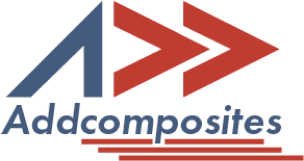
Imagine crafting a sleek airplane wing or a streamlined boat hull without the need for expensive, custom-made moulds. This scenario, once a distant dream for composite manufacturers, is now inching closer to reality thanks to an innovative technique called Eccentric Fibre Prestress (EFP).
In the world of advanced materials, fibre-reinforced polymer (FRP) composites have long been celebrated for their exceptional strength-to-weight ratio. These materials are the unsung heroes in industries where every gram matters, from aerospace to high-performance automobiles. However, the creation of complex curved structures using FRPs has traditionally been a costly and inflexible process, often requiring substantial investments in moulding equipment.
Enter Eccentric Fibre Prestress - a groundbreaking approach that promises to reshape the landscape of composite manufacturing. By cleverly manipulating the internal stresses within composite laminates, EFP allows engineers to create compound curvatures without the need for complex moulds. This technique not only has the potential to significantly reduce production costs but also opens up new avenues for design innovation.
In this post, we'll dive into the fascinating world of EFP, exploring how this technique works, its experimental validation, and its potential to revolutionize industries reliant on advanced composite materials. From simplified manufacturing processes to the creation of intricate aerofoil shapes, EFP is poised to usher in a new era of composite design and production.
To fully appreciate the innovation of Eccentric Fibre Prestress (EFP), it's crucial to understand the current landscape of composite manufacturing and some key concepts.
Fibre-reinforced polymer (FRP) composites have become indispensable in industries where high strength and low weight are paramount. These materials consist of strong fibres (such as carbon or glass) embedded in a polymer matrix, resulting in a material that's both lightweight and incredibly strong.
Traditionally, creating complex shapes with FRP composites involves laying the composite material over or into a mould, then curing it to retain the desired shape. This process, while effective, comes with significant drawbacks:
Before delving into EFP, let's clarify some important terms:
Understanding these concepts sets the stage for appreciating how EFP works and why it represents such a significant advancement in composite manufacturing. By manipulating these elements, EFP offers a novel approach to creating complex shapes without the need for expensive moulds.
Despite the numerous advantages of FRP composites, their manufacturing process has long been plagued by several limitations:
These limitations have long been accepted as necessary trade-offs for the benefits of composite materials. However, they have also restricted the wider adoption of composites in various industries, particularly where cost-effectiveness and design flexibility are crucial.
Eccentric Fibre Prestress emerges as an innovative solution to address these longstanding challenges. At its core, EFP is a technique that manipulates the internal stresses within a composite laminate to create desired curvatures without the need for a shaped mould.
Here's how EFP works:
The advantages of EFP over traditional methods are significant:
By addressing the core limitations of traditional composite manufacturing, EFP opens up new possibilities for the use of composites across various industries, from aerospace and automotive to marine and renewable energy.
To demonstrate the effectiveness of EFP, researchers conducted a series of experiments using different laminate configurations:
These experiments not only validated the EFP concept but also highlighted its versatility in creating various curved profiles using different material combinations and prestress configurations.
To predict and optimize EFP outcomes, researchers developed an analytical model based on Euler-Bernoulli beam theory. This model provides a mathematical framework for understanding and designing EFP laminates.
Key aspects of the analytical model include:
The accuracy of this model was demonstrated by comparing its predictions with the experimental results. Across all experiments, the model showed good correlation with actual outcomes, with low root mean square errors (RMSE) between predicted and measured profiles.
For instance:
This close agreement between analytical predictions and experimental results validates the model's effectiveness as a design tool for EFP laminates.
The development of this accurate analytical model is crucial for the practical application of EFP. It allows engineers to design and optimize EFP laminates for specific curvatures without extensive trial and error, potentially saving time and resources in the manufacturing process.
To demonstrate the practical potential of EFP in real-world applications, the researchers tackled a challenging and relevant example: creating the upper surface of a NACA 4412 aerofoil.
The NACA 4412 aerofoil presents a complex, compound curvature that's crucial for its aerodynamic performance. To achieve this shape using EFP, the researchers employed an inverse design approach utilizing a Genetic Algorithm (GA).
Here's how the process worked:
a) Problem Definition: The goal was to determine the optimal laminate configuration to produce the desired aerofoil shape.
b) GA Setup:
c) Optimization Process: The GA iteratively adjusted the number and arrangement of plies in each segment, comparing the resulting shape to the target aerofoil profile.
d) Convergence: After 150 generations, the algorithm converged on a solution with a low root mean square error (RMSE) of 1.98, indicating a close match to the desired profile.
This inverse design approach demonstrates the power of combining EFP with computational optimization techniques, enabling the creation of complex, precisely defined shapes.
