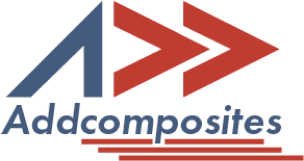
Quality assurance (QA) and quality control (QC) are essential aspects of any manufacturing process, and composites manufacturing is no exception. QA focuses on preventing defects before they occur by establishing and maintaining processes that ensure the desired quality is consistently achieved 1. QC, on the other hand, focuses on verifying that quality standards are met through testing and inspection 1. In the context of composites manufacturing, QA/QC becomes even more critical due to the unique challenges and considerations involved in producing high-quality composite parts. This report provides an introduction to QA and QC in composites manufacturing, covering various aspects, including common defects, non-destructive testing methods, quality standards, and the role of automation and Industry 4.0 in enhancing quality.
QA and QC are essential for maintaining high standards in manufacturing. QA takes a proactive approach to defect prevention, while QC focuses on identifying and correcting defects during production 1. Implementing a well-structured Quality Management System (QMS) is fundamental to QA, involving documenting processes, establishing procedures, and setting standards to ensure consistent quality throughout all manufacturing stages 2. Key pillars of QA in manufacturing include process control, supplier quality management, employee training, product testing and inspection, and continuous improvement 2.
To ensure customer satisfaction and maintain high-quality standards, key performance indicators (KPIs) are used in quality assurance. These KPIs include:
Furthermore, QA in manufacturing offers several benefits, including:
QC procedures involve testing and verification at various production phases to identify and rectify defects 4. Effective QC methods include inspection, testing, documentation, monitoring systems, corrective action plans, and continuous improvement initiatives 4. The quality control process is crucial for ensuring trustworthy products and demonstrating brand integrity. By implementing extensive procedures for product inspection and testing, manufacturers can minimize unexpected issues, support customer safety, and build trust with consumers 5.
Several approaches can be used for quality control in manufacturing:
Different techniques are employed for measuring quality in manufacturing. Univariate charts analyze a specific product attribute, while multivariate charts measure variances in several product attributes. These charts help track defects per production unit and identify the types of defects occurring 7.
Enterprise Resource Planning (ERP) systems play a crucial role in quality assurance by acting as a centralized hub for various business processes and consolidating data from different departments. This centralized data management ensures easy accessibility to quality-related information, allowing teams to monitor and analyze quality metrics efficiently 4.
Composites manufacturing presents unique challenges due to the anisotropic nature of composite materials, their susceptibility to delamination, complex failure modes, and sensitivity to process parameters 8. The quality of composite parts is highly sensitive to process parameters such as temperature, pressure, and cure cycle, making precise control crucial 8. In addition to manufacturing defects, composites can also experience issues during their service life, such as environmental degradation, fatigue damage, thermal damage, and chemical attack 8. Some specific challenges include:
Furthermore, machining composite materials presents its own set of challenges:
Another important consideration in composites manufacturing is worker safety. The materials used in composites production, such as resins, fibers, and curing agents, can pose potential health hazards to workers 10. These hazards include:
To mitigate these risks, manufacturers should implement appropriate safety measures, such as:
Addressing these challenges and considerations is crucial for ensuring the quality and safety of composite parts and the manufacturing process.
The heterogeneous microstructure of composites can lead to various defects during manufacturing. Some common defects include:
In addition to manufacturing defects, composites can also experience issues during their service life, such as environmental degradation, fatigue damage, thermal damage, and chemical attack 8. These issues can lead to various types of failures in composite materials, including bond failure, fiber buckling, cracking, and delamination 13.
Several factors can contribute to the formation of defects in composite materials:
Understanding these defects and their causes is crucial for implementing effective quality control measures and ensuring the production of high-quality composite parts.
NDT methods are essential for evaluating the quality of composite parts without causing damage. These methods allow for the detection of internal and surface flaws, characterization of material properties, and assessment of structural integrity 15. Some common NDT methods used in composites manufacturing include:
In addition to these common methods, other NDT techniques used in composites inspection include:
The selection of an appropriate NDT method depends on factors such as the type of defect to be detected, material properties, accessibility, and cost constraints 15. Often, a multi-method approach is employed for comprehensive inspection, combining the strengths of different techniques 8.
The future development of NDT techniques for composites is directed towards intelligent and automated inspection systems with high accuracy and efficient data processing capabilities 17. These advancements will improve the efficiency and effectiveness of quality control, leading to safer and more reliable composite structures.
Various quality standards and certifications are relevant to composites manufacturing, ensuring that materials and processes meet industry requirements and safety standards. These standards are developed and maintained by several organizations, including:
Some important standards and certifications include:
These standards and certifications play a crucial role in ensuring the quality and reliability of composite materials and products.
Automation and Industry 4.0 technologies are transforming QA/QC processes in composites manufacturing. Automated systems offer several advantages, including:
One example of automation in QA is the use of barcodes for tracking composite products. Each product is equipped with a unique barcode, and quality assurance tracking is automated by attaching relevant data to the barcode as the product proceeds through the fabrication and quality control sequence 25. This technology improves efficiency and traceability in quality control.
