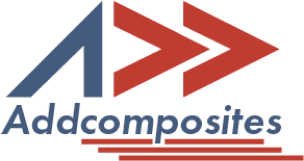
Because of their superior properties, composites have been used in many industrial applications, including aerospace, wind turbines, ships, cars, fishing rods, storage tanks, swimming pool panels, and baseball bats. Each application may require different combinations of reinforcements and matrices, which raises safety concerns during the manufacture of these substances. This article focuses on the safety issues in composite manufacturing, be it manual and automated manufacturing.
The materials used in composites manufacturing, ie matrix (polyester, vinyl ester, phenolic, epoxies, methyl ethyl ketone peroxide, benzoyl peroxide, hardeners, and solvents) and reinforcement (carbon, glass and Kevlar fibers, honeycomb and foams), can be highly toxic to the human body. These materials can also be very toxic to the environment when dumped out uncontrollably, creating major future health and environmental concerns. Throughout the labor-intensive manufacturing process, workers inhale vapors of the liquid matrix, hardeners and solvents/thinners, as well as airborne reinforcement materials (chopped fibers and particles). These can often result in extreme rashes, irritation, skin disorders, coughing, severe eye and lung injury, among other serious illnesses, as demonstrated by the table below.
Primary steps to protect workers from those hazardous substances
Automation in composite manufacturing is increasing as manufacturers have to adjust to:
As a manufacturer planning to incorporate automation, a completely different set of safety challenges need to be considered. The manufacturer should consider implementing an automated system with the following components: modern components, process monitoring, and smart systems. We will discuss these more in-depth below, but for a basic guide to incorporating automation can be found in a past article of ours, titled "A Roadmap to Automated Composites".
Traditionally, robots and humans worked separately, with the risk of injury reduced only by barriers such as cages and light curtains keeping the partners apart. However, a new generation of collaborative robots specifically designed to work alongside humans is becoming more commonplace in the factory environment.
Collaborative safety solutions such as ABB’s SafeMove allow for humans and robots to work simultaneously on the same task. Through features such as safe position and speed supervision, the flexibility and intuitiveness of humans are combined with the precision, strength, and speed of robots. This collaboration increases safety and efficiency during both operations and maintenance.
During automated processes, the control of the process parameters is very critical to ensure the quality and reduce constant vigilance by the operator. One example is Addcomposites IR thermal sensor by Optris, the process parameters can be constantly tracked and logic can be incorporated to stop layup and alarm the operator.
This type of process control through machine sensors uses real-time information about a product to improve the manufacturing process, fine-tune production and ensure consistent quality control. This happens autonomously, removing the need for humans to work with dangerous products or in dangerous areas.
Machine learning, a type of artificial intelligence (AI), allows computer systems to learn without being explicitly programmed by searching data to find patterns.
Any system which uses the information to alter the controls of a machine can be subject to machine learning integration. If programmed correctly, machine learning allows the system to not only constantly monitor and adapt to changing conditions, it can also prevent the repetition of previously learned unsafe scenarios. Addcomposites tool control provides raw data access from tool sensors for technical centers and Universities, to train their AI model, enabling the constant adoption to improve the process outcome.
Before the employee is allowed to begin working, there needs to be a thorough training course hosted by the company. This educational session needs to be tailored to your company's specific processes, and the dangers of each material and system used in manufacturing and the cleaning of tools after production. Tailoring the course allows for the employees to relate directly to their everyday working lives, and how handling these carelessly will affect them.
The key for employees to retain the most information is through engagement during the session. Engaging the employees throughout the session will make them feel more comfortable asking questions about the situation and how to protect themselves in these situations. Once the session is completed, collect signatures of the employees in attendance to make sure everyone is educated about the processes, harmful chemicals involved, and how to protect themselves in their working lives in order to ensure a safe return to their families after every shift.
Today, composites production utilizes both manual labor and advanced automation for production. With access to advanced automation technology, more and more manufacturers are aiming for complete automation. During this transition, the composite community needs to follow both protocols ensuring safety by combining the unique problem solving and flexibility of humans with the benefits of robots and automation.
