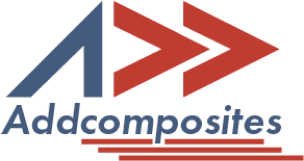
The urban air mobility sector stands at a critical juncture. While multiple eVTOL designs have achieved successful test flights, the path to commercial viability remains challenging. Current technological limitations create a complex web of interdependent constraints that significantly impact operational capabilities and economic feasibility. Understanding these limitations is crucial for appreciating why revolutionary approaches, rather than incremental improvements, are necessary.
Current limitations of conventional eVTOL designs face several challenges that demand innovative solutions. For more background on these challenges, see "Automating the Future: The Role of Automated Fiber Placement in Structural Battery Manufacturing".
Analysis of current eVTOL designs, exemplified by the CityAirbus, reveals a fundamental challenge: conventional battery systems consume approximately 22% of the maximum takeoff weight (MTOW). In the CityAirbus's case, this translates to 550kg of batteries in a 2,450kg aircraft, leaving only 250kg for payload - a mere 10% of MTOW. This ratio creates several cascading effects:
Current eVTOL manufacturing faces multiple technical challenges:
For detailed analysis of these challenges, see "Manufacturing the Future: Next-Gen Aerospace Components with Automated Fiber Placement".
The global urban population is projected to reach 6.7 billion by 2050. To understand how these market demands are shaping manufacturing approaches, read "Navigating the Automation Revolution in Aerospace Composite Manufacturing".This growth creates several imperatives:
Environmental considerations are becoming increasingly critical:
Traditional approaches to these challenges - focusing on incremental improvements in battery technology or manufacturing processes - are insufficient. The interdependence of these limitations requires a fundamentally different approach:
The convergence of structural battery technology with advanced manufacturing processes represents more than an incremental improvement - it offers a pathway to overcome the fundamental limitations currently constraining the eVTOL industry. This approach not only addresses current technical challenges but also aligns with market demands for sustainable, economically viable urban air mobility solutions.
Structural batteries represent a paradigm shift in how we approach energy storage in aerospace applications. Unlike traditional battery integration, where cells are merely embedded within structures, structural battery composites (SPCs) achieve true multifunctionality at the material level, enabling simultaneous energy storage and load-bearing capabilities. For an in-depth understanding of structural battery integration in aerospace applications, see "Automating the Future: The Role of Automated Fiber Placement in Structural Battery Manufacturing".
The latest developments in structural battery composites build upon advanced manufacturing techniques. For more details on manufacturing considerations, refer to "Understanding Tension and Compaction in AFP: Beyond Traditional Debulking".Modern structural batteries utilize a laminated architecture consisting of:
The latest research demonstrates two primary approaches:
Analysis of eVTOL requirements, using the CityAirbus as a reference platform, indicates the following minimum performance targets:
Recent developments in structural electrolytes focus on creating bi-continuous networks:
For insights into overcoming integration challenges, see "Process Monitoring AI for AFP Composites Manufacturing" and "Data-driven Optimisation for Zero Defect Composites Manufacturing".
The path to achieving required performance metrics involves:
The structural battery revolution represents a critical enabling technology for next-generation eVTOL aircraft. While current performance metrics fall short of ultimate requirements, the rapid pace of development and clear pathway to improvement suggest that structural batteries will play a crucial role in future aircraft design and manufacturing.
The integration of structural batteries into eVTOL production requires manufacturing capabilities that combine precision, flexibility, and scalability. Recent advances in automated composite manufacturing, particularly through modular and adaptable systems, are creating new possibilities for cost-effective production of these complex multifunctional components.
For comprehensive coverage of modern AFP technologies, see "The Evolution of Automated Fiber Placement: Early Developments to Modern Applications".
Traditional Automated Fiber Placement (AFP) systems, while powerful, have historically presented barriers to adoption:
The emergence of modular systems like AFP-XS represents a paradigm shift in accessibility and capability:
Learn more about various manufacturing processes in "Future of Composites Manufacturing: Addcomposites' Plug&Play AFP, Filament Winding & SCF3D Printing".
