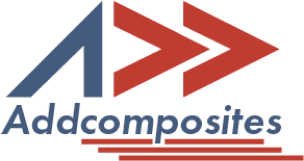
The space industry is experiencing a remarkable transformation. Private companies have disrupted the traditionally institutionalized launcher market with an innovative spirit and substantial funding, all while pursuing the ambitious goal of making space access more affordable. This shift has created a new paradigm where traditional aerospace manufacturers must reimagine their approach to production and efficiency.
At the heart of this transformation lies a critical component: propellant tanks. These essential structures must meet increasingly demanding requirements while becoming more cost-effective to manufacture. Automated Fiber Placement (AFP) has emerged as a revolutionary solution, offering precise control and consistency in manufacturing these complex components.
Traditional aerospace manufacturing faces a crucial dilemma: how to increase performance while simultaneously reducing costs. This challenge is particularly acute in upper stage components, where every gram of weight directly impacts payload capacity. The Automated Fiber Placement process offers a promising solution, enabling manufacturers to:
The journey from traditional manufacturing to modern automated processes represents a significant leap forward. Modern AFP systems incorporate advanced features such as:
This evolution in manufacturing technology isn't just about automation – it's about creating smarter, more efficient processes that can adapt to the demanding requirements of modern spacecraft components.
Modern propellant tank manufacturing has become increasingly sophisticated, incorporating AI and machine learning capabilities to optimize production processes. This integration of advanced technology allows manufacturers to:
As we delve deeper into the evolution of composite propellant tanks and their manufacturing processes, we'll explore how these technological advances are reshaping the aerospace industry and creating new possibilities for space exploration.
The story of composite propellant tanks represents one of aerospace engineering's most fascinating evolution stories. This journey, beginning in 1987, showcases how advanced composites manufacturing has transformed from an experimental concept to a crucial technology in modern spacecraft design.
The composite propellant tank story began with McDonell Douglas's groundbreaking development of their first liquid hydrogen (LH2) tank. This initial prototype featured:
The DC-XA marked a significant milestone as the first flying composite tank, designed for both LH2 and liquid oxygen (LOX) storage. Key features included:
The turn of the millennium brought significant advancements in composite manufacturing techniques, particularly in addressing key challenges:
Today's composite tank manufacturing incorporates several groundbreaking approaches:
Modern composite tank manufacturing has evolved to address several critical aspects:
The evolution continues as manufacturers explore new possibilities:
This evolutionary journey demonstrates not just technological advancement, but a fundamental shift in how we approach aerospace manufacturing. The next section will explore the specific challenges faced in modern manufacturing and how innovative solutions are addressing them.
Today's aerospace manufacturers face unprecedented challenges in producing composite propellant tanks. These challenges extend beyond simple manufacturing concerns to encompass a complex web of technical, economic, and performance requirements. Let's explore the key challenges and their implications for modern manufacturing.
Design for Manufacturing has become increasingly crucial as internal components become more sophisticated:
Advanced material selection presents several critical challenges:
Modern quality assurance in composites demands:
Process optimization presents unique challenges:
Manufacturers must balance multiple cost factors:
Safety practices in manufacturing include:
Perhaps the most significant challenge is integrating all these requirements into a cohesive manufacturing process that is both efficient and reliable. This requires:
Understanding these challenges is crucial for developing effective solutions. The next section will explore how innovative AFP manufacturing solutions address these complex requirements, creating more efficient and reliable production processes.
Modern Automated Fiber Placement (AFP) has evolved into a sophisticated manufacturing process that addresses the complex challenges of propellant tank production. This revolutionary approach has transformed how we think about composite manufacturing, introducing innovative solutions that enhance both efficiency and quality.
The heart of modern AFP technology lies in its sophisticated in-situ consolidation capabilities. Advanced heating systems, including flash lamp technology, enable real-time temperature control with unprecedented precision. These systems achieve optimal compaction pressure while maintaining advanced cooling control, ensuring consistent material properties throughout the manufacturing process.