Sources:
Canadian Centre of Occupational Health and Safety
Because of their superior properties, composites have been used in many industrial applications, including aerospace, wind turbines, ships, cars, fishing rods, storage tanks, swimming pool panels, and baseball bats. Each application may require different combinations of reinforcements and matrices, which raises safety concerns during the manufacture of these substances. This article focuses on the safety issues in composite manufacturing, be it manual and automated manufacturing.
The materials used in composites manufacturing, ie matrix (polyester, vinyl ester, phenolic, epoxies, methyl ethyl ketone peroxide, benzoyl peroxide, hardeners, and solvents) and reinforcement (carbon, glass and Kevlar fibers, honeycomb and foams), can be highly toxic to the human body. These materials can also be very toxic to the environment when dumped out uncontrollably, creating major future health and environmental concerns. Throughout the labor-intensive manufacturing process, workers inhale vapors of the liquid matrix, hardeners and solvents/thinners, as well as airborne reinforcement materials (chopped fibers and particles). These can often result in extreme rashes, irritation, skin disorders, coughing, severe eye and lung injury, among other serious illnesses, as demonstrated by the table below.
Primary steps to protect workers from those hazardous substances
Automation in composite manufacturing is increasing as manufacturers have to adjust to:
As a manufacturer planning to incorporate automation, a completely different set of safety challenges need to be considered. The manufacturer should consider implementing an automated system with the following components: modern components, process monitoring, and smart systems. We will discuss these more in-depth below, but for a basic guide to incorporating automation can be found in a past article of ours, titled "A Roadmap to Automated Composites".
Traditionally, robots and humans worked separately, with the risk of injury reduced only by barriers such as cages and light curtains keeping the partners apart. However, a new generation of collaborative robots specifically designed to work alongside humans is becoming more commonplace in the factory environment.
Collaborative safety solutions such as ABB’s SafeMove allow for humans and robots to work simultaneously on the same task. Through features such as safe position and speed supervision, the flexibility and intuitiveness of humans are combined with the precision, strength, and speed of robots. This collaboration increases safety and efficiency during both operations and maintenance.
During automated processes, the control of the process parameters is very critical to ensure the quality and reduce constant vigilance by the operator. One example is Addcomposites IR thermal sensor by Optris, the process parameters can be constantly tracked and logic can be incorporated to stop layup and alarm the operator.
This type of process control through machine sensors uses real-time information about a product to improve the manufacturing process, fine-tune production and ensure consistent quality control. This happens autonomously, removing the need for humans to work with dangerous products or in dangerous areas.
Machine learning, a type of artificial intelligence (AI), allows computer systems to learn without being explicitly programmed by searching data to find patterns.
Any system which uses the information to alter the controls of a machine can be subject to machine learning integration. If programmed correctly, machine learning allows the system to not only constantly monitor and adapt to changing conditions, it can also prevent the repetition of previously learned unsafe scenarios. Addcomposites tool control provides raw data access from tool sensors for technical centers and Universities, to train their AI model, enabling the constant adoption to improve the process outcome.
Before the employee is allowed to begin working, there needs to be a thorough training course hosted by the company. This educational session needs to be tailored to your company's specific processes, and the dangers of each material and system used in manufacturing and the cleaning of tools after production. Tailoring the course allows for the employees to relate directly to their everyday working lives, and how handling these carelessly will affect them.
The key for employees to retain the most information is through engagement during the session. Engaging the employees throughout the session will make them feel more comfortable asking questions about the situation and how to protect themselves in these situations. Once the session is completed, collect signatures of the employees in attendance to make sure everyone is educated about the processes, harmful chemicals involved, and how to protect themselves in their working lives in order to ensure a safe return to their families after every shift.
Today, composites production utilizes both manual labor and advanced automation for production. With access to advanced automation technology, more and more manufacturers are aiming for complete automation. During this transition, the composite community needs to follow both protocols ensuring safety by combining the unique problem solving and flexibility of humans with the benefits of robots and automation.
Sources:
Canadian Centre of Occupational Health and Safety