Modern automated systems enable multiple manufacturing processes with a single platform:
For detailed information about quality control processes, refer to "Manual Inspection to Profilometer based Automated Process Control for AFP".
For insights into manufacturing strategies, see "Step-by-Step Guide for Optimizing Automated Thermoplastic Fiber Placement".
The advanced manufacturing revolution, enabled by flexible automated systems, provides the foundation for practical implementation of structural batteries in eVTOL production. By combining precision automation with adaptable manufacturing strategies, manufacturers can achieve the quality, consistency, and scale required for successful commercialization.
The successful integration of structural batteries into eVTOL manufacturing requires a carefully orchestrated approach that leverages advanced manufacturing capabilities while addressing the unique challenges of multifunctional aerospace components. This section examines the specific strategies and methods for implementing this integration effectively.
Learn more about parameter optimization in "Optimizing AFP Manufacturing Through Strategic Data Use".
The synergistic integration of structural batteries and advanced manufacturing processes provides a clear pathway to improved eVTOL performance and commercial viability. Success requires careful attention to process optimization, quality control, and scaling strategies, but the potential benefits justify the development effort required.
The successful integration of structural batteries with advanced manufacturing in eVTOLs represents more than just a technological advancement - it opens a pathway to transforming the broader aerospace industry. This section explores how mastery of these technologies in eVTOL applications can lead to revolutionary changes in larger aircraft development and aerospace manufacturing.
For perspectives on scaling manufacturing capabilities, see "Advancements in Thermoplastic AFP for Large Aerospace Structures".
Understand market transformation through "The Shift in Composite Manufacturing: From Traditional to Intelligent".
The successful implementation of structural batteries and advanced manufacturing in eVTOLs creates a foundation for broader aerospace industry transformation. Companies that master these technologies and successfully scale them to larger aircraft applications have the potential to emerge as future industry leaders, potentially rivaling established aerospace manufacturers.
The successful integration of structural batteries and advanced manufacturing requires a systematic approach to implementation. This roadmap provides a framework for organizations to develop capabilities while managing technical and commercial risks.
For detailed technical requirements, refer to "Mastering Automated Fiber Placement: A Comprehensive Guide for Manufacturers".
Learn about implementation strategies in "Choosing the Right Automated Fiber Placement System for Your Needs".
The implementation roadmap provides a structured approach to developing structural battery manufacturing capabilities. Success requires careful attention to technical requirements, personnel development, and risk management while maintaining focus on commercial objectives.
The convergence of structural battery technology and advanced manufacturing processes stands poised to revolutionize not just the eVTOL sector, but the entire aerospace industry. This final section examines the likely evolution of these technologies and their implications for the future of aviation.
For insights into future developments, see "Innovations in Automated Fiber Deposition for Aerospace Applications 2023".
Understand industry transformation through "Revolutionizing the Future of Composite Manufacturing: Automation Techniques and Innovation".
The future of aerospace manufacturing lies at the intersection of structural battery technology and advanced automated manufacturing. Organizations that successfully navigate this transformation will not only revolutionize the eVTOL sector but potentially reshape the entire aerospace industry. The pathway to success requires careful attention to both technical excellence and market development, while maintaining focus on sustainable and socially beneficial outcomes.
As we stand at the threshold of this transformation, the opportunity exists for new players to establish themselves as industry leaders through the masterful integration of these technologies. The next decade will likely see the emergence of new aerospace giants, built on the foundation of structural battery integration and advanced manufacturing capabilities.
This article draws significantly from several groundbreaking research papers and industry analyses:
At Addcomposites, we're leading the revolution in automated composite manufacturing with our innovative AFP-XS technology. Our solution enables manufacturers to transform standard industrial robots into sophisticated automated fiber placement systems, making advanced composite manufacturing accessible and affordable.
Contact our team to discuss how AFP-XS can help you develop and scale your structural battery composite manufacturing capabilities:
Join the manufacturers who are already using AFP-XS to revolutionize composite manufacturing and lead the future of urban air mobility.