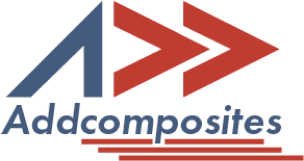
3D printing, also known as additive manufacturing, has revolutionized the way we create complex parts and prototypes. This technology allows for the rapid production of intricate geometries by building objects layer by layer. However, traditional 3D printing using polymer materials often results in parts with limited strength and performance, which can restrict their use in demanding applications.
To address these limitations, researchers and manufacturers have been exploring ways to enhance the mechanical properties of 3D printed parts. One promising approach is the use of Continuous Fiber-Reinforced Thermoplastic Composites (CFRTPC) in 3D printing. This method combines the versatility of 3D printing with the superior strength and stiffness of continuous fiber reinforcements.
CFRTPC 3D printing involves laying down continuous fibers, such as carbon or glass fibers, along with a thermoplastic matrix material. This process can significantly improve the mechanical properties of the printed parts, making them suitable for a wider range of applications in industries such as aerospace, automotive, and consumer products.
However, CFRTPC 3D printing faces a significant challenge: the discrepancy between the planned (ideal) printing tracks and the actual tracks produced during the printing process. This discrepancy can lead to several issues, including:
Understanding and addressing these discrepancies is crucial for improving the reliability and effectiveness of CFRTPC 3D printing. This blog post will explore recent research into simulating CFRTPC printing tracks, with the goal of developing more accurate models that can help predict and mitigate track errors.
By improving our ability to simulate and predict the behavior of continuous fibers during the printing process, we can take significant steps towards enhancing the quality and performance of 3D printed composite parts. This research has the potential to unlock new applications for CFRTPC 3D printing and contribute to the ongoing advancement of additive manufacturing technologies.
While Continuous Fiber-Reinforced Thermoplastic Composites (CFRTPC) 3D printing offers significant advantages in terms of part strength and performance, it also presents unique challenges. One of the most prevalent issues is the discrepancy between the planned printing path and the actual path of the deposited material. Let's explore the key aspects of these print track errors.
A frequent problem encountered during CFRTPC printing is nozzle clogging. This occurs when excess fiber material accumulates inside the printer nozzle, specifically in the PTFE (polytetrafluoroethylene) tube. The clogging can lead to printing interruptions and failures, significantly impacting the manufacturing process.
The root cause of this issue lies in the mismatch between the theoretical (planned) fiber path and the actual path taken by the fiber during printing. As the printer extrudes material based on the theoretical path, which is longer than the actual path, excess material builds up in the nozzle over time.
To better understand and quantify these track errors, researchers have focused on two key aspects:
Understanding the causes of these track deviations is crucial for developing effective solutions. Two primary factors contribute to the discrepancies:
By identifying and analyzing these print track errors, researchers can develop more accurate models and simulation techniques. These advancements are crucial for improving the reliability and quality of CFRTPC 3D printing, ultimately leading to better performance of the printed parts.
To address the challenges of track errors in Continuous Fiber-Reinforced Thermoplastic Composites (CFRTPC) 3D printing, researchers have developed mathematical models to simulate and predict fiber paths. These models aim to bridge the gap between the ideal printing tracks and the actual paths taken by the fibers during the printing process. Let's explore two key models: the line-following model and its modified version.
The line-following model is the initial approach to simulating fiber paths in CFRTPC printing. This model is based on the following principles:
This model provides a first approximation of how the fiber behaves during the printing process, taking into account the physical constraints of the nozzle and the continuous nature of the fiber.
To address the limitations of the initial model, particularly at sharp corners, researchers developed a modified line-following model. This enhanced model introduces two key improvements:
This modified model offers several advantages:
By developing and refining these mathematical models, researchers are taking significant steps towards improving the reliability and accuracy of CFRTPC 3D printing. These advancements in simulation techniques pave the way for better print path planning, reduced defects, and ultimately, higher quality 3D printed composite parts.
After developing the mathematical models for simulating fiber paths in Continuous Fiber-Reinforced Thermoplastic Composites (CFRTPC) 3D printing, it's crucial to evaluate their performance and understand their implications for real-world applications. This evaluation process involves comparing the models with actual printing results, assessing their effectiveness in reducing void areas, and analyzing the relationship between model parameters and corner angles.
