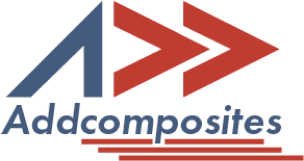
In the ever-evolving world of composites, we often think we've seen it all. But every once in a while, a technology emerges that takes us by surprise, challenges our assumptions, and opens new horizons. Continuous Fiber Additive Manufacturing (CFRP-AM) is that unexpected revolution.
Continuous Fiber Reinforced Polymer (CFRP) composites are transforming the industry with their high specific stiffness and strength. Here's what you need to know:
Cellular Structure Design: With CFRP-AM, you can design 3D-printed composite structures with tunable mechanical properties while maintaining lightweight.
Incorporating Functionalities: Actuators, sensors, energy storage modules - CFRP-AM paves the road for intelligent devices, from 3D printed smart composite structures to carbon fiber-embedded artificial hands.
Electro-Induced Shape Memory Effect: Imagine 4D printed auxetic composites using innovative materials like PLA/TPU/CNT filament.
CFRP-AM is more than a technological advancement; it's a revolution in the fabrication process of continuous fiber reinforced polymer composites. The development of additive manufacturing has enabled products with ever-increasing complexity and previously unattainable performance. From shape morphing to sensing and energy storage, CFRP-AM is enabling novel applications that are reshaping industries.
Design Opportunities: The design space endowed by additive manufacturing is being explored to improve the overall performance of composites. Material, process, and structure are the three design domains in CFRP-AM, each with variables that can be leveraged for performance improvement. Multi-objective optimization and multi-criteria decision-making techniques ensure that design considers functional, economic, and environmental aspects.
Challenges and Future Work: CFRP-AM is not without its challenges, but the future is promising. The strength of interfacial bonds is related to failures such as delamination or stress concentration, requiring further research. Recent endeavors aim to further improve efficiency, accuracy, and fabrication quality, such as 3D microwave printing technology.
The journey of Continuous Fiber Additive Manufacturing is just beginning, and the road ahead is filled with opportunities, challenges, and surprises. From revolutionizing fabrication to empowering innovation and enhancing lives, CFRP-AM is more than a technological advancement; it's a human-centered approach that's reshaping the future. The article provides valuable insights into the design opportunities, novel applications, and future outlook of CFRP-AM, offering a comprehensive view of this exciting field. The future is bright, and the possibilities are endless.
Discover the future of composite manufacturing with Addcomposites! Here's how you can get involved:
At Addcomposites, we are dedicated to revolutionizing composite manufacturing. Our AFP and Structural continuous fiber additive manufacturing systems and comprehensive support services are waiting for you to harness. So, don't wait – get started on your journey to the future of manufacturing today!
In the ever-evolving world of composites, we often think we've seen it all. But every once in a while, a technology emerges that takes us by surprise, challenges our assumptions, and opens new horizons. Continuous Fiber Additive Manufacturing (CFRP-AM) is that unexpected revolution.
Continuous Fiber Reinforced Polymer (CFRP) composites are transforming the industry with their high specific stiffness and strength. Here's what you need to know:
Cellular Structure Design: With CFRP-AM, you can design 3D-printed composite structures with tunable mechanical properties while maintaining lightweight.
Incorporating Functionalities: Actuators, sensors, energy storage modules - CFRP-AM paves the road for intelligent devices, from 3D printed smart composite structures to carbon fiber-embedded artificial hands.
Electro-Induced Shape Memory Effect: Imagine 4D printed auxetic composites using innovative materials like PLA/TPU/CNT filament.
CFRP-AM is more than a technological advancement; it's a revolution in the fabrication process of continuous fiber reinforced polymer composites. The development of additive manufacturing has enabled products with ever-increasing complexity and previously unattainable performance. From shape morphing to sensing and energy storage, CFRP-AM is enabling novel applications that are reshaping industries.
Design Opportunities: The design space endowed by additive manufacturing is being explored to improve the overall performance of composites. Material, process, and structure are the three design domains in CFRP-AM, each with variables that can be leveraged for performance improvement. Multi-objective optimization and multi-criteria decision-making techniques ensure that design considers functional, economic, and environmental aspects.
Challenges and Future Work: CFRP-AM is not without its challenges, but the future is promising. The strength of interfacial bonds is related to failures such as delamination or stress concentration, requiring further research. Recent endeavors aim to further improve efficiency, accuracy, and fabrication quality, such as 3D microwave printing technology.
The journey of Continuous Fiber Additive Manufacturing is just beginning, and the road ahead is filled with opportunities, challenges, and surprises. From revolutionizing fabrication to empowering innovation and enhancing lives, CFRP-AM is more than a technological advancement; it's a human-centered approach that's reshaping the future. The article provides valuable insights into the design opportunities, novel applications, and future outlook of CFRP-AM, offering a comprehensive view of this exciting field. The future is bright, and the possibilities are endless.
Discover the future of composite manufacturing with Addcomposites! Here's how you can get involved:
At Addcomposites, we are dedicated to revolutionizing composite manufacturing. Our AFP and Structural continuous fiber additive manufacturing systems and comprehensive support services are waiting for you to harness. So, don't wait – get started on your journey to the future of manufacturing today!