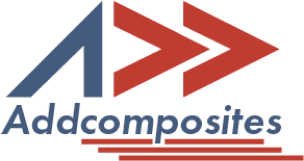
In today's aerospace and advanced manufacturing sectors, the pursuit of sustainability has become as crucial as the quest for performance. One of the most pressing challenges facing the composite manufacturing industry is the significant volume of material waste, particularly in the form of out-of-spec and expired prepregs. These materials, though technically sophisticated and expensive, often find their way to landfills due to stringent aerospace regulations and certification requirements.
The composite manufacturing industry faces a unique paradox. While advanced composite materials continue to revolutionize everything from aircraft components to sporting goods, a substantial portion of these valuable materials never makes it into final products. This waste stems from various sources:
Recent research indicates that these materials, particularly out-of-spec carbon fiber prepregs, retain significant mechanical properties that could make them valuable in non-aerospace applications. For instance, studies show that expired prepregs can maintain up to 85-87% of their original mechanical properties, making them more than suitable for many high-performance applications outside the aerospace sector.
The environmental impact of composite waste extends beyond the obvious issue of landfill space. The manufacturing and recycling of carbon fiber thermoplastic composites represents a significant energy investment, and disposing of these materials negates this investment entirely. As industries worldwide pivot towards more sustainable practices, finding ways to upcycle these materials has become not just an environmental imperative but a business opportunity.
Rather than viewing out-of-spec prepregs as waste, forward-thinking manufacturers are beginning to see them as valuable resources for sustainable manufacturing. This shift in perspective opens up new possibilities for:
The key lies in understanding that while these materials may not meet the exacting standards of aerospace applications, they still possess impressive mechanical properties that make them suitable for numerous other high-performance applications.
Advances in automated fiber placement technology and processing techniques have made it increasingly feasible to effectively utilize these materials. Modern AFP systems can handle various material states and conditions, enabling manufacturers to process out-of-spec prepregs with precision and reliability. This technological capability, combined with proper material characterization and process control, creates a viable pathway for upcycling these valuable materials.
The financial implications of upcycling out-of-spec prepregs are compelling. With carbon fiber prepreg costs ranging from $50 to $200 per kilogram, finding ways to utilize these materials in alternative applications represents a significant cost-saving opportunity. Additionally, as companies face increasing pressure to reduce waste and improve sustainability metrics, the ability to upcycle these materials can contribute positively to environmental, social, and governance (ESG) goals.
In the following sections, we'll delve deeper into the technical aspects of working with out-of-spec prepregs, explore real-world applications, and examine how modern automated manufacturing solutions can help organizations implement effective upcycling programs.
The term "out-of-spec" in composite manufacturing often carries an immediate negative connotation, leading to automatic disposal of materials that might still hold significant value. However, recent research, including a comprehensive study from Khalifa University, reveals that understanding these materials' true capabilities could unlock substantial opportunities for sustainable composites development.
Out-of-spec prepregs typically fall into this category due to several factors, with time-based expiration being the most common. However, the actual degradation of these materials is far more nuanced than a simple date stamp might suggest. When we examine composite materials basics, we find that prepreg quality depends on multiple factors:
Recent studies indicate that prepregs stored under proper refrigerated conditions can maintain up to 95.4% cure rates even after exceeding their labeled expiration date. This finding challenges the binary "good-or-bad" approach traditionally applied to these materials.
Understanding the aging process of prepregs requires examining both the resin system and fiber components. Advanced material selection research shows that the primary changes occur in the resin system, while the carbon fibers remain largely unaffected. Key characteristics that evolve over time include:
Recent research demonstrates that out-of-spec materials can retain impressive mechanical properties:
Traditional industry practices often default to disposal of out-of-spec materials, particularly in aerospace applications where certification and quality control requirements are stringent. However, this approach overlooks significant opportunities in other sectors where slightly reduced mechanical properties are perfectly acceptable.
