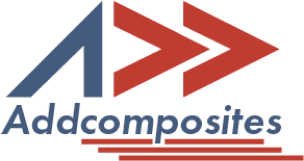
Automated Fiber Placement (AFP) technology has evolved significantly in recent years, with one of the most promising developments being the ability to process dry fibers. This advancement opens new possibilities for composite manufacturing across various industries, particularly aerospace.
Dry fiber placement refers to the automated deposition of non-resin-impregnated carbon fibers that are pre-coated with a binder to maintain fiber cohesion during the placement process. Unlike traditional pre-impregnated (prepreg) materials, dry fibers require subsequent infusion with resin after the layup is complete46.
The process utilizes specialized AFP equipment that places multiple narrow tows of dry fiber material directly onto mold surfaces using computer-guided systems. These systems typically incorporate:
Dry fiber placement offers several significant advantages over traditional prepreg AFP:
When transitioning from prepreg to dry fiber processing, several key equipment modifications are necessary:
Successful dry fiber AFP implementation requires careful attention to environmental conditions:
Temperature Management:
Humidity Control:
Clean Room Practices:
For optimal dry fiber placement results:
Dry fiber AFP technology has found particular success in aerospace applications, including:
The technology is also expanding into other industries where large-scale, high-performance composite structures are required.
Dry fiber placement represents a significant advancement in AFP technology, offering cost savings, improved processing rates, and enhanced design possibilities. While implementing dry fiber AFP systems requires careful consideration of equipment modifications and process parameters, the benefits make it an increasingly attractive option for modern composite manufacturing.
As the technology continues to mature, we can expect to see wider adoption across aerospace and other industries seeking to leverage the advantages of composite materials while reducing production costs and improving manufacturing efficiency.