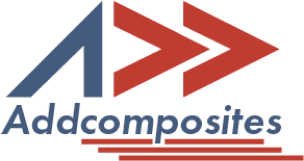
In the ever-evolving landscape of composite manufacturing, Automated Fiber Placement (AFP) and Automated Tape Laying (ATL) have emerged as revolutionary technologies for producing high-performance composite structures. These processes, characterized by their ability to sequentially add material to build complex parts, represent a significant advancement in additive manufacturing technologies for composites.
At its core, Automated Tape Laying is a sophisticated process where tracks of endless fiber-reinforced tapes are precisely laid down layer by layer to create a composite laminate. What makes this process particularly intriguing for thermoplastic matrices like PEEK (Polyether Ether Ketone) is their unique ability to undergo rapid, reversible phase transitions from solid to liquid states. During the ATL process, this characteristic enables the creation of cohesive bonds through polymer chain diffusion and entanglement between layers.
Despite the significant potential of ATL technology, achieving optimal material properties while maintaining production efficiency remains a complex challenge. The industry has consistently faced two critical questions:
The complexity of composites manufacturing means that finding the right balance between these factors is crucial for producing parts that meet stringent quality requirements while maintaining economic viability.
When it comes to automated tape laying, placement rate isn't just about how quickly we can produce parts - it's about finding the sweet spot between productivity and quality. In our investigation, we examined three distinct placement rates:
These speeds represent a significant range in production capability, from careful, controlled placement to high-speed manufacturing scenarios. Each rate brings its own set of challenges and benefits, particularly when it comes to material consolidation and void formation.
Temperature control in composite manufacturing plays a crucial role in determining final part properties. Our study focused on two specific temperature conditions:
The selection of 250°C as our heated tooling temperature wasn't arbitrary - it represents a carefully chosen point between the melting and glass transition temperatures of PEEK, where isothermal crystallization becomes possible. This temperature selection has significant implications for both processing efficiency and final material properties.
Both placement rate and tooling temperature work in concert to influence critical material properties such as void content, crystallinity, and mechanical performance. Understanding these relationships is key to optimizing the ATL process for specific applications and requirements.
Understanding defects and damage in composite materials is crucial for producing high-quality parts. Our investigation revealed fascinating relationships between processing parameters and void formation that have significant implications for manufacturers.
Our findings revealed a clear correlation between placement rate and void content:
Temperature control in composite processing showed interesting effects on void formation:
The degree of crystallinity in thermoplastic composites plays a crucial role in determining final part properties. Our research uncovered several key insights:
For reference, post-consolidated specimens achieved:
Understanding these crystallization mechanisms is crucial for optimizing the ATL process. The rapid cooling inherent in ATL creates a unique crystallization environment, different from traditional processing methods:
These findings demonstrate the complex interplay between processing parameters and final material structure, highlighting the importance of careful parameter selection in achieving desired material properties.
Advanced composites manufacturing requires careful attention to mechanical properties. Our investigation revealed interesting patterns across different mechanical tests, providing valuable insights for manufacturers.
The compression shear test results revealed critical insights into layer bonding quality:
Fiber direction strength showed interesting trends:
The material stiffness showed more stability across processing conditions:
These results highlight the complexity of composites design for automated production, where different mechanical properties respond differently to processing parameters. Understanding these relationships is crucial for optimizing the manufacturing process for specific application requirements.
The investigation of post-processing through out-of-autoclave consolidation revealed significant insights for manufacturers looking to optimize their composite production processes.
Understanding the composite manufacturing process becomes particularly important when considering post-processing options. Our findings showed:
The shift in composite manufacturing from traditional to intelligent processes requires careful consideration of various processing parameters. Our research provides several key takeaways for manufacturers:
Understanding temperature effects in automated fiber placement leads to these practical recommendations:
For manufacturers looking to implement or optimize their ATL processes, consider:
These findings suggest that manufacturers should carefully evaluate their specific requirements and constraints when selecting processing parameters. The choice between direct ATL processing and post-consolidation depends on various factors including:
Our comprehensive investigation into ATL processing parameters has revealed crucial insights for the future of composite manufacturing. The evolution of automated fiber placement continues to present both challenges and opportunities.
The future of composites manufacturing will likely focus on:
The success of ATL processing depends on understanding and controlling the complex relationships between processing parameters and final part properties. While challenges exist, particularly in achieving high production rates while maintaining quality, the potential for optimization and improvement remains significant. Manufacturers must carefully consider their specific requirements and constraints when selecting processing parameters, whether opting for direct ATL processing or including post-consolidation steps.
For more information on advanced composite manufacturing techniques and optimization strategies, explore our related resources on composites design for automated production and advanced material selection.
This blog post is based on the research paper:
Backmann, V., Adil, M., Wettemann, T., & Drechsler, K. (2024). Laser-assisted automated tape laying: Effects of placement rate and heated tooling on layer bonding and tensile properties. Journal of Thermoplastic Composite Materials, 0(0), 1-22. DOI: 10.1177/08927057241290469
Are you looking to optimize your composite manufacturing processes? Addcomposites offers cutting-edge solutions for automated fiber placement and tape laying applications.
Contact our team of experts to discuss how we can help optimize your composite manufacturing operations:
Join the growing community of manufacturers who are revolutionizing their composite production with Addcomposites' advanced automation solutions.
Stay updated with the latest in composite manufacturing technology - follow us on LinkedIn and subscribe to our newsletter for regular insights and updates.