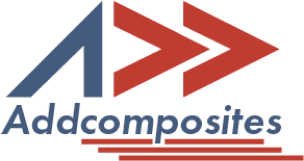
The blog article is a summary of the work "Analysis of New Concepts for the Consolidation Roller in Laser-Assisted Automated Tape Placement Processes" by wonderful authors Nils Widmaier and Lukas Raps.
The work aimed to find new concepts for compaction roller designs to enable the use of the laser-assisted thermoplastic in-situ tape placement process on curved surfaces. Both experimental and simulative methods were used to explore new concepts of compaction rollers to improve adaptability to curved surfaces, pressure uniformity, and compaction pressure.
The present consolidation rollers have several issues, particularly when dealing with complex part geometries and curved surfaces. Here are the main problems:
The author, Nils Widmaier, approaches the problem of current consolidation rollers by investigating new concepts for the consolidation roller to enable the successful use of in-situ placement technologies on complex part geometries. Here's a summary of the approach:
The article addresses the challenges faced by current consolidation rollers used in the production of fiber composite materials. The main issues include pressure uniformity, adaptability to complex geometries, misalignment, material limitations, and pressure variations. These problems become particularly pronounced when dealing with curved surfaces.
To tackle these issues, the author employs a combination of experimental and simulative methods. Different sheath thicknesses and materials are investigated experimentally, while a Finite Element Method (FEM) model is set up to replicate the deformation behavior of the silicone roller and explore more complex, perforated compaction roller geometries. The simulation model is then validated against analytical calculations.
The study concludes that the best compromise for the counteracting mechanisms of higher compaction force at the expense of lower pressure uniformity can be achieved with a solid 10 mm Shore A60 (SS960) silicone sheath. However, compaction roller designs that deviate from a pure solid material sheath are not recommended due to the significant reduction in compaction pressure.
Discover the future of composite manufacturing with Addcomposites! Here's how you can get involved:
At Addcomposites, we are dedicated to revolutionizing composite manufacturing. Our AFP systems and comprehensive support services are waiting for you to harness. So, don't wait – get started on your journey to the future of manufacturing today!
The blog article is a summary of the work "Analysis of New Concepts for the Consolidation Roller in Laser-Assisted Automated Tape Placement Processes" by wonderful authors Nils Widmaier and Lukas Raps.
The work aimed to find new concepts for compaction roller designs to enable the use of the laser-assisted thermoplastic in-situ tape placement process on curved surfaces. Both experimental and simulative methods were used to explore new concepts of compaction rollers to improve adaptability to curved surfaces, pressure uniformity, and compaction pressure.
The present consolidation rollers have several issues, particularly when dealing with complex part geometries and curved surfaces. Here are the main problems:
The author, Nils Widmaier, approaches the problem of current consolidation rollers by investigating new concepts for the consolidation roller to enable the successful use of in-situ placement technologies on complex part geometries. Here's a summary of the approach:
The article addresses the challenges faced by current consolidation rollers used in the production of fiber composite materials. The main issues include pressure uniformity, adaptability to complex geometries, misalignment, material limitations, and pressure variations. These problems become particularly pronounced when dealing with curved surfaces.
To tackle these issues, the author employs a combination of experimental and simulative methods. Different sheath thicknesses and materials are investigated experimentally, while a Finite Element Method (FEM) model is set up to replicate the deformation behavior of the silicone roller and explore more complex, perforated compaction roller geometries. The simulation model is then validated against analytical calculations.
The study concludes that the best compromise for the counteracting mechanisms of higher compaction force at the expense of lower pressure uniformity can be achieved with a solid 10 mm Shore A60 (SS960) silicone sheath. However, compaction roller designs that deviate from a pure solid material sheath are not recommended due to the significant reduction in compaction pressure.
Discover the future of composite manufacturing with Addcomposites! Here's how you can get involved:
At Addcomposites, we are dedicated to revolutionizing composite manufacturing. Our AFP systems and comprehensive support services are waiting for you to harness. So, don't wait – get started on your journey to the future of manufacturing today!