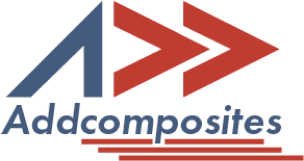
In the world of advanced manufacturing, Automated Fiber Placement (AFP) has emerged as a game-changing technology. This innovative process has revolutionized the production of high-quality, lightweight composite structures, particularly in the aerospace industry. AFP systems precisely lay down narrow strips of composite material, called tows, to create complex parts with exceptional strength-to-weight ratios.
Initially developed for flat or slightly curved geometries, AFP technology has come a long way. Today, there's a growing interest in pushing the boundaries of what's possible with AFP, particularly in manufacturing more complex, double-curved structures. This evolution is opening up new opportunities for AFP applications across various industries beyond aerospace.
However, as we strive to create increasingly intricate shapes, we face significant challenges. One of the most critical components in the AFP process is the compaction roller, which plays a crucial role in ensuring proper tape placement and preventing defects. The compaction roller applies pressure to bond the composite material to the tooling or substrate, but its effectiveness can be limited when dealing with highly curved surfaces.
Understanding these limitations and optimizing the design of compaction rollers is crucial for advancing AFP technology. That's where our latest research comes in. We've conducted an in-depth study to model the influence of compaction roller properties on manufacturable geometries, aiming to push the boundaries of what's possible with AFP.
In this blog post, we'll take you on a journey through our research, exploring how different roller parameters affect the manufacturing process and what it means for the future of composite manufacturing. Whether you're an AFP expert or new to the field, you'll gain valuable insights into the cutting-edge developments shaping the future of this transformative technology.
At the heart of any Automated Fiber Placement (AFP) system lies a crucial component: the compaction roller. These unassuming cylindrical tools play a pivotal role in ensuring the quality and integrity of composite parts produced through AFP. But what exactly do these rollers do, and why are they so important?
Compaction rollers are responsible for applying pressure to the composite material as it's laid down during the AFP process. This pressure serves several critical functions:
The design of compaction rollers isn't a one-size-fits-all affair. Different roller properties can significantly impact the layup quality and the types of geometries that can be successfully manufactured. Key parameters include:
Understanding how these parameters interact is crucial for optimizing the AFP process for different applications and geometries.
While AFP technology has come a long way, manufacturing highly complex, double-curved geometries remains a significant challenge. The limitations often stem from the compaction roller's ability (or inability) to maintain consistent pressure across the entire surface of intricate shapes.
When dealing with tight curves or rapid changes in surface geometry, traditional roller designs may struggle to maintain full contact. This can lead to issues such as:
These challenges have driven researchers and engineers to explore new approaches to compaction roller design, aiming to push the boundaries of what's possible with AFP technology.
In our study, we set out to model these limitations systematically, with the goal of understanding how different roller properties influence the range of manufacturable geometries. By gaining a deeper understanding of these relationships, we aim to pave the way for more advanced AFP systems capable of producing increasingly complex composite parts with high precision and quality.
To address the challenges of manufacturing complex geometries with AFP, our research team conducted a comprehensive study aimed at modeling the influence of compaction roller properties on manufacturable geometries. Let's dive into the details of this groundbreaking research.
The primary goal of our study was to estimate the maximum achievable curvatures for a given compaction roller. By understanding these limitations, we aimed to provide insights that could inform the design of more effective AFP systems capable of producing increasingly complex composite parts.
Specifically, we sought to:
Our study focused on four critical parameters of compaction rollers:
These parameters were chosen based on their potential influence on the roller's ability to maintain consistent contact and pressure across complex geometries.
Our experimental investigation was carefully designed to provide comprehensive data on roller behavior. Here's an overview of our approach:
A key innovation in our study was the introduction of the Displacement Pressure Coefficient (DPC). This coefficient quantifies the relationship between roller indentation and the corresponding contact pressure. The DPC allows us to predict how different roller configurations will perform on various surface curvatures, providing a powerful tool for optimizing AFP processes for complex geometries.
By systematically investigating these parameters and developing a predictive model, our study aims to provide valuable insights for AFP system design and optimization. In the next section, we'll delve into the key findings from this research and their implications for the future of AFP technology.
