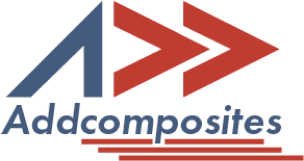
In the ever-evolving world of advanced materials, thermoplastic composites are gaining significant traction, particularly in aerospace and automotive industries. These materials offer numerous advantages, including high strength-to-weight ratios, recyclability, and the potential for rapid manufacturing. However, producing high-quality thermoplastic composite parts efficiently remains a challenge for manufacturers.
Enter Thermoplastic Automated Fiber Placement (T-AFP), a cutting-edge manufacturing process that promises to revolutionize how we create complex composite structures. But like any advanced technology, T-AFP comes with its own set of challenges. How do we balance speed and quality? How do different process parameters interact to affect the final product? And how can we achieve the desired material properties consistently?
Recent research conducted by Kilian Seefried and colleagues at the Fraunhofer Institute for Casting, Composite and Processing Technology IGCV sheds light on these questions. Their study, published in the Journal of Reinforced Plastics and Composites, delves deep into the influence of T-AFP process parameters on laminate quality, offering valuable insights for both researchers and industry professionals.
In this blog post, we'll explore the key findings of this research, unpack the complex relationships between process parameters and laminate properties, and discuss the practical implications for thermoplastic composite manufacturing. Whether you're an engineer, a materials scientist, or simply curious about the future of advanced materials, this exploration of T-AFP optimization will provide you with a deeper understanding of the challenges and opportunities in this exciting field.
In recent years, thermoplastic composites have been gaining momentum in various industries, particularly aerospace and automotive. Unlike their thermoset counterparts, thermoplastic composites offer several advantages:
These benefits have driven increased interest in developing efficient manufacturing processes for thermoplastic composite parts.
To understand the research findings, it's essential to familiarize ourselves with some key concepts:
Understanding how these process parameters influence the laminate quality indicators is crucial for optimizing the T-AFP process and producing high-quality thermoplastic composite parts efficiently.
While T-AFP offers great potential for thermoplastic composite manufacturing, it comes with several challenges:
Seefried and colleagues' research provides valuable insights into addressing these challenges:
These findings provide a roadmap for optimizing the T-AFP process, balancing production speed with laminate quality, and potentially revolutionizing thermoplastic composite manufacturing.
The research findings offer several valuable insights for industry professionals and researchers working with thermoplastic composites:
By applying these insights, manufacturers can work towards optimizing their thermoplastic composite production processes, potentially achieving higher quality parts at faster production rates.
The research by Seefried and colleagues into the optimization of the Thermoplastic Automated Fiber Placement (T-AFP) process marks a significant step forward in the field of advanced composites manufacturing. By meticulously examining the relationships between process parameters and laminate quality, this study provides valuable insights that can drive the industry towards more efficient and effective production methods.
Key findings from this research include:
These insights not only enhance our understanding of the T-AFP process but also open up new avenues for process optimization and quality control in thermoplastic composite manufacturing.
Looking to the future, this research lays a foundation for several exciting directions:
As we continue to push the boundaries of what's possible with thermoplastic composites, research like this plays a crucial role in bridging the gap between laboratory innovations and industrial applications. For engineers, materials scientists, and manufacturers working in this field, staying abreast of such developments is key to remaining competitive and driving innovation.
We encourage readers to consider how these findings might apply to their own work with thermoplastic composites. Whether you're optimizing existing processes or developing new applications, the insights from this research offer valuable guidance for achieving high-quality, efficiently produced thermoplastic composite parts.
By continually refining our understanding and implementation of advanced manufacturing processes like T-AFP, we can unlock the full potential of thermoplastic composites, paving the way for lighter, stronger, and more sustainable products across a wide range of industries.
Robotics Power displayed through Tesla Optimus Robot
Discover the future of composite manufacturing with Addcomposites! Here's how you can get involved:
At Addcomposites, we are dedicated to revolutionizing composite manufacturing. Our AFP systems and comprehensive support services are waiting for you to harness. So, don't wait – get started on your journey to the future of manufacturing today!
