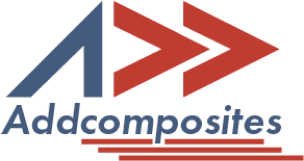
In the ever-evolving landscape of aerospace engineering, a quiet revolution has been taking place. Advanced composites, once a niche material reserved for specialized applications, have now become the backbone of modern aircraft design. These materials are not just incremental improvements over their predecessors; they represent a quantum leap in materials science, redefining what's possible in the skies.
Advanced composites have transformed the aviation industry, introducing a new era of performance, efficiency, and safety. From lightweight fuselages to high-strength wing structures, these materials are pushing the boundaries of aircraft design and capabilities. But what exactly are these wonder materials, and why have they become so crucial to the aerospace sector?
Advanced composites are engineered materials made from two or more constituents with significantly different physical or chemical properties. When combined, they create a material with characteristics different from the individual components. In the context of aerospace:
The adoption of advanced composites in civilian aircraft manufacturing has been nothing short of revolutionary. Here's why they've become indispensable:
As we delve deeper into the world of advanced composites, we'll explore the various materials, forms, and manufacturing processes that are shaping the future of aerospace. From the microscopic structure of carbon fibers to the macroscopic design of aircraft components, the story of composites is one of innovation, engineering prowess, and the relentless pursuit of excellence in aviation.
At the heart of every advanced composite material are the fibers that provide the fundamental properties required for aerospace applications. These fibers are the load-bearing components of the composite, offering strength and stiffness that often surpass traditional metals. Let's explore the various fiber types and their unique characteristics:
Aramid fibers, known for their distinctive golden-yellow color, are synthetic polymers with some remarkable properties:
Aramid fibers excel in applications where lightness, high tensile strength, and resistance to impact are crucial.
Boron fibers, while less common due to their cost, offer some unique advantages:
The high cost of boron fibers often limits their use to specialized applications where their unique properties justify the expense.
Carbon and graphite fibers are the workhorses of the aerospace composite world:
The adaptability of carbon fibers to various forms and manufacturing processes makes them indispensable in modern aerospace design.
Fiberglass, the most widely used fiber in composite materials, offers a balance of performance and economy:
Fiberglass is often the go-to choice for less critical structures where cost is a significant factor.
As aerospace technology advances, so too does the science of fiber materials. Researchers are continually pushing the boundaries, developing fibers with even greater strength, stiffness, and functionality. Some areas of ongoing research include:
The choice of fiber material is a critical decision in aerospace design, balancing performance requirements with cost considerations. As we'll see in the following sections, the way these fibers are arranged and combined with matrix materials is equally important in creating the advanced composites that are redefining modern aerospace.
The performance of a composite material isn't solely determined by the type of fiber used; the form and arrangement of these fibers play a crucial role in defining the material's properties. Let's explore the various forms fibers can take and how they function within composite structures.
At their most basic level, fibers are grouped into strands or tows:
These forms are versatile and can be used in various manufacturing processes, from hand lay-up to automated fiber placement (AFP).
Fibers can be woven into fabrics, which offer several advantages:
Fabrics are particularly useful in creating complex geometries often found in aerospace structures.
The orientation of fibers within a composite is critical to its performance:
Engineers carefully design the fiber orientation to align with expected load paths in the final structure. This is where processes like Automated Fiber Placement (AFP) excel, allowing precise control over fiber placement.
Preforms are engineered arrangements of fibers shaped to fit a specific mold:
Preforms are particularly useful in complex aerospace components where traditional layup methods might be challenging.
While less common in primary aerospace structures, chopped fibers have their place:
Chopped fibers can be useful in complex-shaped parts where continuous fibers might be difficult to use.
The form and function of fibers in composites are integral to the design process. By carefully selecting and arranging fibers, engineers can create materials tailored to the specific needs of aerospace applications, balancing strength, weight, and manufacturability. As we'll see in the next section, these fibers are often combined with matrix materials in the form of prepregs, further enhancing their utility in aerospace manufacturing.
Prepreg materials have revolutionized the manufacturing of advanced composites in aerospace. These pre-impregnated fibers offer a level of consistency and ease of use that has made them indispensable in the production of high-performance aircraft components.
Prepregs are fiber reinforcements that have been pre-impregnated with a resin system. The resin is only partially cured, leaving the material tacky and ready for layup. There are two main types of prepregs:
The use of prepregs offers several significant advantages in aerospace manufacturing:
Prepregs are widely used in critical aerospace structures due to their superior performance:
Prepregs are compatible with various manufacturing methods:
While prepregs offer many advantages, there are some challenges to consider:
The future of prepreg materials in aerospace looks promising:
Prepreg materials have become a cornerstone of advanced composite manufacturing in aerospace. Their ability to deliver consistent, high-performance parts has made them invaluable in the production of modern aircraft. As technology continues to advance, prepregs are likely to play an even more significant role in shaping the future of aerospace composites.
