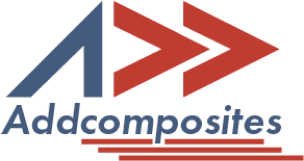
Pultrusion is a continuous manufacturing process used to produce composite materials with constant cross-sections and significantly long lengths. The term "pultrusion" is derived from the words "pull" and "extrusion," reflecting the unique nature of this process.
In pultrusion, continuous fibers are pulled through a resin bath for impregnation, then through a heated die where the resin cures, forming a solid composite profile. This process allows for the creation of high-strength, lightweight composite products with consistent quality and properties.
Learn more about composite materials
The pultrusion process has a rich history dating back to the early 1950s:
Despite these limitations, pultrusion remains a popular and efficient method for producing continuous fiber-reinforced composite profiles, particularly for applications requiring long, straight components with consistent cross-sections.
The pultrusion process is a continuous manufacturing method for producing composite materials with constant cross-sections. The process involves the following key steps:
Learn more about composite manufacturing processes
The pultrusion process relies on several essential components:
Pultrusion utilizes various materials to create high-performance composite products:
Explore different types of fiber reinforcements
Learn about thermoplastic and thermoset resins
The combination of these materials allows for the creation of pultruded products with tailored properties to meet specific application requirements.
The pultrusion process relies on several key components, each playing a crucial role in the production of high-quality composite profiles. Let's examine each component in detail:
The reinforcement dispenser is where the pultrusion process begins:
The resin impregnator ensures thorough saturation of the reinforcement with the matrix material:
Forming guides shape the resin-impregnated reinforcements:
The die is crucial for shaping and curing the composite:
The puller and clamp system draws the cured profile through the die:
The cut-off saw is the final station in the pultrusion process:
Learn more about composite manufacturing processes
Understanding these components and their operations is crucial for optimizing the pultrusion process and producing high-quality composite profiles.
The quality and performance of pultruded products largely depend on the materials used in the process. Let's examine the three main categories of materials used in pultrusion:
Reinforcements are the primary load-carrying constituents in pultruded composites:
Common types of reinforcements include:
Learn more about fiber reinforcements
The matrix material binds the reinforcements together and transfers loads between fibers:
Matrix materials are divided into two main categories:
Explore thermoplastic and thermoset resins
Fillers and additives are used to enhance specific performance aspects, reduce costs, or improve processability:
The careful selection and combination of these materials allow manufacturers to create pultruded products with tailored properties to meet specific application requirements. Understanding the characteristics and interactions of these materials is crucial for optimizing the pultrusion process and achieving desired product performance.
Discover innovations in composite materials
Optimizing the pultrusion process is crucial for producing high-quality composite profiles efficiently. This chapter explores the key process parameters, optimization techniques, and quality control measures in pultrusion.
Several parameters significantly influence the pultrusion process and product quality:
Learn more about composite manufacturing processes
Various techniques have been developed to optimize the pultrusion process:
Explore innovations in composite materials
Maintaining consistent product quality is essential in pultrusion. Key quality control measures include:
By carefully managing these process parameters, employing optimization techniques, and implementing robust quality control measures, manufacturers can ensure the production of high-quality pultruded profiles consistently and efficiently.
Pultrusion has emerged as a versatile manufacturing process, finding applications across various industrial sectors. This chapter explores the diverse applications of pultruded products and the industries that benefit from this technology.
Pultruded products have gained popularity in numerous industries due to their unique combination of properties, including high strength-to-weight ratio, corrosion resistance, and design flexibility. Key sectors include:
Explore where composites are used
Pultrusion technology allows for the production of a wide range of products. Some notable examples include:
Innovation Spotlight: Emerging Applications
Recent advancements in pultrusion technology have led to new and exciting applications:
Discover innovations in composite materials
The versatility of the pultrusion process, combined with the excellent properties of composite materials, continues to drive the adoption of pultruded products across various industries. As technology advances and new materials are developed, the range of applications for pultruded products is expected to expand further, offering innovative solutions to complex engineering challenges.
As the pultrusion industry evolves, new techniques and process variants have emerged to address specific challenges and expand the capabilities of this manufacturing method. This chapter explores some of the key innovations and variants in pultrusion technology.
Injection pultrusion (IP) is a hybrid technique that combines elements of traditional pultrusion and resin transfer molding (RTM).
Key features:
Advantages:
Challenges:
Variants:
Learn more about innovations in composite materials
Microwave pultrusion utilizes microwave energy for rapid, volumetric heating of the composite material during the pultrusion process.
Key features:
Advantages:
Challenges:
Applications:
Several other innovative pultrusion variants have been developed to address specific manufacturing needs:
Explore advanced composite manufacturing techniques
These innovations and variants in pultrusion technology continue to expand the capabilities of the process, allowing for the production of more complex, efficient, and tailored composite products. As research and development in this field progress, we can expect to see further advancements that will open up new applications and improve the overall efficiency and sustainability of composite manufacturing.
As the pultrusion industry continues to evolve, several trends and developments are shaping its future. This chapter explores emerging technologies, market outlook, and sustainability considerations that are likely to influence the pultrusion landscape in the coming years.
Explore innovations in composite materials
The pultrusion market is poised for significant growth:
Discover where composites are used
Sustainability is becoming increasingly important in the pultrusion industry:
Learn about sustainable composites manufacturing
As the pultrusion industry embraces these emerging technologies, responds to market trends, and addresses sustainability concerns, it is well-positioned for continued growth and innovation. The future of pultrusion lies in its ability to provide high-performance, cost-effective, and environmentally friendly solutions to meet the evolving needs of various industries.
Throughout this course, we've explored the pultrusion manufacturing process in detail. Let's recap the key points:
Explore fundamentals of composites manufacturing
Pultrusion plays a crucial and expanding role in the composite manufacturing landscape:
Discover innovations in composite materials
In conclusion, pultrusion stands as a critical technology in the composite manufacturing landscape. Its ability to produce high-quality, consistent profiles efficiently makes it indispensable for many applications. As the industry continues to evolve, pultrusion is likely to play an even more significant role, driven by technological advancements, market demands, and the push for more sustainable manufacturing practices. The future of pultrusion looks bright, with ongoing innovations promising to expand its capabilities and application areas even further.
We hope this comprehensive guide to pultrusion manufacturing has been informative and valuable. To further enhance your understanding of composite materials and manufacturing processes, we encourage you to:
Remember, the field of composite manufacturing is constantly evolving. By staying curious and engaged, you'll be well-positioned to leverage the full potential of technologies like pultrusion in your projects and career. We're excited to be part of your journey in the fascinating world of composite materials!