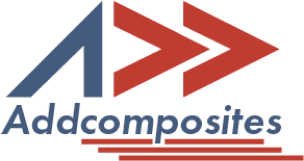
Welcome to our deep dive into the sophisticated world of composite pressure vessel design—a discipline where precision engineering meets advanced materials science to create structures of unparalleled strength and efficiency. This blog is an exploration of the core elements that constitute the optimal design of composite pressure vessels, showcasing the intricate balance between theoretical concepts and their practical applications.
In this technical narrative, we'll explore:
By the end of this blog, readers will gain insights into the meticulous considerations that go into crafting pressure vessels that are not only theoretically sound but also practically robust and economically feasible. J
In the quest for achieving the pinnacle of pressure vessel design within the composite materials industry, one must first confront the disparities between the theoretical models and the realities of fiber bundle behavior. This understanding is crucial as it sets the stage for optimizing the manufacturing process and the final structural integrity of the vessel.
When designing pressure vessels, the initial approach often involves utilizing an idealized version of fiber bundles—imaginary lines that represent the path of the fibers without considering their physical dimensions. This simplification, while useful for basic calculations, falls short when transferred into the practical realm.
In reality, a fiber bundle has a finite thickness and width, leading to a trajectory that deviates from the ideal path. The "real" fiber bundle's centerline is not perfectly tangent to the mandrel's polar openings, which introduces a complexity that must be accounted for in the design. This is where the simplified netting theory of earlier chapters gives way to a more nuanced approach, acknowledging that the roving's physical dimensions can result in overlap or gaps, potentially compromising the vessel's integrity and performance.
To address the complexities introduced by the physical attributes of real fiber bundles, the modified Clairaut equation comes into play. For geodesically wound pressure vessels, the equation takes into account the dimensionless radius and the effective polar opening, refining the winding angle distribution and adjusting the fiber path accordingly.
The equation is given by:
𝛼=arcsin(𝑣/𝑌)
Where α is the winding angle, v represents the dimensionless effective polar opening, and Y is the dimensionless radius. This adjusted formula is pivotal for predicting the modified trajectory of the fiber bundles as they are wound onto the mandrel, ensuring that the fibers align correctly during the manufacturing process.
By incorporating the physical dimensions of the fiber bundles into the design via the modified Clairaut equation, engineers can predict and compensate for the inevitable variations in fiber paths. This ensures that the structural analysis remains robust, and the design of the pressure vessel is optimized not only for theoretical strength but also for the practical realities of material behavior and production techniques.
The construction of composite pressure vessels requires meticulous attention to the transition between winding patterns. This section of the vessel's design is not merely a matter of aesthetics but a critical point that can dictate the vessel's overall structural integrity.
The complexity of constructing a cylindrical pressure vessel is compounded by the need to incorporate both polar and hoop windings. This necessity arises due to the structural demands placed on different areas of the vessel. Polar windings provide the required strength at the poles, while hoop windings reinforce the cylindrical body. The intersection of these two winding patterns is where transitional circuits become essential.
Transitioning from polar to hoop windings is not straightforward; it is a nuanced process that involves altering the winding angle gradually. This is crucial to maintain the continuity of the production process and the structural integrity of the vessel. Without transitional circuits, there would be a significant risk of weak spots where the fiber bundle is cut and reattached, which could become potential failure points under pressure.
Transitional circuits demand a departure from geodesic winding to non-geodesic winding patterns. This shift is necessary to accommodate the angle changes required for a smooth transition. The design equations provided in the chapter enable engineers to calculate the precise angles and paths necessary for these transitions.
One of the fundamental equations that guide the design of transitional circuits is:
Here, α(θ) represents the winding angle as a function of the angle θ, β is related to the initial winding angle at θc (the transition start point), μ is the coefficient of friction, and ζ is a parameter linked to the roving direction change.
Implementing these equations allows for a calculated and controlled transition, which is iterated until the winding angle reaches the desired value for hoop winding, typically π/2 radians. The process may require several runs over the cylindrical part, considering factors such as the cylinder length and available friction.
In the engineering of composite pressure vessels, there is a fine line between theoretical designs and practical applications. This delicate balance is most evident when attempting to align winding patterns with the structural requirements necessary for optimal performance.