Our comprehensive study on compaction roller performance in Automated Fiber Placement (AFP) has yielded several significant insights. These findings not only enhance our understanding of the AFP process but also pave the way for more advanced and efficient composite manufacturing techniques.
One of the most important outcomes of our research was the introduction of the Displacement Pressure Coefficient (DPC). This novel metric quantifies the relationship between roller indentation and the corresponding contact pressure. The DPC proved to be a powerful tool for predicting roller performance across various surface curvatures.
Key observations about the DPC include:
Our analysis revealed that several roller parameters significantly influence the DPC:
These findings provide valuable insights for optimizing AFP processes and roller design.
Our study revealed several key relationships between roller parameters and the ability to manufacture complex curvatures:
These findings have significant implications for AFP system design:
These results represent a significant step forward in our understanding of AFP technology and open up new possibilities for advanced composite manufacturing. In the next section, we'll explore the practical implications of these findings and how they can be applied to improve AFP processes.
The insights gained from our study on compaction roller behavior have significant practical implications for the design and optimization of Automated Fiber Placement (AFP) systems. Let's explore how these findings can be applied to enhance AFP technology and expand its capabilities.
Our research provides valuable guidance for AFP layup head design:
The model we developed allows for precise optimization of roller parameters for specific manufacturing tasks:
Perhaps the most exciting implication of our research is the potential to manufacture more complex composite parts using AFP:
Our research also has implications for quality control in AFP processes:
By applying these insights, manufacturers can enhance the capabilities of their AFP systems, optimize processes for specific applications, and potentially unlock new possibilities in composite part design and manufacturing. As we continue to push the boundaries of what's possible with AFP technology, these findings provide a solid foundation for future innovations in the field.
While our study has provided valuable insights into the behavior of compaction rollers in Automated Fiber Placement (AFP), it also opens up exciting new avenues for further research. Let's explore some of the potential directions for future investigations and how they might shape the evolution of AFP technology.
The insights from our research have the potential to be integrated with other design and manufacturing methodologies:
The complexity of AFP technology and the breadth of potential applications call for collaborative research efforts:
As we look to the future, the potential for advancements in AFP technology is truly exciting. By building on the foundation laid by studies like ours and embracing collaborative, multidisciplinary approaches, we can push the boundaries of what's possible in composite manufacturing. The journey towards more efficient, capable, and versatile AFP systems is ongoing, and each step forward opens up new possibilities for creating lighter, stronger, and more complex composite structures.
As we conclude our deep dive into the world of Automated Fiber Placement (AFP) and compaction roller design, let's recap the key insights from our groundbreaking research and consider their implications for the future of composite manufacturing.
Our study has shed new light on the complex relationship between compaction roller properties and manufacturable geometries in AFP:
These findings provide a solid foundation for optimizing AFP processes and pushing the boundaries of what's possible in composite part design and manufacturing.
The insights gained from this study are crucial for advancing AFP technology:
As we look to the future, the potential for advancements in AFP technology and composite manufacturing is truly exciting:
The journey towards more advanced AFP technology is ongoing, and each step forward brings us closer to realizing the full potential of composite materials. Our research contributes to this journey by providing a deeper understanding of the fundamental interactions between compaction rollers and composite materials.
As we continue to push the boundaries of what's possible with AFP, we invite researchers, engineers, and manufacturers to build upon these findings. The future of composite manufacturing is bright, and together, we can shape it to create a world of stronger, lighter, and more sustainable products.
Explore more about the future of composites manufacturing
Are you ready to take your composite manufacturing to the next level? At Addcomposites, we're at the forefront of Automated Fiber Placement technology, translating cutting-edge research like the study we've discussed into practical, industry-leading solutions.
Whether you're looking to optimize your current AFP processes, explore new applications for complex geometries, or integrate the latest advancements in compaction roller technology, we're here to help. Our team of experts can guide you through the process of implementing or upgrading your AFP systems to achieve unprecedented levels of efficiency and capability.
Don't let the complexities of AFP hold you back from realizing your manufacturing potential. Contact Addcomposites today to discover how we can help you push the boundaries of what's possible in composite manufacturing.
Get in touch with Addcomposites and let's shape the future of composites together!