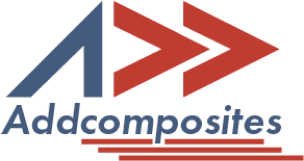
Composite materials, often simply called composites, are engineered materials made from two or more constituent materials with significantly different physical or chemical properties. When combined, they produce a material with characteristics different from the individual components. The individual components remain separate and distinct within the finished structure, differentiating composites from mixtures and solid solutions.
Introduction to Composite Materials
Composites typically consist of:
Common types of composites include:
Composites are used in a wide range of applications due to their unique properties:
Mechanical testing of composites is crucial for several reasons:
Mechanical Testing of Composites
Composite materials exhibit unique stress-strain relationships due to their heterogeneous nature:
A typical stress-strain curve for a unidirectional fiber-reinforced composite loaded in the fiber direction shows:
Anisotropy is a fundamental characteristic of many composite materials, especially fiber-reinforced composites:
Understanding the anisotropic behavior of composites is crucial for:
The complex behavior of composite materials, including their anisotropic nature and unique stress-strain relationships, underscores the importance of thorough and appropriate mechanical testing. These tests provide the necessary data to understand, predict, and optimize the performance of composite structures in various applications.
Tensile testing is one of the most fundamental and widely used mechanical tests for composite materials. It provides critical information about the material's strength, stiffness, and behavior under uniaxial loading conditions. The ASTM D3039 standard is the most commonly used method for conducting tensile tests on polymer matrix composite materials.
Mechanical Testing of Composites
The ASTM D3039 standard specifies several key aspects of specimen geometry:
Composite materials, especially those with unidirectional reinforcement, exhibit highly anisotropic behavior. Therefore, testing in both longitudinal (0°, parallel to fibers) and transverse (90°, perpendicular to fibers) directions is crucial for a complete characterization.
The stark difference in properties between these two orientations highlights the anisotropic nature of composite materials and the importance of testing in multiple directions.
Given the inherent variability in composite materials, statistical analysis of test results is crucial:
Examining the failure mode of tensile specimens provides valuable insights:
Understanding and correctly interpreting tensile test data is crucial for:
Tensile testing, while seemingly straightforward, requires careful attention to specimen preparation, test execution, and data analysis to obtain reliable and meaningful results for composite materials.
Compression testing is a critical aspect of characterizing composite materials, particularly for applications where compressive loads are significant, such as in aerospace structures. The ASTM D3410 standard provides a method for determining the in-plane compressive properties of polymer matrix composite materials reinforced by high-modulus fibers.
Mechanical Testing of Composites
Compression testing of composites is more challenging than tensile testing due to the difficulty in introducing a purely compressive load without inducing buckling or other undesirable failure modes. Several test methods and fixtures have been developed to address these challenges:
The Illinois Institute of Technology Research Institute (IITRI) fixture is the most commonly used method specified in ASTM D3410:
While primarily designed for unreinforced plastics, this method can be adapted for composite materials:
This method combines end loading and shear loading:
Proper specimen geometry is crucial for obtaining valid compression test results:
Compression testing of composites presents several unique challenges:
Compression testing of composites, while challenging, provides critical data for material characterization and structural design. Understanding these challenges and implementing appropriate solutions is key to obtaining reliable and meaningful compression test results for composite materials.
Flexural and shear testing are crucial for characterizing the mechanical behavior of composite materials under bending and shear loads. These tests provide valuable insights into the material's performance in applications where bending and shear stresses are significant.
Mechanical Testing of Composites
Flexural testing determines a material's behavior under bending loads. The ASTM D7264 standard describes procedures for both three-point and four-point bending tests.
The ASTM D3518 test method determines the in-plane shear properties of polymer matrix composite materials reinforced by high-modulus fibers.
The ASTM D2344 standard, also known as the Short Beam Strength (SBS) test, is used to determine the interlaminar shear strength of composite materials.
Interpreting the failure mode is crucial for validating the test results.
Flexural and shear testing provide essential data for understanding the behavior of composite materials under complex loading conditions. These tests, when combined with tensile and compression testing, offer a comprehensive characterization of a composite material's mechanical properties, crucial for design and analysis in various applications.
Impact and fatigue testing are crucial for understanding the behavior of composite materials under sudden loads and cyclic loading conditions. These tests provide valuable insights into a material's toughness, energy absorption capabilities, and long-term performance under repeated loading.
Mechanical Testing of Composites
Impact tests measure a material's ability to absorb energy during fracture. For composite materials, these tests are particularly important in assessing damage tolerance and energy absorption capabilities.
Defects and Damage in Composite Materials and Structures
Fatigue testing assesses a material's performance under cyclic loading conditions. For composites, fatigue behavior is crucial due to their use in long-term, cyclic loading applications like wind turbine blades or aircraft structures.
Impact and fatigue testing provide critical information about a composite material's performance under dynamic and cyclic loading conditions. These tests are essential for predicting the long-term behavior and reliability of composite structures in various applications, from aerospace to wind energy.