The design of a pressure vessel is a symphony of numbers: integers that govern winding patterns must harmonize with the number of rovings determined by structural analysis. This is where design becomes a complex dance of mathematics and engineering – one cannot simply add more rovings to increase strength without considering the impact on the winding pattern, and hence, on the integrity of the vessel.
The winding pattern must satisfy the structural needs while adhering to manufacturing constraints, such as the winding machine's capabilities and the physical properties of the rovings. The chapter presents a critical equation that illustrates this balance:
Nf=2𝜋𝑎𝑞0 F b δ
Where Nf is the total number of fiber bundles passing the equator, a is a dimensionless geometric parameter, q0 is the radius of the polar opening, F is the maximum allowable tensile force of the fiber bundle, b is the width, and δ is the thickness of the fiber bundle.
The methodology for achieving the optimal design involves a delicate interplay between the mechanical properties of the fiber bundles and the pattern-related integers. The chapter outlines a process that begins with determining the required number of fiber bundles to withstand the vessel's internal pressure, then transitions to adjusting the winding pattern to meet these needs within the constraints of the fiber's tensile strength and cross-sectional dimensions.
A pivotal part of this methodology is ensuring that the product adheres to the rules of structural analysis while also matching the pattern-related integers to the number of rovings. The chapter elucidates this through a set of equations and design rules that guide the reader in finding the optimal balance:
Here, o is the fiber strength, BA denotes the dimensionless width and thickness, p is the pattern constant, Pr is the internal pressure, and a is the aforementioned dimensionless geometric parameter.
One of the most critical yet often overlooked aspects of composite pressure vessel design is the distribution of laminate thickness. This section delves into how variations in laminate thickness influence structural efficiency and the practical limitations of achieving isotensoid layering.
The laminate thickness in a pressure vessel varies due to the layering process of fibers during manufacturing. Ideally, each layer would contribute uniformly to the vessel's strength. However, the reality is that fibers tend to stack more densely at certain points, particularly near the poles, leading to a non-uniform thickness distribution. This stacking can result in regions where the stress is not optimally distributed, thereby reducing the structural efficiency of the vessel.
The chapter presents a simplified method to estimate the reduction in structural efficiency due to non-uniform thickness distribution. It introduces the concept that the layers of the laminate cannot simultaneously be isotensoid—having constant stress across the layer—due to this variation in thickness. This is articulated through an equation that relates the thickness distribution to the mechanical performance:
Here, L′(Y,v) is the derivative of the roving length with respect to the dimensionless radius Y, considering the effect of variable thickness represented by v. This equation highlights the impact of the fiber's trajectory on the mechanical performance of the vessel.
While the theory of isotensoid designs is appealing due to their efficiency in stress distribution, the practical implementation faces significant hurdles. The challenge arises from the fact that the layers, once applied, have varying thickness profiles, which leads to a non-isotensoid state. The resulting laminate has a dimension in the thickness direction where the profile is not constant, and the participating layers cannot all experience the same level of stress.
The limitations of achieving isotensoid layering in practical applications are further explained through the effect of the laminate's thickness distribution on the stress within the vessel walls:
In this equation, P(i,Y) represents the profile of the meridian after considering the thickness build-up for a collection of circuits i, and Z(Y) is the original meridian profile.
Fiber stacking in composite pressure vessels is an area where theoretical design and manufacturing realities collide. The way fiber layers stack and overlap during the winding process has profound implications on the vessel’s mechanical properties, which if ignored, can lead to designs that fall short in real-world applications.
The reinforcing layers of a pressure vessel are rarely uniform in thickness due to the fiber winding process. Ignoring this variation can lead to a miscalculation of the vessel’s strength and potentially, its failure. The fiber bundles, when wound around the vessel, tend to accumulate more densely near the poles, creating thicker regions that can alter the stress distribution across the vessel's structure.
This phenomenon is particularly crucial to consider when layers of the vessel are assumed to be isotensoid, a state that is theoretically ideal but practically challenging to achieve. The chapter discusses the importance of recognizing the thickness variation through equations that take into account the fiber stacking, such as:
This equation models the thickness build-up for every collection i of circuits, with T(i, Y) representing the thickness function and Z′(Y) being the derivative of the original meridian profile.
To ensure the performance of a pressure vessel aligns with design expectations, it's critical to integrate the realities of fiber stacking into the design considerations. This includes understanding how the stacking will affect the vessel's ability to withstand internal and external pressures and how it will behave under stress.
