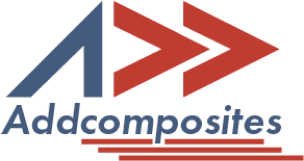
At Addcomposites, we’re excited to share how our latest innovation, the AFP-X system, is transforming high-volume composite manufacturing while maintaining precision for even the most complex geometries. Building on the success of our widely adopted AFP-XS platform, we’ve created a solution that delivers industrial-grade performance without the traditional barriers to entry.
The AFP-X represents our commitment to democratizing advanced composite manufacturing technology. As the first high-production-grade Automated Fiber Placement (AFP) tool designed specifically to bring high-volume capabilities to the masses, it packs four times the production power of our standard systems while maintaining the accessibility that has made our solutions so popular[9].
Our modular 4-tow system is changing how industries approach high-performance composite part production, offering unparalleled versatility and precision for manufacturers across aerospace, automotive, marine, and other sectors requiring high-performance composites[1].
The AFP-X Multi-Tow system delivers industrial-grade performance specifications:
The production advantages of AFP technology are well-documented, and our AFP-X system builds on these fundamentals while making them accessible to more manufacturers:
These metrics demonstrate why AFP technology has become essential in industries where both production volume and precision are critical requirements.
The AFP-X system particularly shines when tackling geometries that traditional manufacturing approaches struggle with:
Our customers are successfully using the AFP-X for manufacturing:
The AFP-X system provides exceptional fiber steering capabilities – crucial for optimizing structural performance in complex parts. While wider tow systems are limited in their steering radius, our technology enables production-ready components with superior fiber orientation control[11].
One of the most powerful features of the AFP-X is its advanced digital twin technology integration. Working with our AddPath software, this capability enables:
Using AddPath, design engineers can turn a CAD model into a fully planned and automated layup in just a few steps. The software allows for controlling parameters like fiber orientation and allowed gaps, with the ability to add reinforced areas or suppress specific tool paths as needed[4].
We designed the AFP-X as a plug-and-play solution that integrates easily with your existing robotic arms from major manufacturers including Kuka, ABB, Fanuc, Kawasaki, and Yaskawa[1]. This approach dramatically reduces implementation time and costs compared to traditional AFP systems that require complete infrastructure overhauls.
The system’s comprehensive integration capabilities include:
Our customers are already experiencing the benefits of the AFP-X system across multiple industries:
The video demonstrations on our website showcase the AFP-X in action, highlighting:
For early adopters looking to gain a competitive edge in composite manufacturing, the AFP-X represents an opportunity to access production-grade AFP capabilities without the traditional barriers to entry. We’ve designed this system specifically to democratize advanced composite manufacturing, making high-volume, high-precision production accessible to a broader range of manufacturers.
Whether you’re considering AFP technology for the first time or looking to scale up your existing composite manufacturing capabilities, we invite you to:
Contact our team at sales@addcomposites.com to learn more about how the AFP-X can revolutionize your composite manufacturing process, or to request your free AddPath license to begin exploring the possibilities from your own workstation[1].
Visit www.addcomposites.com for detailed specifications, case studies, and video demonstrations of the AFP-X in action.
The AFP-X represents our continued commitment to making advanced composite manufacturing technology accessible to more manufacturers. By combining multi-tow production capabilities with user-friendly design and seamless integration, we’re enabling a new generation of composite manufacturers to achieve unprecedented levels of efficiency, precision, and innovation.
As the composites industry continues to evolve, the AFP-X system provides a scalable solution that grows with your production needs while maintaining the precision and quality that your most demanding applications require.