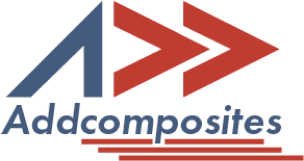
In the high-stakes world of aerospace engineering, the manufacturing process of composite materials is often shrouded in strict environmental controls. Temperature and humidity are watched with hawk-like precision, under the assumption that even slight variations could compromise the integrity of the final product. But what if these stringent controls aren't always necessary? A recent NASA study on T1100/3960 carbon fiber/epoxy prepreg challenges this conventional wisdom, potentially revolutionizing how we approach composite manufacturing.
The study, conducted by researchers at NASA's Marshall Space Flight Center, delves into the effects of temperature and relative humidity on T1100/3960 carbon fiber/epoxy prepreg during the critical period before layup and curing. This material, known for its high performance in aerospace applications, has been put under the microscope to determine just how sensitive it really is to environmental fluctuations.
Why does this matter? In the aerospace industry, where safety and performance are paramount, understanding the true environmental sensitivity of materials can lead to more efficient manufacturing processes, potential cost savings, and ultimately, better end products. But the implications stretch beyond aerospace - any industry utilizing high-performance composites could benefit from these insights.
To fully appreciate the significance of NASA's study, it's crucial to understand the context of environmental sensitivity in composite materials and some key concepts related to their manufacturing.
Composite materials, particularly those used in aerospace applications, have long been thought to be highly sensitive to environmental conditions during the manufacturing process. This sensitivity stems from the nature of the materials themselves. Composites typically consist of strong fibers (like carbon) embedded in a polymer matrix (often epoxy). The epoxy component, being hygroscopic, can absorb moisture from the air, potentially leading to changes in its chemical structure and physical properties.
Traditionally, it's been believed that exposure to high humidity or temperature fluctuations during the pre-cure stages could lead to moisture absorption in the epoxy, potentially causing:
As a result, composite manufacturing facilities often implement strict environmental controls, maintaining specific temperature and humidity levels. However, these controls can be costly and energy-intensive, making the manufacturing process more complex and expensive.
This is where the NASA study comes in, challenging these long-held assumptions by investigating how T1100/3960 carbon fiber/epoxy prepreg actually responds to varying environmental conditions before curing.
In the world of high-performance composites, particularly in aerospace applications, manufacturers have long grappled with a significant challenge: how to maintain optimal environmental conditions during the pre-cure stages of composite production. The concern stems from the potential negative effects of temperature fluctuations and humidity exposure on uncured prepreg materials.
The specific problems this creates include:
The core of the problem lies in the balance between ensuring product quality and optimizing manufacturing efficiency. If prepreg materials are indeed highly sensitive to environmental conditions, then strict controls are necessary to maintain product integrity. However, if they are more robust than previously thought, there may be opportunities to relax some of these controls, leading to more flexible and cost-effective manufacturing processes.
This is the challenge that the NASA study on T1100/3960 carbon fiber/epoxy prepreg set out to address. By subjecting this high-performance material to various environmental conditions before curing, the researchers aimed to provide concrete data on its true sensitivity to temperature and humidity variations.
To address the problem of uncertain environmental sensitivity in composite materials, NASA researchers designed a comprehensive study to evaluate the effects of temperature and relative humidity on T1100/3960 carbon fiber/epoxy prepreg. Their approach was both practical and rigorous, mimicking real-world manufacturing conditions while employing precise scientific methods.
The researchers created four test groups:
These conditions were chosen to reflect a range of environments commonly encountered in large-volume high bay manufacturing facilities.
After conditioning, the researchers fabricated composite laminates and subjected them to a battery of tests:
This comprehensive approach allowed the researchers to evaluate multiple aspects of the material's performance, from visual quality to mechanical properties and thermal characteristics. By comparing the results across the different environmental exposure groups, they could determine the true impact of temperature and humidity variations on the T1100/3960 prepreg system.
