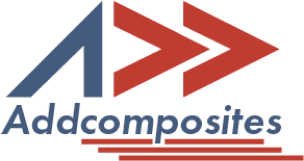
Over the past decades, composites have emerged as the material of choice for the aerospace industry, driven by their significant advantages over traditional materials. The global composite market, valued at USD 23.8 billion in 2020, is projected to grow to USD 41.4 billion by 2025, at a compound annual growth rate of 11.7%. This growth is largely attributed to the increased utilization of advanced lightweight composite materials, such as carbon fiber reinforced plastic (CFRP), in aero structure components of commercial aircraft programs. Composites offer promising weight reduction—up to 50%—tailor-made design capabilities, high impact resistance, high damage tolerance, and the ability to avoid galvanic corrosion problems unlike metals.
The aerospace sector's growing demand has been met with a significant uptake in composite materials for aerospace applications, as evident in recent years. However, to meet future demands, experts from academia and industry agree that the level of automation in aerospace composite manufacturing process chains needs improvement. The focus so far has been on automating siloed operations, with limited attention to end-to-end integration of process chains. This lack of integration leads to inefficiencies, rising operational costs, and low productivity.
Airbus's Global Market Forecast for 2019–2038 highlights the addition of more than 39,000 new aircraft to meet demand and replace over 14,000 from existing fleets. With the number of composite parts in aircraft increasing rapidly, the transition from nest production to production-line manufacturing demands automated mass production. Holmes identified composites as a critical area for increasing overall aircraft manufacturing throughput.
Despite these challenges, traditional manufacturing techniques still widely used in aerospace composites are labor-oriented, time-consuming, or costly, and full automation in composite manufacturing has not been realized. The literature focuses on specific technologies like Automated Fiber Placement (AFP) and Automated Tape Layup (ATL), but there's a limited focus on ramping up automation across the entire process chain with novel digital technologies.Pain Points in Traditional Composite Manufacturing
Traditional composite manufacturing in the aerospace industry faces several critical challenges that hinder its efficiency and scalability. These challenges are deeply rooted in the manual labor-intensive processes, issues with quality consistency, scalability of production, and environmental concerns. This section explores these pain points in detail, using information derived from the document on aerospace composite manufacturing automation.
Advancing Automation in Aerospace Composites
The aerospace industry is on the cusp of a significant transformation, driven by the need for increased automation in composite manufacturing processes. This shift is crucial for meeting the rising demand for composite materials, characterized by their lightweight and strength, which are increasingly used in aircraft construction. The research methodology adopted to explore this transformation includes a pre-study, task categorization, and automation level assessment, aiming to understand how automation can be leveraged effectively.
Automated Solutions Transforming Aerospace
The transition towards fully automated aerospace composite manufacturing processes is a complex journey marked by the integration of various advanced technologies. This section delves into detailed findings on automated manufacturing technologies such as Autoclave Molding, Filament Winding, Automated Tape Layup (ATL), Automated Fiber Placement (AFP), Resin Transfer Molding (RTM), and Pultrusion, illustrating how they address traditional manufacturing challenges.
ReferencesWe extend our heartfelt thanks to Deepesh Jayasekara, Nai Yeen Gavin Lai, Kok-Hoong Wong, Kulwant Pawar, and Yingdan Zhu for their invaluable contributions to the field of aerospace composite manufacturing. Their research and findings have significantly enhanced our understanding and have been instrumental in crafting this blog post. Their dedication to advancing automation in aerospace composites is truly appreciated and deserves recognition.
What's Next!
Discover the future of composite manufacturing with Addcomposites! Here's how you can get involved:
At Addcomposites, we are dedicated to revolutionizing composite manufacturing. Our AFP systems and comprehensive support services are waiting for you to harness. So, don't wait – get started on your journey to the future of manufacturing today!
Over the past decades, composites have emerged as the material of choice for the aerospace industry, driven by their significant advantages over traditional materials. The global composite market, valued at USD 23.8 billion in 2020, is projected to grow to USD 41.4 billion by 2025, at a compound annual growth rate of 11.7%. This growth is largely attributed to the increased utilization of advanced lightweight composite materials, such as carbon fiber reinforced plastic (CFRP), in aero structure components of commercial aircraft programs. Composites offer promising weight reduction—up to 50%—tailor-made design capabilities, high impact resistance, high damage tolerance, and the ability to avoid galvanic corrosion problems unlike metals.
The aerospace sector's growing demand has been met with a significant uptake in composite materials for aerospace applications, as evident in recent years. However, to meet future demands, experts from academia and industry agree that the level of automation in aerospace composite manufacturing process chains needs improvement. The focus so far has been on automating siloed operations, with limited attention to end-to-end integration of process chains. This lack of integration leads to inefficiencies, rising operational costs, and low productivity.
Airbus's Global Market Forecast for 2019–2038 highlights the addition of more than 39,000 new aircraft to meet demand and replace over 14,000 from existing fleets. With the number of composite parts in aircraft increasing rapidly, the transition from nest production to production-line manufacturing demands automated mass production. Holmes identified composites as a critical area for increasing overall aircraft manufacturing throughput.
Despite these challenges, traditional manufacturing techniques still widely used in aerospace composites are labor-oriented, time-consuming, or costly, and full automation in composite manufacturing has not been realized. The literature focuses on specific technologies like Automated Fiber Placement (AFP) and Automated Tape Layup (ATL), but there's a limited focus on ramping up automation across the entire process chain with novel digital technologies.Pain Points in Traditional Composite Manufacturing
Traditional composite manufacturing in the aerospace industry faces several critical challenges that hinder its efficiency and scalability. These challenges are deeply rooted in the manual labor-intensive processes, issues with quality consistency, scalability of production, and environmental concerns. This section explores these pain points in detail, using information derived from the document on aerospace composite manufacturing automation.
Advancing Automation in Aerospace Composites
The aerospace industry is on the cusp of a significant transformation, driven by the need for increased automation in composite manufacturing processes. This shift is crucial for meeting the rising demand for composite materials, characterized by their lightweight and strength, which are increasingly used in aircraft construction. The research methodology adopted to explore this transformation includes a pre-study, task categorization, and automation level assessment, aiming to understand how automation can be leveraged effectively.
Automated Solutions Transforming Aerospace
The transition towards fully automated aerospace composite manufacturing processes is a complex journey marked by the integration of various advanced technologies. This section delves into detailed findings on automated manufacturing technologies such as Autoclave Molding, Filament Winding, Automated Tape Layup (ATL), Automated Fiber Placement (AFP), Resin Transfer Molding (RTM), and Pultrusion, illustrating how they address traditional manufacturing challenges.
ReferencesWe extend our heartfelt thanks to Deepesh Jayasekara, Nai Yeen Gavin Lai, Kok-Hoong Wong, Kulwant Pawar, and Yingdan Zhu for their invaluable contributions to the field of aerospace composite manufacturing. Their research and findings have significantly enhanced our understanding and have been instrumental in crafting this blog post. Their dedication to advancing automation in aerospace composites is truly appreciated and deserves recognition.
What's Next!
Discover the future of composite manufacturing with Addcomposites! Here's how you can get involved:
At Addcomposites, we are dedicated to revolutionizing composite manufacturing. Our AFP systems and comprehensive support services are waiting for you to harness. So, don't wait – get started on your journey to the future of manufacturing today!