Multi-tow capabilities have revolutionized the layup process, offering varying width options with individual tow control. The integration of automated cut-restart systems with precision placement control allows for complex geometries while maintaining consistent quality. This advancement in tow management has significantly improved manufacturing efficiency and reduced material waste.
Modern heating solutions have introduced smart heating systems that provide adaptive temperature control with zone-specific heating capabilities. These systems optimize energy efficiency while maintaining precise thermal management throughout the manufacturing process. The integration of synchronized heating control with temperature monitoring ensures optimal thermal profiles and energy distribution, crucial for achieving consistent material properties.
Contemporary path planning solutions have transformed manufacturing precision through advanced programming capabilities. These systems optimize fiber orientation while ensuring collision avoidance, generating automated paths that maximize structural efficiency. The integration of steering optimization with digital twin technology enables real-time simulation and process verification, enhancing both quality assurance and performance prediction.
The implementation of cutting-edge monitoring solutions has revolutionized quality control in AFP manufacturing. Real-time inspection capabilities now include inline thermography and tape profile monitoring, enabling immediate defect detection and automated documentation. Advanced data analytics correlate process parameters with quality outcomes, enabling predictive analysis and performance optimization throughout the manufacturing process.
Modern manufacturing cells represent a significant advancement in system integration. Sophisticated robotic control systems work in harmony with safety monitoring protocols, ensuring seamless process synchronization and equipment coordination. The implementation of automated material handling systems, coupled with intelligent tool management and production scheduling, has significantly enhanced manufacturing efficiency.
Recent developments in material processing have focused on achieving precise tension control and environmental management. Advanced tension control systems ensure optimal material properties while sophisticated tracking systems monitor material conditions throughout the process. These innovations have enabled enhanced crystallinity control, minimized void content, and improved surface quality, ultimately leading to superior bond strength in the final product.
The evolution toward intelligent manufacturing has introduced comprehensive Industry 4.0 features into AFP processes. IoT integration enables complete data connectivity and process automation, while remote monitoring capabilities ensure continuous oversight of manufacturing operations. The integration of artificial intelligence has brought sophisticated machine learning algorithms into play, enabling predictive maintenance, quality prediction, and continuous process optimization.
Looking ahead, we see emerging trends in advanced automation, with enhanced robotics integration and automated quality control becoming increasingly sophisticated. Smart process control systems continue to evolve, enabling truly adaptive manufacturing capabilities that respond to changing conditions in real-time.
The industry's focus on sustainability has led to significant developments in waste reduction and energy efficiency. Material optimization techniques, combined with environmental considerations, are shaping the next generation of AFP manufacturing solutions, ensuring both performance and responsibility in production processes.
These innovative solutions represent a significant leap forward in composite manufacturing technology, setting new standards for quality, efficiency, and sustainability. The next section will explore how these advances are integrated into comprehensive quality assurance systems, ensuring consistent, high-quality output in every manufacturing run.
In the demanding world of aerospace manufacturing, quality assurance isn't just a checkpoint – it's an integral part of the entire manufacturing process. Modern quality assurance systems in AFP manufacturing represent a significant shift from traditional to intelligent manufacturing, incorporating advanced technologies and methodologies that ensure consistent, high-quality output.
Modern AFP systems integrate sophisticated thermal monitoring through inline thermography, providing continuous process observation and comprehensive temperature distribution analysis. The system performs real-time verification of cooling rates and heat distribution mapping, ensuring optimal processing conditions throughout the manufacturing process. These capabilities enable immediate detection of potential issues such as voids, delamination, and poor consolidation, while simultaneously assessing bond quality.
The integration of advanced sensor systems takes quality assurance to the next level through sophisticated tape profile sensors. These systems perform continuous geometric verification, measuring gaps, detecting overlaps, and verifying fiber orientation with unprecedented precision. Real-time path verification ensures placement accuracy, while continuous monitoring of steering radius and layer thickness maintains consistent quality throughout the layup process.