This methodology provides a solution to the problem of uncertainty by generating concrete, quantitative data on the material's environmental sensitivity. It offers a template for how other composite materials could be evaluated, potentially leading to more informed and efficient manufacturing processes across the industry.
The results of NASA's study on T1100/3960 carbon fiber/epoxy prepreg were both surprising and encouraging. Here's a breakdown of the key findings:
For those interested in a more detailed look at the thermal behavior of the material, the following figure shows representative DMA output from each test group:
These findings provide a solution to the problem of uncertainty regarding environmental sensitivity in composite manufacturing. They demonstrate that T1100/3960 prepreg is remarkably robust against variations in temperature and humidity during the pre-cure stage. Specifically:
This solution has significant implications for composite manufacturing processes:
In essence, these findings offer a data-driven solution to the problem of overly cautious manufacturing practices, paving the way for more efficient and flexible composite production processes without compromising product quality.
The findings from NASA's study on T1100/3960 carbon fiber/epoxy prepreg have far-reaching implications for the composite manufacturing industry, particularly in aerospace applications. Here are the key implications and practical takeaways:
These implications and takeaways provide a roadmap for potentially significant improvements in composite manufacturing processes, balancing the need for product quality with opportunities for increased efficiency and cost savings.
NASA's groundbreaking study on the effects of temperature and relative humidity on T1100/3960 carbon fiber/epoxy prepreg has challenged long-held assumptions in the composite manufacturing industry. Let's recap the key findings and consider their broader implications:
These findings suggest that the T1100/3960 prepreg system is more robust than previously thought, potentially allowing for more flexible and cost-effective manufacturing processes without compromising product quality.
While this study provides valuable insights, it also opens up new avenues for further research:
Robotics Power displayed through Tesla Optimus Robot
Discover the future of composite manufacturing with Addcomposites! Here's how you can get involved:
At Addcomposites, we are dedicated to revolutionizing composite manufacturing. Our AFP systems and comprehensive support services are waiting for you to harness. So, don't wait – get started on your journey to the future of manufacturing today!
In the high-stakes world of aerospace engineering, the manufacturing process of composite materials is often shrouded in strict environmental controls. Temperature and humidity are watched with hawk-like precision, under the assumption that even slight variations could compromise the integrity of the final product. But what if these stringent controls aren't always necessary? A recent NASA study on T1100/3960 carbon fiber/epoxy prepreg challenges this conventional wisdom, potentially revolutionizing how we approach composite manufacturing.
The study, conducted by researchers at NASA's Marshall Space Flight Center, delves into the effects of temperature and relative humidity on T1100/3960 carbon fiber/epoxy prepreg during the critical period before layup and curing. This material, known for its high performance in aerospace applications, has been put under the microscope to determine just how sensitive it really is to environmental fluctuations.
Why does this matter? In the aerospace industry, where safety and performance are paramount, understanding the true environmental sensitivity of materials can lead to more efficient manufacturing processes, potential cost savings, and ultimately, better end products. But the implications stretch beyond aerospace - any industry utilizing high-performance composites could benefit from these insights.
To fully appreciate the significance of NASA's study, it's crucial to understand the context of environmental sensitivity in composite materials and some key concepts related to their manufacturing.
Composite materials, particularly those used in aerospace applications, have long been thought to be highly sensitive to environmental conditions during the manufacturing process. This sensitivity stems from the nature of the materials themselves. Composites typically consist of strong fibers (like carbon) embedded in a polymer matrix (often epoxy). The epoxy component, being hygroscopic, can absorb moisture from the air, potentially leading to changes in its chemical structure and physical properties.
Traditionally, it's been believed that exposure to high humidity or temperature fluctuations during the pre-cure stages could lead to moisture absorption in the epoxy, potentially causing:
As a result, composite manufacturing facilities often implement strict environmental controls, maintaining specific temperature and humidity levels. However, these controls can be costly and energy-intensive, making the manufacturing process more complex and expensive.