The way fibers are woven into fabrics plays a crucial role in determining the properties and performance of composite materials. In aerospace applications, where every aspect of material behavior is critical, understanding fabric weaves is essential for optimal design and manufacturing.
The plain weave is the most fundamental and commonly used pattern:
Twill weaves create a distinctive diagonal pattern:
Satin weaves have fewer intersections between warp and weft fibers:
The choice of weave pattern significantly impacts the final composite's properties:
Beyond these basic patterns, advanced weaves are being developed for specialized applications:
When selecting fabric weaves for aerospace composites, designers must consider:
The choice of fabric weave is a critical decision in the design of aerospace composites. It affects not only the final performance of the part but also its manufacturability and cost. As automated manufacturing processes like AFP become more prevalent, the ability to tailor fiber orientations and weave patterns offers even greater potential for optimizing composite structures in aerospace applications.
While fibers provide the primary strength and stiffness in composite materials, the matrix plays a crucial role in binding these fibers together and distributing loads between them. In aerospace applications, the choice of matrix material can significantly impact the performance, durability, and manufacturability of composite parts.
The matrix in a composite material serves several vital functions:
Thermoset resins undergo a chemical reaction during curing, forming a cross-linked structure that cannot be remolded or reshaped.
Thermoplastic resins can be remelted and reshaped after initial forming, offering potential advantages in manufacturing and recycling.
The choice between thermoset and thermoplastic matrices involves several trade-offs:
The aerospace industry is continuously pushing the boundaries of matrix material technology:
When selecting matrix materials for aerospace composites, designers must consider:
The choice of matrix material is a critical decision in the design of aerospace composites. It affects not only the final performance of the part but also its manufacturability, cost, and lifecycle characteristics. As the industry continues to push for lighter, stronger, and more sustainable materials, innovations in matrix technology will play a key role in shaping the future of aerospace composites.
As aerospace technology continues to evolve, so do the materials and manufacturing processes used to create advanced composites. This section explores some of the cutting-edge developments that are shaping the future of aerospace materials.
Traditional laminated composites have limitations, particularly in terms of through-thickness strength. Advanced 3D textile processes are addressing these challenges:
Incorporating nanomaterials into composites is opening up new possibilities:
Future composites aren't just structural; they're being designed to serve multiple functions:
While not entirely new, thermoplastic composites are gaining traction in aerospace:
Nature-inspired designs are influencing the next generation of composites:
New manufacturing methods are enabling more complex and efficient composite structures:
The future of aerospace composites is bright, with several trends emerging:
As these advanced forms and future materials continue to develop, they promise to revolutionize aerospace design, enabling lighter, stronger, and more efficient aircraft. However, challenges remain in scaling up production, ensuring consistency, and meeting stringent aerospace regulations. The successful integration of these innovations will require close collaboration between material scientists, aerospace engineers, and regulatory bodies.
Designing with composite materials in aerospace applications requires a unique approach that differs significantly from traditional metallic designs. The anisotropic nature of composites, combined with their complex failure modes and manufacturing considerations, presents both challenges and opportunities for aerospace engineers.
Choosing the right combination of fibers, matrix, and fabric forms is crucial:
Material databases are essential tools for making informed decisions during the selection process.
The arrangement of composite plies significantly impacts the part's performance:
Automated Fiber Placement (AFP) technologies allow for precise control over ply placement and orientation.
Connecting composite parts requires special consideration:
Composites behave differently from metals when damaged:
The manufacturing process can significantly influence design decisions:
One of the primary advantages of composites is their potential for weight savings:
Explore opportunities to integrate additional functionalities into composite structures:
Ensuring compliance with aerospace regulations is critical:
While composites offer performance benefits, cost is always a factor:
Increasing focus on environmental impact influences design decisions:
Utilize specialized software for composite design and analysis:
By carefully considering these factors, aerospace engineers can fully leverage the advantages of composite materials to create lighter, stronger, and more efficient aircraft structures. The successful implementation of composites in aerospace design requires a holistic approach that balances performance, manufacturability, cost, and regulatory compliance.
As we've explored throughout this blog post, advanced composites have truly transformed the landscape of materials used in civilian aircraft. From the microscopic structure of carbon fibers to the macroscopic design of aircraft components, composites are redefining what's possible in aerospace engineering.
The future of composites in aerospace is bright and full of potential. As we continue to innovate in materials science and manufacturing technology, we can expect to see:
The journey of composites in aerospace is far from over. In fact, it's clear that we're just scratching the surface of what's possible with these remarkable materials.
Are you inspired by the potential of advanced composites in aerospace? Here's how you can get involved and stay at the forefront of this exciting field:
At Addcomposites, we are dedicated to revolutionizing composite manufacturing. Our AFP systems and comprehensive support services are waiting for you to harness. So, don't wait – get started on your journey to the future of manufacturing today!