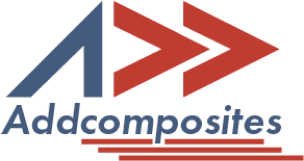
Prosthetic foot manufacturing, while rich with technological advancements, encounters a spectrum of challenges that significantly impact both the production and the end-user experience. Traditional manufacturing techniques, particularly lamination, have been the cornerstone of prosthetic foot production, offering high structural efficiency through the use of carbon fiber-reinforced composites. However, this method is fraught with limitations that necessitate a reevaluation of manufacturing paradigms.
These challenges highlight a critical need for alternative manufacturing approaches that can offer greater efficiency, flexibility, and sustainability. As the prosthetics industry evolves, there is a growing emphasis on exploring innovative solutions, such as Additive Manufacturing (AM), to address these limitations. By adopting new technologies, the industry can move towards producing more accessible, customizable, and environmentally friendly prosthetic solutions, thereby enhancing the quality of life for users around the globe.
The advent of laminated prosthetic feet has undeniably marked a significant milestone in the domain of prosthetics, offering amputees a blend of functionality and durability. Yet, beneath the surface of these achievements lie several pain points that affect both the manufacturers and the end-users, necessitating a critical evaluation of the lamination process and its outcomes.
These pain points underscore the urgent need for a paradigm shift in prosthetic foot manufacturing. Innovations in manufacturing technology, particularly the adoption of Additive Manufacturing (AM) and Continuous Fiber-Reinforced Additively Manufactured (CFRAM) techniques, hold promise for addressing these challenges. By leveraging the capabilities of AM, manufacturers can achieve greater customizability, reduce production costs, accelerate the innovation cycle, and mitigate the environmental impact, ultimately enhancing the overall value proposition of prosthetic feet for users worldwide.
The exploration of advanced manufacturing techniques, particularly Additive Manufacturing (AM), heralds a new era in the production of prosthetic feet. This innovative approach promises to mitigate many of the pain points associated with traditional lamination methods, offering a beacon of hope for both manufacturers and users. By embracing 3D printing and Continuous Fiber-Reinforced Additively Manufactured (CFRAM) technologies, the prosthetics industry is poised to overcome significant challenges, paving the way for prostheses that are more accessible, customizable, and efficient.
Despite these promising advancements, the adoption of 3D printing in prosthetic foot manufacturing is not without its challenges. Technical limitations, such as the need for more robust materials or the optimization of print parameters for mechanical properties, require ongoing research and development. Additionally, regulatory and standardization considerations must be addressed to ensure that 3D-printed prostheses meet all safety and efficacy requirements.
The culmination of efforts to address the significant challenges in traditional prosthetic foot manufacturing has led to the development of an innovative, stiffness-driven design and optimization framework. This breakthrough leverages the power of beam finite element (FE) modeling, offering a sophisticated tool for creating prosthetic feet that align more closely with the dynamic and static needs of users. By integrating this framework with Additive Manufacturing (AM) and Continuous Fiber-Reinforced Additively Manufactured (CFRAM) technologies, a new pathway opens up for producing prosthetic feet that are not only more functional but also customizable and efficient.
The beam finite element-based framework represents a significant advancement in the field of prosthetic foot design and manufacturing. Its development not only addresses the critical challenges of customization, cost, and performance but also sets a new standard for the integration of computational modeling and additive manufacturing techniques. As this framework continues to evolve, it holds the promise of revolutionizing prosthetic foot technology, making high-quality, personalized prosthetic solutions a reality for individuals around the world.
We extend our heartfelt gratitude to Abdel Rahman N. Al Thahabi, Luca M. Martulli, Andrea Sorrentino, Marino Lavorgna, Emanuele Gruppioni, and Andrea Bernasconi for their groundbreaking contributions detailed in "Stiffness-driven design and optimization of a 3D-printed composite prosthetic foot: A beam finite Element-Based framework." Their collaborative research has significantly advanced the field of prosthetic technology, setting a new benchmark in the design and optimization of prosthetic feet. Through the integration of advanced 3D printing technologies and beam finite element modeling, they have opened new avenues for enhancing customization, accessibility, and the overall quality of life for individuals with limb loss. Their dedication and pioneering efforts are greatly appreciated, marking a significant milestone in the future of prosthetic design and manufacturing.
Discover the future of composite manufacturing with Addcomposites! Here's how you can get involved:
At Addcomposites, we are dedicated to revolutionizing composite manufacturing. Our AFP systems and comprehensive support services are waiting for you to harness. So, don't wait – get started on your journey to the future of manufacturing today!
