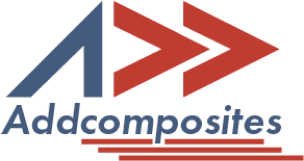
Fiber-reinforced composite materials have revolutionized various industries, particularly aerospace, renewable energy, civil engineering, marine, and automotive sectors. These advanced materials offer a unique combination of properties, including high strength-to-weight ratios, corrosion resistance, and the ability to be tailored for specific applications. As the use of composites continues to grow, so does the need for effective inspection and quality control methods.
Fiber-reinforced composites typically consist of two main components:
The combination of these materials results in a composite with properties superior to those of its individual components. Some key advantages of fiber-reinforced composites include:
For a more comprehensive understanding of composite materials, you can refer to our Introduction to Composite Materials guide.
Given the critical applications of fiber-reinforced composites in industries like aerospace and automotive, ensuring the integrity and quality of these materials is paramount. Non-destructive testing (NDT) plays a crucial role in:
NDT methods allow for the inspection of composites without causing damage, enabling the detection of defects, damage, or material degradation that could compromise the performance or safety of the composite structure. To learn more about common defects in composites, check out our article on Defects and Damage in Composite Materials and Structures.
In this comprehensive guide, we will explore the various non-destructive testing methods used for inspecting fiber-reinforced composite materials, their principles, applications, and relative advantages and limitations. Whether you're involved in composite manufacturing, quality control, or research and development, understanding these NDT techniques is essential for ensuring the reliability and performance of composite structures.
Non-destructive testing (NDT) plays a crucial role in ensuring the quality, safety, and performance of fiber-reinforced composite materials throughout their lifecycle. This section provides an overview of NDT and its importance in the context of composite materials.
Non-destructive testing refers to a wide range of analytical techniques used to evaluate the properties of a material, component, or system without causing damage. The main principle behind NDT is to inspect and gather information about a material's condition without altering its ability to fulfill its intended function.
Key principles of NDT include:
For a deeper understanding of composite manufacturing processes that benefit from NDT, you can explore our Fundamentals of Composites Manufacturing guide.
NDT is particularly important for fiber-reinforced composites due to several factors:
To understand the various applications of composites and why their inspection is crucial, check out our article on Where Are Composites Used.
Several NDT methods are commonly used for inspecting fiber-reinforced composites:
Each method has its strengths and limitations, and the choice of technique often depends on the specific application, type of composite, and nature of potential defects. We'll explore each of these methods in detail in the following sections.
Inspecting composites presents unique challenges compared to traditional materials:
For more information on the challenges of working with composites, including inspection difficulties, see our article on Challenges of Switching to Composite Materials.
Understanding these challenges is crucial for selecting and implementing effective NDT strategies for composite materials. In the following sections, we'll delve into each NDT method, exploring how they address these challenges and their specific applications in composite inspection.
Visual Testing (VT) is one of the most fundamental and widely used non-destructive testing methods for fiber-reinforced composite materials. This section will explore the principles, equipment, applications, and limitations of visual testing.
Visual Testing is a non-destructive evaluation technique that relies on the use of the human eye, often aided by various tools and technologies, to inspect the surface or interior of composite materials. Key points include:
The effectiveness of VT depends on several factors:
For more information on how visual inspection fits into the overall composite manufacturing process, see our guide on What Are the Fundamental Steps of Composites Manufacturing.
VT can be enhanced with various tools and technologies:
VT is used throughout the lifecycle of composite materials:
To understand how visual inspection is applied in specific manufacturing processes, check out our article on Filament Winding, where visual inspection plays a crucial role in quality control.
Advantages of VT:
Limitations of VT:
For a comparison of VT with other NDT methods, see our comprehensive guide on Non-Destructive Testing for Composites: Different Inspection Methods.
Various organizations provide standards and guidelines for VT:
The future of VT in composite inspection is likely to include:
For insights into how AI and automation are shaping the future of composite manufacturing and inspection, read our article on The Shift in Composite Manufacturing from Traditional to Intelligent.
Visual Testing remains a critical tool in the NDT arsenal for composite materials, offering a cost-effective and versatile method for initial inspections and complementing other more advanced techniques. As the composite industry continues to evolve, VT will likely see further enhancements in technology and methodology to meet the growing demands for quality and reliability in composite structures.
Ultrasonic Testing (UT) is one of the most widely used and effective non-destructive testing methods for fiber-reinforced composite materials. This section will explore the principles, equipment, applications, and limitations of ultrasonic testing.
Ultrasonic testing uses high-frequency sound waves to detect and characterize flaws in composite materials. Key points include:
For a broader understanding of how UT fits into the composite manufacturing process, see our guide on Fundamentals of Composites Manufacturing.
