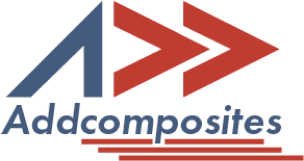
Updated: Nov 16, 2021
Sandwich construction is a structural panel concept that consists in its simplest form of two relatively thin, parallel face sheets bonded to and separated by a relatively thick, lightweight core. The core supports the face sheets against buckling and resists out-of-plane shear loads. The core must have high shear strength and compression stiffness. (Read more about the theory behind sandwich structures here)
Composite sandwich construction is most often fabricated using autoclave cure, press cure, or vacuum bag cure. Skin laminates may be pre-cured and subsequently bonded to the core, co-cured to the core in one operation, or a combination of the two methods. Examples of honeycomb structures are wing spoilers, fairings, ailerons, flaps, nacelles, floorboards, and rudders.
Sandwich construction has high bending stiffness at minimal weight in comparison to aluminum and composite laminate construction. Most honeycombs are anisotropic;
that is, properties are directional. The figure illustrates the advantages of using a honeycomb construction. Increasing the core thickness greatly increases the stiffness of the honeycomb construction, while the weight increase is minimal. Due to the high stiffness of a honeycomb construction, it is not necessary to use external stiffeners,
such as stringers and frames.
Most honeycomb structures in aircraft construction are used in combination with aluminum, fiberglass, Kevlar®, or carbon fiber face sheets. Carbon fiber face sheets cannot be used with the aluminum honeycomb core material, because it causes the aluminum to corrode. Titanium and steel cores are used for specialty applications in high-temperature environments. The face sheets of many components, such as spoilers and flight controls, are very thin-sometimes only 3 or 4 plies. Field reports have indicated that these face sheets do not have a good impact resistance.
Each honeycomb material provides certain properties and has specific benefits. The most common core material used for structures containing honeycomb core is aramid paper (Nomex® or Korex®). Fiberglass or aluminum cores are used for higher strength applications.
The standard and most common core shape, especially for aerospace applications, is the honeycomb core. Its name comes from the resemblance the hexagonal cells have of honeycombs. The cells are made by bonding stacked sheets at specific locations and intervals, then the sheets are expanded. As the sheets pull apart from each other, the bonded sections keep the sheets together, while the unbonded sections spread and create the hexagons. The direction parallel to the sheets (where the bonding occurred) is called the ribbon direction.
Bisected hexagonal core has another sheet of material cutting across each hexagon. Bisected hexagonal honeycomb is stiffer and stronger than the hexagonal core.
Bell-shaped core, or flexcore, has curved cell walls, that make it extremely flexible along the ribbon direction, and moderately flexible in all other directions. The bell-shaped core is used in panels with complex curves.
Overexpanded core is made by expanding the sheets more than is needed to make hexagons. The cells of the overexpanded core are rectangular. This core is flexible perpendicular to the ribbon direction and is used in panels with simple curves.
Honeycomb core is available with different cell sizes and densities. Smaller cell sizes with higher densities are much stiffer and heavier than larger cell sizes with lower densities. Small cell sizes are better for co-curing applications on longer, flatter components, ie helicopter blades, while larger cell sizes are better for bonding applications of curved components, ie engine nacelles. The density of the core chosen is dependent upon your structural requirements for a chosen application.
Foam cores are used on homebuilt and lighter aircraft to give strength and shape to wingtips, flight controls, fuselage sections, wings, and wing ribs. Foam cores are not commonly used on commercial-type aircraft. Foams are typically heavier than honeycomb and not as strong. A variety of foams can be used as core material including:
Sandwich structures are one of the best ways to utilize structural mechanics to design lighter and stiffer panels. Cores are the essential elements to sandwich structures. Core comes in many different combinations of materials, shapes, sizes, and densities, and a given application/manufacturing process guides the decision to choose the right core.
Addcomposites is the provider of the Automated Fiber Placement (AFP) system. The AFP system can be rented on a monthly basis to work with thermosets, thermoplastic, dry fiber placement, or in combination with 3d printers.