Out-of-spec prepregs can find new life in various applications where the certification requirements are less stringent but performance demands are still high:
Successfully working with out-of-spec prepregs requires understanding and adapting to their modified characteristics. Modern AFP systems can be particularly effective in handling these materials through:
Research shows that with proper processing parameters, laminates manufactured from out-of-spec prepregs can achieve void contents as low as 2.4%, which is well within acceptable limits for many applications.
Before implementing out-of-spec materials in new applications, proper characterization is essential. This includes:
Modern manufacturing facilities equipped with advanced process monitoring capabilities can effectively track and control these parameters, ensuring consistent results even with out-of-spec materials.
Recent groundbreaking research into out-of-spec carbon fiber prepregs has revealed surprising insights that challenge traditional assumptions about expired materials. A comprehensive study conducted at Khalifa University provides compelling evidence that these materials retain significant value for advanced composites manufacturing.
The research findings present a nuanced picture of how out-of-spec prepregs perform compared to their pristine counterparts. When examining composite manufacturing fundamentals, several key performance indicators stand out:
The study revealed remarkably well-preserved mechanical characteristics:
These findings align with modern understanding of defects and damage in composite materials, suggesting that proper processing can minimize the impact of aging.
One of the most significant discoveries relates to the material's cure behavior. The research demonstrates that out-of-spec prepregs can achieve:
These results indicate that optimizing manufacturing processes for out-of-spec materials can yield high-quality parts suitable for many applications.
The research paid particular attention to structural quality indicators:
Microscopic examination revealed:
These findings align with modern composite quality control standards and suggest that proper processing can achieve reliable results.
The study identified optimal processing conditions for out-of-spec materials:
These parameters demonstrate the importance of understanding composite cure cycles and their impact on final properties.
These research findings have significant implications for manufacturers considering the use of out-of-spec materials:
The research points to several opportunities for implementing these findings in modern manufacturing environments:
Modern manufacturing technology plays a crucial role in successfully utilizing out-of-spec materials:
While aerospace applications may be off-limits for out-of-spec prepregs, these materials open up a world of opportunities across various industries. The demonstrated retention of 85-87% of original mechanical properties makes them ideal candidates for numerous high-performance applications where cost-effectiveness is as crucial as performance.
The sporting goods industry has emerged as a particularly promising arena for upcycled composite materials. Carbon fiber's unique properties make it ideal for creating high-performance sporting equipment. Recent success stories include the development of professional touring bicycle frames weighing under 1 kg while supporting riders up to 150 kg. This achievement demonstrates how continuous fiber composites can be effectively utilized in demanding applications even when using out-of-spec materials.
The cycling industry represents just the beginning. Tennis rackets, golf clubs, hockey sticks, and skiing equipment manufacturers can all benefit from these materials. The combination of high strength-to-weight ratio and the ability to tune mechanical properties makes out-of-spec prepregs particularly valuable in these applications, where performance requirements are high but aerospace-grade certification isn't necessary.
The automotive sector presents another significant opportunity for out-of-spec prepregs. Continuous fiber composites in automobiles are increasingly important as manufacturers seek to reduce vehicle weight while maintaining structural integrity. Non-structural components such as interior panels, aesthetic elements, and aerodynamic additions represent perfect applications for these materials.
A particularly innovative application has emerged in the electric vehicle sector. The development of composite sleeves for electric motors demonstrates how efficient manufacturing processes can utilize out-of-spec materials to create high-performance components. These applications benefit from the material's retained mechanical properties while operating well within their performance capabilities.
In the industrial sector, the opportunities for out-of-spec prepregs extend far beyond simple structural components. One particularly promising area is the manufacture of pressure vessels and storage tanks. While these materials might not be suitable for critical applications like hydrogen storage tanks, they excel in less demanding storage applications where weight savings and corrosion resistance are valuable but maximum performance isn't critical.
The research and development sector also benefits significantly from access to these materials. Prototyping and testing new designs becomes more economically feasible when using out-of-spec prepregs, allowing for more extensive experimentation and innovation without the burden of full material costs.