Following the GA optimization, an aerofoil demonstrator was manufactured using the determined laminate configuration:
a) Manufacturing Process:
b) Results Analysis:
This successful creation of a complex aerofoil shape demonstrates the potential of EFP for producing high-precision, aerodynamic structures without the need for expensive moulds. It showcases the technique's ability to create shapes that would be challenging or costly to produce using traditional composite manufacturing methods.
The NACA 4412 aerofoil example serves as a powerful proof-of-concept for EFP, illustrating its potential applications in aerospace, wind energy, and other industries where precise, complex curvatures are crucial. It highlights how EFP, combined with advanced optimization techniques, can open new possibilities in composite design and manufacturing.
The development of Eccentric Fibre Prestress (EFP) represents a significant advancement in composite manufacturing. Here are the key practical implications and potential applications of this technology:
While EFP shows great promise, there are still areas that require further investigation:
By addressing these areas, EFP could become an even more powerful tool in the composite manufacturing toolkit, potentially revolutionizing how we approach the design and production of complex curved structures across numerous industries.
Eccentric Fibre Prestress (EFP) represents a significant leap forward in the field of composite manufacturing, offering a novel solution to long-standing challenges in the industry. Let's recap the key points and consider the future implications of this technology:
A. Summary of EFP Benefits
B. Future Directions for the Technology
As promising as EFP is, it's important to recognize that this is just the beginning. The future of EFP could include:
In conclusion, Eccentric Fibre Prestress represents not just a new manufacturing technique, but a paradigm shift in how we approach the design and production of composite structures. By freeing composite manufacturing from the constraints of traditional moulding processes, EFP opens up a world of possibilities for innovation across numerous industries. As we continue to push the boundaries of what's possible with composites, technologies like EFP will play a crucial role in shaping a more flexible, efficient, and sustainable manufacturing future.
The journey of EFP is just beginning, and its full potential is yet to be realized. As research continues and the technology matures, we can expect to see even more exciting developments in this field. The future of composite manufacturing looks bright, and EFP is poised to play a significant role in shaping that future.
Robotics Power displayed through Tesla Optimus Robot
Discover the future of composite manufacturing with Addcomposites! Here's how you can get involved:
At Addcomposites, we are dedicated to revolutionizing composite manufacturing. Our AFP systems and comprehensive support services are waiting for you to harness. So, don't wait – get started on your journey to the future of manufacturing today!
Imagine crafting a sleek airplane wing or a streamlined boat hull without the need for expensive, custom-made moulds. This scenario, once a distant dream for composite manufacturers, is now inching closer to reality thanks to an innovative technique called Eccentric Fibre Prestress (EFP).
In the world of advanced materials, fibre-reinforced polymer (FRP) composites have long been celebrated for their exceptional strength-to-weight ratio. These materials are the unsung heroes in industries where every gram matters, from aerospace to high-performance automobiles. However, the creation of complex curved structures using FRPs has traditionally been a costly and inflexible process, often requiring substantial investments in moulding equipment.
Enter Eccentric Fibre Prestress - a groundbreaking approach that promises to reshape the landscape of composite manufacturing. By cleverly manipulating the internal stresses within composite laminates, EFP allows engineers to create compound curvatures without the need for complex moulds. This technique not only has the potential to significantly reduce production costs but also opens up new avenues for design innovation.
In this post, we'll dive into the fascinating world of EFP, exploring how this technique works, its experimental validation, and its potential to revolutionize industries reliant on advanced composite materials. From simplified manufacturing processes to the creation of intricate aerofoil shapes, EFP is poised to usher in a new era of composite design and production.
To fully appreciate the innovation of Eccentric Fibre Prestress (EFP), it's crucial to understand the current landscape of composite manufacturing and some key concepts.
Fibre-reinforced polymer (FRP) composites have become indispensable in industries where high strength and low weight are paramount. These materials consist of strong fibres (such as carbon or glass) embedded in a polymer matrix, resulting in a material that's both lightweight and incredibly strong.
Traditionally, creating complex shapes with FRP composites involves laying the composite material over or into a mould, then curing it to retain the desired shape. This process, while effective, comes with significant drawbacks:
Before delving into EFP, let's clarify some important terms:
Understanding these concepts sets the stage for appreciating how EFP works and why it represents such a significant advancement in composite manufacturing. By manipulating these elements, EFP offers a novel approach to creating complex shapes without the need for expensive moulds.
Despite the numerous advantages of FRP composites, their manufacturing process has long been plagued by several limitations:
These limitations have long been accepted as necessary trade-offs for the benefits of composite materials. However, they have also restricted the wider adoption of composites in various industries, particularly where cost-effectiveness and design flexibility are crucial.
