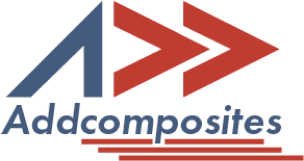
In the rapidly evolving world of advanced manufacturing, a groundbreaking technology is set to transform the landscape of composite production: non-planar slicing with continuous fiber reinforcement. This innovative approach is poised to overcome the limitations of traditional 3D printing methods, opening up new possibilities for creating high-performance, lightweight structures across various industries.
Conventional 3D printing techniques, which rely on planar slicing, have long been the standard in additive manufacturing. However, when it comes to continuous fiber-reinforced composites, these methods fall short. Planar slicing often results in:
These limitations have hindered the full potential of 3D printing in composite manufacturing, particularly for complex geometries and parts subject to multidirectional stresses (Nayyeri et al., 2022).
Non-planar slicing represents a paradigm shift in additive manufacturing, especially for continuous fiber reinforcement. This advanced technique allows for:
While the potential of non-planar slicing is immense, its implementation has been challenging due to the need for specialized hardware and complex software solutions. This is where AddPrint, developed by Addcomposites, comes into play.
AddPrint bridges the gap between cutting-edge research and practical application, offering a user-friendly solution that makes non-planar slicing accessible to a wider range of users. Key features include:
Non-planar slicing with continuous fiber reinforcement is set to revolutionize composite manufacturing. From aerospace and automotive industries to renewable energy and beyond, this technology promises to deliver:
As we stand on the brink of this manufacturing revolution, tools like AddPrint are paving the way for widespread adoption of non-planar slicing techniques. By making this advanced technology accessible and user-friendly, Addcomposites is empowering engineers, designers, and manufacturers to push the boundaries of what's possible in composite production.
Experience the future of composite manufacturing firsthand by trying AddPrint today. Visit www.addcomposites.com to start your free trial and unlock the potential of non-planar slicing for your projects.
Bhatt, R., Mandil, G., & Anand, S. (2018). Computer-Aided Design and Applications. Fang, G., et al. (2024). Additive Manufacturing. Li, Y., et al. (2021). Computer-Aided Design. Nayyeri, P., Zareinia, K., & Bougherara, H. (2022). The International Journal of Advanced Manufacturing Technology. Yao, Y., et al. (2021). Applied Sciences.