In the ever-evolving world of advanced materials, thermoplastic composites are gaining significant traction, particularly in aerospace and automotive industries. These materials offer numerous advantages, including high strength-to-weight ratios, recyclability, and the potential for rapid manufacturing. However, producing high-quality thermoplastic composite parts efficiently remains a challenge for manufacturers.
Enter Thermoplastic Automated Fiber Placement (T-AFP), a cutting-edge manufacturing process that promises to revolutionize how we create complex composite structures. But like any advanced technology, T-AFP comes with its own set of challenges. How do we balance speed and quality? How do different process parameters interact to affect the final product? And how can we achieve the desired material properties consistently?
Recent research conducted by Kilian Seefried and colleagues at the Fraunhofer Institute for Casting, Composite and Processing Technology IGCV sheds light on these questions. Their study, published in the Journal of Reinforced Plastics and Composites, delves deep into the influence of T-AFP process parameters on laminate quality, offering valuable insights for both researchers and industry professionals.
In this blog post, we'll explore the key findings of this research, unpack the complex relationships between process parameters and laminate properties, and discuss the practical implications for thermoplastic composite manufacturing. Whether you're an engineer, a materials scientist, or simply curious about the future of advanced materials, this exploration of T-AFP optimization will provide you with a deeper understanding of the challenges and opportunities in this exciting field.
In recent years, thermoplastic composites have been gaining momentum in various industries, particularly aerospace and automotive. Unlike their thermoset counterparts, thermoplastic composites offer several advantages:
These benefits have driven increased interest in developing efficient manufacturing processes for thermoplastic composite parts.
To understand the research findings, it's essential to familiarize ourselves with some key concepts:
Understanding how these process parameters influence the laminate quality indicators is crucial for optimizing the T-AFP process and producing high-quality thermoplastic composite parts efficiently.
While T-AFP offers great potential for thermoplastic composite manufacturing, it comes with several challenges:
Seefried and colleagues' research provides valuable insights into addressing these challenges:
These findings provide a roadmap for optimizing the T-AFP process, balancing production speed with laminate quality, and potentially revolutionizing thermoplastic composite manufacturing.
The research findings offer several valuable insights for industry professionals and researchers working with thermoplastic composites:
By applying these insights, manufacturers can work towards optimizing their thermoplastic composite production processes, potentially achieving higher quality parts at faster production rates.
The research by Seefried and colleagues into the optimization of the Thermoplastic Automated Fiber Placement (T-AFP) process marks a significant step forward in the field of advanced composites manufacturing. By meticulously examining the relationships between process parameters and laminate quality, this study provides valuable insights that can drive the industry towards more efficient and effective production methods.
Key findings from this research include:
These insights not only enhance our understanding of the T-AFP process but also open up new avenues for process optimization and quality control in thermoplastic composite manufacturing.
Looking to the future, this research lays a foundation for several exciting directions:
As we continue to push the boundaries of what's possible with thermoplastic composites, research like this plays a crucial role in bridging the gap between laboratory innovations and industrial applications. For engineers, materials scientists, and manufacturers working in this field, staying abreast of such developments is key to remaining competitive and driving innovation.
We encourage readers to consider how these findings might apply to their own work with thermoplastic composites. Whether you're optimizing existing processes or developing new applications, the insights from this research offer valuable guidance for achieving high-quality, efficiently produced thermoplastic composite parts.
By continually refining our understanding and implementation of advanced manufacturing processes like T-AFP, we can unlock the full potential of thermoplastic composites, paving the way for lighter, stronger, and more sustainable products across a wide range of industries.
Robotics Power displayed through Tesla Optimus Robot
Discover the future of composite manufacturing with Addcomposites! Here's how you can get involved:
At Addcomposites, we are dedicated to revolutionizing composite manufacturing. Our AFP systems and comprehensive support services are waiting for you to harness. So, don't wait – get started on your journey to the future of manufacturing today!