The effectiveness of UT depends on several factors:
UT systems for composites typically include:
UT is used throughout the lifecycle of composite materials:
To understand how UT is applied in specific industries, check out our article on Applications and Limitations of Composite Materials in Aerospace Engineering.
Several advanced UT techniques are used for composite inspection:
Advanced signal processing and imaging techniques enhance UT capabilities:
For insights into how advanced signal processing is shaping the future of composite manufacturing and inspection, read our article on The Shift in Composite Manufacturing from Traditional to Intelligent.
While UT is highly effective, it faces some challenges in composite inspection:
To understand more about the challenges in composite manufacturing and inspection, see our post on Challenges of Switching to Composite Materials.
The future of UT for composites is likely to include:
For a glimpse into the future of automated composite inspection, check out our article on Process Monitoring AI for AFP Composites Manufacturing.
Ultrasonic Testing remains a critical tool in the NDT arsenal for composite materials, offering high sensitivity to internal defects and the ability to inspect thick and complex structures. Ongoing research and development continue to enhance its capabilities and overcome existing limitations, making it an invaluable technique for ensuring the quality and reliability of composite structures.
Infrared Thermography Testing (IRT) is a powerful and versatile non-destructive testing method for fiber-reinforced composite materials. This section will explore the principles, equipment, applications, and limitations of infrared thermography testing.
Infrared thermography is a non-contact inspection technique that uses infrared radiation to detect and characterize defects in composite materials. Key points include:
To understand how IRT fits into the broader context of composite manufacturing and inspection, see our guide on What Are the Fundamental Steps of Composites Manufacturing.
The effectiveness of IRT depends on several factors:
IRT systems for composites typically include:
IRT is used throughout the lifecycle of composite materials:
For insights into specific applications of IRT in the aerospace industry, check out our article on The Composite Sky: Advanced Materials Defining Modern Aerospace.
Several advanced IRT techniques are used for composite inspection:
Advanced signal processing and image analysis techniques enhance IRT capabilities:
To learn more about advanced signal processing in composite manufacturing and inspection, see our post on Process Monitoring AI for AFP Composites Manufacturing.
While IRT is highly effective, it faces some challenges in composite inspection:
For more information on the challenges in composite manufacturing and inspection, refer to our article on Challenges of Switching to Composite Materials.
The future of IRT for composites is likely to include:
To explore how AI and automation are shaping the future of composite manufacturing and inspection, read our article on The Shift in Composite Manufacturing from Traditional to Intelligent.
Infrared Thermography Testing remains a critical tool in the NDT arsenal for composite materials, offering rapid, non-contact inspection capabilities and the ability to detect a wide range of defects. As the composite industry continues to evolve, IRT will likely see further enhancements in technology and methodology to meet the growing demands for quality and reliability in composite structures.
Terahertz (THz) testing has emerged as a promising non-destructive testing method for fiber-reinforced composite materials. This section will explore the principles, equipment, applications, and future prospects of terahertz testing in composite inspection.
Terahertz radiation occupies the electromagnetic spectrum between microwaves and infrared light, with frequencies ranging from 0.1 to 10 THz. Key points include:
Recent advancements in photonics, semiconductors, and ultrafast electronics have enabled the development of more practical and efficient THz systems for industrial applications.
For a broader understanding of how THz testing fits into the composite manufacturing process, see our guide on Fundamentals of Composites Manufacturing.
Two main types of THz systems are used for composite inspection:
THz imaging can be performed in transmission, reflection, or scatter configurations. Key aspects include:
To understand how advanced imaging techniques are applied in composite manufacturing, check out our article on Virtual Composite Manufacturing Simulation.
THz Imaging
THz Spectroscopy
Online Process Monitoring
For insights into online process monitoring in composite manufacturing, see our post on Process Monitoring AI for AFP Composites Manufacturing.
Off-Line NDT Inspection
To learn more about defects and damage in composites, refer to our article on Defects and Damage in Composite Materials and Structures.
Advantages:
Limitations:
The future of THz testing for composites is promising, with potential developments including:
For a glimpse into the future of composite manufacturing and inspection technologies, read our article on The Shift in Composite Manufacturing from Traditional to Intelligent.
Terahertz testing offers significant potential for the non-destructive evaluation of fiber-reinforced composites. As research and development continue to address current limitations, THz testing is likely to become an increasingly valuable tool in the NDT arsenal for composite materials, complementing existing techniques and opening new possibilities for defect detection and material characterization.
Acoustic Emission (AE) testing has emerged as a valuable non-destructive testing technique for fiber-reinforced composite materials. This section explores the principles, applications, and advantages of AE in composite inspection.
Acoustic Emission refers to the phenomenon where materials release elastic energy in the form of stress waves when subjected to deformation or damage. In NDT, AE involves:
For a broader understanding of how AE fits into the composite manufacturing process, see our guide on Fundamentals of Composites Manufacturing.
