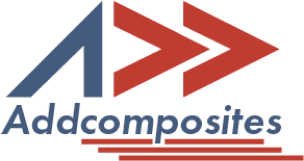
The global race toward a hydrogen-based economy has thrust a seemingly simple component into the spotlight: the pressure vessel. As industries worldwide push for more efficient hydrogen storage solutions, the challenge isn't just about storing hydrogen – it's about doing so in a way that maximizes efficiency while minimizing weight and cost. At the heart of this challenge lies a critical manufacturing innovation: dome reinforcement through automated fiber placement (AFP) technology.
Traditional pressure vessel manufacturing has long relied on conventional filament winding techniques, which, while proven, come with inherent limitations. The fundamental challenges of filament winding have become increasingly apparent as industry demands push toward higher performance standards. These limitations are particularly evident in the crucial dome regions of pressure vessels, where traditional manufacturing methods often result in excessive material usage and suboptimal fiber orientations.
Enter automated fiber placement technology – a revolutionary approach that's reshaping how we think about dome reinforcement in composite pressure vessels. This technology, exemplified by systems like the AFP-XS, represents more than just an incremental improvement; it's a paradigm shift in composite manufacturing. By combining precise fiber placement capabilities with advanced control systems, AFP technology is opening new possibilities in pressure vessel design and manufacturing.
As we delve into the evolution and impact of dome reinforcement technology, we'll explore how AFP is not just solving today's manufacturing challenges but also paving the way for future innovations in composite pressure vessel production. From material efficiency to production scalability, the implications of this technological advancement extend far beyond traditional manufacturing boundaries.
The foundation of modern pressure vessel production begins with rotomolded liners, typically using high-density polyethylene (HDPE) or polyamide materials. These liners are then reinforced through various composite winding techniques, ranging from traditional wet winding to advanced prepreg systems.
Current manufacturing methods face several critical limitations:
Recent studies in composite pressure vessel design indicate that these limitations directly impact vessel performance. Traditional winding patterns often result in up to 30% excess material in dome regions, significantly affecting both weight and cost efficiency.
These challenges become particularly acute as industries push for:
The evolution of manufacturing techniques shows a clear need for more sophisticated approaches to dome reinforcement, particularly in high-performance applications like hydrogen storage systems.
Dome reinforcement represents a crucial advancement in pressure vessel optimization. Recent studies in hydrogen tank design demonstrate that proper dome reinforcement can:
The most effective approach for complex geometries, offering:
Traditional method utilizing prefabricated dome caps:
Modern manufacturing combines multiple techniques:
Data from recent implementations shows:
Detailed analysis of these improvements demonstrates the substantial impact on both manufacturing efficiency and product performance.
Automated Fiber Placement (AFP) technology transforms pressure vessel manufacturing by eliminating traditional winding constraints. Unlike conventional methods, AFP offers:
Modern AFP systems handle multiple material types:
Learn more about material selection
Comparative studies show AFP superiority in:
AFP systems enable:
The AFP-XS system uniquely combines filament winding and AFP capabilities:
Advanced control features include:
Implementation data shows:
Cost analysis demonstrates:
Advanced automation technologies are reshaping production:
Next-generation manufacturing incorporates:
Emerging developments include:
Market projections indicate:
The evolution from traditional winding to AFP-based dome reinforcement represents more than just a technological advancement—it's a paradigm shift in pressure vessel manufacturing. As industries continue to push the boundaries of performance and efficiency, technologies like the AFP-XS system stand at the forefront of this revolution, enabling the creation of lighter, stronger, and more efficient storage solutions.
The future of pressure vessel manufacturing lies in the intelligent integration of advanced manufacturing techniques, and AFP technology is leading the way. By combining precision, versatility, and efficiency, we're not just building better tanks—we're laying the foundation for a more sustainable energy future.
Are you ready to take your composite manufacturing to the next level? Addcomposites offers cutting-edge solutions for CFRTPC 3D printing and automated fiber placement that can help you achieve higher quality parts, improved efficiency, and reduced waste.
Whether you're in aerospace, automotive, or any industry requiring high-performance composite parts, Addcomposites has the tools and expertise to support your manufacturing goals.
Contact us today to learn how we can help you harness the power of advanced composite manufacturing technologies. Let's innovate together!