Automated testing systems also play a crucial role in quality control. These systems can handle specimens, perform tests according to standard requirements, and sort specimens for verification 26. The benefits of automated testing systems include:
However, implementing automation in composites manufacturing also presents challenges:
The composites industry faces challenges in adopting Industry 4.0 technologies due to the lack of a structured implementation framework. To address this gap, a conceptual framework based on the systems engineering V model has been proposed 28. This framework guides the implementation of Industry 4.0 technologies by considering various aspects, such as:
This framework provides a structured approach to implementing Industry 4.0 technologies, helping composite manufacturers overcome the challenges and realize the benefits of automation and digitalization.
Comparison of Hand Layup and Automated Manufacturing
Traditional hand layup methods have been a cornerstone of composite manufacturing, but they have limitations in terms of efficiency, consistency, and material utilization. Automated composite manufacturing techniques, such as AFP and continuous fiber printing, offer several advantages over hand layup:
While automated manufacturing offers significant benefits, it also requires higher upfront investment and specialized knowledge. The choice between hand layup and automated manufacturing depends on factors such as production volume, part complexity, and budget constraints.
The manufacturing of composite structures is a complex task with inherent risks, particularly associated with the uncertainty of materials and processes 29. Industry 4.0 technologies can help mitigate these risks by enabling better decision-making through data-driven models and real-time process monitoring.
Advancements in composites manufacturing technologies are further enhancing quality and efficiency. This section explores three key technologies:
Continuous fiber printing is an additive manufacturing process that combines a composite base material with continuous fibers, such as carbon fiber or Kevlar, to create strong and lightweight parts with tailored properties 30. This technology allows for precise control over fiber placement and orientation, enabling the creation of parts with optimized mechanical properties.
Different technologies are used to produce filament with continuous fiber. These technologies involve impregnating fiber strands with a polymer matrix, such as a thermoplastic or thermoset resin. The impregnation process must be carefully controlled to ensure proper fiber wet-out and avoid voids or defects, which can compromise the mechanical properties of the printed part 32.
Continuous fiber printing offers several advantages over traditional composite manufacturing methods:
However, quality control for continuous fiber printing presents unique challenges. Ensuring proper fiber alignment, void-free impregnation, and consistent resin distribution are crucial for achieving high-quality printed parts 32.
AFP uses robotic systems to precisely place pre-impregnated fibers onto a mold, enabling the creation of complex shapes with optimized fiber orientations 34. This technology offers several advantages over manual layup methods:
AFP is used in various industries, including aerospace and automotive. In automotive manufacturing, AFP is used to create lightweight body panels, aerodynamic components, and structural parts 35.
Despite its advantages, AFP also has challenges:
Thermoplastic composites use thermoplastic polymers as the matrix material, offering advantages such as high impact strength, good chemical resistance, and recyclability 36. These materials provide significant weight savings compared to traditional metals, contributing to improved fuel efficiency and reduced emissions 37.
Key properties of thermoplastic composites include:
Thermoplastic composites are used in various applications, including:
Thermoplastic composites also offer environmental benefits:
Artificial intelligence (AI) is playing an increasingly important role in QA/QC for composites. AI-based vision systems can automatically inspect composite parts for defects, while AI-powered analysis tools can help identify trends and patterns in quality data 40. These tools can significantly improve the efficiency and accuracy of quality inspections, leading to better decision-making and continuous improvement.
AI-based vision tools offer several benefits:
AI-powered analysis tools can help identify trends and patterns in quality data, enabling manufacturers to:
When implementing AI-based vision and analysis tools, it is important to consider security and compliance aspects. Data privacy and security are crucial, and manufacturers should ensure that the chosen tools comply with relevant regulations and standards. Some AI platforms offer built-in security features, such as data deletion policies and compliance certifications, to address these concerns 42.
Quality assurance and quality control are essential for ensuring the production of high-quality composite parts. By understanding the challenges and considerations specific to composites manufacturing, implementing appropriate QA/QC procedures, and leveraging advanced technologies like automation, NDT methods, and AI-powered tools, manufacturers can consistently produce composite parts that meet the stringent requirements of various industries.
The growing demand for composite materials across diverse industries, from aerospace to automotive and construction, underscores the increasing importance of QA/QC. Automation and Industry 4.0 technologies play a crucial role in improving quality and efficiency in composites manufacturing. Automated systems offer increased production rates, improved consistency, enhanced quality, and real-time process monitoring. However, implementing automation also presents challenges, such as high upfront costs and the need for specialized knowledge.
Advancements in composite materials and manufacturing technologies, such as continuous fiber printing, automated fiber placement, and thermoplastic composites, are further enhancing quality and efficiency. These technologies offer unique advantages, but they also require careful consideration of quality control aspects.
AI-based vision and analysis tools have the potential to transform quality control in composites manufacturing. These tools can automate visual inspection tasks, improve accuracy, and provide valuable insights for process optimization and decision-making.
The future of composites manufacturing relies on continuous improvement and innovation in QA/QC processes. By embracing new technologies and adopting a proactive approach to quality management, manufacturers can ensure the production of high-quality, reliable, and safe composite parts that meet the evolving needs of various industries.