Eccentric Fibre Prestress emerges as an innovative solution to address these longstanding challenges. At its core, EFP is a technique that manipulates the internal stresses within a composite laminate to create desired curvatures without the need for a shaped mould.
Here's how EFP works:
The advantages of EFP over traditional methods are significant:
By addressing the core limitations of traditional composite manufacturing, EFP opens up new possibilities for the use of composites across various industries, from aerospace and automotive to marine and renewable energy.
To demonstrate the effectiveness of EFP, researchers conducted a series of experiments using different laminate configurations:
These experiments not only validated the EFP concept but also highlighted its versatility in creating various curved profiles using different material combinations and prestress configurations.
To predict and optimize EFP outcomes, researchers developed an analytical model based on Euler-Bernoulli beam theory. This model provides a mathematical framework for understanding and designing EFP laminates.
Key aspects of the analytical model include:
The accuracy of this model was demonstrated by comparing its predictions with the experimental results. Across all experiments, the model showed good correlation with actual outcomes, with low root mean square errors (RMSE) between predicted and measured profiles.
For instance:
This close agreement between analytical predictions and experimental results validates the model's effectiveness as a design tool for EFP laminates.
The development of this accurate analytical model is crucial for the practical application of EFP. It allows engineers to design and optimize EFP laminates for specific curvatures without extensive trial and error, potentially saving time and resources in the manufacturing process.
To demonstrate the practical potential of EFP in real-world applications, the researchers tackled a challenging and relevant example: creating the upper surface of a NACA 4412 aerofoil.
The NACA 4412 aerofoil presents a complex, compound curvature that's crucial for its aerodynamic performance. To achieve this shape using EFP, the researchers employed an inverse design approach utilizing a Genetic Algorithm (GA).
Here's how the process worked:
a) Problem Definition: The goal was to determine the optimal laminate configuration to produce the desired aerofoil shape.
b) GA Setup:
c) Optimization Process: The GA iteratively adjusted the number and arrangement of plies in each segment, comparing the resulting shape to the target aerofoil profile.
d) Convergence: After 150 generations, the algorithm converged on a solution with a low root mean square error (RMSE) of 1.98, indicating a close match to the desired profile.
This inverse design approach demonstrates the power of combining EFP with computational optimization techniques, enabling the creation of complex, precisely defined shapes.
Following the GA optimization, an aerofoil demonstrator was manufactured using the determined laminate configuration:
a) Manufacturing Process:
b) Results Analysis:
This successful creation of a complex aerofoil shape demonstrates the potential of EFP for producing high-precision, aerodynamic structures without the need for expensive moulds. It showcases the technique's ability to create shapes that would be challenging or costly to produce using traditional composite manufacturing methods.
The NACA 4412 aerofoil example serves as a powerful proof-of-concept for EFP, illustrating its potential applications in aerospace, wind energy, and other industries where precise, complex curvatures are crucial. It highlights how EFP, combined with advanced optimization techniques, can open new possibilities in composite design and manufacturing.
The development of Eccentric Fibre Prestress (EFP) represents a significant advancement in composite manufacturing. Here are the key practical implications and potential applications of this technology:
While EFP shows great promise, there are still areas that require further investigation:
By addressing these areas, EFP could become an even more powerful tool in the composite manufacturing toolkit, potentially revolutionizing how we approach the design and production of complex curved structures across numerous industries.
Eccentric Fibre Prestress (EFP) represents a significant leap forward in the field of composite manufacturing, offering a novel solution to long-standing challenges in the industry. Let's recap the key points and consider the future implications of this technology:
A. Summary of EFP Benefits
B. Future Directions for the Technology
As promising as EFP is, it's important to recognize that this is just the beginning. The future of EFP could include:
In conclusion, Eccentric Fibre Prestress represents not just a new manufacturing technique, but a paradigm shift in how we approach the design and production of composite structures. By freeing composite manufacturing from the constraints of traditional moulding processes, EFP opens up a world of possibilities for innovation across numerous industries. As we continue to push the boundaries of what's possible with composites, technologies like EFP will play a crucial role in shaping a more flexible, efficient, and sustainable manufacturing future.
The journey of EFP is just beginning, and its full potential is yet to be realized. As research continues and the technology matures, we can expect to see even more exciting developments in this field. The future of composite manufacturing looks bright, and EFP is poised to play a significant role in shaping that future.
Robotics Power displayed through Tesla Optimus Robot
Discover the future of composite manufacturing with Addcomposites! Here's how you can get involved:
At Addcomposites, we are dedicated to revolutionizing composite manufacturing. Our AFP systems and comprehensive support services are waiting for you to harness. So, don't wait – get started on your journey to the future of manufacturing today!