The design must accommodate the variations in layer thickness, which are expressed in the equations provided in the chapter. A crucial aspect of this accommodation is the calculation of the load-bearing contribution of each individual layer, factoring in the non-linear distribution along the meridian profile. The contribution is a function of the dimensionless radius Y and can be defined by:
Here, D(i,Y) is the load-bearing contribution, a(i,Y) is the axial load-bearing capacity, α(Y) is the winding angle, θ(i,Y) is the characteristic angle considering fiber stacking, ka is the axial load, and Y is the dimensionless radius.
The journey through the complexities of designing composite pressure vessels illuminates the critical role of comprehensive design analysis. It is an intricate blend of science, engineering, and mathematics, where each decision resonates through the entire structure of the vessel.
The chapters discussed underscore the necessity of a multi-faceted design approach. From considering the real geometry of fiber bundles to the meticulous calculations required for transitional circuits and the accommodation of non-uniform laminate thickness—each step is pivotal. The thorough analysis ensures that the vessels not only meet the theoretical expectations for strength and efficiency but also stand up to the practical demands of manufacturing and real-world application.
This comprehensive design analysis is more than just due diligence; it's a commitment to excellence and safety. It's about foreseeing the implications of each layer of fiber, predicting the stresses it will endure, and ensuring that the final product can withstand the pressures it was designed to contain.
As we look to the future of pressure vessel optimization in the composites industry, it's evident that innovation will be driven by advancements in both materials and manufacturing techniques. The continued development of stronger, lighter, and more durable composite materials, coupled with the precision of automated and intelligent manufacturing, holds the promise of even more efficient and reliable pressure vessels.
The methodologies and equations presented within the chapters serve as a foundation upon which this future will be built. The pursuit of the 'real' optimal design—a vessel that embodies the pinnacle of material utilization and cost-efficiency—remains the ultimate goal. This pursuit is not static but a dynamic challenge that evolves as new materials and technologies emerge
Discover the future of composite manufacturing with Addcomposites! Here's how you can get involved:
At Addcomposites, we are dedicated to revolutionizing composite manufacturing. Our AFP systems and comprehensive support services are waiting for you to harness. So, don't wait – get started on your journey to the future of manufacturing today!
Welcome to our deep dive into the sophisticated world of composite pressure vessel design—a discipline where precision engineering meets advanced materials science to create structures of unparalleled strength and efficiency. This blog is an exploration of the core elements that constitute the optimal design of composite pressure vessels, showcasing the intricate balance between theoretical concepts and their practical applications.
In this technical narrative, we'll explore:
By the end of this blog, readers will gain insights into the meticulous considerations that go into crafting pressure vessels that are not only theoretically sound but also practically robust and economically feasible. J
In the quest for achieving the pinnacle of pressure vessel design within the composite materials industry, one must first confront the disparities between the theoretical models and the realities of fiber bundle behavior. This understanding is crucial as it sets the stage for optimizing the manufacturing process and the final structural integrity of the vessel.
When designing pressure vessels, the initial approach often involves utilizing an idealized version of fiber bundles—imaginary lines that represent the path of the fibers without considering their physical dimensions. This simplification, while useful for basic calculations, falls short when transferred into the practical realm.
In reality, a fiber bundle has a finite thickness and width, leading to a trajectory that deviates from the ideal path. The "real" fiber bundle's centerline is not perfectly tangent to the mandrel's polar openings, which introduces a complexity that must be accounted for in the design. This is where the simplified netting theory of earlier chapters gives way to a more nuanced approach, acknowledging that the roving's physical dimensions can result in overlap or gaps, potentially compromising the vessel's integrity and performance.
To address the complexities introduced by the physical attributes of real fiber bundles, the modified Clairaut equation comes into play. For geodesically wound pressure vessels, the equation takes into account the dimensionless radius and the effective polar opening, refining the winding angle distribution and adjusting the fiber path accordingly.
The equation is given by:
𝛼=arcsin(𝑣/𝑌)
Where α is the winding angle, v represents the dimensionless effective polar opening, and Y is the dimensionless radius. This adjusted formula is pivotal for predicting the modified trajectory of the fiber bundles as they are wound onto the mandrel, ensuring that the fibers align correctly during the manufacturing process.