Perhaps one of the most valuable applications lies in educational and research institutions. These organizations can utilize out-of-spec materials to provide hands-on experience with advanced composites while managing costs effectively. This approach allows for comprehensive training in composites design and manufacturing without the financial pressure of using pristine materials.
The academic sector can also use these materials for research into new manufacturing techniques, process optimization, and material behavior studies. This research often leads to innovations that benefit the entire industry, creating a virtuous cycle of knowledge and advancement.
The economic advantages of utilizing out-of-spec prepregs extend beyond simple material cost savings. Companies can realize benefits through:
Reduced waste disposal costs and environmental impact fees Lower material costs enabling more competitive pricing Ability to enter markets previously cost-prohibited Enhanced sustainability metrics and ESG performance
Success in these applications relies heavily on proper manufacturing processes. Modern automated manufacturing cells can be optimized to work with out-of-spec materials, ensuring consistent quality and reliability. The key lies in understanding the material's characteristics and adjusting processing parameters accordingly.
While these applications may not require aerospace-grade certification, maintaining consistent quality remains crucial. Advanced inspection methods and quality control processes ensure that the final products meet their intended performance requirements, even when using out-of-spec materials.
The successful utilization of out-of-spec prepregs requires more than just understanding their potential—it demands the right technology and expertise. Addcomposites, headquartered in Espoo, Finland, has developed a comprehensive ecosystem of solutions specifically designed to make composite manufacturing more accessible and efficient, including the processing of out-of-spec materials.
At the heart of Addcomposites' offering lies a revolutionary approach to automated fiber placement. The AFP-XS system exemplifies this innovation, providing a uniquely accessible entry point into automated composite manufacturing. This single-tow system's compatibility with major robot brands including Kuka, Fanuc, ABB, Kawasaki, and Yaskawa makes it an ideal solution for organizations looking to implement out-of-spec material processing efficiently.
For higher volume requirements, the AFP-X system offers enhanced capabilities with its four-tow design and significantly increased material capacity. This advanced system operates at speeds up to 500mm/s, making it perfect for organizations ready to scale their out-of-spec material utilization. The system's advanced sensors ensure continuous production monitoring, critical when working with materials that may have varying characteristics.
The processing of out-of-spec materials requires precise control and monitoring, which is where Addcomposites' software solutions shine. AddPath, their strategic path planning platform, incorporates sophisticated features essential for successful out-of-spec material processing. The software's simulation capabilities and digital twin functionality allow manufacturers to optimize their processes before actual production, reducing waste and ensuring quality outcomes.
The integration with Altair FEA software provides crucial structural analysis capabilities, helping manufacturers understand and account for any variations in material properties. This becomes particularly valuable when working with out-of-spec materials, where understanding and adapting to material characteristics is crucial for success.
The AddCell integration package represents Addcomposites' commitment to complete manufacturing solutions. This comprehensive safety cell integration package includes everything needed for successful automated manufacturing implementation:
A sophisticated safety control box ensures operator protection and process reliability. The complete wiring and cable management solutions streamline installation and maintenance. Additionally, the precise base positioning and calibration tools ensure accuracy in production, crucial when working with materials that may require specific processing parameters.
Processing out-of-spec materials often requires precise temperature control, and Addcomposites offers multiple heating solutions to address this need. The company's ability to integrate third-party heater systems and support for the Humm3 Flash lamp system provides manufacturers with the flexibility needed to optimize their processes for different material states.
Their laser system integration capabilities, including solutions from Laserline GmbH, offer power options ranging from 2KW to 4KW. This flexibility in heating solutions becomes particularly valuable when processing out-of-spec materials that may require modified processing parameters.
Understanding that successful composite manufacturing requires attention to every detail, Addcomposites provides a comprehensive range of accessories designed to optimize system performance. From specialized materials for AFP systems to precision-engineered compaction rollers, every component is designed to enhance manufacturing efficiency and quality.
