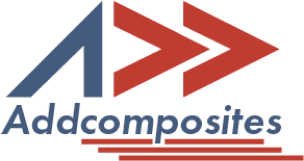
Automated Fiber Placement (AFP) technology has revolutionized composite manufacturing, particularly when it comes to creating complex geometries that were once considered impossible or prohibitively expensive to produce. Single-tow AFP systems offer unique advantages in handling intricate geometries, providing precision and flexibility that make them indispensable for certain applications.
Single-tow AFP systems excel at tow steering—the ability to place fiber tows along curved paths. The narrower the tow, the tighter the steering radius possible:
In exceptional cases, steering radii as small as 100 millimeters (4 inches) have been demonstrated, though this isn't typical for production applications7.
The use of narrow tows in the AFP process significantly enhances drapability, allowing for the lamination of more complex geometries6. This is particularly valuable when working with concave parts, sandwich structures, and closed sections that would be challenging with wider tows or manual layup techniques.
Single-tow systems maintain high precision even on complex surfaces through:
The AFP-XS system has demonstrated its capabilities across various complex geometries:
The system has been successfully used for manufacturing:
The AFP-XS's dual AFP/filament winding capability allows for the production of complex geometries like Type IV hydrogen tanks, switching between AFP and filament winding modes without cell reconfiguration2. This hybrid approach has achieved 40% faster cycle times compared to manual methods2.
A case study in the marine industry showed 55% weight reduction in hydrofoils using dry fiber AFP versus traditional manual wet layup techniques2, demonstrating the system's ability to create complex, lightweight structures.
The choice between single-tow and multi-tow approaches depends on the specific application:
The AFP technology landscape continues to evolve, with innovations focusing on:
Single-tow AFP systems like the AFP-XS have democratized access to advanced composite manufacturing, enabling small and medium enterprises to produce complex geometries that were previously only possible for large aerospace corporations with multimillion-dollar budgets2. As the technology continues to mature, we can expect even greater capabilities in mastering complex geometries with automated fiber placement.