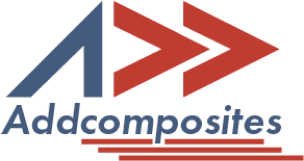
The world of composite materials is undergoing a revolutionary transformation through additive manufacturing technologies. At the forefront of this evolution is the 3D printing of continuous carbon fiber reinforced thermoplastics (c-CFRTP), a technology that promises to deliver complex composite structures with unprecedented design freedom and performance capabilities.
Understanding continuous fiber composites reveals their remarkable potential: these materials combine the strength of continuous carbon fibers with the versatility of thermoplastic matrices, offering exceptional mechanical properties and design flexibility. Through 3D printing, manufacturers can create complex composite structures with curvilinear fiber steering - a capability that traditional manufacturing methods struggle to achieve.
However, this promising technology faces significant challenges. Current 3D printing processes for c-CFRTP often result in:
These defects and damage in composite materials have historically restricted the application of 3D-printed c-CFRTP in high-performance structural parts, where mechanical properties are crucial.
Recent research has unveiled a promising solution to these challenges through the innovative application of tension and compaction forces during the printing process. This approach addresses two critical aspects of composite printing:
The results are compelling: mechanical property improvements of up to 45% in flexural strength and 28% in flexural stiffness compared to standard printing processes. These improvements bring 3D-printed composites closer to the performance levels of traditionally manufactured composite materials.
The ability to precisely control fiber orientation and minimize voids during 3D printing opens new possibilities for:
In this article, we'll explore how this innovative approach works, examine the key findings from recent research, and discuss the practical implications for composite manufacturing. Whether you're a manufacturer, researcher, or composite enthusiast, understanding these advancements is crucial for staying at the forefront of composite technology.
When it comes to 3D printing of continuous fiber composites, two primary challenges significantly impact the final part's performance: fiber waviness and void formation. Let's dive deep into these issues to understand why they occur and how they affect the printed components.
Fiber waviness in 3D-printed composites occurs at two distinct scales:
This larger-scale distortion occurs primarily due to the printing process itself. When the fused filament is bent 90° just after extrusion from the nozzle, it creates a fundamental geometric challenge: the outer and inner radii of the bend must accommodate different lengths of material. This length difference leads to:
At the individual fiber level, misalignments occur as the fibers attempt to accommodate the geometric constraints of the printing path. This results in:
Defects in composite materials often manifest as voids, which occur at two distinct scales in 3D-printed c-CFRTP:
The presence of these defects significantly impacts the mechanical properties of printed components:
Previous attempts to address these issues have included:
However, these solutions often introduce new complications or trade-offs that limit their practical application. What's needed is a more comprehensive approach that addresses both fiber waviness and void formation simultaneously - which is where the innovative tension and compaction control method comes into play.
Understanding these core problems is crucial for appreciating the significance of the tension and compaction control solution, which we'll explore in detail in the next section.
While traditional filament winding has long used tension control, applying these principles to 3D printing requires a novel approach. The innovation lies in combining precise tension control with strategic compaction force application, creating a synergistic effect that addresses multiple manufacturing challenges simultaneously.
The tension control system operates through a surprisingly elegant principle: asynchronous feeding. This means:
The compaction force system introduces another key parameter: the compaction rate.
When combined, tension and compaction create multiple benefits:
The innovation goes beyond simple parameter settings to include intelligent control:
For successful implementation, several factors must be considered:
This innovative approach represents a significant advancement in composite manufacturing processes, offering a practical solution to long-standing challenges in 3D printed composites. The next section will explore the quantitative improvements and real-world benefits this system provides.
The implementation of tension and compaction control in 3D printed continuous fiber composites has led to significant measurable improvements across multiple performance metrics. Let's break down these improvements and understand their practical implications.
The combination of tension and compaction achieved:
As documented through advanced inspection methods, the enhanced process showed:
These improvements have significant implications for composite applications:
These results demonstrate that the combination of tension and compaction control represents a significant advancement in 3D printed composite manufacturing, offering substantial improvements in both material properties and manufacturing reliability.
When implementing tension and compaction control in automated fiber placement, several key parameters must be carefully controlled:
As outlined in composite manufacturing tracking:
As composite manufacturing evolves, consider:
The development of tension and compaction control in 3D printed composites represents more than just a technical advancement - it signals a fundamental shift in how we approach composite manufacturing. Let's explore the far-reaching implications of this innovation.
The improvements in mechanical properties and consistency open new possibilities for aerospace composites:
Automotive applications benefit from:
This technology aligns with sustainable composite practices:
Future research directions include:
Areas for further investigation:
The future of this technology points toward:
This innovation represents a significant step forward in advancing composite manufacturing, setting the stage for continued development and broader adoption across industries.
The introduction of tension and compaction control in 3D printed composites marks a significant milestone in manufacturing technology. This advancement addresses long-standing challenges that have historically limited the adoption of 3D printed continuous fiber composites in high-performance applications.
The real-world implications of this technology are substantial:
As composite manufacturing evolves, this technology positions itself as a cornerstone for future developments:
The development of tension and compaction control in 3D printed composites represents more than just a technical advancement - it's a paradigm shift in composite manufacturing. By addressing fundamental challenges while maintaining practical implementability, this innovation opens new possibilities for composite applications across industries.
As we look to the future, the potential for further development and optimization remains vast. The foundation has been laid for continued advancement in composite manufacturing technology, promising even greater capabilities and applications in the years to come.
For manufacturers, engineers, and researchers in the field, this technology offers a clear path forward - one that combines enhanced performance with practical implementation. The journey toward perfect composite parts continues, but with tension and compaction control, we've taken a significant step in the right direction.
Remember: The path to innovation is rarely straight, but with careful control of tension and compaction, we can ensure our composite materials follow the path we design for them.
This blog post is based on the research paper:
Ichihara, N., et al. (2023). "3D printing with tension and compaction: Prevention of fiber waviness in 3D-printed continuous carbon fiber reinforced thermoplastics." Advanced Composite Materials. DOI: 10.1080/09243046.2023.2260233
Are you ready to revolutionize your composite manufacturing process? Addcomposites offers cutting-edge solutions that incorporate advanced tension and compaction control technologies.
Visit www.addcomposites.com to learn more about how we can help optimize your composite manufacturing processes.