Perhaps most importantly, Addcomposites recognizes that technology alone isn't enough. Their commitment to comprehensive training and global support ensures that organizations can successfully implement and optimize their composite manufacturing processes. This becomes particularly valuable when working with out-of-spec materials, where process optimization and understanding are crucial for success.
Implementing an automated solution for processing out-of-spec materials doesn't have to be overwhelming. Addcomposites' approach to AFP implementation focuses on making the technology accessible and effective. Their systems are characterized by:
Modular design with minimal moving parts, reducing complexity and maintenance needs User-friendly operation requiring minimal expert intervention Cost-effective end-to-end solutions that scale with your needs Straightforward verification through simulation and pilot projects
As the industry continues to evolve toward more sustainable practices, Addcomposites' solutions provide the foundation for future-ready manufacturing. Their commitment to advancing composite manufacturing with machine learning and digital twin technology ensures that manufacturers can stay ahead of industry trends while maximizing the value of their materials.
Successfully implementing an out-of-spec material upcycling program requires a structured approach that balances technical requirements with practical considerations. Based on recent research and industry experience, organizations can maximize their success by following established best practices and leveraging modern automation technologies.
Before diving into implementation, organizations should conduct a thorough assessment of their current operations and future needs. Design for manufacturing becomes particularly crucial when working with out-of-spec materials. This initial phase should include:
The research from Khalifa University provides valuable insights into process optimization for out-of-spec materials. Their findings suggest a two-stage approach to cure cycle development:
The optimal processing window should maintain:
Understanding these parameters forms the foundation of successful automated fiber placement processing, but each organization must fine-tune them based on their specific materials and requirements.
Quality assurance becomes particularly critical when working with out-of-spec materials. A robust quality control system should incorporate multiple elements working in harmony:
Modern process monitoring systems should track critical parameters throughout production. This includes real-time monitoring of:
Temperature profiles and thermal history Compaction pressure and uniformity Layup accuracy and fiber orientation Void content and consolidation quality
Quality verification shouldn't end with production. Implementing comprehensive non-destructive testing protocols ensures consistent product quality. This typically involves:
Ultrasonic inspection for void content verification Visual inspection for surface quality assessment Mechanical testing of representative samples Thermal analysis for cure verification
The successful implementation of an upcycling program relies heavily on well-trained personnel. Organizations should develop comprehensive training programs that cover:
Selecting the right equipment configuration is crucial for success. Modern AFP systems and components should be configured to handle the specific challenges of out-of-spec materials. Key considerations include:
The processing setup should account for material variability while maintaining consistency. Essential elements include:
Maintaining detailed documentation becomes especially important when working with out-of-spec materials. Organizations should establish:
Implementing robust process control strategies helps ensure consistent results. Key elements include:
A successful upcycling program should incorporate continuous improvement mechanisms. This includes:
Regular process performance reviews Documentation of lessons learned Update of procedures based on experience Integration of new technologies and methods Regular staff feedback and suggestion implementation
Understanding and managing risks becomes particularly important when working with out-of-spec materials. Organizations should implement:
The successful implementation of out-of-spec material upcycling programs has been demonstrated across various industries. These real-world examples showcase how proper processing, advanced automation, and careful material handling can transform what was once considered waste into valuable products.
One of the most compelling success stories comes from the professional cycling industry, where out-of-spec carbon fiber prepregs have been successfully upcycled into high-performance bicycle frames. This case study demonstrates the practical application of advanced composites manufacturing principles in a demanding real-world scenario.
The manufacturing process utilized the Mandrel wrapping technique combined with automated fiber placement technology, demonstrating how modern automation can effectively process out-of-spec materials. The success of this project validated the research findings regarding material performance retention and processing capabilities.
Another significant success story emerges from the electric vehicle sector, where manufacturers have successfully implemented efficient sleeves for electric motors using AFP. This application showcases the versatility of out-of-spec materials in demanding industrial applications.