Advanced composites materials chapter-7
Updated: Nov 16, 2021
Sandwich construction is a structural panel concept that consists in its simplest form of two relatively thin, parallel face sheets bonded to and separated by a relatively thick, lightweight core. The core supports the face sheets against buckling and resists out-of-plane shear loads. The core must have high shear strength and compression stiffness. (Read more about the theory behind sandwich structures here)
Composite sandwich construction is most often fabricated using autoclave cure, press cure, or vacuum bag cure. Skin laminates may be pre-cured and subsequently bonded to the core, co-cured to the core in one operation, or a combination of the two methods. Examples of honeycomb structures are wing spoilers, fairings, ailerons, flaps, nacelles, floorboards, and rudders.
Sandwich construction has high bending stiffness at minimal weight in comparison to aluminum and composite laminate construction. Most honeycombs are anisotropic;
that is, properties are directional. The figure illustrates the advantages of using a honeycomb construction. Increasing the core thickness greatly increases the stiffness of the honeycomb construction, while the weight increase is minimal. Due to the high stiffness of a honeycomb construction, it is not necessary to use external stiffeners,
such as stringers and frames.
Most honeycomb structures in aircraft construction are used in combination with aluminum, fiberglass, Kevlar®, or carbon fiber face sheets. Carbon fiber face sheets cannot be used with the aluminum honeycomb core material, because it causes the aluminum to corrode. Titanium and steel cores are used for specialty applications in high-temperature environments. The face sheets of many components, such as spoilers and flight controls, are very thin-sometimes only 3 or 4 plies. Field reports have indicated that these face sheets do not have a good impact resistance.
Each honeycomb material provides certain properties and has specific benefits. The most common core material used for structures containing honeycomb core is aramid paper (Nomex® or Korex®). Fiberglass or aluminum cores are used for higher strength applications.
The standard and most common core shape, especially for aerospace applications, is the honeycomb core. Its name comes from the resemblance the hexagonal cells have of honeycombs. The cells are made by bonding stacked sheets at specific locations and intervals, then the sheets are expanded. As the sheets pull apart from each other, the bonded sections keep the sheets together, while the unbonded sections spread and create the hexagons. The direction parallel to the sheets (where the bonding occurred) is called the ribbon direction.
Bisected hexagonal core has another sheet of material cutting across each hexagon. Bisected hexagonal honeycomb is stiffer and stronger than the hexagonal core.
Bell-shaped core, or flexcore, has curved cell walls, that make it extremely flexible along the ribbon direction, and moderately flexible in all other directions. The bell-shaped core is used in panels with complex curves.
Overexpanded core is made by expanding the sheets more than is needed to make hexagons. The cells of the overexpanded core are rectangular. This core is flexible perpendicular to the ribbon direction and is used in panels with simple curves.
Honeycomb core is available with different cell sizes and densities. Smaller cell sizes with higher densities are much stiffer and heavier than larger cell sizes with lower densities. Small cell sizes are better for co-curing applications on longer, flatter components, ie helicopter blades, while larger cell sizes are better for bonding applications of curved components, ie engine nacelles. The density of the core chosen is dependent upon your structural requirements for a chosen application.
Foam cores are used on homebuilt and lighter aircraft to give strength and shape to wingtips, flight controls, fuselage sections, wings, and wing ribs. Foam cores are not commonly used on commercial-type aircraft. Foams are typically heavier than honeycomb and not as strong. A variety of foams can be used as core material including:
Sandwich structures are one of the best ways to utilize structural mechanics to design lighter and stiffer panels. Cores are the essential elements to sandwich structures. Core comes in many different combinations of materials, shapes, sizes, and densities, and a given application/manufacturing process guides the decision to choose the right core.
Addcomposites is the provider of the Automated Fiber Placement (AFP) system. The AFP system can be rented on a monthly basis to work with thermosets, thermoplastic, dry fiber placement, or in combination with 3d printers.
Advanced composites materials chapter-7