The AE process in composite inspection typically involves:
AE testing systems for composites typically include:
AE has found applications in various industries using composite materials:
To understand how AE is applied in specific industries, check out our article on Applications and Limitations of Composite Materials in Aerospace Engineering.
AE signal analysis involves several key parameters:
Advanced signal processing techniques, including pattern recognition and neural networks, are often employed to interpret AE data. For insights into how AI and machine learning are shaping composite manufacturing and inspection, read our article on Machine Learning to Optimize AFP Composite Production.
While powerful, AE also faces some challenges:
To understand more about the challenges in composite manufacturing and inspection, see our post on Challenges of Switching to Composite Materials.
The field of AE for composite inspection is evolving:
For a glimpse into the future of automated composite inspection, check out our article on Process Monitoring AI for AFP Composites Manufacturing.
Acoustic Emission testing offers a unique and powerful approach to inspecting fiber-reinforced composites. As the technology continues to advance, it's likely to play an increasingly important role in ensuring the safety and reliability of composite structures across various industries. The real-time monitoring capabilities of AE make it particularly valuable for in-service inspection and structural health monitoring applications.
While Visual, Ultrasonic, Infrared Thermography, Terahertz, and Acoustic Emission testing are widely used for composite inspection, several other non-destructive testing methods can provide valuable insights into the condition of composite materials. This section explores additional NDT techniques applicable to fiber-reinforced composites.
Radiographic testing uses various types of radiation to inspect the interior of composite structures:
For more information on advanced imaging techniques in composites, see our article on Material Analysis with X-ray Scattering Tensor Tomography.
Shearography is an optical interferometric technique that can detect surface and subsurface defects:
To understand how shearography fits into the broader context of composite inspection, check out our guide on Non-Destructive Testing for Composites: Different Inspection Methods.
While primarily used for conductive materials, eddy current testing can be applied to carbon fiber reinforced polymers (CFRPs):
These techniques use electromagnetic waves to inspect dielectric materials like glass fiber reinforced polymers (GFRPs):
Several laser-based NDT techniques are used for composite inspection:
For insights into how laser technology is advancing composite manufacturing, read our article on Innovations in Automated Fiber Deposition for Aerospace Applications.
These techniques analyze changes in a structure's dynamic properties to detect damage:
For conductive composites like CFRPs, electrical resistance measurement can be used:
To learn more about mechanical testing of composites, see our post on Mechanical Testing of Composites.
When selecting an NDT method for composite inspection, consider:
Different NDT methods may be combined for a more comprehensive evaluation of composite structures. For example, visual inspection might be used for initial screening, followed by ultrasonic testing for detailed internal inspection and infrared thermography for large area scanning.
The field of NDT for composites continues to evolve:
For a glimpse into the future of composite manufacturing and inspection, check out our article on The Shift in Composite Manufacturing from Traditional to Intelligent.
As composite materials continue to find new applications across various industries, the development and refinement of NDT methods will play a crucial role in ensuring the quality, safety, and longevity of composite structures. The selection of appropriate NDT techniques and their effective implementation will remain key to the successful utilization of composite materials in demanding applications.
As the use of fiber-reinforced composites continues to grow across various industries, so does the need for effective non-destructive testing (NDT) methods. This section summarizes the current state of NDT for composite materials and explores future prospects in this rapidly evolving field.
For a comprehensive understanding of the challenges in composite manufacturing and inspection, see our post on Challenges of Switching to Composite Materials.
To learn more about how AI is shaping composite manufacturing and inspection, check out our article on Machine Learning to Optimize AFP Composite Production.
For insights into the future of composite manufacturing, including NDT advancements, read our article on The Shift in Composite Manufacturing from Traditional to Intelligent.
To understand how these challenges are being addressed in specific applications, see our article on Optimal Design for Composite High Pressure Hydrogen Storage Tank.
The principles of Industry 4.0, including digitalization, interconnectivity, and smart manufacturing, are set to transform NDT for composites:
For more information on how Industry 4.0 concepts are being applied to composite manufacturing, check out our post on Hybrid Manufacturing Cells: Complete Digitization of Production.
As the field of NDT for fiber-reinforced composites continues to evolve, addressing these challenges and capitalizing on emerging technologies will be crucial for ensuring the safety, reliability, and longevity of composite structures across various industries. The future of NDT in composites is bright, with ongoing research and development promising more accurate, efficient, and comprehensive inspection methods.
W. Nsengiyumva, S. Zhong, M. Luo, Q. Zhang, J. Lin, Critical insights into the state-of-the-art NDE data fusion techniques for the inspection of structural systems. Struct. Control Health Monit. (2021). https://doi.org/10.1002/stc.2857