The implemented solution achieved:
Academic institutions have successfully leveraged out-of-spec materials to enhance their research and educational capabilities. One notable case involves a partnership between a leading engineering school and industry partners, demonstrating how composites training and education can benefit from these materials.
The program achieved several key objectives:
A manufacturer of industrial equipment successfully implemented an upcycling program for producing non-critical components, showcasing how automated composite manufacturing can transform waste into value.
Their systematic approach yielded impressive results:
A sporting goods manufacturer successfully scaled their production using out-of-spec materials, demonstrating how continuous fiber composites can be effectively utilized in consumer products.
The manufacturer implemented:
Across these case studies, several common financial benefits emerged:
These success stories typically followed a structured implementation timeline:
Analysis of these case studies reveals several critical success factors:
These implementations have provided valuable insights for future projects:
The journey from waste to worth in composite manufacturing represents more than just a sustainability initiative—it's a paradigm shift in how we view and utilize valuable materials. As we've explored throughout this discussion, the successful upcycling of out-of-spec prepregs opens new horizons for manufacturers while addressing crucial environmental and economic challenges.
Recent research and successful implementations have clearly demonstrated that the shift in composite manufacturing is well underway. With retained mechanical properties of 85-87% and achievable void content of just 2.4%, out-of-spec materials present a viable option for many high-performance applications. This technical viability, combined with significant cost savings and environmental benefits, creates a compelling case for implementation.
The evidence presented supports several crucial conclusions:
For organizations looking to begin their upcycling journey, the path forward is clear. The future of composites manufacturing lies in embracing these innovative approaches through a structured implementation process:
Start with a thorough assessment of your current operations and future needs. Consider how automated manufacturing solutions can support your goals and enable efficient processing of out-of-spec materials.
Modern AFP systems, like those offered by Addcomposites, provide the precision and control needed for successful implementation. The combination of hardware solutions and advanced software capabilities ensures optimal processing and consistent results.
Success requires careful attention to:
The future of composite manufacturing lies in sustainable, efficient practices that maximize the value of all available materials. Emerging technologies and innovations continue to expand the possibilities for out-of-spec material utilization:
As the industry continues to evolve, organizations that embrace these innovative approaches will lead the way in sustainable manufacturing. The implementation of advanced composite manufacturing techniques for out-of-spec materials represents a significant opportunity for:
The time to act is now. Organizations interested in implementing an out-of-spec material upcycling program should:
The successful upcycling of out-of-spec prepregs represents a significant opportunity for the composite manufacturing industry. With proper planning, appropriate technology, and systematic implementation, organizations can transform what was once considered waste into valuable products while contributing to sustainability goals and improving bottom-line results.
Ready to transform your composite manufacturing operations? Discover how Addcomposites' solutions can help you implement an effective upcycling program. Contact us today to learn more about our automated manufacturing solutions and comprehensive support services.
Additional Resources:
This blog post draws significantly from the following research paper:
Rao, S., & Bastienne, D. (2024). Performance Evaluation of Out-of-Spec Carbon Prepregs for Upcycling Purposes. Polymers, 16(12), 1625. https://doi.org/10.3390/polym16121625
The research was conducted at the Department of Aerospace Engineering, Khalifa University of Science and Technology, Abu Dhabi, United Arab Emirates, and provides the foundational data and insights for our discussion of out-of-spec prepreg performance and processing.
Special thanks to:
The primary research paper this blog is based on was published in the open-access journal Polymers (MDPI) under the Creative Commons Attribution (CC BY) license. The research was supported by Khalifa University of Science and Technology internal grants FSU-2020-35 and received financial support from the Abu Dhabi Sports Council (ADSC).
For readers interested in diving deeper into specific aspects of composite manufacturing and automation, we recommend exploring the following resources:
This blog post was created to provide educational and informational content about composite manufacturing and material upcycling. While we strive for accuracy in all our content, readers should consult with appropriate experts and conduct their own due diligence before implementing any new manufacturing processes or technologies.