The backbone of modern quality assurance lies in its sophisticated data management systems. Real-time data collection encompasses comprehensive process parameters, including temperature data, pressure measurements, speed monitoring, and position tracking. Quality metrics are continuously gathered, enabling immediate identification of defects, verification of placement accuracy, assessment of consolidation quality, and evaluation of surface finish.
Advanced data management takes this collected information and transforms it into actionable insights through sophisticated analysis tools. Automated analysis systems perform pattern recognition, trend analysis, and correlation studies, while predictive analytics help anticipate and prevent potential issues. The integration capabilities extend to digital twin synchronization, process optimization, and comprehensive quality documentation, ensuring complete traceability throughout the manufacturing process.
The integration of AI-driven quality control represents a quantum leap in manufacturing capability. Machine learning applications enable automated inspection processes with advanced pattern recognition and anomaly detection capabilities. These systems not only identify current issues but can predict potential problems before they occur. Process optimization through AI extends to parameter adjustment, performance prediction, and resource optimization, while also managing maintenance scheduling to prevent unexpected downtimes.
Modern quality assurance systems maintain comprehensive documentation through automated reporting systems. These systems create detailed process records that include parameter logging, quality metrics, defect mapping, and production timelines. The documentation extends to compliance requirements, ensuring material traceability, process validation, and quality verification at every step.
Non-destructive testing methods have evolved to include sophisticated inline testing capabilities. Ultrasonic inspection, thermal analysis, visual inspection, and dimensional verification occur during the manufacturing process. Post-production verification employs advanced techniques such as CT scanning, ultrasonic testing, thermography, and detailed surface analysis to ensure complete quality validation.
Advanced process control systems operate in closed-loop configurations, enabling real-time adjustments to temperature, pressure, speed, and position. These systems continuously monitor quality metrics, process parameters, and performance indicators, triggering immediate adjustments when necessary to maintain optimal production conditions.
Looking toward the future, quality assurance systems continue to evolve, moving toward enhanced integration with full process automation and complete digital integration. Predictive quality control and real-time optimization capabilities are becoming more sophisticated, while advanced analytics incorporate big data integration, AI-driven analysis, predictive modeling, and performance optimization to push the boundaries of what's possible in composite manufacturing.
The integration of these comprehensive quality assurance systems represents a fundamental shift in how we approach composite manufacturing. This evolution from traditional inspection methods to intelligent, integrated quality systems ensures consistent, high-quality output while reducing waste and optimizing resource utilization. The next section will explore how Addcomposites can help implement these advanced solutions in your manufacturing process.
Addcomposites offers a comprehensive ecosystem of solutions designed to address the complex challenges of modern composite manufacturing. Through innovative technology and integrated approaches, they're revolutionizing how manufacturers approach composite production.
The flagship AFP-XS system represents a revolutionary response to manufacturing challenges, offering exceptional versatility in integration capabilities. The system seamlessly connects with major robot brands including Kuka, Fanuc, ABB, Kawasaki, and Yaskawa, providing single-tow precision placement with remarkable accuracy. What sets this system apart is its rapid deployment capability, requiring only a month for installation, along with its ability to process multiple material types effectively.
The system's material flexibility extends across thermoset and thermoplastic processing, with additional capabilities for dry fiber handling. This versatility, combined with adaptable processing parameters, ensures manufacturers can meet diverse production requirements with a single system.
For high-volume production needs, the AFP-X system elevates capabilities to new heights. With its four-tow system and material capacity sixteen times greater than the AFP-XS, it represents a significant leap in production capability. The integration of advanced sensors and speeds up to 500mm/s makes it ideal for demanding manufacturing environments where efficiency and precision are paramount.