By incorporating the physical dimensions of the fiber bundles into the design via the modified Clairaut equation, engineers can predict and compensate for the inevitable variations in fiber paths. This ensures that the structural analysis remains robust, and the design of the pressure vessel is optimized not only for theoretical strength but also for the practical realities of material behavior and production techniques.
The construction of composite pressure vessels requires meticulous attention to the transition between winding patterns. This section of the vessel's design is not merely a matter of aesthetics but a critical point that can dictate the vessel's overall structural integrity.
The complexity of constructing a cylindrical pressure vessel is compounded by the need to incorporate both polar and hoop windings. This necessity arises due to the structural demands placed on different areas of the vessel. Polar windings provide the required strength at the poles, while hoop windings reinforce the cylindrical body. The intersection of these two winding patterns is where transitional circuits become essential.
Transitioning from polar to hoop windings is not straightforward; it is a nuanced process that involves altering the winding angle gradually. This is crucial to maintain the continuity of the production process and the structural integrity of the vessel. Without transitional circuits, there would be a significant risk of weak spots where the fiber bundle is cut and reattached, which could become potential failure points under pressure.
Transitional circuits demand a departure from geodesic winding to non-geodesic winding patterns. This shift is necessary to accommodate the angle changes required for a smooth transition. The design equations provided in the chapter enable engineers to calculate the precise angles and paths necessary for these transitions.
One of the fundamental equations that guide the design of transitional circuits is:
Here, α(θ) represents the winding angle as a function of the angle θ, β is related to the initial winding angle at θc (the transition start point), μ is the coefficient of friction, and ζ is a parameter linked to the roving direction change.
Implementing these equations allows for a calculated and controlled transition, which is iterated until the winding angle reaches the desired value for hoop winding, typically π/2 radians. The process may require several runs over the cylindrical part, considering factors such as the cylinder length and available friction.
In the engineering of composite pressure vessels, there is a fine line between theoretical designs and practical applications. This delicate balance is most evident when attempting to align winding patterns with the structural requirements necessary for optimal performance.
The design of a pressure vessel is a symphony of numbers: integers that govern winding patterns must harmonize with the number of rovings determined by structural analysis. This is where design becomes a complex dance of mathematics and engineering – one cannot simply add more rovings to increase strength without considering the impact on the winding pattern, and hence, on the integrity of the vessel.
The winding pattern must satisfy the structural needs while adhering to manufacturing constraints, such as the winding machine's capabilities and the physical properties of the rovings. The chapter presents a critical equation that illustrates this balance:
Nf=2𝜋𝑎𝑞0 F b δ
Where Nf is the total number of fiber bundles passing the equator, a is a dimensionless geometric parameter, q0 is the radius of the polar opening, F is the maximum allowable tensile force of the fiber bundle, b is the width, and δ is the thickness of the fiber bundle.
The methodology for achieving the optimal design involves a delicate interplay between the mechanical properties of the fiber bundles and the pattern-related integers. The chapter outlines a process that begins with determining the required number of fiber bundles to withstand the vessel's internal pressure, then transitions to adjusting the winding pattern to meet these needs within the constraints of the fiber's tensile strength and cross-sectional dimensions.
A pivotal part of this methodology is ensuring that the product adheres to the rules of structural analysis while also matching the pattern-related integers to the number of rovings. The chapter elucidates this through a set of equations and design rules that guide the reader in finding the optimal balance:
Here, o is the fiber strength, BA denotes the dimensionless width and thickness, p is the pattern constant, Pr is the internal pressure, and a is the aforementioned dimensionless geometric parameter.
One of the most critical yet often overlooked aspects of composite pressure vessel design is the distribution of laminate thickness. This section delves into how variations in laminate thickness influence structural efficiency and the practical limitations of achieving isotensoid layering.
The laminate thickness in a pressure vessel varies due to the layering process of fibers during manufacturing. Ideally, each layer would contribute uniformly to the vessel's strength. However, the reality is that fibers tend to stack more densely at certain points, particularly near the poles, leading to a non-uniform thickness distribution. This stacking can result in regions where the stress is not optimally distributed, thereby reducing the structural efficiency of the vessel.