This is where the NASA study comes in, challenging these long-held assumptions by investigating how T1100/3960 carbon fiber/epoxy prepreg actually responds to varying environmental conditions before curing.
In the world of high-performance composites, particularly in aerospace applications, manufacturers have long grappled with a significant challenge: how to maintain optimal environmental conditions during the pre-cure stages of composite production. The concern stems from the potential negative effects of temperature fluctuations and humidity exposure on uncured prepreg materials.
The specific problems this creates include:
The core of the problem lies in the balance between ensuring product quality and optimizing manufacturing efficiency. If prepreg materials are indeed highly sensitive to environmental conditions, then strict controls are necessary to maintain product integrity. However, if they are more robust than previously thought, there may be opportunities to relax some of these controls, leading to more flexible and cost-effective manufacturing processes.
This is the challenge that the NASA study on T1100/3960 carbon fiber/epoxy prepreg set out to address. By subjecting this high-performance material to various environmental conditions before curing, the researchers aimed to provide concrete data on its true sensitivity to temperature and humidity variations.
To address the problem of uncertain environmental sensitivity in composite materials, NASA researchers designed a comprehensive study to evaluate the effects of temperature and relative humidity on T1100/3960 carbon fiber/epoxy prepreg. Their approach was both practical and rigorous, mimicking real-world manufacturing conditions while employing precise scientific methods.
The researchers created four test groups:
These conditions were chosen to reflect a range of environments commonly encountered in large-volume high bay manufacturing facilities.
After conditioning, the researchers fabricated composite laminates and subjected them to a battery of tests:
This comprehensive approach allowed the researchers to evaluate multiple aspects of the material's performance, from visual quality to mechanical properties and thermal characteristics. By comparing the results across the different environmental exposure groups, they could determine the true impact of temperature and humidity variations on the T1100/3960 prepreg system.
This methodology provides a solution to the problem of uncertainty by generating concrete, quantitative data on the material's environmental sensitivity. It offers a template for how other composite materials could be evaluated, potentially leading to more informed and efficient manufacturing processes across the industry.
The results of NASA's study on T1100/3960 carbon fiber/epoxy prepreg were both surprising and encouraging. Here's a breakdown of the key findings:
For those interested in a more detailed look at the thermal behavior of the material, the following figure shows representative DMA output from each test group:
These findings provide a solution to the problem of uncertainty regarding environmental sensitivity in composite manufacturing. They demonstrate that T1100/3960 prepreg is remarkably robust against variations in temperature and humidity during the pre-cure stage. Specifically:
This solution has significant implications for composite manufacturing processes:
In essence, these findings offer a data-driven solution to the problem of overly cautious manufacturing practices, paving the way for more efficient and flexible composite production processes without compromising product quality.
The findings from NASA's study on T1100/3960 carbon fiber/epoxy prepreg have far-reaching implications for the composite manufacturing industry, particularly in aerospace applications. Here are the key implications and practical takeaways:
These implications and takeaways provide a roadmap for potentially significant improvements in composite manufacturing processes, balancing the need for product quality with opportunities for increased efficiency and cost savings.
NASA's groundbreaking study on the effects of temperature and relative humidity on T1100/3960 carbon fiber/epoxy prepreg has challenged long-held assumptions in the composite manufacturing industry. Let's recap the key findings and consider their broader implications:
These findings suggest that the T1100/3960 prepreg system is more robust than previously thought, potentially allowing for more flexible and cost-effective manufacturing processes without compromising product quality.
While this study provides valuable insights, it also opens up new avenues for further research:
Robotics Power displayed through Tesla Optimus Robot
Discover the future of composite manufacturing with Addcomposites! Here's how you can get involved:
At Addcomposites, we are dedicated to revolutionizing composite manufacturing. Our AFP systems and comprehensive support services are waiting for you to harness. So, don't wait – get started on your journey to the future of manufacturing today!