensuring optimal fiber orientation and compaction. This technology offers several benefits in EV manufacturing:
From a technical standpoint, AFP allows engineers to apply classical laminate theory in new ways. By manipulating the orientation of fibers in each ply of a laminate, engineers can tailor the material's anisotropic properties to withstand specific stress profiles14. This enables the creation of highly optimized composite parts with enhanced performance.
AFP is being used in the EV industry to manufacture a variety of components, including:
Filament winding is another widely used automated process for manufacturing composite parts, particularly those with cylindrical or tubular shapes15. This technique involves winding continuous fiber rovings, impregnated with resin, onto a rotating mandrel. The fibers are laid down in precise geometric patterns to create a structural solid of revolution. Filament winding offers several advantages in EV manufacturing:
Filament winding is ideal for manufacturing cylindrical composite structures like pipes, compressed gas cylinders, or huge rolls. This process can be performed using either wet winding, where fibers are impregnated with resin during the winding process, or dry winding, where pre-impregnated fibers are used16.
In the EV industry, filament winding is used to manufacture components such as:
LFAM is an emerging technology that combines additive and subtractive manufacturing techniques to produce large-scale parts from thermoplastic materials19. This process involves the deposition of molten thermoplastic material layer by layer, followed by machining to achieve the final shape and surface finish. LFAM offers several benefits in EV manufacturing:
While LFAM is still a relatively new technology in the EV industry, it has the potential to be used for manufacturing components such as:
Large-format continuous fiber 3D printing is another emerging technology that is gaining traction in the EV industry. This process involves the integration of continuous fibers, such as carbon or glass, into a polymer matrix during the 3D printing process22. This technology offers several advantages:
In the EV industry, large-format continuous fiber 3D printing can be used to manufacture components such as:
Addcomposites is a leading provider of advanced composite manufacturing solutions, offering a range of systems and software that are transforming the EV industry. Their innovative technologies are helping EV manufacturers produce lighter, stronger, and more efficient vehicles. Addcomposites is committed to making composite manufacturing more accessible and efficient, enabling wider adoption of these materials in the EV industry.
Addcomposites offers a comprehensive ecosystem of solutions for composite manufacturing, including:
Addcomposites' AddPath software is a key component of their composite manufacturing ecosystem. This software provides advanced features for planning, simulating, and analyzing the composite manufacturing process. AddPath can read CAD surfaces, allowing for precise planning and execution of the manufacturing process25. It also allows for the input of various parameters and provides visual notifications to guide the user. With AddPath, users can simulate programmed AFP tape courses, predict and measure the effects of various factors on their process, and plan single or multiple tow paths in one course of motion25. AddPath also facilitates data analysis by allowing users to export tape course geometry to standard CAD formats and import captured data during the process for production data analysis25.
While composite materials and automation techniques offer significant advantages in EV manufacturing, there are also challenges that need to be addressed:
Despite these challenges, the future outlook for composite materials and automation techniques in the EV industry is promising. The increasing demand for lightweight, efficient, and high-performance EVs is driving innovation in composite materials and manufacturing processes. Automation technologies are becoming more sophisticated and cost-effective, making them more accessible to EV manufacturers. Addcomposites, with its innovative systems and software, is playing a crucial role in shaping the future of composite manufacturing in the EV industry. Their technologies are helping to overcome the challenges and unlock the full potential of composite materials, enabling the production of next-generation EVs that are lighter, stronger, and more sustainable.
Composite materials and automation technologies are revolutionizing the EV industry, enabling the production of vehicles that are lighter, more efficient, and safer. AFP, filament winding, LFAM, and large-format continuous fiber 3D printing are key automation technologies that are adding value to the manufacturing process. These technologies offer increased precision, complexity handling, material efficiency, and speed, enabling the creation of highly optimized composite parts. Addcomposites, with its innovative systems and software, is at the forefront of this transformation, providing EV manufacturers with the tools they need to produce next-generation vehicles. As the EV industry continues to grow, composite materials and automation technologies will play an increasingly important role in driving innovation and sustainability. Addcomposites is committed to pushing the boundaries of composite manufacturing, making these technologies more accessible and efficient, and enabling the creation of EVs that are better for the environment and offer superior performance.
Composite materials and automation techniques are revolutionizing the EV industry, enabling the production of vehicles that are lighter, more efficient, and safer. AFP, filament winding, LFAM, and large-format continuous fiber 3D printing are key automation technologies that are adding value to the manufacturing process. Addcomposites, with its innovative systems and software, is at the forefront of this transformation, providing EV manufacturers with the tools they need to produce next-generation vehicles. As the EV industry continues to grow, composite materials and automation technologies will play an increasingly important role in driving innovation and sustainability.
Automating the Future: The Role of Automated Fiber Placement in Structural Battery Manufacturing - Addcomposite, accessed on January 28, 2025, https://www.addcomposites.com/post/automating-the-future-the-role-of-automated-fiber-placement-in-structural-battery-manufacturing