Environmental factors can significantly influence the mechanical properties of composite materials. Understanding these effects is crucial for predicting long-term performance and ensuring reliability in various applications. This chapter focuses on moisture absorption, temperature effects, and combined environmental and mechanical testing.
Mechanical Testing of Composites
Moisture absorption can significantly affect the mechanical properties of polymer matrix composites, particularly those with hygroscopic matrices like epoxy.
Temperature can significantly affect the mechanical properties of composites, particularly the matrix-dominated properties.
Real-world applications often involve simultaneous exposure to environmental conditions and mechanical loads. Combined testing provides more realistic performance data.
RT: Room Temperature
Understanding the environmental effects on mechanical properties is crucial for:
By comprehensively testing composites under various environmental conditions, engineers can ensure the long-term reliability and performance of composite structures in challenging real-world applications.
Non-destructive testing (NDT) is crucial for evaluating the integrity of composite materials and structures without causing damage. These techniques are essential for quality control during manufacturing, in-service inspection, and damage assessment. This chapter focuses on key NDT methods for composites: ultrasonic testing, thermography, and X-ray computed tomography.
Non-Destructive Testing for Composites: Different Inspection Methods
Ultrasonic testing is one of the most widely used NDT methods for composites due to its versatility and effectiveness in detecting internal defects.
Thermography uses infrared cameras to detect temperature differences on the surface of a material, which can indicate subsurface defects.
X-ray CT provides detailed 3D images of the internal structure of composites, allowing for comprehensive defect analysis.
Factors to consider:
Non-destructive testing is a critical aspect of ensuring the quality and reliability of composite materials and structures. By employing a combination of NDT methods and staying abreast of technological advancements, engineers and inspectors can effectively detect and characterize defects, ensuring the safety and performance of composite components throughout their lifecycle.
Proper data analysis, interpretation, and quality control are crucial for extracting meaningful information from mechanical tests on composite materials. This chapter covers statistical analysis techniques, failure mode identification, property prediction and modeling, relevant standards, and databases for composite properties.
Statistical analysis is essential for understanding the variability inherent in composite materials and for making reliable predictions about their properties.
Understanding failure modes is crucial for improving material design and predicting long-term performance.
Predictive modeling is essential for design and optimization of composite structures.
Standards ensure consistency and comparability of test results across different laboratories and organizations.
Databases are valuable resources for material selection, design, and research.
Databases on Mechanical Properties of Composites
Effective data analysis, interpretation, and quality control are essential for maximizing the value of mechanical testing of composites. By employing rigorous statistical techniques, understanding failure modes, utilizing predictive models, adhering to established standards, and leveraging comprehensive databases, engineers and researchers can make informed decisions in the design, manufacture, and application of composite materials.
As composite materials and manufacturing technologies evolve, so do the testing methods required to characterize these advanced materials. This chapter focuses on testing methodologies for sandwich structures, 3D woven composites, and continuous fiber 3D printed composites.
Sandwich structures, consisting of two thin, stiff face sheets bonded to a lightweight core, are widely used in aerospace, marine, and wind energy applications due to their high stiffness-to-weight ratio.
3D woven composites offer improved through-thickness properties and damage tolerance compared to traditional laminated composites.
Continuous fiber 3D printing is an emerging technology that allows for complex, tailored fiber orientations within a part.
Advanced composite testing presents unique challenges but also opportunities for innovation. As materials and manufacturing technologies continue to evolve, testing methodologies must adapt to provide accurate, reliable data for design, quality control, and certification of these advanced materials.
As composite materials continue to evolve and find new applications, the methods for testing and analyzing these materials are also advancing. This chapter explores the future trends in composite testing, with a focus on automation and artificial intelligence, and examines case studies in key industrial sectors.
Automation is revolutionizing composite testing, offering increased efficiency, repeatability, and data quality.
Benefits:
Challenges:
Artificial Intelligence (AI) and Machine Learning (ML) are transforming the way composite test data is analyzed and interpreted.
The Shift in Composite Manufacturing from Traditional to Intelligent
Examining real-world applications of advanced composite testing in key industries provides insight into current practices and future directions.
Case Study: Next-Generation Aircraft Wing
Case Study: Electric Vehicle Battery Enclosure
Case Study: Next-Generation Wind Turbine Blades
The future of composite testing is likely to see:
The future of composite testing is characterized by increased automation, intelligent data analysis, and a holistic approach to material characterization and structural performance. As composites continue to push the boundaries of material capabilities, testing methodologies will evolve to meet these new challenges, enabling the development of safer, more efficient, and more sustainable composite structures across various industries.
As we conclude this comprehensive course on "Mechanical Testing of Advanced Fibre Composites," we encourage you to continue your journey in this exciting and rapidly evolving field:
Remember, the field of composite materials and testing is dynamic and continually evolving. Your ongoing engagement and contribution will not only advance your career but also help shape the future of this critical technology sector.
For more information and resources, visit our website: AddComposites - Advancing Composite Manufacturing
Thank you for participating in this course, and we wish you success in your future endeavors in the world of advanced composite materials!