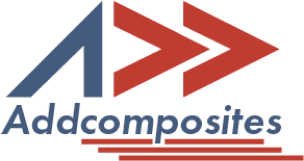
As manufacturing methods develop, industries are finding ways to create eco-friendly composite materials with sustainable attributes. Manufacturers are aiming to utilize more sustainable material from natural sources and sustainable lifecycle and disposal. The goal is to reduce the impact on the environment and reduce the overall carbon footprint. In this article, we are aiming to understand the natural fiber and manufacturing choices we have in the world of composites…
Natural fibers are produced by plants, animals, and geological processes. They can be used as a component of composite materials, where the orientation of fibers impacts the properties. In the table below a few successful natural fiber evolutions are covered and compared to E-glass fiber in the property.
While designing composite parts, the choice of reinforcement is one of the first important decisions that need to be made. When choosing the right reinforcement for your application, you shouldn't ignore natural fiber as a viable option until they are ruled out based upon your requirements, as they bring sustainability to the overall production. However, there are a few key properties that you should take into consideration before making the decision. In the table below, some advantages and comparative disadvantages of natural fibers are highlighted.
The use of natural fibers for technical composite applications has recently been the subject of intensive research in Europe. Many automotive components are already produced using natural composites, primarily based on flax, hemp, or sisal fibers using either polyester or polypropylene as a matrix. The adoption of natural fiber composites in this industry is lead by motives of:
When natural fibers are selected for the end product, their technical aspects have a rather low priority. The range of products is restricted to the interior and non-structural components, such as door upholstery, dashboard accents, or body panels such as the trunk lid or the hood.
The production of natural fibers can be carried out by traditional know-how in developing countries, such as in Southeast Asia, where local natural fibers grow quickly and at low cost. The importing of non-domestic materials - like carbon or glass fibers - is expensive, not environmentally sustainable, and just plain difficult. In order to be even more sustainable by producing the lowest amount of waste, SMEs should have easy access to automation to deposit the material in order to create high-quality composite parts.
Presently, most thermoset-based composite material processing can use only a select amount of processes, mentioned below.
Additionally, there is no cost-effective method of automation that can process natural fiber thermoplastic composites.
Automated Fiber Placement (AFP) is regarded as one of the most accurate and repeatable composites manufacturing processes available today. A recent study show how the Flex-PP tapes can be used to make the desired structures using AFP
This study required the preparation of tape with a calibrated width from impregnated fiber sheets. The unidirectional tapes showed polymer-rich zones on the surface. During manufacture, the polypropylene (PP) is melted locally with a laser. A consolidation step in a hot press is then required to reduce void content. The study concluded that AFP appears to be a technically apt automated process for biocomposites. (source)
Traditionally AFP systems have been really expensive. However, Addcomposites' new offering, the AFP-XS, is available on a monthly subscription basis converting your existing robots into the most cost-effective sustainable production system.
Contact the Addcomposites team for more information on how we can help you join sustainable manufacturing economically!
As manufacturing methods develop, industries are finding ways to create eco-friendly composite materials with sustainable attributes. Manufacturers are aiming to utilize more sustainable material from natural sources and sustainable lifecycle and disposal. The goal is to reduce the impact on the environment and reduce the overall carbon footprint. In this article, we are aiming to understand the natural fiber and manufacturing choices we have in the world of composites…
Natural fibers are produced by plants, animals, and geological processes. They can be used as a component of composite materials, where the orientation of fibers impacts the properties. In the table below a few successful natural fiber evolutions are covered and compared to E-glass fiber in the property.
While designing composite parts, the choice of reinforcement is one of the first important decisions that need to be made. When choosing the right reinforcement for your application, you shouldn't ignore natural fiber as a viable option until they are ruled out based upon your requirements, as they bring sustainability to the overall production. However, there are a few key properties that you should take into consideration before making the decision. In the table below, some advantages and comparative disadvantages of natural fibers are highlighted.
The use of natural fibers for technical composite applications has recently been the subject of intensive research in Europe. Many automotive components are already produced using natural composites, primarily based on flax, hemp, or sisal fibers using either polyester or polypropylene as a matrix. The adoption of natural fiber composites in this industry is lead by motives of:
When natural fibers are selected for the end product, their technical aspects have a rather low priority. The range of products is restricted to the interior and non-structural components, such as door upholstery, dashboard accents, or body panels such as the trunk lid or the hood.
The production of natural fibers can be carried out by traditional know-how in developing countries, such as in Southeast Asia, where local natural fibers grow quickly and at low cost. The importing of non-domestic materials - like carbon or glass fibers - is expensive, not environmentally sustainable, and just plain difficult. In order to be even more sustainable by producing the lowest amount of waste, SMEs should have easy access to automation to deposit the material in order to create high-quality composite parts.
Presently, most thermoset-based composite material processing can use only a select amount of processes, mentioned below.
Additionally, there is no cost-effective method of automation that can process natural fiber thermoplastic composites.
Automated Fiber Placement (AFP) is regarded as one of the most accurate and repeatable composites manufacturing processes available today. A recent study show how the Flex-PP tapes can be used to make the desired structures using AFP
This study required the preparation of tape with a calibrated width from impregnated fiber sheets. The unidirectional tapes showed polymer-rich zones on the surface. During manufacture, the polypropylene (PP) is melted locally with a laser. A consolidation step in a hot press is then required to reduce void content. The study concluded that AFP appears to be a technically apt automated process for biocomposites. (source)
Traditionally AFP systems have been really expensive. However, Addcomposites' new offering, the AFP-XS, is available on a monthly subscription basis converting your existing robots into the most cost-effective sustainable production system.
Contact the Addcomposites team for more information on how we can help you join sustainable manufacturing economically!