AddPath, the strategic planning platform, stands as a testament to Addcomposites' commitment to comprehensive manufacturing solutions. The software incorporates sophisticated simulation capabilities and digital twin functionality, enhanced by AI-powered defect detection systems. Its seamless integration with Altair FEA software ensures thorough structural analysis capabilities. The platform's availability in both Basic and Pro versions allows manufacturers to choose the feature set that best matches their specific needs.
Continuous fiber 3D printing reaches new heights with AddPrint software. This specialized processing solution handles complex CAD geometry with remarkable precision, offering 12-axis capability for intricate surface printing. The system's advanced control features ensure optimal results in even the most challenging applications.
The SCF3D system represents a revolutionary approach to manufacturing flexibility. Its ability to work with both pellets and continuous reinforcement materials opens new possibilities in production. The system excels in processing advanced materials including PA, PEEK, and PAEK, with support for both carbon and glass reinforcement options. With impressive deposition rates reaching up to 9kg/hr, it maintains precise control and consistent quality throughout the manufacturing process.
The ADD Filament Winding system takes composite manufacturing to the next level with its advanced winding capabilities. High-tension control and multi-material support enable the creation of complex components, while advanced non-geodesic paths ensure optimal fiber placement for maximum structural efficiency.
AddCell represents the pinnacle of manufacturing integration, providing comprehensive safety cell integration for modern production environments. The sophisticated control box manages complete wiring solutions and robot installation components, while precise calibration tools ensure accurate system setup and operation. The system's digital integration capabilities enhance user control and real-time monitoring, enabling comprehensive data collection and process optimization.
Addcomposites understands that technology alone isn't enough – success requires comprehensive support and training. Their expert training programs cover system operation, design optimization, and manufacturing best practices. Global support ensures assistance is always available, with local technical support and remote diagnostics providing peace of mind for manufacturers worldwide.
Addcomposites' solutions serve a diverse range of industries, from aerospace and aviation to automotive manufacturing, marine construction, and renewable energy sectors. Their presence in research institutions demonstrates the systems' versatility and cutting-edge capabilities. The company's distinctive approach, featuring modular design with minimal moving parts and user-friendly operation, makes advanced manufacturing accessible while maintaining cost-effectiveness.
What truly sets Addcomposites apart is their holistic approach to manufacturing solutions. Their integrated ecosystem provides complete manufacturing solutions, backed by comprehensive support and future-ready technology. This focus on accessibility ensures that advanced manufacturing capabilities are within reach for organizations of all sizes, with affordable solutions that can be rapidly deployed and scaled as needed.
The combination of advanced technology, comprehensive support, and practical solutions positions Addcomposites as an ideal partner for organizations looking to enhance their composite manufacturing capabilities. As we look toward future developments in composite manufacturing, Addcomposites continues to lead the way in innovation and accessibility.
As we look toward the future of composite manufacturing, several emerging trends and technologies are set to reshape the industry. These developments promise to revolutionize production methods, enhance quality, and create new possibilities in composite applications.
The integration of AI and machine learning is transforming manufacturing processes in unprecedented ways. Autonomous systems are revolutionizing process control through real-time optimization and predictive quality management. These advanced systems enable autonomous decision-making and adaptive manufacturing processes that respond instantly to changing conditions. The enhancement of quality assurance through automated defect prediction and proactive maintenance ensures consistent product quality while minimizing downtime and waste.
The push toward sustainable composites represents a significant shift in manufacturing philosophy. Material innovation has opened new possibilities through the integration of natural fibers and development of recyclable matrices. Manufacturers are increasingly focusing on biodegradable options and waste reduction strategies. Process efficiency has become paramount, with energy optimization and material utilization driving improvements in manufacturing sustainability. The implementation of circular economy principles is reshaping how the industry approaches resource management and waste reduction.
The evolution of composite materials continues to push boundaries in performance and functionality. Material selection and development now focuses on enhanced thermal resistance and improved mechanical properties. Advanced multifunctionality is being achieved through smart material integration and innovative processing techniques. The development of in-situ polymerization methods and hybrid material systems is creating new possibilities in manufacturing. Nano-enhanced composites and self-healing capabilities represent the cutting edge of material science in composite manufacturing.