The chapter presents a simplified method to estimate the reduction in structural efficiency due to non-uniform thickness distribution. It introduces the concept that the layers of the laminate cannot simultaneously be isotensoid—having constant stress across the layer—due to this variation in thickness. This is articulated through an equation that relates the thickness distribution to the mechanical performance:
Here, L′(Y,v) is the derivative of the roving length with respect to the dimensionless radius Y, considering the effect of variable thickness represented by v. This equation highlights the impact of the fiber's trajectory on the mechanical performance of the vessel.
While the theory of isotensoid designs is appealing due to their efficiency in stress distribution, the practical implementation faces significant hurdles. The challenge arises from the fact that the layers, once applied, have varying thickness profiles, which leads to a non-isotensoid state. The resulting laminate has a dimension in the thickness direction where the profile is not constant, and the participating layers cannot all experience the same level of stress.
The limitations of achieving isotensoid layering in practical applications are further explained through the effect of the laminate's thickness distribution on the stress within the vessel walls:
In this equation, P(i,Y) represents the profile of the meridian after considering the thickness build-up for a collection of circuits i, and Z(Y) is the original meridian profile.
Fiber stacking in composite pressure vessels is an area where theoretical design and manufacturing realities collide. The way fiber layers stack and overlap during the winding process has profound implications on the vessel’s mechanical properties, which if ignored, can lead to designs that fall short in real-world applications.
The reinforcing layers of a pressure vessel are rarely uniform in thickness due to the fiber winding process. Ignoring this variation can lead to a miscalculation of the vessel’s strength and potentially, its failure. The fiber bundles, when wound around the vessel, tend to accumulate more densely near the poles, creating thicker regions that can alter the stress distribution across the vessel's structure.
This phenomenon is particularly crucial to consider when layers of the vessel are assumed to be isotensoid, a state that is theoretically ideal but practically challenging to achieve. The chapter discusses the importance of recognizing the thickness variation through equations that take into account the fiber stacking, such as:
This equation models the thickness build-up for every collection i of circuits, with T(i, Y) representing the thickness function and Z′(Y) being the derivative of the original meridian profile.
To ensure the performance of a pressure vessel aligns with design expectations, it's critical to integrate the realities of fiber stacking into the design considerations. This includes understanding how the stacking will affect the vessel's ability to withstand internal and external pressures and how it will behave under stress.
The design must accommodate the variations in layer thickness, which are expressed in the equations provided in the chapter. A crucial aspect of this accommodation is the calculation of the load-bearing contribution of each individual layer, factoring in the non-linear distribution along the meridian profile. The contribution is a function of the dimensionless radius Y and can be defined by:
Here, D(i,Y) is the load-bearing contribution, a(i,Y) is the axial load-bearing capacity, α(Y) is the winding angle, θ(i,Y) is the characteristic angle considering fiber stacking, ka is the axial load, and Y is the dimensionless radius.
The journey through the complexities of designing composite pressure vessels illuminates the critical role of comprehensive design analysis. It is an intricate blend of science, engineering, and mathematics, where each decision resonates through the entire structure of the vessel.
The chapters discussed underscore the necessity of a multi-faceted design approach. From considering the real geometry of fiber bundles to the meticulous calculations required for transitional circuits and the accommodation of non-uniform laminate thickness—each step is pivotal. The thorough analysis ensures that the vessels not only meet the theoretical expectations for strength and efficiency but also stand up to the practical demands of manufacturing and real-world application.
This comprehensive design analysis is more than just due diligence; it's a commitment to excellence and safety. It's about foreseeing the implications of each layer of fiber, predicting the stresses it will endure, and ensuring that the final product can withstand the pressures it was designed to contain.
As we look to the future of pressure vessel optimization in the composites industry, it's evident that innovation will be driven by advancements in both materials and manufacturing techniques. The continued development of stronger, lighter, and more durable composite materials, coupled with the precision of automated and intelligent manufacturing, holds the promise of even more efficient and reliable pressure vessels.
The methodologies and equations presented within the chapters serve as a foundation upon which this future will be built. The pursuit of the 'real' optimal design—a vessel that embodies the pinnacle of material utilization and cost-efficiency—remains the ultimate goal. This pursuit is not static but a dynamic challenge that evolves as new materials and technologies emerge
Discover the future of composite manufacturing with Addcomposites! Here's how you can get involved:
At Addcomposites, we are dedicated to revolutionizing composite manufacturing. Our AFP systems and comprehensive support services are waiting for you to harness. So, don't wait – get started on your journey to the future of manufacturing today!