Prosthetic foot manufacturing, while rich with technological advancements, encounters a spectrum of challenges that significantly impact both the production and the end-user experience. Traditional manufacturing techniques, particularly lamination, have been the cornerstone of prosthetic foot production, offering high structural efficiency through the use of carbon fiber-reinforced composites. However, this method is fraught with limitations that necessitate a reevaluation of manufacturing paradigms.
These challenges highlight a critical need for alternative manufacturing approaches that can offer greater efficiency, flexibility, and sustainability. As the prosthetics industry evolves, there is a growing emphasis on exploring innovative solutions, such as Additive Manufacturing (AM), to address these limitations. By adopting new technologies, the industry can move towards producing more accessible, customizable, and environmentally friendly prosthetic solutions, thereby enhancing the quality of life for users around the globe.
The advent of laminated prosthetic feet has undeniably marked a significant milestone in the domain of prosthetics, offering amputees a blend of functionality and durability. Yet, beneath the surface of these achievements lie several pain points that affect both the manufacturers and the end-users, necessitating a critical evaluation of the lamination process and its outcomes.
These pain points underscore the urgent need for a paradigm shift in prosthetic foot manufacturing. Innovations in manufacturing technology, particularly the adoption of Additive Manufacturing (AM) and Continuous Fiber-Reinforced Additively Manufactured (CFRAM) techniques, hold promise for addressing these challenges. By leveraging the capabilities of AM, manufacturers can achieve greater customizability, reduce production costs, accelerate the innovation cycle, and mitigate the environmental impact, ultimately enhancing the overall value proposition of prosthetic feet for users worldwide.
The exploration of advanced manufacturing techniques, particularly Additive Manufacturing (AM), heralds a new era in the production of prosthetic feet. This innovative approach promises to mitigate many of the pain points associated with traditional lamination methods, offering a beacon of hope for both manufacturers and users. By embracing 3D printing and Continuous Fiber-Reinforced Additively Manufactured (CFRAM) technologies, the prosthetics industry is poised to overcome significant challenges, paving the way for prostheses that are more accessible, customizable, and efficient.
Despite these promising advancements, the adoption of 3D printing in prosthetic foot manufacturing is not without its challenges. Technical limitations, such as the need for more robust materials or the optimization of print parameters for mechanical properties, require ongoing research and development. Additionally, regulatory and standardization considerations must be addressed to ensure that 3D-printed prostheses meet all safety and efficacy requirements.
The culmination of efforts to address the significant challenges in traditional prosthetic foot manufacturing has led to the development of an innovative, stiffness-driven design and optimization framework. This breakthrough leverages the power of beam finite element (FE) modeling, offering a sophisticated tool for creating prosthetic feet that align more closely with the dynamic and static needs of users. By integrating this framework with Additive Manufacturing (AM) and Continuous Fiber-Reinforced Additively Manufactured (CFRAM) technologies, a new pathway opens up for producing prosthetic feet that are not only more functional but also customizable and efficient.
The beam finite element-based framework represents a significant advancement in the field of prosthetic foot design and manufacturing. Its development not only addresses the critical challenges of customization, cost, and performance but also sets a new standard for the integration of computational modeling and additive manufacturing techniques. As this framework continues to evolve, it holds the promise of revolutionizing prosthetic foot technology, making high-quality, personalized prosthetic solutions a reality for individuals around the world.
We extend our heartfelt gratitude to Abdel Rahman N. Al Thahabi, Luca M. Martulli, Andrea Sorrentino, Marino Lavorgna, Emanuele Gruppioni, and Andrea Bernasconi for their groundbreaking contributions detailed in "Stiffness-driven design and optimization of a 3D-printed composite prosthetic foot: A beam finite Element-Based framework." Their collaborative research has significantly advanced the field of prosthetic technology, setting a new benchmark in the design and optimization of prosthetic feet. Through the integration of advanced 3D printing technologies and beam finite element modeling, they have opened new avenues for enhancing customization, accessibility, and the overall quality of life for individuals with limb loss. Their dedication and pioneering efforts are greatly appreciated, marking a significant milestone in the future of prosthetic design and manufacturing.
Discover the future of composite manufacturing with Addcomposites! Here's how you can get involved:
At Addcomposites, we are dedicated to revolutionizing composite manufacturing. Our AFP systems and comprehensive support services are waiting for you to harness. So, don't wait – get started on your journey to the future of manufacturing today!