The transition to intelligent manufacturing marks a fundamental shift in production methodology. Complete process digitization, supported by IoT sensor networks and cloud-based solutions, enables unprecedented levels of control and monitoring. Advanced analytics capabilities, powered by big data processing and digital twin evolution, provide manufacturers with deep insights into their processes. Predictive modeling and performance optimization tools ensure maximum efficiency and quality in production operations.
The space industry continues to drive innovation in composite manufacturing, particularly in propulsion systems and structural components. Satellite structures and launch vehicle components demand ever-higher performance from composite materials and manufacturing processes. The development of space habitats presents new challenges and opportunities for composite applications.
The clean energy sector represents another frontier for composite manufacturing. Wind energy components require increasingly sophisticated manufacturing techniques to meet growing demand and performance requirements. Hydrogen storage solutions and solar applications are creating new demands for composite manufacturing capabilities. Energy storage systems benefit from advances in composite technology and manufacturing processes.
The future of manufacturing lies in enhanced automation and process advancement. Robotic integration is becoming more sophisticated, with collaborative systems enabling flexible manufacturing approaches. Quality systems are evolving to provide real-time verification and integrated testing capabilities. Automated documentation and predictive quality control ensure consistent production excellence.
The evolution of manufacturing methods continues through focused research and development efforts. Process innovation drives improvements in efficiency and quality, while material development opens new possibilities in performance and application. The industry's focus on cost reduction and value optimization ensures that advanced manufacturing capabilities become increasingly accessible.
The technical aspects of composite manufacturing continue to evolve, with material qualification and process validation remaining critical focuses. Performance verification and standards development ensure industry-wide consistency and reliability. Market factors, including cost competition and skill development, shape the industry's growth trajectory. Market acceptance and regulatory compliance guide development priorities and implementation strategies.
Success in future composite manufacturing will depend on strategic technology adoption and process optimization. Market alignment and sustainable practices will become increasingly important differentiators. Industry collaboration through knowledge sharing and standard development will accelerate innovation and market development. Research cooperation ensures that advances in manufacturing technology translate effectively to market applications.
The future of composite manufacturing offers numerous opportunities for innovation and growth. Organizations that embrace these emerging technologies and approaches while maintaining focus on sustainability and efficiency will be well-positioned for success in this evolving industry.
The landscape of composite manufacturing for propellant tanks and aerospace components has undergone a remarkable transformation. From its early beginnings to today's advanced automated systems, the industry continues to push the boundaries of what's possible in manufacturing technology.
The manufacturing breakthrough is evident in:
Modern manufacturing has achieved:
Addcomposites' comprehensive solution offers:
To stay competitive in this evolving industry, manufacturers should:
Ready to transform your manufacturing capabilities? Here's how to begin:
Take the first step toward manufacturing excellence:
The future of composite manufacturing is here, and it's more accessible than ever. With the right partner and technology, your organization can achieve new levels of manufacturing excellence. Whether you're looking to upgrade existing processes or implement entirely new capabilities, Addcomposites provides the expertise, technology, and support you need to succeed.
Start your journey toward manufacturing excellence today. Contact Addcomposites to learn how our solutions can transform your manufacturing capabilities and help you stay ahead in an increasingly competitive market.
This blog post draws significant insights from the following research paper presented at the SAMPE Europe Conference 2020:
Brandt, L., Deden, D., Bruckner, F., Engelschall, M., Mayer, M., Schuster, A., Nieberl, D., Frommel, C., Krebs, F., Jarka, S., Fischer, F., & Larsen, L. (2020). Development of a Lean Production Process for a Thermoplastic Composite Upper Stage Propellant Tank. SAMPE Europe Conference 2020, Amsterdam, Netherlands.
Note: All links and resources are current as of publication date. For the most up-to-date information, please visit www.addcomposites.com.