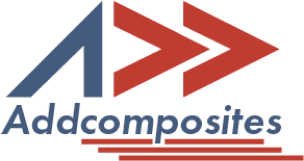
In the rapidly evolving landscape of industrial manufacturing, we at Addcomposites are proud to introduce our groundbreaking Structural Continuous Fiber 3D Printing (SCF3D) system. This innovative technology represents a significant leap forward in large-format additive manufacturing, offering unprecedented capabilities for producing high-quality structural components with continuous fiber reinforcement. As we continue to push the boundaries of what’s possible in composite manufacturing, we’re excited to share this transformative technology with forward-thinking early adopters who are ready to elevate their production capabilities.
In the current manufacturing paradigm, industries heavily rely on pure polymer or chopped fiber for printing molds and structural components. However, this approach has inherent limitations, particularly regarding the strength and weight of the final products. As a result, manufacturers are forced to use excessive material, leading to bulky and unwieldy parts that fail to optimize the strength-to-weight ratio so crucial in advanced applications[1].
Traditional large-format additive manufacturing systems primarily focus on polymer output volume, sacrificing structural integrity for production speed. This trade-off has long been a bottleneck for industries requiring both complex geometries and high-performance mechanical properties. Until now, achieving both has seemed like an impossible goal, with manufacturers forced to choose between design freedom and structural performance[7].
SCF3D emerges as a revolutionary solution that bridges the gap between conventional additive manufacturing and high-performance composite production. By integrating continuous fiber reinforcement—ranging between 30-40%—into the printing process, our system dramatically enhances the strength-to-weight ratio of manufactured parts[1].
Unlike conventional 3D printing methods, SCF3D has been designed from the ground up with composite engineering in mind. It employs extrusion-based fused granulate fabrication through our novel printing head for the AFP-XS system, allowing for multi-directional reinforcement while maintaining higher fiber volume fraction and superior bonding quality during the print process[4][5].
Our comprehensive SCF3D system includes:
The system can process a wide range of industrial polymers at temperatures up to 400°C, making it suitable for the most demanding applications across various industries[4].
By strategically incorporating continuous fiber reinforcement, SCF3D enables the production of components that are not only lighter but also up to 200 to 240 times stronger compared to conventional methods[1]. This dramatic improvement in mechanical properties opens new possibilities for weight-critical applications in aerospace, automotive, and marine industries.
One of the pivotal features of SCF3D is its ability to align strength strategically in a predetermined direction, tailored for specific applications[1][5]. Engineers can now place reinforcements precisely where needed, maximizing properties with minimal material usage. This optimization leads to more efficient and purposeful designs that were previously impossible to achieve[4].
SCF3D offers the revolutionary ability to produce complex components without the need for traditional molds, significantly reducing lead times and production costs. Additionally, the system provides the flexibility to print your own mold and add reinforcement as needed, offering unprecedented versatility in manufacturing approaches[4].
Our SCF3D system boasts an impressive throughput of 6-9 kg per hour for both continuous fiber and chopped formats, ensuring rapid production without compromising on material usage or quality[1]. This high-efficiency operation translates to faster time-to-market and reduced production costs, providing a compelling competitive advantage.
The full potential of SCF3D is unlocked through our sophisticated AddPrint software. Drawing inspiration from traditional fiber placement methodologies but specifically tailored for 3D printing applications, AddPrint offers unparalleled freedom in production planning and execution[1].
The software provides comprehensive simulation capabilities, allowing users to optimize fiber paths, predict mechanical properties, and visualize the manufacturing process before production begins. This predictive capability minimizes waste, reduces iteration cycles, and ensures first-time-right manufacturing.
SCF3D technology is poised to revolutionize manufacturing across numerous sectors:
The exceptional strength-to-weight ratio of SCF3D-printed components makes them ideal for aerospace applications where every gram matters. From structural components to complex internal geometries, the ability to strategically reinforce critical areas opens new design possibilities for next-generation aircraft and spacecraft.
Automotive manufacturers can leverage SCF3D to produce lighter, stronger components that contribute to increased fuel efficiency and performance. The technology is particularly valuable for prototyping and small-batch production of specialized parts.
The corrosion resistance of composite materials combined with the structural integrity provided by continuous fiber reinforcement makes SCF3D an excellent choice for marine applications, from boat hulls to internal structural components.
The ability to tailor fiber orientation for specific load cases makes SCF3D ideal for producing high-performance sporting equipment with optimized weight, strength, and flexibility characteristics.
Structural Continuous Fiber 3D Printing represents not just an incremental improvement but a paradigm shift in additive manufacturing. By combining the design freedom of 3D printing with the superior mechanical properties of continuous fiber composites, SCF3D opens new horizons for innovative product development and efficient manufacturing processes.
As we continue to refine and expand this technology, we invite forward-thinking manufacturers and designers to join us in exploring the possibilities. The future of manufacturing is here, and it’s being shaped by technologies like SCF3D that challenge conventional limitations and embrace the full potential of composite materials.
Are you ready to explore how SCF3D technology can transform your manufacturing capabilities? Our team at Addcomposites is eager to discuss your specific applications and requirements.
Get a Free License of AddPrint: Experience the power of our advanced software firsthand. Contact our team today to request your free license of AddPrint and begin your journey toward manufacturing optimization.
Reach out to learn more about SCF3D technology, schedule a demonstration, or discuss how we can help you implement this revolutionary system in your production environment. Together, we can redefine what’s possible in manufacturing.