To validate the accuracy of the line-following model and its modified version, researchers compared the simulated fiber paths with those observed in actual CFRTPC printing processes. This comparison involved:
The results showed that the modified line-following model, which incorporates the removal of minimum curvature points and the addition of Bezier curve transitions, provided a much closer approximation to the actual fiber paths, especially at sharp corners.
One of the primary goals of developing these models was to reduce the void areas that occur during CFRTPC printing, particularly at corners. The evaluation revealed:
These findings suggest that the modified model could significantly improve the quality of printed parts by minimizing internal voids and defects, particularly in complex geometries with sharp corners.
An important aspect of the research was understanding how the model parameters relate to different corner angles. Key findings include:
These relationships provide valuable insights for optimizing printing parameters and path planning strategies in CFRTPC 3D printing.
The evaluation of these models demonstrates their potential to significantly improve the accuracy and reliability of CFRTPC 3D printing. By providing more accurate predictions of fiber behavior, especially around corners, these models can help manufacturers:
As research in this field continues, these models may play a crucial role in advancing additive manufacturing technologies and expanding the applications of 3D printed composite materials.
The development of accurate simulation models for Continuous Fiber-Reinforced Thermoplastic Composites (CFRTPC) 3D printing opens up a range of practical applications and avenues for future research. Let's explore how these advancements can be applied in real-world scenarios and what future directions this field might take.
One of the most immediate practical applications of this research is the potential to significantly enhance the reliability of CFRTPC 3D printing processes. By implementing the modified line-following model, manufacturers can:
These improvements could lead to more consistent print quality and reduced material waste, making CFRTPC 3D printing a more viable option for a wider range of applications.
The insights gained from this research have the potential to significantly improve the quality and performance of 3D printed composite parts:
These improvements could expand the use of CFRTPC 3D printing in industries such as aerospace, automotive, and high-performance sports equipment.
While this research represents a significant step forward, there are still many exciting avenues for future investigation:
These research directions could lead to even more significant advancements in CFRTPC 3D printing technology, potentially revolutionizing how we approach the design and manufacture of composite parts.
As the field of additive manufacturing continues to evolve, the insights gained from this research into fiber path simulation will play a crucial role in pushing the boundaries of what's possible with 3D printed composites. By continuing to refine our understanding and control of the printing process, we can unlock new potentials for creating stronger, lighter, and more complex parts than ever before.
The research into simulating Continuous Fiber-Reinforced Thermoplastic Composites (CFRTPC) printing tracks represents a significant step forward in the field of additive manufacturing. By developing and refining mathematical models to predict fiber behavior during the printing process, this study has paved the way for substantial improvements in CFRTPC 3D printing technology.
The importance of simulation in advancing CFRTPC 3D printing and broader additive manufacturing technologies cannot be overstated:
As we look to the future, the continued refinement of these simulation models, potentially incorporating advanced technologies like AI and machine learning, will play a crucial role in realizing the full potential of CFRTPC 3D printing.
The journey towards perfecting CFRTPC 3D printing is ongoing, with each advancement bringing us closer to a future where complex, high-performance composite parts can be produced reliably, efficiently, and at scale. This research into fiber path simulation is a vital step in that journey, contributing to the broader goal of revolutionizing manufacturing processes across various industries.
As we continue to push the boundaries of what's possible with 3D printed composites, the insights gained from this research will undoubtedly play a crucial role in shaping the future of additive manufacturing, opening up new possibilities for innovation in aerospace, automotive, and beyond.
Are you ready to take your composite manufacturing to the next level? Addcomposites offers cutting-edge solutions for CFRTPC 3D printing and automated fiber placement that can help you achieve higher quality parts, improved efficiency, and reduced waste.
Whether you're in aerospace, automotive, or any industry requiring high-performance composite parts, Addcomposites has the tools and expertise to support your manufacturing goals.
Contact us today to learn how we can help you harness the power of advanced composite manufacturing technologies. Let's innovate together!